1 Measurement of Water Temperature
Total Page:16
File Type:pdf, Size:1020Kb
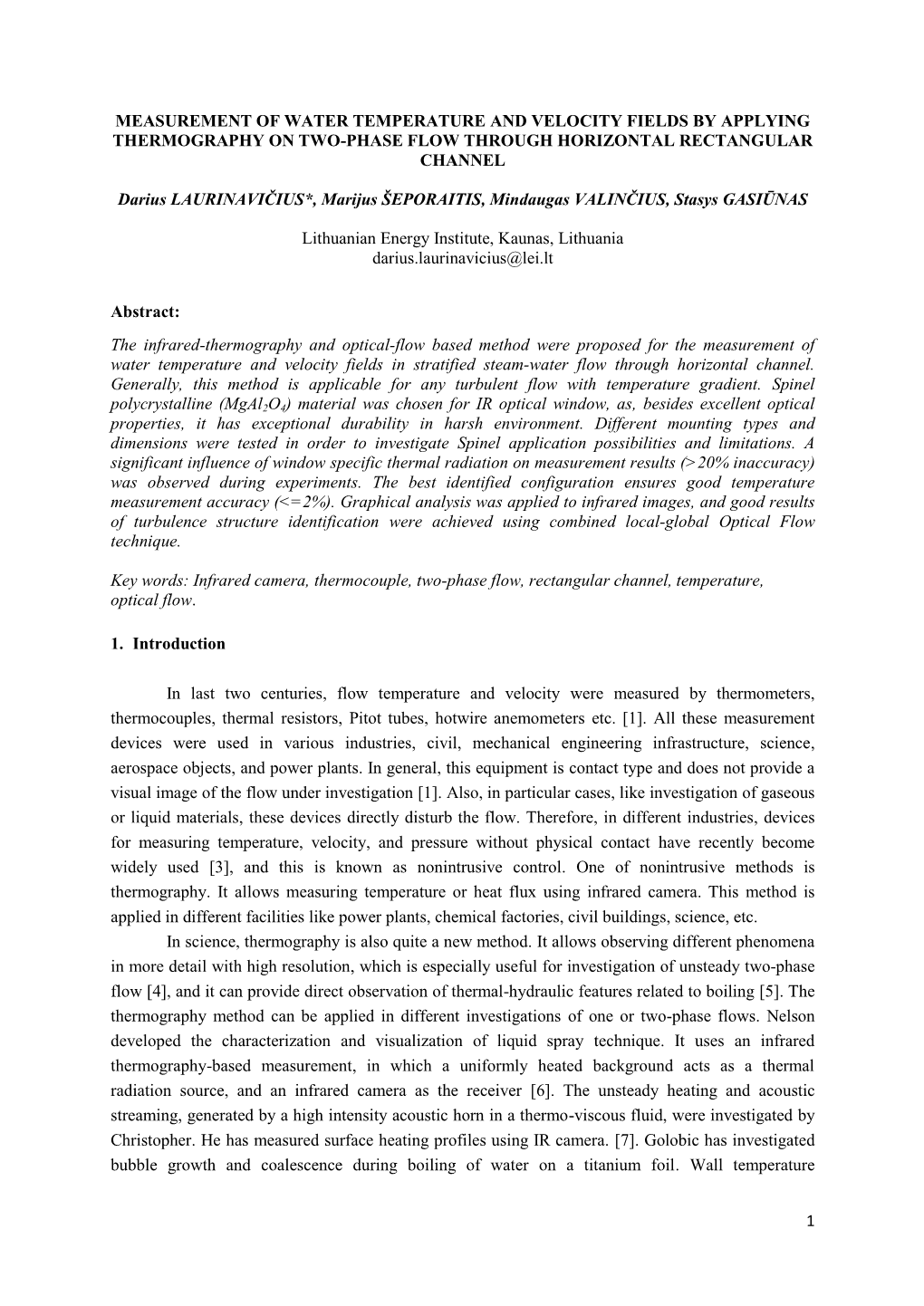
Load more
Recommended publications
-
TUNING the OPTICAL and MECHANICAL PROPERTIES of Y2O3 CERAMICS by the INCLUSION of La3+ ION in the MATRIX for INFRARED TRANSPARENT WINDOW APPLICATIONS
International Journal of Advanced Research in Engineering and Technology (IJARET) Volume 10, Issue 2, March- April 2019, pp. 1-13, Article ID: IJARET_10_02_001 Available online at http://iaeme.com/Home/issue/IJARET?Volume=10&Issue=2 ISSN Print: 0976-6480 and ISSN Online: 0976-6499 © IAEME Publication TUNING THE OPTICAL AND MECHANICAL PROPERTIES OF Y2O3 CERAMICS BY THE INCLUSION OF La3+ ION IN THE MATRIX FOR INFRARED TRANSPARENT WINDOW APPLICATIONS Mathew C.T EMRL, Department of Physics, Mar Ivanios College, Thiruvananthapuram, Kerala, India ABSTRACT Infrared transparent windows are generally used to protect highly delicate infrared sensor circuits from the harsh environments. In the present work a combustion technique was effectively used to incorporate La3+ ion in the yttria matrix. The crystallites were in the size limit of 20 nm. Powder characterization using X-ray diffraction, HRTEM and FTIR spectroscopy revealed that the La3+ ions were effectively replacing the Y3+ ion in the yttria matrix. There was a slight reduction in optical band gap with La3+ concentration. A novel sintering mechanism was used for sintering the samples by coupling definite proportions of resistive heating and microwave heating. The highly dense pellets showed better transmittance and hardness properties, which improved with La3+concentration. The present study authorises that combustion synthesis of the samples followed by resistive coupled microwave sintering can effectively be used to tune the optical and mechanical, properties of infrared transparent ceramics. -
Transparent Armor Ceramics As Spacecraft Windows
University of Nebraska - Lincoln DigitalCommons@University of Nebraska - Lincoln NASA Publications National Aeronautics and Space Administration 2012 Transparent Armor Ceramics as Spacecraft Windows Jonathan Salem NASA Glenn Research Center, [email protected] Follow this and additional works at: https://digitalcommons.unl.edu/nasapub Salem, Jonathan, "Transparent Armor Ceramics as Spacecraft Windows" (2012). NASA Publications. 121. https://digitalcommons.unl.edu/nasapub/121 This Article is brought to you for free and open access by the National Aeronautics and Space Administration at DigitalCommons@University of Nebraska - Lincoln. It has been accepted for inclusion in NASA Publications by an authorized administrator of DigitalCommons@University of Nebraska - Lincoln. J. Am. Ceram. Soc., 1–9 (2012) DOI: 10.1111/jace.12089 © Journal 2012 The American Ceramic Society Transparent Armor Ceramics as Spacecraft Windows Jonathan A. Salem*,† NASA Glenn Research Center, Cleveland, OH 44135 The slow crack growth parameters of several transparent In addition to generating material properties, an equation is armor ceramics were measured as part of a program to lighten derived to estimate the required window pane mass in terms next generation spacecraft windows. Transparent magnesium of crack growth parameters and specified lifetime. aluminate (spinel, MgAl2O4) and AlON exhibit superior slow crack resistance relative to fused silica, which is the historical II. Test Materials material of choice. For spinel, slow crack growth, strength, and fracture toughness are significantly influenced by the grain size, To date, transparent spinel (MgAl2O4) and aluminum-oxy- and alumina-rich phases and porosity at the grain boundaries nitride (AlON) have been tested by using specimens extracted lead to intergranular fracture in coarse grain spinel. -
Development of Highly Transparent Zirconia Ceramics
11 Development of highly transparent zirconia ceramics Isao Yamashita *1 Masayuki Kudo *1 Koji Tsukuma *1 Highly transparent zirconia ceramics were developed and their optical and mechanical properties were comprehensively studied. A low optical haze value (H<1.0 %), defined as the diffuse transmission divided by the total forward transmission, was achieved by using high-purity powder and a novel sintering process. Theoretical in-line transmission (74 %) was observed from the ultraviolet–visible region up to the infra-red region; an absorption edge was found at 350 nm and 8 µm for the ultraviolet and infrared region, respectively. A colorless sintered body having a high refractive index (n d = 2.23) and a high Abbe’s number (νd = 27.8) was obtained. A remarkably large dielectric constant (ε = 32.7) with low dielectric loss (tanδ = 0.006) was found. Transparent zirconia ceramics are candidates for high-refractive index lenses, optoelectric devices and infrared windows. Transparent zirconia ceramics also possess excellent mechanical properties. Various colored transparent zirconia can be used as exterior components and for complex-shaped gemstones. fabricating transparent cubic zirconia ceramics.9,13-19 1.Introduction Transparent zirconia ceramics using titanium oxide as Transparent and translucent ceramics have been a sintering additive were firstly reported by Tsukuma.15 studied extensively ever since the seminal work on However, the sintered body had poor transparency translucent alumina polycrystal by Coble in the 1960s.1 and low mechanical strength. In this study, highly Subsequently, researchers have conducted many transparent zirconia ceramics of high strength were studies to develop transparent ceramics such as MgO,2 developed. -
PERLUCOR® Transparent Ceramics Transparent, Durable and Hard-Wearing − Wherever It Counts
The Innovative Material for New Dimensions PERLUCOR® Transparent Ceramics Transparent, durable and hard-wearing − wherever it counts Transparent Ceramics PERLUCOR® is opening up completely new areas of application. A material for the extremes: everywhere where conventional glasses, special glasses and protective glasses reach their limits, PERLUCOR® displays greater strength. The material combines transpar ency with the extraordinary qualities of highperformance ceramic. With excellent properties, the optically perfected highperformance ceramic offers superior qualities for transparent extreme applications, for exam ple, in the areas of ARCHITECTURE SCANNERS & DISPLAYS INDUSTRY OPTICS & SENSORS JEWELLERY & DESIGN Let yourself be inspired by this innovative material: for a multitude of new application possibilities. SCRATCH-PROOF HARD CHEMICALLY RESISTANT TEMPERATURE-RESISTANT TRANSPARENT BRILLIANT Architecture Shining prospects for the architecture of the future Think beyond borders. Combine functionality with aesthetics in modern architecture. Transparent Ceramics PERLUCOR® is opening up new perspectives and possibilities. It sur passes the conventional borders of durability and remains abrasionresistant, nonslip, break proof and transparent. Perfect for applications in architecture, such as skywalks, stairways, glass flooring and lighting systems – when it comes to unclouded vision, the greatest stabil ity and lasting robustness. Scanners & Displays Longer-lasting visibility for data collection Scanners and modern displays for data collec tion and processing must consistently withstand high mechanical loads and constantly maintain optimal transparency. To enable data to be collected and processed fast, safely and without error. No problem with PERLUCOR®: its extreme robustness and its resistance to scratches, shocks, wear, chemicals and breakage provide longlasting protection. At airport checkins, or in fingerprint or hand scanners, for example. -
Solid-State Lasers for Medical Applications 129
5 Solid- state lasers for medical applications J. ŠULC and H. JELÍNKOVÁ, Czech Technical University in Prague, Czech Republic DOI: 10.1533/9780857097545.2.127 Abstract: The goal of this chapter is to provide the fundamentals of solid- state lasers used in medical applications. After a brief introduction, the fundamental properties of solid- state laser active media are described. The main part of this chapter contains the description of a solid- state laser system, its pumping and cooling, modes of operation, and emission wavelength control, including a non- linear conversion of radiation. In the following part, a detailed description of selected solid- state laser types used in medical applications is given. At the end of this chapter, the construction and materials of some novel solid- state lasers are described. Key words: solid- state lasers, non- linear conversion of radiation, laser crystal, diode pumping, Q-switching, tunable solid- state laser. 5.1 Introduction Solid- state lasers (SSL) are attractive sources of coherent radiation for various scientifi c as well as industrial applications. As was mentioned in Chapter 2 , lasers can be divided into fi ve groups: solid- state, semiconductor, liquid, gas, and plasma lasers. According to the state of a laser active environment, solid- state and semiconductor lasers can be integrated into one group, because both these active media are in solid form. But, in a narrower sense of the term, solid-state lasers are systems whose active medium consists of a transparent solid matrix (e.g. crystal, glass or ceramics) doped by an optically active ion and using optical pumping for excitation. -
Strategic Marketing Innovations, Incorporated
Overview of the Advanced Ceramics Industry in the United States John E. Holowczak Chair, United States Advanced Ceramics Association Associate Director – Advanced Materials United Technologies Research Center Glen Mandigo and Doug Freitag, USACA 1020 Nineteenth St. NW Suite 375 Washington, D.C. 20036 This document does not contain any export controlled technical data. Introduction to USACA Established in 1985 to promote the research, development, and application of advanced ceramics 38 member companies and organizations USACA works to promote advanced ceramic materials, disseminate information about the materials, and interface with the U.S. government on behalf of the industry. Members advise federal agencies through technology roadmaps and conferences. Active technology roadmaps include: Advanced Ceramics Technology Roadmap, 2001 Advanced Ceramics for Distributed Energy, 2004 Ceramic Composites Affordability and Producibility Initiative, 2009 Transparent Ceramic Armor Producibility Roadmap, 2013 Transparent Ceramic Sensor Windows Roadmap, 2017 Ceramic Composites Affordability and Producibility Roadmap update, 2016 2 This page does not contain any export controlled technical data. What are Advanced Ceramics Lightweight, strong materials capable of performing in extreme environments: High Temperature and Pressure High Stiffness and Durability Ultra Hard & Tough Surface Not This! 3 This page does not contain any export controlled technical data. Membership Across the Supply Chain Design/Stds/ Raw Test & Research Fabrication Machining -
Transparent Ballistic Armour Ceramics. Recent Advances and Issues to Be Overcome
Transparent ballistic armour ceramics. Recent advances and issues to be overcome Felipe Orgaz Instituto de Ceramica y Vidrio, CSIC, Spain Transparent armour is a system designed to be -Transparent ceramics offer significant ballistic optically transparent to support dynamic protection in relation to conventional glass/plastic fragmentation when subjected to the high strain systems. A few companies produce this kind of rates produced by ballistic impacts. They are mainly products: Surmet (ALON® technology), Armorline used to protect vehicle occupants from terrorist (Spinel), Saint Gobain Group (Sapphire), Technology actions and other hostile conflicts, as visors for non- Assessment and Transfer (TA&T) (Spinel). For combat use like riot control or explosive actions, etc. technology transfer: Fraunhofer Institut (IKTS). Light weight, small thickness, low optical distortion, compatibility with night vision equipment and multi Some issues must be overcome: commercial hit capability are needed to defeat armour piercing availability, very high cost raw materials, high ammunitions (AP) threats. These systems consist of investments, complex processing techniques (hot a sandwich structure with a hard front layer of pressing, hot isostatic pressing, Spark Plasma transparent ceramic joined to several plies of glass Sintering), machining and polishing costs, large with polymer inter layers and polycarbonate formats and curved shapes, new structural designs backing. Advances in material science and for multi hit capability, etc technology over the last 40 years has made available sub-μm grain size polycrystalline α- Al2O3 -Several programs are investigating for cost aluminium oxynitride (AlON) , magnesium aluminate reduction, new processing ways and scale up of spinel (MgAl2O4)3 and these materials: As strategies are proposed: single crystal sapphire (Al2O3) as alternative ceramic Conventional pressureless sintering, gel casting, materials able to satisfy the requirements of nanotechnology, nanocomposite optical ceramics transparency and hardness for armours application. -
Security Materials Technologies Roadmap Synthesis Report
Security and disruptive technologies Security Materials Technologies Roadmap Synthesis Report prepared by the Security Materials Technologies Industry Steering Committee, National Research Council of Canada Security Materials Technologies Program, and Defence Research and Development Canada Editors Andrew Johnston, Ph.D. Program Leader, Security Materials Technologies National Research Council Canada Kevin Williams, Ph.D. Scientific Advisor, Soldier S&T Program Defence Research and Development Canada Alan Bolster Client Relationship Leader National Research Council Canada Andrew Plater Program Manager, Land Combat Systems Defence Research and Development Canada Marc McArthur Innovation Networks Advisor National Research Council Canada Contributing Authors Behnam Ashrafi, NRC Sylvain Labonté, NRC Yves Baillargeon, DRDC Chun Li, NRC Wayne Baird, NRC Catalin Mandache, NRC LCol Ron Bell, CAF Marc McArthur, NRC Alan Bolster, NRC Major Mark McNeil, CAF Brenda Brady, NRC Ali Merati, NRC Alain Bujold, Mawashi Science and Technology Dennis Nandlall, DRDC Jean-Philippe Dionne, Med-Eng Meysam Rahmat, NRC David Fraser, Inkas Jennifer Vuong, NRC Christa Homenick, NRC Kevin Williams, DRDC Michael Jakubinek, NRC Yunfa Zhang, NRC James Kempston, Morgan Advanced Materials i Table of Contents ACKNOWLEDGEMENTS ........................................................................................................................ 1 EXECUTIVE SUMMARY ........................................................................................................................ -
On the Use of Infrared Thermography and Acousto—Ultrasonics NDT Techniques for † Ceramic-Coated Sandwich Structures
energies Article On the Use of Infrared Thermography and Acousto—Ultrasonics NDT Techniques for y Ceramic-Coated Sandwich Structures Yuxia Duan 1, Hai Zhang 2,* , Stefano Sfarra 3 , Nicolas P. Avdelidis 2, Theodoros H. Loutas 4, George Sotiriadis 4, Vassilis Kostopoulos 4, Henrique Fernandes 5,6 , Florian Ion Petrescu 7, Clemente Ibarra-Castanedo 2 and Xavier P.V. Maldague 2 1 School of Physics and Electronics, Central South University, Changsha 410083, China 2 Computer Vision and Systems Laboratory, Department of Electrical and Computer Engineering, Laval University, Quebec City, QC G1V 0A6, Canada 3 Department of Industrial and Information Engineering and Economics, University of L’Aquila, I-67100 L’Aquila, Italy 4 Department of Mechanical & Aeronautical Engineering, University of Patras, 26504 Rio Achaia, Greece 5 School of Computer Science, Federal University of Uberlandia, Uberlandia 38408-100, Brazil 6 Fraunhofer Institute for Nondestructive Testing, Campus E3 1, 66123 Saarbrücken, Germany 7 Bucharest Polytechnic University, 060042 Bucharest, Romania * Correspondence: [email protected] This paper is an extended version of paper which published in the 10th ECNDT, Moscow, Russia, y 7–11 June 2010. Received: 5 December 2018; Accepted: 20 June 2019; Published: 1 July 2019 Abstract: Ceramic-coated materials used in different engineering sectors are the focus of world-wide interest and have generated a need for inspection techniques that detect very small structural anomalies. Non-destructive testing is increasingly being used to evaluate coating thickness and to test for coating flaws. The main pros of non-destructive testing is that the tested object remains intact and available for continued use afterward. -
Transparent Armor Parimal J
A D VA N C E D M A T E R I A L S A N D AP R O C E S S E SMPTIAT E C H N O L O G Y C The AMPTIAC News l et te r, Fall 2000 Transparent Armor Parimal J. Patel, Gary A. Gilde, Peter G. Dehmer, James W. McCauley Volume 4, Number 3 Weapons and Materials Research Directorate, Army Research Laboratory Introduction Transparent armor is a material or system of materials designed to be optically transparent, yet pro- tect from fragmentation or ballistic impacts. This class of materials is used in such diverse applica- Spotlight on Technology … 1 tions as protective visors for non-combat usage, including riot control or explosive ordinance disposal (EOD) actions. They are also used to protect vehicle occupants from terrorist actions or other hos- Titanium Aluminide Intermetallics … 7 tile conflicts. Each of these systems are designed to defeat specific threats, however, there are general requirements common to most. The primary requirement for a transparent armor system is to not only defeat the designated threat but also provide a multi-hit capability with minimized distortion Calendar … 10 of surrounding areas. Land and air platforms of the future have several parameters that must be opti- mized, such as weight, space efficiency, and cost versus performance. Transparent armor windows P4A: An Affordable Composite must also be compatible with night vision equipment. One potential solution to increase the ballis- Process … 11 tic performance of a window material is to increase its thickness. However, this solution is impracti- cal in most applications, as it will increase the weight and impose space limitations in many vehicles. -
Highly Transparent Fluorotellurite Glass
Highly Transparent Fluorotellurite Glass-Ceramics: Structural Investigations and Luminescence Properties Jean-Paul Laval, Jean-René Duclère, Vincent Couderc, Mathieu Allix, Cécile Genevois, Vincent Sarou-Kanian, Franck Fayon, Pierre-Eugène Coulon, Sébastien Chenu, Maggy Dutreilh-Colas, et al. To cite this version: Jean-Paul Laval, Jean-René Duclère, Vincent Couderc, Mathieu Allix, Cécile Genevois, et al.. Highly Transparent Fluorotellurite Glass-Ceramics: Structural Investigations and Luminescence Properties. Inorganic Chemistry, American Chemical Society, 2019, 58 (24), pp.16387-16401. 10.1021/acs.inorgchem.9b01955. hal-02443274 HAL Id: hal-02443274 https://hal.archives-ouvertes.fr/hal-02443274 Submitted on 6 Jan 2021 HAL is a multi-disciplinary open access L’archive ouverte pluridisciplinaire HAL, est archive for the deposit and dissemination of sci- destinée au dépôt et à la diffusion de documents entific research documents, whether they are pub- scientifiques de niveau recherche, publiés ou non, lished or not. The documents may come from émanant des établissements d’enseignement et de teaching and research institutions in France or recherche français ou étrangers, des laboratoires abroad, or from public or private research centers. publics ou privés. Highly transparent fluorotellurite glass-ceramics: structural investigations and luminescence properties Jean-Paul Laval1, Jean-René Duclère1, Vincent Couderc2, Mathieu Allix3, Cécile Genevois3, Vincent Sarou-Kanian3, Franck Fayon3, Pierre-Eugène Coulon4, Sébastien Chenu1, Maggy Colas1, -
Sintered Al2o3 Vs Cubic Materials
UNCLASSIFIED/UNLIMITED Physics and Technology of Transparent Ceramic Armor: Sintered Al2O3 vs Cubic Materials Andreas Krell, Thomas Hutzler, Jens Klimke Fraunhofer Institute of Ceramic Technologies and Sintered Materials Winterbergstrasse 28, 01277 Dresden, Germany [email protected] ABSTRACT Sintered sub-µm alumina (α-Al2O3) is the hardest transparent armor. However, its trigonal structure gives rise to a strong thickness effect that makes thicker components translucent. Cubic ceramics (no birefrin- gence!), on the other hand, are less hard but may exhibit an improved transmission. Known cubic armor ceramics are manufactured in a way resulting in coarse microstructures with low hardness. Therefore, a cubic sub-µm spinel was developed here that associates a high hardness > 14 GPa with an in-line transmission approaching the theoretical limit - with the consequence that the thickness effect becomes very small, and transparent components can be manufactured with several mm thickness without loss of transmissivity. Additionally, weight benefits at high protective strength are expected be- cause the hard components can be designed thinner than using known spinel or AlON grades. 1 INTRODUCTION The central difficulty in the development of transparent armor is that some thickness of the component is imperative for obtaining a high protective strength whereas, on the other hand, light transmission de- creases and specific weight increases with increasing thickness. The final goal is, therefore, a transparent material the high ballistic mass efficiency of which enables the design of thinner windows. This ballistic mass efficiency scales with the hardness of ceramic armor [1]. Sintered Al2O3 with sub-µm grain size is the hardest of all transparent armor (including sapphire).