Biomimetic Drill
Total Page:16
File Type:pdf, Size:1020Kb
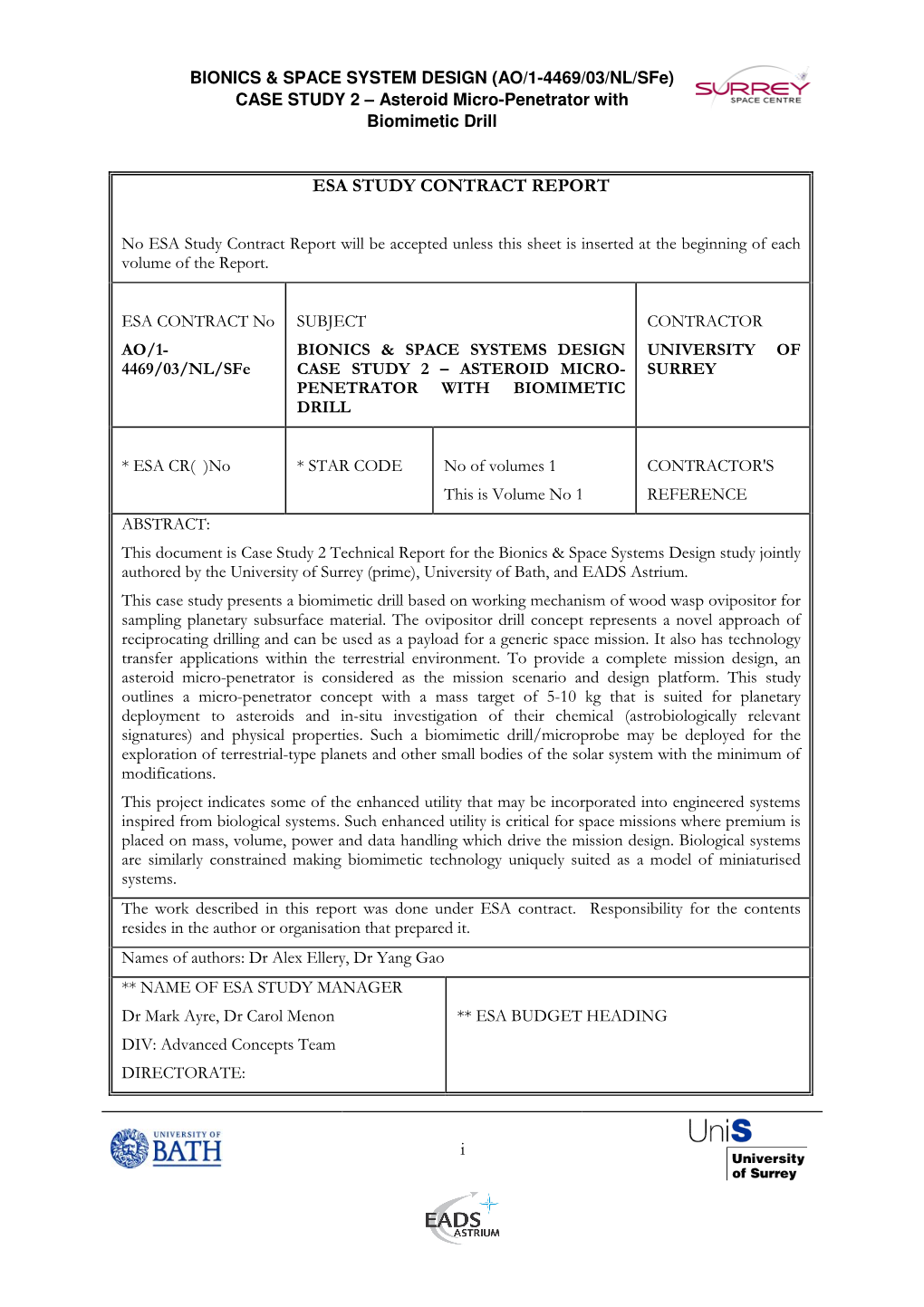
Load more
Recommended publications
-
Low-Energy Lunar Trajectory Design
LOW-ENERGY LUNAR TRAJECTORY DESIGN Jeffrey S. Parker and Rodney L. Anderson Jet Propulsion Laboratory Pasadena, California July 2013 ii DEEP SPACE COMMUNICATIONS AND NAVIGATION SERIES Issued by the Deep Space Communications and Navigation Systems Center of Excellence Jet Propulsion Laboratory California Institute of Technology Joseph H. Yuen, Editor-in-Chief Published Titles in this Series Radiometric Tracking Techniques for Deep-Space Navigation Catherine L. Thornton and James S. Border Formulation for Observed and Computed Values of Deep Space Network Data Types for Navigation Theodore D. Moyer Bandwidth-Efficient Digital Modulation with Application to Deep-Space Communication Marvin K. Simon Large Antennas of the Deep Space Network William A. Imbriale Antenna Arraying Techniques in the Deep Space Network David H. Rogstad, Alexander Mileant, and Timothy T. Pham Radio Occultations Using Earth Satellites: A Wave Theory Treatment William G. Melbourne Deep Space Optical Communications Hamid Hemmati, Editor Spaceborne Antennas for Planetary Exploration William A. Imbriale, Editor Autonomous Software-Defined Radio Receivers for Deep Space Applications Jon Hamkins and Marvin K. Simon, Editors Low-Noise Systems in the Deep Space Network Macgregor S. Reid, Editor Coupled-Oscillator Based Active-Array Antennas Ronald J. Pogorzelski and Apostolos Georgiadis Low-Energy Lunar Trajectory Design Jeffrey S. Parker and Rodney L. Anderson LOW-ENERGY LUNAR TRAJECTORY DESIGN Jeffrey S. Parker and Rodney L. Anderson Jet Propulsion Laboratory Pasadena, California July 2013 iv Low-Energy Lunar Trajectory Design July 2013 Jeffrey Parker: I dedicate the majority of this book to my wife Jen, my best friend and greatest support throughout the development of this book and always. -
Cross-References ASTEROID IMPACT Definition and Introduction History of Impact Cratering Studies
18 ASTEROID IMPACT Tedesco, E. F., Noah, P. V., Noah, M., and Price, S. D., 2002. The identification and confirmation of impact structures on supplemental IRAS minor planet survey. The Astronomical Earth were developed: (a) crater morphology, (b) geo- 123 – Journal, , 1056 1085. physical anomalies, (c) evidence for shock metamor- Tholen, D. J., and Barucci, M. A., 1989. Asteroid taxonomy. In Binzel, R. P., Gehrels, T., and Matthews, M. S. (eds.), phism, and (d) the presence of meteorites or geochemical Asteroids II. Tucson: University of Arizona Press, pp. 298–315. evidence for traces of the meteoritic projectile – of which Yeomans, D., and Baalke, R., 2009. Near Earth Object Program. only (c) and (d) can provide confirming evidence. Remote Available from World Wide Web: http://neo.jpl.nasa.gov/ sensing, including morphological observations, as well programs. as geophysical studies, cannot provide confirming evi- dence – which requires the study of actual rock samples. Cross-references Impacts influenced the geological and biological evolu- tion of our own planet; the best known example is the link Albedo between the 200-km-diameter Chicxulub impact structure Asteroid Impact Asteroid Impact Mitigation in Mexico and the Cretaceous-Tertiary boundary. Under- Asteroid Impact Prediction standing impact structures, their formation processes, Torino Scale and their consequences should be of interest not only to Earth and planetary scientists, but also to society in general. ASTEROID IMPACT History of impact cratering studies In the geological sciences, it has only recently been recog- Christian Koeberl nized how important the process of impact cratering is on Natural History Museum, Vienna, Austria a planetary scale. -
Information Summaries
TIROS 8 12/21/63 Delta-22 TIROS-H (A-53) 17B S National Aeronautics and TIROS 9 1/22/65 Delta-28 TIROS-I (A-54) 17A S Space Administration TIROS Operational 2TIROS 10 7/1/65 Delta-32 OT-1 17B S John F. Kennedy Space Center 2ESSA 1 2/3/66 Delta-36 OT-3 (TOS) 17A S Information Summaries 2 2 ESSA 2 2/28/66 Delta-37 OT-2 (TOS) 17B S 2ESSA 3 10/2/66 2Delta-41 TOS-A 1SLC-2E S PMS 031 (KSC) OSO (Orbiting Solar Observatories) Lunar and Planetary 2ESSA 4 1/26/67 2Delta-45 TOS-B 1SLC-2E S June 1999 OSO 1 3/7/62 Delta-8 OSO-A (S-16) 17A S 2ESSA 5 4/20/67 2Delta-48 TOS-C 1SLC-2E S OSO 2 2/3/65 Delta-29 OSO-B2 (S-17) 17B S Mission Launch Launch Payload Launch 2ESSA 6 11/10/67 2Delta-54 TOS-D 1SLC-2E S OSO 8/25/65 Delta-33 OSO-C 17B U Name Date Vehicle Code Pad Results 2ESSA 7 8/16/68 2Delta-58 TOS-E 1SLC-2E S OSO 3 3/8/67 Delta-46 OSO-E1 17A S 2ESSA 8 12/15/68 2Delta-62 TOS-F 1SLC-2E S OSO 4 10/18/67 Delta-53 OSO-D 17B S PIONEER (Lunar) 2ESSA 9 2/26/69 2Delta-67 TOS-G 17B S OSO 5 1/22/69 Delta-64 OSO-F 17B S Pioneer 1 10/11/58 Thor-Able-1 –– 17A U Major NASA 2 1 OSO 6/PAC 8/9/69 Delta-72 OSO-G/PAC 17A S Pioneer 2 11/8/58 Thor-Able-2 –– 17A U IMPROVED TIROS OPERATIONAL 2 1 OSO 7/TETR 3 9/29/71 Delta-85 OSO-H/TETR-D 17A S Pioneer 3 12/6/58 Juno II AM-11 –– 5 U 3ITOS 1/OSCAR 5 1/23/70 2Delta-76 1TIROS-M/OSCAR 1SLC-2W S 2 OSO 8 6/21/75 Delta-112 OSO-1 17B S Pioneer 4 3/3/59 Juno II AM-14 –– 5 S 3NOAA 1 12/11/70 2Delta-81 ITOS-A 1SLC-2W S Launches Pioneer 11/26/59 Atlas-Able-1 –– 14 U 3ITOS 10/21/71 2Delta-86 ITOS-B 1SLC-2E U OGO (Orbiting Geophysical -
Questioning the Surface of Mars As the 21St Century's Ultimate Pioneering Destination in Space
Questioning The Surface Of Mars As The 21st Century's Ultimate Pioneering Destination In Space Small Bodies Assessment Group Meeting #13 Washington D.C. 1 July 2015 Questioning Mars As The Ultimate Pioneering Destination In Space Background And Context • Foreseeable human-initiated activity in space can be divided into two categories - Exploring (e.g. Lewis & Clark ca. 1805): survey foreign territory + A major component of NASA's charter + Can be conducted by humans directly or by robots under human control + Virtual human presence is possible via tele-robotics stationed < 100,000 km away + Mars never approaches Earth closer than 56 million km - Pioneering (e.g. Pilgrims ca.1620): put down multi-generation roots in foreign territory + NOT in NASA's charter + MUST be conducted by humans in situ and ultimately return sustained profits + Any examples to date are dubious and Earth-centered (e.g. communication satellites) • Mars is widely accepted as the ultimate 21st century pioneering destination in space - Why would 202,586* adults volunteer in 2013 for a one-way trip to the surface of Mars? - What are potential obstacles to pioneering the surface of Mars? - Might there be more accessible and hospitable pioneering destinations than Mars? * The number of applications actually completed and submitted to Mars One was reported in 2015 to be 4227. Daniel R. Adamo ([email protected]) 1 1 July 2015 Questioning Mars As The Ultimate Pioneering Destination In Space History† Indicates Humans Pioneer For Compelling Reasons • Escape from war, starvation, -
Planetary Defence Activities Beyond NASA and ESA
Planetary Defence Activities Beyond NASA and ESA Brent W. Barbee 1. Introduction The collision of a significant asteroid or comet with Earth represents a singular natural disaster for a myriad of reasons, including: its extraterrestrial origin; the fact that it is perhaps the only natural disaster that is preventable in many cases, given sufficient preparation and warning; its scope, which ranges from damaging a city to an extinction-level event; and the duality of asteroids and comets themselves---they are grave potential threats, but are also tantalising scientific clues to our ancient past and resources with which we may one day build a prosperous spacefaring future. Accordingly, the problems of developing the means to interact with asteroids and comets for purposes of defence, scientific study, exploration, and resource utilisation have grown in importance over the past several decades. Since the 1980s, more and more asteroids and comets (especially the former) have been discovered, radically changing our picture of the solar system. At the beginning of the year 1980, approximately 9,000 asteroids were known to exist. By the beginning of 2001, that number had risen to approximately 125,000 thanks to the Earth-based telescopic survey efforts of the era, particularly the emergence of modern automated telescopic search systems, pioneered by the Massachusetts Institute of Technology’s (MIT’s) LINEAR system in the mid-to-late 1990s.1 Today, in late 2019, about 840,000 asteroids have been discovered,2 with more and more being found every week, month, and year. Of those, approximately 21,400 are categorised as near-Earth asteroids (NEAs), 2,000 of which are categorised as Potentially Hazardous Asteroids (PHAs)3 and 2,749 of which are categorised as potentially accessible.4 The hazards posed to us by asteroids affect people everywhere around the world. -
The Pancam Instrument for the Exomars Rover
ASTROBIOLOGY ExoMars Rover Mission Volume 17, Numbers 6 and 7, 2017 Mary Ann Liebert, Inc. DOI: 10.1089/ast.2016.1548 The PanCam Instrument for the ExoMars Rover A.J. Coates,1,2 R. Jaumann,3 A.D. Griffiths,1,2 C.E. Leff,1,2 N. Schmitz,3 J.-L. Josset,4 G. Paar,5 M. Gunn,6 E. Hauber,3 C.R. Cousins,7 R.E. Cross,6 P. Grindrod,2,8 J.C. Bridges,9 M. Balme,10 S. Gupta,11 I.A. Crawford,2,8 P. Irwin,12 R. Stabbins,1,2 D. Tirsch,3 J.L. Vago,13 T. Theodorou,1,2 M. Caballo-Perucha,5 G.R. Osinski,14 and the PanCam Team Abstract The scientific objectives of the ExoMars rover are designed to answer several key questions in the search for life on Mars. In particular, the unique subsurface drill will address some of these, such as the possible existence and stability of subsurface organics. PanCam will establish the surface geological and morphological context for the mission, working in collaboration with other context instruments. Here, we describe the PanCam scientific objectives in geology, atmospheric science, and 3-D vision. We discuss the design of PanCam, which includes a stereo pair of Wide Angle Cameras (WACs), each of which has an 11-position filter wheel and a High Resolution Camera (HRC) for high-resolution investigations of rock texture at a distance. The cameras and electronics are housed in an optical bench that provides the mechanical interface to the rover mast and a planetary protection barrier. -
Photographs Written Historical and Descriptive
CAPE CANAVERAL AIR FORCE STATION, MISSILE ASSEMBLY HAER FL-8-B BUILDING AE HAER FL-8-B (John F. Kennedy Space Center, Hanger AE) Cape Canaveral Brevard County Florida PHOTOGRAPHS WRITTEN HISTORICAL AND DESCRIPTIVE DATA HISTORIC AMERICAN ENGINEERING RECORD SOUTHEAST REGIONAL OFFICE National Park Service U.S. Department of the Interior 100 Alabama St. NW Atlanta, GA 30303 HISTORIC AMERICAN ENGINEERING RECORD CAPE CANAVERAL AIR FORCE STATION, MISSILE ASSEMBLY BUILDING AE (Hangar AE) HAER NO. FL-8-B Location: Hangar Road, Cape Canaveral Air Force Station (CCAFS), Industrial Area, Brevard County, Florida. USGS Cape Canaveral, Florida, Quadrangle. Universal Transverse Mercator Coordinates: E 540610 N 3151547, Zone 17, NAD 1983. Date of Construction: 1959 Present Owner: National Aeronautics and Space Administration (NASA) Present Use: Home to NASA’s Launch Services Program (LSP) and the Launch Vehicle Data Center (LVDC). The LVDC allows engineers to monitor telemetry data during unmanned rocket launches. Significance: Missile Assembly Building AE, commonly called Hangar AE, is nationally significant as the telemetry station for NASA KSC’s unmanned Expendable Launch Vehicle (ELV) program. Since 1961, the building has been the principal facility for monitoring telemetry communications data during ELV launches and until 1995 it processed scientifically significant ELV satellite payloads. Still in operation, Hangar AE is essential to the continuing mission and success of NASA’s unmanned rocket launch program at KSC. It is eligible for listing on the National Register of Historic Places (NRHP) under Criterion A in the area of Space Exploration as Kennedy Space Center’s (KSC) original Mission Control Center for its program of unmanned launch missions and under Criterion C as a contributing resource in the CCAFS Industrial Area Historic District. -
2004-118.Pdf
East MeetsWest in Near-Earth The Hubble Space Telescope Space SpaceTechnologies for Building Making the Most of Earth Observation Data The Hubble Space Telescope ESA's Cooperation with International Partners - Present and Future - Export Control lssues Nino Panagia Andre Farand & Ukike Bohlmann 49 ESA Reaches Out into Deep Space from Spain lntellectual Property Rights -The New Cebreros Station - A New Regime in ESA Contracts Valeriano Claros, Gisela Siiss & Manfred Warhaut tt Karl Eisermann & Christian Grafd 55 East Meets West in Near-Earth Space Programmes in Progress bU - Double Star Bodo Gramkow et al. z.t News - In Brief 76 Making the Most of Earth Observation with Publications 82 Data Assimilation Alan O'Neill, Pierre-Philippe Mathieu & Claus Zehner JJ Space Technologies for the Building Sector Fritz Gamoe 41 eso bulletin ll8-moy 2004 For over twenty yeors Gore Spoce Wire ond Cobies hcve contributed to the success of mony spoce missions, slch os Moon Londing, Spcceob, EURECA, ERSI + 2, lfolsol, SAX, SPCT, lSC, Envisot, XMM, Metop, Integrol, scienfific reseorch in spoce, Co,.lmbus As o speciol cob e supplier we support you in p onning the nexf sfep inlo spoce Coll us now. EORE IEI + 49/91 44/6 Al O Creative Technologies FAX.+ 49/91 44/6a l4 53 Worldwide e ectronics europe@w gore com www goree ecfron co com Our spoce communicotion scenqrio covers the whole ronge of sotellite ond spocecroh opplicotions: Telecommunicotions, Eorth Observotion, Science, Spoce Inlrostructure ond Novigotion. As on experienced developer & supplier of On-Boord TTC & Doto Tronsmission, Pqssive Microwoves, Digitol Processing Units. For over fifteen yeors, Alcotel Espocio hos contributed to the success of more thon 50 progroms sotellites Alcotel Espocio is o Sponish subsidiory compony of Alcotel Spoce BROADEN YOUR IIFE Nino Panogio Spoce Telexope Srience Inslilule, ISA Direclorole of Scientific Progrommes, Boltimore, USA Hubble role in n of the mosl importonl ond prolilic spoce oslronomy nissions of oll time. -
Apollo Over the Moon: a View from Orbit (Nasa Sp-362)
chl APOLLO OVER THE MOON: A VIEW FROM ORBIT (NASA SP-362) Chapter 1 - Introduction Harold Masursky, Farouk El-Baz, Frederick J. Doyle, and Leon J. Kosofsky [For a high resolution picture- click here] Objectives [1] Photography of the lunar surface was considered an important goal of the Apollo program by the National Aeronautics and Space Administration. The important objectives of Apollo photography were (1) to gather data pertaining to the topography and specific landmarks along the approach paths to the early Apollo landing sites; (2) to obtain high-resolution photographs of the landing sites and surrounding areas to plan lunar surface exploration, and to provide a basis for extrapolating the concentrated observations at the landing sites to nearby areas; and (3) to obtain photographs suitable for regional studies of the lunar geologic environment and the processes that act upon it. Through study of the photographs and all other arrays of information gathered by the Apollo and earlier lunar programs, we may develop an understanding of the evolution of the lunar crust. In this introductory chapter we describe how the Apollo photographic systems were selected and used; how the photographic mission plans were formulated and conducted; how part of the great mass of data is being analyzed and published; and, finally, we describe some of the scientific results. Historically most lunar atlases have used photointerpretive techniques to discuss the possible origins of the Moon's crust and its surface features. The ideas presented in this volume also rely on photointerpretation. However, many ideas are substantiated or expanded by information obtained from the huge arrays of supporting data gathered by Earth-based and orbital sensors, from experiments deployed on the lunar surface, and from studies made of the returned samples. -
General Assembly Distr.: General 7 January 2005
United Nations A/AC.105/839 General Assembly Distr.: General 7 January 2005 Original: English Committee on the Peaceful Uses of Outer Space Scientific and Technical Subcommittee Forty-second session Vienna, 21 February-4 March 2004 Item 10 of the provisional agenda∗ Near-Earth objects Information on research in the field of near-Earth objects carried out by international organizations and other entities Note by the Secretariat Contents Page I. Introduction ................................................................... 2 II. Replies received from international organizations and other entities ..................... 2 European Space Agency ......................................................... 2 The Spaceguard Foundation ...................................................... 17 __________________ ∗ A/AC.105/C.1/L.277. V.05-80067 (E) 010205 020205 *0580067* A/AC.105/839 I. Introduction In accordance with the agreement reached at the forty-first session of the Scientific and Technical Subcommittee (A/AC.105/823, annex II, para. 18) and endorsed by the Committee on the Peaceful Uses of Outer Space at its forty-seventh session (A/59/20, para. 140), the Secretariat invited international organizations, regional bodies and other entities active in the field of near-Earth object (NEO) research to submit reports on their activities relating to near-Earth object research for consideration by the Subcommittee. The present document contains reports received by 17 December 2004. II. Replies received from international organizations and other entities European Space Agency Overview of activities of the European Space Agency in the field of near-Earth object research: hazard mitigation Summary 1. Near-Earth objects (NEOs) pose a global threat. There exists overwhelming evidence showing that impacts of large objects with dimensions in the order of kilometres (km) have had catastrophic consequences in the past. -
Connecting @Ll Space People Welcome Message 2
Connecting @ll Space People Welcome Message 2 IAF 2018 Events Overview 3 IAF General Assembly 4 ISF 2017 6 IAF Spring Meetings 2018 8 GLAC 2018 9 IAC 2018 10 Overview 11 Plenaries 13 Highlight Lectures 20 Late Breaking News 23 IAF Global Networking Forum (GNF) 24 IAC Special Sessions 37 IAF IDEA “3G” Diversity Events 44 IAC Hosts Summit 46 9th IAF International Meeting for Members 48 of Parliaments YPP Networking Reception 50 Emerging Space Leaders 51 Grant Programme (ESL Grants) Press Conference: Upcoming Global Conference 52 on Space for Emerging Countries, GLEC 2019 ISF 2018 54 IAF Committees’ Reports 56 Technical Committees 57 Administrative Committees 78 Published by the International Astronautical Federation (IAF) 3rd Issue - February 2019 IAF 2018 Activities 80 Copyright © International Astronautical Federation. Other 2018 Events 80 All rights reserved. No part of this magazine may be reproduced or transmitted by any form or by any The International Astronautical Federation 83 means, electronical or mechanical, including photocopying or recording by any information storage or retrieval system without prior written permission from the publishers. CONTENTS IAF 2018 Events Overview Welcome Message Spring has already event in Uruguay. For three days, than 10,000 attendees came to Meetings begun, but experts gathered in Montevideo witness this exceptional event. 2018 2019 we can look to discuss space applications back at 2018 as a very impressive with a specific focus on emerging The majority of IAF publications and successful year. This publica- space nations and Latin America. and for the first time, the IAC tion, the IAF Highlights, is sum- Final Programmes, have been marizing the main IAF events The 69th International Astro- printed in recycled paper this and activities that took place. -
Proceedings of the 2018 Conference on Adding Value and Preserving Data
Conference Proceedings RAL-CONF-2018-001 PV2018: Proceedings of the 2018 conference on adding value and preserving data Harwell, UK 15th-17th May, 2018 Esther Conway (editor), Kate Winfield (editorial assistant) May 2018 ©2018 Science and Technology Facilities Council This work is licensed under a Creative Commons Attribution 4.0 Unported License. Enquiries concerning this report should be addressed to: RAL Library STFC Rutherford Appleton Laboratory Harwell Oxford Didcot OX11 0QX Tel: +44(0)1235 445384 Fax: +44(0)1235 446403 email: [email protected] Science and Technology Facilities Council reports are available online at: http://epubs.stfc.ac.uk ISSN 1362-0231 Neither the Council nor the Laboratory accept any responsibility for loss or damage arising from the use of information contained in any of their reports or in any communication about their tests or investigations. Proceedings of the 2018 conference on adding value and preserving data This publication is a Conference report published by the This publication is a Conference report published by the Science and Technology (STFC) Library and Information Service. The scientific output expressed does not imply a policy position of STFC. Neither STFC nor any person acting on behalf of the Commission is responsible for the use that might be made of this publication. Contact information Name: Esther Conway Address: STFC, Rutherford Appleton Laboratory Harwell, Oxon, UK Email: [email protected] Tel.: +44 01235 446367 STFC https://www.stfc.ac.uk RAL-CONF-2018-001 ISSN- 1362-0231. Preface The PV2018 Conference welcomes you to its 9th edition, to be held 15th – 17th May 2018 at the Rutherford Appleton Laboratory, Harwell Space Cluster (UK), hosted by the UK Space Agency and jointly organised by STFC, NCEO and the Satellite Applications Catapult.