Development of a Single Emitter Ionic Liquid Ion Source Research Platform
Total Page:16
File Type:pdf, Size:1020Kb
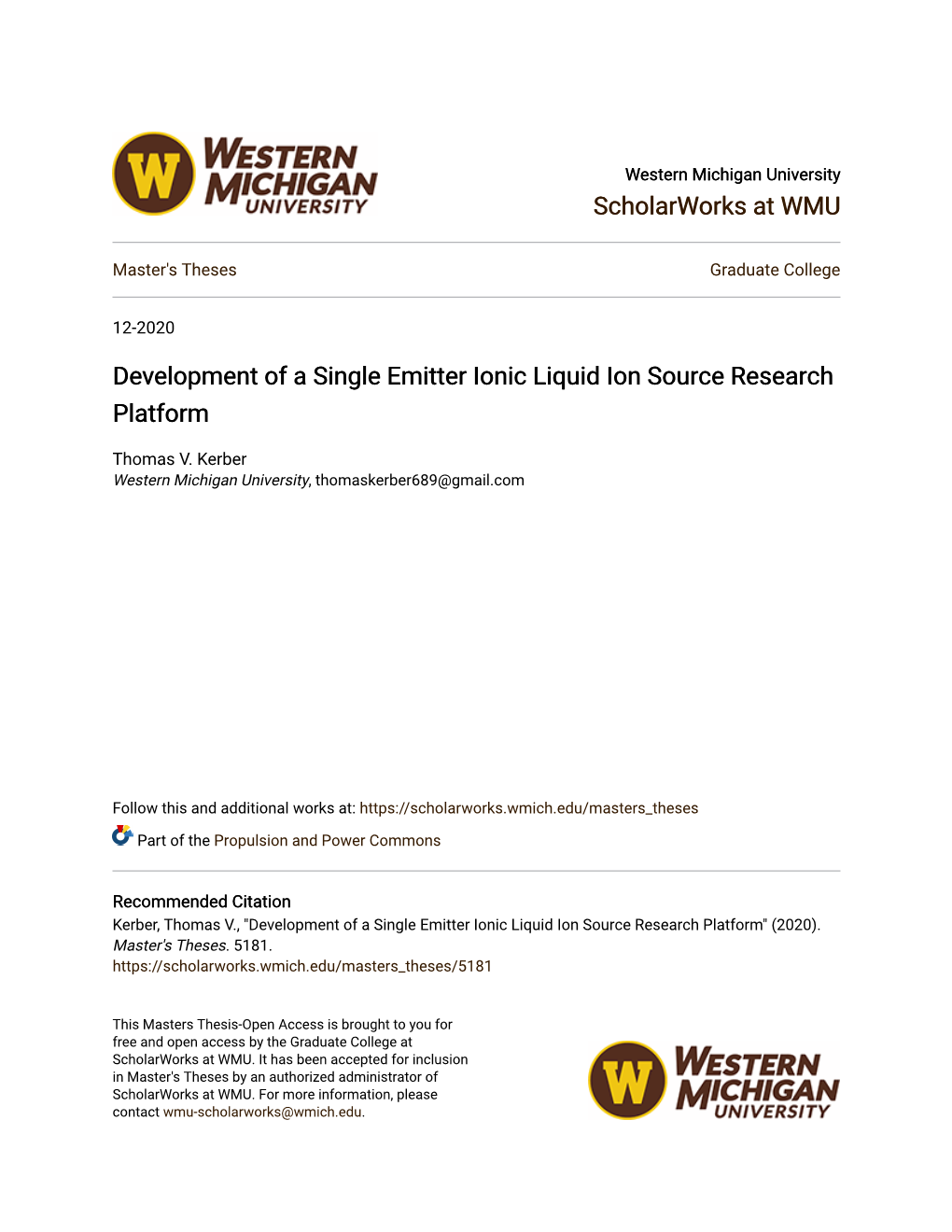
Load more
Recommended publications
-
Progress on Colloid Micro-Thruster Research and Flight Testing
PROGRESS ON COLLOID MICRO-THRUSTER RESEARCH AND FLIGHT TESTING F REDDY M ATHIAS P RANAJAYA PROF. MARK CAPPELLI, ADVISOR Space Systems Development Laboratory Department of Aeronautics and Astronautics, Stanford University Plasma Dynamic Laboratory Department of Mechanical Engineering, Stanford University ABSTRACT - Electric propulsion devices are know for their high specific impulses, which 1. INTRODUCTION makes them very appealing to space mission requiring ultimate utilization of the limited Space mission designers have long been resources on board the spacecraft. relying on electric propulsion because of its characteristic of high specific impulse, Advances in microelectronics have allowed allowing higher total delta-V, which makes it increased functionality while reducing the suitable for long space missions or for sizes of the spacecraft. However this has not spacecraft with limited fuel storage capacity. been entirely true for propulsion units. Colloid Despite of this advantage, the high power Micro-Thruster held the promise for micro- consumption and massive power supply and nanosatellite propulsion application requirements have made electric propulsion because of their size, low cost, integrated option unattractive for 100kg-class package, high efficiency, and custom microsatellites and 10-kg class nanosatellites. configurability to fit a specific application. Colloid Micro-Thruster technology is expected This paper outlines the renewed research to satisfy the need for high-performance efforts on Colloid Thruster, in an attempt to propulsion units for small spacecraft. Recent understand the underlying principles and to study by Mueller, 1997 [1] concluded that “… uncover its true potential. A one-nozzle and a of all micro-electric primary propulsion 100-nozzle prototype have been built and options reviewed, Colloid Thrusters are quite tested. -
Space Propulsion Technology for Small Spacecraft
Space Propulsion Technology for Small Spacecraft The MIT Faculty has made this article openly available. Please share how this access benefits you. Your story matters. Citation Krejci, David, and Paulo Lozano. “Space Propulsion Technology for Small Spacecraft.” Proceedings of the IEEE, vol. 106, no. 3, Mar. 2018, pp. 362–78. As Published http://dx.doi.org/10.1109/JPROC.2017.2778747 Publisher Institute of Electrical and Electronics Engineers (IEEE) Version Author's final manuscript Citable link http://hdl.handle.net/1721.1/114401 Terms of Use Creative Commons Attribution-Noncommercial-Share Alike Detailed Terms http://creativecommons.org/licenses/by-nc-sa/4.0/ PROCC. OF THE IEEE, VOL. 106, NO. 3, MARCH 2018 362 Space Propulsion Technology for Small Spacecraft David Krejci and Paulo Lozano Abstract—As small satellites become more popular and capa- While designations for different satellite classes have been ble, strategies to provide in-space propulsion increase in impor- somehow ambiguous, a system mass based characterization tance. Applications range from orbital changes and maintenance, approach will be used in this work, in which the term ’Small attitude control and desaturation of reaction wheels to drag com- satellites’ will refer to satellites with total masses below pensation and de-orbit at spacecraft end-of-life. Space propulsion 500kg, with ’Nanosatellites’ for systems ranging from 1- can be enabled by chemical or electric means, each having 10kg, ’Picosatellites’ with masses between 0.1-1kg and ’Fem- different performance and scalability properties. The purpose tosatellites’ for spacecrafts below 0.1kg. In this category, the of this review is to describe the working principles of space popular Cubesat standard [13] will therefore be characterized propulsion technologies proposed so far for small spacecraft. -
Final Report Microthrust
Date: 11 Mar 2014 Issue: 1 Rev : 1 Page: 1 of 31 Final Report MicroThrust PROJECT FINAL REPORT Grant Agreement number: 263035 Project acronym: MicroThrust Project title: MEMS-‐Based Electric Micropropulsion for Small Spacecraft to Enable Robotic Space Exploration and Space Science Funding Scheme: SP1-‐Cooperation Period covered: From 01.12.2010 to 30 .11.2013 Name, title and organization of the scientific Prof. Herbert Shea, École Polytechnique representative of the project’s coordinator: Fédéral de Lausanne Tel: +41-‐21-‐693-‐6663 Fax: +41-‐21-‐693-‐6663 E-‐mail: [email protected] Project website address: http://www.microthrust.eu Date: 11 Mar 2014 Issue: 1 Rev : 1 Page: 2 of 31 Final Report MicroThrust Final publishable summary report of MicroThrust Executive Summary In recent years, the interest in small and low cost satellites has increased worldwide. Numerous small and low-‐cost spacecraft have been launched, often based on the CubeSat format. There is an emerging recognition that nano-‐satellites (1-‐10 kg) and micro-‐satellites (10-‐100 kg) will play a major scientific role in space exploration. A critical enabling technology that is required to revolutionize planetary space exploration with small satellites is a suitable efficient compact propulsion system. Under the constraints of high delta-‐V missions, this necessarily leads to an electric propulsion requirement. The MicroThrust consortium has developed a breadboard of a highly efficient microfabricated electric propulsion system prototype to -‐ enable sub 50 kg satellites to perform large orbit changes, thus allowing small satellites to perform exploration missions and mission chitectures ar that were not possible up till now. -
IGNITION! an Informal History of Liquid Rocket Propellants by John D
IGNITION! U.S. Navy photo This is what a test firing should look like. Note the mach diamonds in the ex haust stream. U.S. Navy photo And this is what it may look like if something goes wrong. The same test cell, or its remains, is shown. IGNITION! An Informal History of Liquid Rocket Propellants by John D. Clark Those who cannot remember the past are condemned to repeat it. George Santayana RUTGERS UNIVERSITY PRESS IS New Brunswick, New Jersey Copyright © 1972 by Rutgers University, the State University of New Jersey Library of Congress Catalog Card Number: 72-185390 ISBN: 0-8135-0725-1 Manufactured in the United Suites of America by Quinn & Boden Company, Inc., Rithway, New Jersey This book is dedicated to my wife Inga, who heckled me into writing it with such wifely re marks as, "You talk a hell of a fine history. Now set yourself down in front of the typewriter — and write the damned thing!" In Re John D. Clark by Isaac Asimov I first met John in 1942 when I came to Philadelphia to live. Oh, I had known of him before. Back in 1937, he had published a pair of science fiction shorts, "Minus Planet" and "Space Blister," which had hit me right between the eyes. The first one, in particular, was the earliest science fiction story I know of which dealt with "anti-matter" in realistic fashion. Apparently, John was satisfied with that pair and didn't write any more s.f., kindly leaving room for lesser lights like myself. -
Electric Propulsion Research and Development at NASA
SP2018 00389 Electric Propulsion Research and Development at NASA George Schmidt(1), David Jacobson(1), Michael Patterson(1), Gani Ganapathi(2), John Brophy(2), and Richard Hofer(2) (1)NASA Glenn Research Center, 21000 Brookpark Rd., Cleveland, OH 44135 USA (2)NASA Jet Propulsion Laboratory, Pasadena, CA 91109 USA KEYWORDS: electric propulsion, ion thruster, development for its potential to provide significant Hall thruster, cathode, power processing unit, benefits for future deep-space and astrophysics xenon, iodine, CubeSat, feed system, testing applications. SMD’s current focus is on the flight development of NASA’s Evolutionary Xenon ABSTRACT: Thruster - Commercial (NEXT-C). This project’s goal is to develop and flight qualify two ion Electric propulsion (EP) is an important thruster/power processing unit (PPU) strings, technology for NASA. It has played a major role based on the NEXT technology development on three missions, that is Deep Space 1, Dawn work completed in 2012. NEXT-C hardware is and Space Technology 7, and it is planned for being considered for multiple science missions use on many more. The ion propulsion system including the Double Asteroid and Redirection for the ongoing Dawn mission has achieved Test (DART) mission led by the Applied Physics several notable accomplishments, including Laboratory (APL). SMD is also continuing to providing a total velocity change (V) of over 11 support the HiVHAc Hall thruster system project km/s to the spacecraft. As a result of these that was started in 2002. The focus now is on successes, solar electric propulsion (SEP) is now development of a flexible 4.5 kW prototype PPU broadly recognized as an essential technology for capable of operating with several different NASA both robotic and human exploration. -
A Study of a Low-Power Microwave Arcjet Thruster Using Ammonia Propellant
A Study of a Low-Power Microwave Arcjet Thruster Using Ammonia Propellant Jorge Delgado, McNair Scholar, Pennsylvania State University Faculty Research Adviser Dr. Michael M. Micci, Professor of Aerospace Engineering Pennsylvania State University Research Advisers Dr. Sven G. Bilén, Assistant Professor of Electrical Engineering Benjamin Welander, Masters Candidate Pennsylvania State University Abstract A low-power microwave arjet thruster was studied using ammonia gas as propellant. The purpose of the project was to generate ammonia plasma using a 7.5 GHz magnetron and a cylindrical cavity thruster, which is resonant in the TM001 mode [1]. The desired pressure was atmospheric or above while generating a thrust of roughly 20mN and an Isp of about 500s operating at low power (<100 kW). Introduction/Overview of Electric Propulsion Two main parameters used to describe a rocket engine are the thrust and the specific impulse (Isp) generated by the rocket. Thrust is an exchange of momentum, momentum from the exhaust is transferred to the space vehicle which allows is to propel through space. Below is the derivation of the basic thrust equation where P = momentum, mdot = mass flow, ve = exhaust velocity, and FTHRUST = thrust force. P = mv dP = dm ve dP/dt = dm/dt ve FTHRUST = mdot ve Specific impulse is a performance parameter used for rocket engines, which compares the thrust to the amount of propellant used. The equation for the Isp is shown below where FTHRUST = thrust force, mdot = mass flow, and g0 = gravitational constant. Isp = Fthrust / mdot * g0 91 Though most space vehicles currently use chemical propulsive devices, the substantial growth of Earth-orbiting satellites for communication and surveillance has sparked a new and intense interest in electric propulsive (EP) devices [2]. -
Emission Modes in Electrospray Thrusters Operating with High Conductivity Ionic Liquids
aerospace Article Emission Modes in Electrospray Thrusters Operating with High Conductivity Ionic Liquids Nolan M. Uchizono 1,† , Adam L. Collins 1,† , Anirudh Thuppul 1,† , Peter L. Wright 1,† , Daniel Q. Eckhardt 2 , John Ziemer 3 and Richard E. Wirz 1,*,† 1 Plasma & Space Propulsion Laboratory, UCLA Mechanical and Aerospace Engineering, 420 Westwood Plaza, Los Angeles, CA 90095, USA; [email protected] (N.M.U.); [email protected] (A.L.C.); [email protected] (A.T.); [email protected] (P.L.W.) 2 Electric Propulsion Lead, In-Space Propulsion Branch (RQRS), Air Force Research Laboratory, Edwards AFB, CA 93524, USA; [email protected] 3 LISA Microthruster Technology Lead, NASA Jet Propulsion Laboratory, California Institute of Technology, Pasadena, CA 91109, USA; [email protected] * Correspondence: [email protected] † Current address: UCLA Department of Mechanical and Aerospace Engineering, 420 Westwood Plaza, Los Angeles, CA 90095, USA. Received: 24 August 2020; Accepted: 22 September 2020; Published: 25 September 2020 Abstract: Electrospray thruster life and mission performance are strongly influenced by grid impingement, the extent of which can be correlated with emission modes that occur at steady-state extraction voltages, and thruster command transients. Most notably, we experimentally observed skewed cone-jet emission during steady-state electrospray thruster operation, which leads to the definition of an additional grid impingement mechanism that we termed “tilted emission”. Long distance microscopy was used in conjunction with high speed videography to observe the emission site of an electrospray thruster operating with an ionic liquid propellant (EMI-Im). During steady-state thruster operation, no unsteady electrohydrodynamic emission modes were observed, though the conical meniscus exhibited steady off-axis tilt of up to 15◦. -
Colloid Thruster for Precision Pointing V4.Pptx
National Aeronautics and Space Administration Jet Propulsion Laboratory California Institute of Technology ColloidPasadena, California Micro-Newton Thrusters For Precision Attitude Control John Ziemer, Colleen Marrese-Reading, and Thomas Randolph Jet Propulsion Laboratory, California Institute of Technology Vlad Hruby and Nathaniel Demmons, Busek Company, Inc. April 7, 2017 Cleared for Public Release CL#17-2067 © 2017 California Institute of Technology. Government sponsorship acknowledged. National Aeronautics and Space Administration Jet Propulsion Laboratory California Institute of Technology Main S/C Disturbance: Solar Pressure Pasadena, California » 30 µN ~ 0.1 µN 2 National Aeronautics and Space Administration Jet Propulsion Laboratory California Institute of Technology Colloid Thruster Technology Pasadena, California • Colloid Thrusters emit charged droplets that are electrostatically accelerated to produce thrust 1.5 0.5 Thrust µ IB × VB • Current and voltage are controlled independently by adjusting the flow rate and beam voltage • Precise control of IB (~ µA) and VB (~ kV) facilitates the delivery of micronewton level thrust with better than 0.1 µN precision • The exhaust beam is positively charged, well-defined (all charged Images courtesy of Busek Co. particles), and neutralized by a cathode/electron source if needed 3 National Aeronautics and Space Administration Colloid Thruster History and Technical Jet Propulsion Laboratory California Institute of Technology Pasadena, California Challenges 2004 Emitters, Bubbles and Lifetime -
Disparate Electrospray Systems for Undergraduate and Graduate Education
Paper ID #26529 Disparate Electrospray Systems for Undergraduate and Graduate Education Dr. Amelia Greig, California Polytechnic State University, San Luis Obispo Dr Amelia Greig has degrees in Mechanical and Aerospace Engineering, and Science from the University of Adelaide, and a PhD in Physics from the Australian National University. She teaches courses in space- craft propulsion and the space environment at Cal Poly San Luis Obispo, and also leads the Aerospace Engineering Department’s micro-propulsion research activities. Mr. Alex Powaser, California Polytechnic State University, San Luis Obispo Alex is a graduate student in Aerospace Engineering at California Polytechnic State Universtiy, San Luis Obispo. His thesis work is on developing a colloid thruster to be used at Cal Poly’s undergraduate labo- ratory. While being a student, Alex enjoys teaching various labs and lectures for the university as well. Outside of the classroom, he enjoys an active leadership role in CRU (formally known as Campus Cru- sade for Christ) and other hobbies such as playing guitar, being an amateur woodworker, and exploring California’s Central Coast with his fiancee.´ Douglas Howe, California Polytechnic State University, San Luis Obispo Mr. Will Alan McGehee, California Polytechnic State University Will McGehee is currently attending California Polytechnic State University (Cal Poly) in pursuit of his Master’s Degree in Aerospace Engineering. He completed his undergraduate degree in Aerospace Engineering at Cal Poly as well. His thesis encompasses the design and initial operational testing of an electrospray (aka colloid) thruster for current and future research efforts at Cal Poly in the field of micro- propulsion. He has experience in electrical systems, micro-fabrication, and diagnostic techniques used in testing of micro-propulsion thrusters. -
Porous Emitter Colloid Thruster Performance Characterization Using Optical Techniques Eric T
Air Force Institute of Technology AFIT Scholar Theses and Dissertations Student Graduate Works 3-21-2013 Porous Emitter Colloid Thruster Performance Characterization Using Optical Techniques Eric T. Wolf Follow this and additional works at: https://scholar.afit.edu/etd Part of the Aerospace Engineering Commons Recommended Citation Wolf, Eric T., "Porous Emitter Colloid Thruster Performance Characterization Using Optical Techniques" (2013). Theses and Dissertations. 848. https://scholar.afit.edu/etd/848 This Thesis is brought to you for free and open access by the Student Graduate Works at AFIT Scholar. It has been accepted for inclusion in Theses and Dissertations by an authorized administrator of AFIT Scholar. For more information, please contact [email protected]. POROUS EMITTER COLLOID THRUSTER PERFORMANCE CHARACTERIZATION USING OPTICAL TECHNIQUES THESIS Eric T. Wolf, Captain, USAF AFIT-ENY-13-M-36 DEPARTMENT OF THE AIR FORCE AIR UNIVERSITY AIR FORCE INSTITUTE OF TECHNOLOGY Wright-Patterson Air Force Base, Ohio APPROVED FOR PUBLIC RELEASE; DISTRIBUTION UNLIMITED. The views expressed in this thesis are those of the author and do not reflect the official policy or position of the United States Air Force, Department of Defense, or the United States Government. This material is declared a work of the U.S. Government and is not subject to copyright protection in the United States. AFIT-ENY-13-M-36 POROUS EMITTER COLLOID THRUSTER PERFORMANCE CHARACTERIZATION USING OPTICAL TECHNIQUES THESIS Presented to the Faculty Department of Aeronautics and Astronautics Graduate School of Engineering and Management Air Force Institute of Technology Air University Air Education and Training Command In Partial Fulfillment of the Requirements for the Degree of Master of Science in Aeronautical Engineering Eric T. -
Game-Changing Technologies for the Lunar Architecture
Technology Horizons: Game-Changing Technologies for the Lunar Architecture September 2009 TABLE OF CONTENTS Executive Summary 3 Goals 3 Process 3 Game-Changing Technologies 3 Technology Watch List 7 Next Steps 7 Introduction 8 What is Game-Changing? 9 Types of Technologies 10 Methodology 11 Top Game-Changing Technology Areas 16 Energy Storage Technologies 17 Anti-Radiation Drugs 22 In-Situ Resource Utilization (ISRU) Manufacturing 26 Radiation Shielding 29 Advanced Pressure Garment Technologies 34 Nuclear Power Technologies 39 Advanced Nanotube-based Materials 43 Next Generation Fuel Cells 47 Next Generation Solar Cells 51 Advanced Cryogenic Technologies 55 Printing Manufacturing 59 Advanced Coatings, Adhesives, and Self-Healing Materials 62 Advanced Electric Propulsion 66 Heat Transfer Materials 70 Autonomous Systems and Vehicle Control 73 Long Distance Power Transmission 77 Advanced Chemical Propulsion 81 Massive Online Collaborative Environments 86 Emerging Communications Systems 90 Technology Watch List 94 Next Steps 96 Appendices 99 Appendix A: Technology Area Quad Charts 99 Appendix B: Sources 144 Appendix C: Initial List of Technologies 145 Appendix D: Acknowledgements___________________________149 September 2009 Page 2 1.0 EXECUTIVE SUMMARY NASA is currently designing a plan to return to the Moon by 2020 and sustain a human presence. While still in evolution, the current lunar architecture includes the vehicles and systems to travel to, explore, build, and sustain an outpost on the Moon. A lunar outpost mission will require technology from across the spectrum of human activity, including health, automobiles, electronics, information technologies, energy generation and storage, materials science, manufacturing, and propulsion, to name a few. Unlike relatively specialized space activities, such as interplanetary probes, the broad base of activities and capabilities required for a human presence on the Moon draws from capabilities across the economy. -
Colloid Thruster to Teach Advanced Electric Propulsion Techniques to Post-Secondary Students
COLLOID THRUSTER TO TEACH ADVANCED ELECTRIC PROPULSION TECHNIQUES TO POST-SECONDARY STUDENTS A Thesis presented to the Faculty of California Polytechnic State University, San Luis Obispo In Partial Fulfillment of the Requirements for the Degree Master of Science in Aerospace Engineering by Alexander M. Powaser June 2019 c 2019 Alexander M. Powaser ALL RIGHTS RESERVED ii COMMITTEE MEMBERSHIP TITLE: Colloid Thruster to Teach Advanced Electric Propulsion Techniques to Post- Secondary Students AUTHOR: Alexander M. Powaser DATE SUBMITTED: June 2019 COMMITTEE CHAIR: Amelia Greig, Ph.D. Assistant Professor of Aerospace Engineering COMMITTEE MEMBER: Kira Abercromby, Ph.D. Associate Professor of Aerospace Engineering COMMITTEE MEMBER: Karl Saunders, Ph.D. Professor of Physics, Department Chair COMMITTEE MEMBER: Joseph Vanherweg, MS Design Engineer at Stellar Exploration iii ABSTRACT Colloid Thruster to Teach Advanced Electric Propulsion Techniques to Post-Secondary Students Alexander M. Powaser Colloid thrusters, and electrospray thrusters as a whole, have been around since the 1960s. When they were first developed, the high efficiency and fine thrust control was overshadowed by the high power requirement for such a low thrust that the system provides. This caused the technology to be put on hold for aerospace applications. Now, as small satellites are becoming more prevalent, there has been a resurgence in interest in electrospray thruster technology. The recent advancements in tech- nology allow electrospray thrusters to use significantly less power and occupy less volume than their predecessors. As electrospray technology continues to advance, these thrusters are meeting the demands of small satellite propulsion. As such, in an effort to keep the spacecraft propulsion curriculum current with today's technology, a colloid thruster is designed, built, tested, and implemented as a laboratory activity at California Polytechnic State University, San Luis Obispo.