Cimdata Cpdm Late-Breaking News
Total Page:16
File Type:pdf, Size:1020Kb
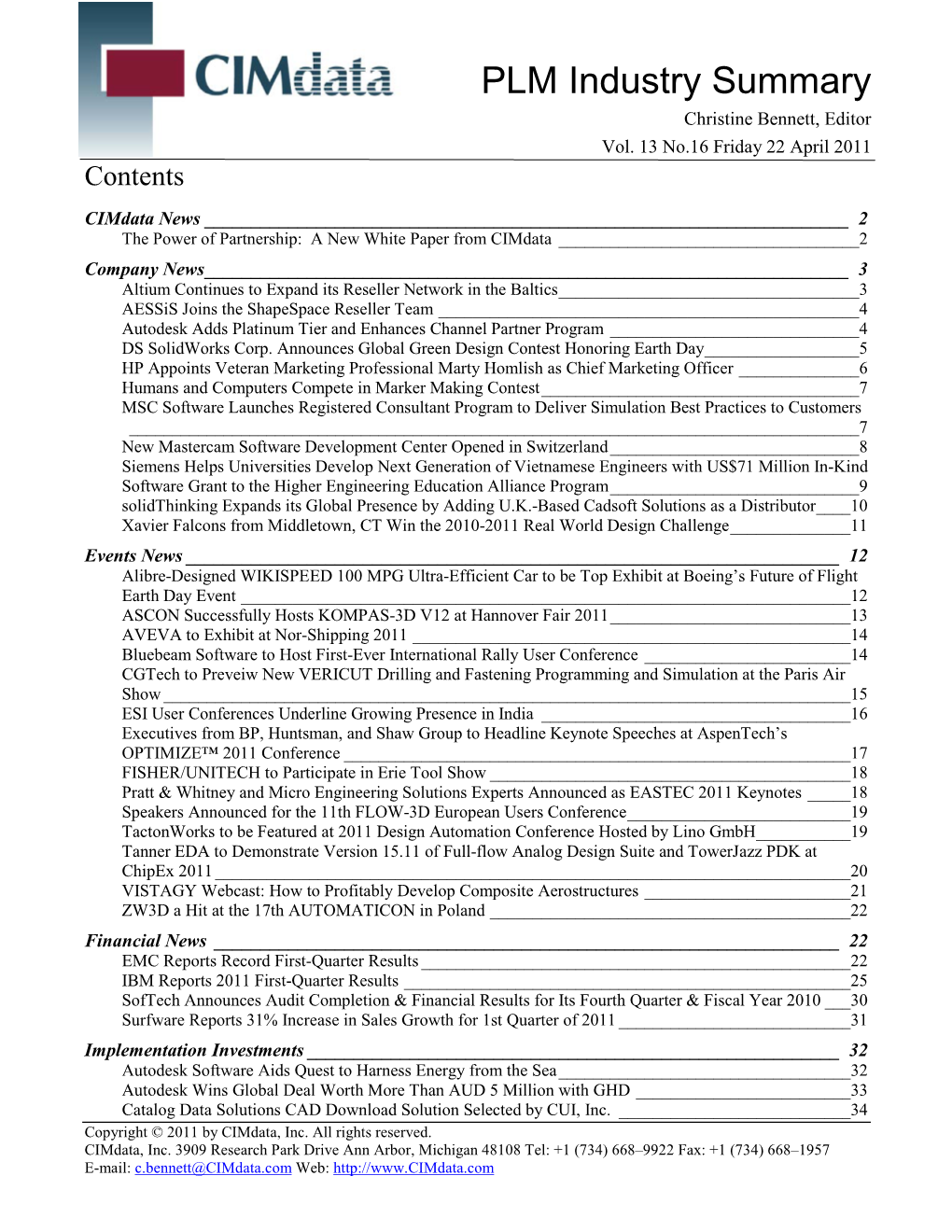
Load more
Recommended publications
-
Download the PLM Industry Summary
PLM Industry Summary Jillian Hayes, Editor Vol. 14 No 35 Friday 31 August 2012 Contents CIMdata News _____________________________________________________________________ 2 CIMdata PLM Late-Breaking News Announcement ____________________________________________2 CIMdata Publishes “CAD Selection Considerations: Product Assemblies” __________________________3 Ford IT Executive, Mark Johnson, to Join the Keynote Line-up at CIMdata’s PLM Road Map™ 2012 _____4 Acquisitions _______________________________________________________________________ 6 Autodesk Continues Strategic Investment in Product Lifecycle Management with Acquisition of Inforbix __6 Company News _____________________________________________________________________ 7 Advanced Technologies Solutions Earns Simulation and Structural Engineering Specializations _________7 Autodesk Now Counts 20 Partners with Platinum Status _________________________________________7 Edgecam Helps Nuclear Manufacturers ______________________________________________________8 GRAITEC is Partnering with DMS Software Co Ltd in China ____________________________________9 Hagerman & Company Announces new President, CEO ________________________________________10 MecSoft Announces New Reseller in India __________________________________________________11 Tata Technologies Earns Autodesk simulation Specialization and Autodesk PLM 360 Specialization Certifications __________________________________________________________________________12 Events News ______________________________________________________________________ -
Izrada Strategije Za Obradu Glodanjem Na Cnc Strojevima Design of Milling Tool Cutting Strategy for Cnc Manufacturing Operations
Eng. Rev. 28-1 (2008) 93-97 93 ____________________________________________________________________________________________________________________________________________________ UDC 621.9-52:621.914:004.89 IZRADA STRATEGIJE ZA OBRADU GLODANJEM NA CNC STROJEVIMA DESIGN OF MILLING TOOL CUTTING STRATEGY FOR CNC MANUFACTURING OPERATIONS Jozef NOVÁK-MARCINČIN Sažetak: Da bi se postiglo kraće vrijeme obrade i bolja kvaliteta površine, proizvodni inženjer mora primijeniti optimizaciju digitalno kontrolirane proizvodnje strojeva za glodanje kao i koncept točnog dizajna – strategiju gibanja alata za glodanje. Zbog mogućnosti izvođenja velikog broja različitih vrsta površina na različitim proizvodnim strojevima, a korištenjem različitih tehnoloških parametara, teško je izabrati optimalan i učinkovit koncept gibanja alata za glodanje. Novi moderan pristup rješavanju tih problema za sobom povlači primjenu ekspertnog sustava i sustava temeljenog na znanju, kao i klasičnog softvera namijenjenog izradi kontrolnog NC programa. Ključne riječi: – strategija obrade glodalom – NC programiranje Summary: In order to obtain better cutting time and better quality of parts surfaces, it is necessary for the manufacturing engineer to implement optimal digitally controlled milling manufacturing machines as well as an accurate design concept—a strategy for milling tool motion. On the grounds of the possibility for realizing a wide array of different type surfaces on different manufacturing devices, and through the exploitation of various technological parameters, it is difficult to choose an optimal and efficient concept for milling tool motion. The new and modern approach to solving these problems constitutes the application of expert and knowledge systems in collaboration with classical software intended for creation by control NC programs. Keywords: – milling tool cutting strategy – NC programming 1. INTRODUCTION A third benefit offered by most forms of CNC machine tools is flexibility. -
PLM Industry Summary Jillian Hayes, Editor Vol
PLM Industry Summary Jillian Hayes, Editor Vol. 16 No. 49 Friday 5 December 2014 Contents CIMdata News _____________________________________________________________________ 2 CIMdata Publishes PLM Industry Report ____________________________________________________2 CIMdata Releases Series of Country-Specific PLM Market Analysis Reports ________________________5 A New Business Calculus from IBM Software Group ___________________________________________6 SmarTeam: Offering Users Options for Growth: a CIMdata Commentary __________________________10 Subscribing to Product Design Software: a CIMdata Commentary ________________________________12 Company News ____________________________________________________________________ 14 3D Systems Makes Forbes’ List of America’s Best 100 Small Companies __________________________14 Adris, MicroCAD and Graitec UK become one Company Graitec Limited _________________________14 ASCENT- Center for Technical Knowledge Announces Plans to Collaborate with 4D Technologies on Training and Learning Resources for Autodesk Software Users __________________________________15 Autodesk Makes Design Software Free to Schools Worldwide ___________________________________16 Brian Beattie Named EVP, Business Operations and Chief Administrative Officer ___________________17 Cimatron Donates $1.7 Million Software to Iowa Community College for Advanced CAD/CAM Training 18 Dassault Systèmes and Expo Milano 2015: Partners to Promote Eco-Sustainability Exhibition __________18 ESI and EDF Energies Nouvelles sign an Exclusive -
13Th DAAAM INTERNATIONAL SYMPOSIUM (12
7th INTERNATIONAL MULTIDISCIPLINARY CONFERENCE Baia Mare, Romania, May 17-18, 2007 ISSN-1224-3264 COMPUTER AIDED MANUFACTURING - CAM SYSTEMS Eduard, Lörinc Technical university of Košice with a seat in Prešov, Faculty of Manufacturing Technologies, ul. Bayerova 1, 080 01, Prešov. Abstract: The goal of this paper is too briefly and comprehensively describe the main features of computer aided manufacturing systems (CAM) and to decrease the lack of information in this area. Maximal production asset can only be achieved by complex application of computer aided manufacturing systems into the all activities related to manufacturing realization, which means that besides design this application should affect the choice of manufacturing technology, workplace project, tools and fixtures project and manufacturing realization itself followed by checking of product quality. Key words: Computer Aided Manufacturing, CAM Systems, NC - Numeric Control, CNC - Computer Numeric Control. 1. INTRODUCTION The history of computer aided systems is essentially identical with the history of computer aided design and construction which is primary related with the history of computer graphics. There was no possibility to create solids, to manipulate with them and to check them until computer graphics began. Computer aided design and construction only contained the computation execution. Although the first project of calculating machine - calculator with the graphic mode was presented in 1945 by Vannevar Bush, it was never realized. First computers with the option of interactive graphic control on screen were produced in early 60’s which was mainly the merit of General Motors, Lockheed, NASA and Bell Labs. Even though first systems of computer graphics and computer aided design and construction were developed using different computer platforms, the biggest producers of computer (IBM, DEC, Control Data, Texas Instruments) ignored this area. -
+ CAD/CAM Okan Üniversitesi MYO / MMAK155 – TEMEL İMALAT İŞLEMLERİ
Okan Üniversitesi MYO MMAK155 TEMEL İMALAT İŞLEMLERİ Dersi Veren: Öğr. Gör. Eren Kayaoğlu [email protected] DERS 10 Temel İmalat İşlemleri Ders Sunumları (.pdf) + Kaynaklar http://okanuni.eren.xyz Web adresinden indirebilirsiniz. Okan Üniversitesi MYO / MMAK155 – TEMEL İMALAT İŞLEMLERİ CNC Programlamaya Giriş (Devam) + CAD/CAM Okan Üniversitesi MYO / MMAK155 – TEMEL İMALAT İŞLEMLERİ Kaynakça: https://tezmaksanakademi.com/cnc-isleme-merkezi http://www.helmancnc.com/cnc-g-code-introduction/ http://www.helmancnc.com/simple-g-code-example-mill-g-code- programming-for-beginners/ https://machmotion.com/blog/g-code-examples https://cadsay.com/cam-programlari https://www.bilkey.com.tr/online-kurs-kurtkoy/cnc/fanuc-cnc- programlama-kodlari.pdf Okan Üniversitesi MYO / MMAK155 – TEMEL İMALAT İŞLEMLERİ CNC – CAD – CAM • CNC: Computer Numerical Control kelimelerinin baş harflerinden oluşan kısaltmadır. Bilgisayarlı Sayısal Kontrol anlamına gelmektedir. • CAD: Computer Aided Design kelimelerinin baş harflerinden oluşan kısaltmadır. Bilgisayar Destekli Tasarım anlamına gelmektedir. • CAM: Computer Aided Manufacturing kelimelerinin baş harflerinden oluşan kıslatmadır. Bilgisayar Destekli İmalat anlamına gelmektedir. Okan Üniversitesi MYO / MMAK155 – TEMEL İMALAT İŞLEMLERİ CAD >> CAM >> CNC • CAD ile kavramsal (geometrik) tasarımı oluşturulan model, CAM ile üretim aşamasına girer. • Daha önce boyut ve şekil olarak CAD yazılımları ile tasarımı yapılan ürünün üretilmesi için CAM ile programlama gerekir. Okan Üniversitesi MYO / MMAK155 – TEMEL İMALAT İŞLEMLERİ CAD >> CAM >> CNC • CAM programları sayesinde üretilecek parçaların programı bir defa yazıldıktan sonra bilgisayar kontrollü tezgâhlar sayesinde otomatik olarak üretimleri yapılır. • CNC teknolojisi sayesinde, parça işleme bilgisayar ile yapıldığından, geleneksel torna, freze gibi teknolojilere nazaran daha hızlı, daha hatasız ve daha düşük maliyetli sonuçlar elde edilir. • Ayrıca elle yapılamayacak kadar detaylı geometrilerin işlenmesine ve neredeyse kusursuz olarak üretilmesine olanak sağlar. -
New Method of Cnc Programs Creation by Group Technology Theory Application
Annals of DAAAM for 2012 & Proceedings of the 23rd International DAAAM Symposium, Volume 23, No.1, ISSN 2304-1382 ISBN 978-3-901509-91-9, CDROM version, Ed. B. Katalinic, Published by DAAAM International, Vienna, Austria, EU, 2012 Make Harmony between Technology and Nature, and Your Mind will Fly Free as a Bird Annals & Proceedings of DAAAM International 2012 NEW METHOD OF CNC PROGRAMS CREATION BY GROUP TECHNOLOGY THEORY APPLICATION NOVAK - MARCINCIN, J[ozef]; JANAK, M[iroslav]; NOVAKOVA - MARCINCINOVA, L[udmila] & TOROK, J[ozef] Abstract: Creation of the control programs for controlling of processed by every machine of corresponding machine the computer numerical controlled (CNC) manufacturing cell. This type of manufacturing in which a part family is machines is very important in manufacturing practice in this produced by a machine cell is known as cellular time. Manufacturing process of the parts with complex and free manufacturing. The manufacturing efficiencies are form figures are realized by NC manufacturing machines application. It is very difficult without application of personal generally increased by employing GT because the computers with special software. Very often this software can required operations may be confined to only a small cell be Computer Aided Manufacturing (CAM) systems. These and thus avoiding the need for transportation of in- programs for control of CNC manufacturing machines can be process parts [5]. realised by other methods, too. In paper is presented new method of NC programs creation by Group Technology theory 2. BASIC METHODS OF NC PROGRAM application. CREATION Keywords: computer aided manufacturing, CNC programming, NC program creation, group technology, GroupNC program In manufacturing practice there are three main 1. -
PLM Industry Summary Jillian Hayes, Editor Vol
PLM Industry Summary Jillian Hayes, Editor Vol. 15 No 25 Friday 21 June 2013 Contents CIMdata News _____________________________________________________________________ 2 PTC Live Global 2013: a CIMdata Commentary _______________________________________________2 Rethinking Application Support: a CIMdata Commentary _______________________________________5 The Experience Economy: An Update on Dassault Systèmes: a CIMdata Commentary ________________10 Acquisitions ______________________________________________________________________ 12 Stratasys to Acquire MakerBot ____________________________________________________________12 Company News ____________________________________________________________________ 14 AMC Bridge and Sight Power Sign Partnership Agreement _____________________________________14 Arena Ranked Top 10 PLM Solution _______________________________________________________14 Autodesk Inks Agreement with Turkey’s Ministry of Education __________________________________15 Delcam Turkiye Introduces Turkish Website to Promote CADCAM Software_______________________16 Ideate, Inc. Expands Tech Expert Team with Four Hires ________________________________________16 Intergraph® Announces 2014 Geospatial Challenge ___________________________________________17 New Industry Report Identifies PTC as the Leading Provider of PLM Software to Global Aerospace & Defense Manufacturers __________________________________________________________________18 GRAITEC Announces Reseller Agreement with VR CAM Technologies in Malaysia ________________19 -
Jozef Novák-Marcincin, Anton Petík COMPUTER AIDED
Jozef Novák-Marcincin, Anton Petík COMPUTER AIDED MANUFACTURING - INSEPARABLE PART OF CAD/CAM/CAE SYSTEMS In the conception of computer aided systems, systems of computer support, respectively CA systems most of us consider only computer systems supporting the drawing, design and constructing of parts and products, so these systems which are called CAD systems (Computer Aided Design). This oneside view is determined by several factors: simple CAD systems without further relation to manufacturing (especially AutoCAD) were extensively used as first in construction offices of our factories and enterprises from 1990; the number of installation of these systems and thus also the number of CAD systems users is several times prevailing the number of the other computer aided systems users; the other CA systems (for example systems of computer aided manufacturing) are dependent on data which have to be processed and prepared by CAD systems; education of the CA systems is mostly realized only in the area of CAD systems; etc. In spite of the above facts, it is obvious, that maximal benefit for production enterprises is reached only by complete application of the computer aided systems to realization of the product, this means that besides of the design and dimensioning of parts and products also to design of the production technology, design of the working-place, design of the working tools and fixtures, realization of own manufacturing and following testing the product quality. The aim of this paper is briefly but completely describe the main features of the systems for computer aided manufacturing - CAM and thus fill the space in knowledges which exists in considered area. -
292 Мундарижа 2-Қисм/Part 2/ Вторая Часть
292 МУНДАРИЖА 2-ҚИСМ/PART 2/ ВТОРАЯ ЧАСТЬ 7.ТАРИХ САҲИФАЛАРИДАГИ ИЗЛАНИШЛАР / RESEARCHES ON HISTORY ИССЛЕДОВА- НИЯ ПО ИСТОРИИ ТАЛАБА-ЁШЛАРГА ТАЪЛИМ-ТАРБИЯ БЕРИШДА АХБОРОТ КОММУНИКАЦИОН ТЕХНОЛО- ГИЯЛАРНИНГ ЎРНИ Назарова Дилдора ..............................................................................................................................................297 TO`GARAKLARNI SAMARALI TASHKIL ETISH Ostonova Zarnigor Usmonovnа ........................................................................................................................299 КОМПЮТЕР ҚАРШИСИДА УЗОҚ ВАҚТ САРФЛАГАН ЎҚУВЧИ ЁШЛАРДА КУЗАТИЛАДИГАН СИНДРОМЛАР Сафаева Севара, Солижонов Жасурбек .......................................................................................................301 O‘QUVCHILAR KOMPETENTLIGINI SHAKLLANTIRISHDA ADABIYOT DARSLARINING O‘RNI TURDIYEVA Nilufar, SAFAROVA Sayyora ...................................................................................................304 СИНФДАН ТАШҚАРИ МАШҒУЛОТЛАРДА ЎҚУВЧИЛАРНИНГ МАТЕМАТИК ТАФАККУРИНИ РИВОЖЛАНТИРИШ Шихова Инобат Омоновна .............................................................................................................................306 ТАЛАБА-ЁШЛАРГА ТАЪЛИМ-ТАРБИЯ БЕРИШДА АХБОРОТ КОММУНИКАЦИОН ТЕХНОЛО- ГИЯЛАРНИНГ ЎРНИ Назарова Дилдора ..............................................................................................................................................310 YOSH AVLODNI TARBIYALASHDA KITOBXONLIKNING AHAMIYATI Jalilov Mirsaid NavDPI, Ergasheva