Operational Excellence at Jabil
Total Page:16
File Type:pdf, Size:1020Kb
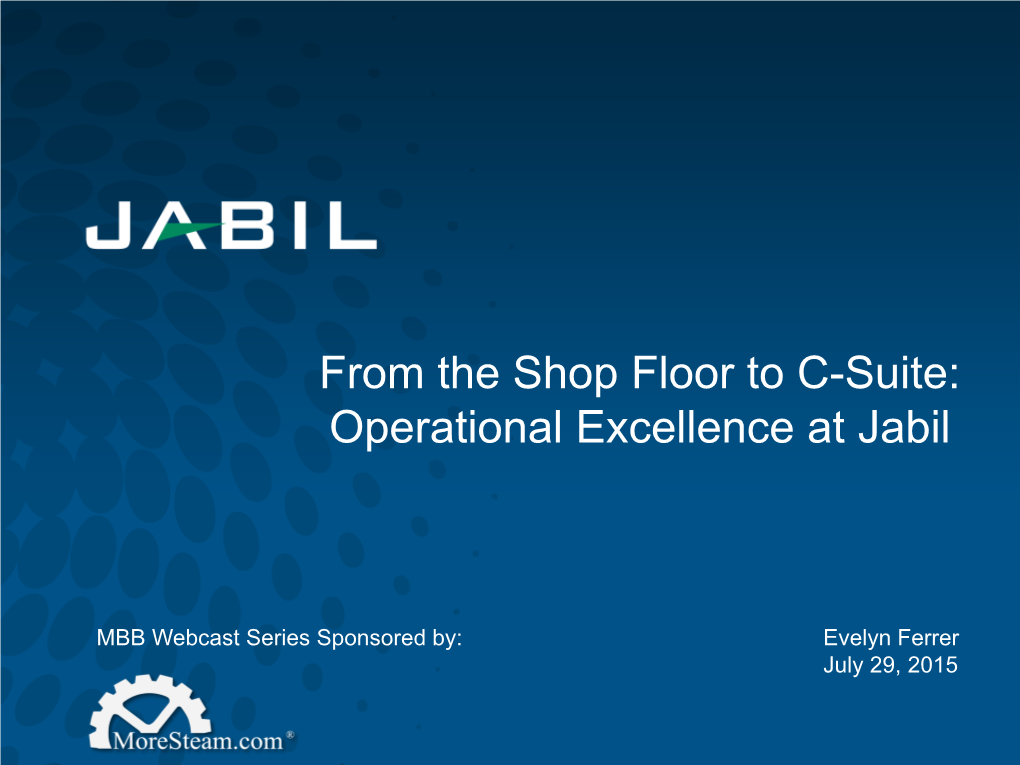
Load more
Recommended publications
-
Achieving Total Quality Management in Construction Project Using Six Sigma Concept
International Research Journal of Engineering and Technology (IRJET) e-ISSN: 2395-0056 Volume: 05 Issue: 06 | June 2018 www.irjet.net p-ISSN: 2395-0072 Achieving Total Quality Management in Construction Project Using Six Sigma Concept Dr.Divakar.K1 and Nishaant.Ha2 1Associate Professor in Civil Engineering, Coimbatore Institute of Technology, Coimbatore-641014 2Assistant Professor in Civil Engineering, Kumaraguru College of Technology, Coimbatore-641049 ---------------------------------------------------------------------***--------------------------------------------------------------------- Abstract - A Six Sigma approach is one of the most Low Sui Pheng and Mok Sze Hui (2004) examined the efficient quality improvement processes. In this study, six strategies and concepts of Six Sigma and implemented sigma concepts were applied in construction scheduling those concepts in construction industry. A. D. Lade et.al. process to avoid delay as well as to maintain the quality of (2015) analysed the quality performance of Ready Mix the construction activities. Detailed schedule of the building Concrete (RMC) plant at Mumbai, India, using the six was analysed & also the updated schedule was verified. At sigma philosophy had been evaluated using various this stage, DMAIC (Define, Measure, Analyse, Improve and quality tools and sigma value was calculated. According to Control) principle was implemented. The variation in the the sigma level, recommendations were given for the scheduling due to delay of the activities was noted down. improvement. Seung Heon Han et.al. in their study they Delay reasons and their impacts in the whole project were developed a general methodology to apply the six sigma calculated. All delayed activities were considered as principles on construction operations rather than “Defects”. DPMO (Defects Per Million Opportunities) was construction materials in terms of the barometers to calculated. -
Revised ASQ 711 THEORY of CONSTRAINS JUNE 13 2017
THEORY OF CONSTRAINTS Presented by CHHANUBHAI (C.G.) MISTRY JULY 19, 2017 ASQ 711 THEORY OF CONSTRAINTS AGENDA Introduction Basics of Theory of Constraints TOC The Thinking Process Throughput, Inventory and Operating Expenses Different types of Constraints TOC, Lean and Six Sigma ASQ 701 6/13/2017 2 THEORY OF CONSTRAINTS INTRODUCTION Book: The GOAL Author: Dr. ELiyahu M. Goldratt • What to change---find and use the leverage point • What to change to---create the simple, practical solutions • How to cause the change---build a secure and stable improvement environment. ASQ 701 6/13/2017 3 THEORY OF CONSTRAINTS INTRODUCTION Every process has a constraint (bottLeneck) and focusing improvement efforts on the constraint is the fastest way to improved profitability. TOC heLps to prioritize the improvement activities. TOC heLps to improve bottom Line profits. It heLps to focus on rapid improvements. TOC heLps to identify constrains in compLex systems. ASQ 701 6/13/2017 4 THEORY OF CONSTRAINTS BOTTLENECK ASQ 701 6/13/2017 5 THEORY OF CONSTRAINTS BASICS OF THEORY OF CONSTRAINS • TOC – It is a methodoLogy used to identify the factor most responsibLe for not aLLowing the achievement of throughput at maximum efficiency and output. • It is a scientific approach to continuous improvements • TOC uses Management tooL - Thinking Process. ASQ 701 6/13/2017 6 THEORY OF CONSTRAINTS THINKING PROCESS When reaL constrain is poLicy or practice, Thinking process is very heLpful: • What to change: What core problem bedeviLs the organization • What to change to: What action wiLL provide a breakthrough soLution • How to create the change: Actions needed to create the desired environment and how they can be executed. -
Lean Six Sigma for Dummies‰
Lean Six Sigma FOR DUMmIES‰ 2ND EDITION by John Morgan and Martin Brenig-Jones A John Wiley and Sons, Ltd, Publication Lean Six Sigma For Dummies®, 2nd Edition Published by John Wiley & Sons, Ltd The Atrium Southern Gate Chichester West Sussex PO19 8SQ England www.wiley.com Copyright © 2012 John Wiley & Sons, Ltd, Chichester, West Sussex, England Published by John Wiley & Sons, Ltd, Chichester, West Sussex All Rights Reserved. No part of this publication may be reproduced, stored in a retrieval system or transmit- ted in any form or by any means, electronic, mechanical, photocopying, recording, scanning or otherwise, except under the terms of the Copyright, Designs and Patents Act 1988 or under the terms of a licence issued by the Copyright Licensing Agency Ltd, Saffron House, 6-10 Kirby Street, London EC1N 8TS, UK, without the permission in writing of the Publisher. Requests to the Publisher for permission should be addressed to the Permissions Department, John Wiley & Sons, Ltd, The Atrium, Southern Gate, Chichester, West Sussex, PO19 8SQ, England, or emailed to [email protected], or faxed to (44) 1243 770620. Trademarks: Wiley, the Wiley logo, For Dummies, the Dummies Man logo, A Reference for the Rest of Us!, The Dummies Way, Dummies Daily, The Fun and Easy Way, Dummies.com, Making Everything Easier, and related trade dress are trademarks or registered trademarks of John Wiley & Sons, Inc., and/or its affiliates in the United States and other countries, and may not be used without written permission. All other trademarks are the property of their respective owners. John Wiley & Sons, Inc., is not associated with any product or vendor mentioned in this book. -
A Concise Literature Review on Comparison Between Lean Manufacturing and Six Sigma with Their Separate and Combined Applications to a Few Specific Industrial Sectors
Proceedings of the International Conference on Industrial & Mechanical Engineering and Operations Management Dhaka, Bangladesh, December 26-27, 2020 A Concise Literature Review on Comparison between Lean Manufacturing and Six Sigma with Their Separate and Combined Applications to a Few Specific Industrial Sectors Nafiz Afsan, Md. Abdul Aziz and A.R.M. Harunur Rashid Department of Mechanical and Production Engineering (MPE) Islamic University of Technology (IUT) Boardbazar, Gazipur, Dhaka, Bangladesh [email protected], [email protected], [email protected] Abstract Lean Manufacturing heavily focuses on reducing waste in order to maximize production. Six Sigma is largely identical to Lean Manufacturing fundamentals, but its main focus is to produce high quality output in consistent manner. Though both methodologies aim at improving manufacturing processes and creating efficiencies, they have their unique set of characteristics that might be best suited when implemented separately. But in the long run, companies have identified the combined implementation of Lean Manufacturing and Six Sigma as the way forward, as it helps to take the advantage of the strengths of both the strategies while providing a comprehensive, effective and suitable solution to various issues related to the improvement of processes and products. This paper focuses on a comparative exploration of lean manufacturing and six-sigma in terms of their different types of applications to various industries. From our study, it has been observed that, Lean Manufacturing and Six Sigma methodologies are actively being implemented in conjunction and thus have coined themselves together as the Lean Six Sigma strategy. Keywords Lean Manufacturing, Six Sigma, Lean Six Sigma, TQM. -
Using the DMAIC Process to Direct the Sequencing of Lean/Six Sigma Tools for Successful Project Outcomes
Using the DMAIC Process to Direct the Sequencing of Lean/Six Sigma Tools for Successful Project Outcomes Jim Ellis Certified Master Black Belt J&J Process Excellence Director – US Sales Strategic Accounts [email protected] Intent: Using the DMAIC Process to Direct the Sequencing of Lean/Six Sigma Tools for Successful Project Outcomes The purpose of this presentation is to share with the attendees my experience over the past 5 years using the DMAIC Process how to determine what Lean and/or 6 Sigma tools is the best to use when for assuring successful outcomes of your projects. Learning Objectives: 1.) Clear understanding of DAMIC Process 2.) Clear understanding of which common Lean and 6 Sigma Tools are best used in what stage of DMAIC 3.) Clear understanding of how to assess success for a project and know if you have achieved it. After Attending the attendees will: 1.) Know what the DMAIC process is and how it is applied in project planning 2.) Understand which Lean and 6 Sigma tools are used in what sequence to assure successful project outcomes © 2008 Ortho Clinical Diagnostics The Driving Forces of Change Today’s Healthcare Delivery Challenges… Declining Resources $29.9 Space Vacancy Capital Funds billion Skilled Labor Rates Medicare/Medicaid Reimbursement Laboratory Techs 5.9% Shortfall Imaging Techs 5.9% Pharmacists 8.1% RNs 8.1% Inpatient Admissions2 ED Visits2 Volume New Technology Market Pressures Increasing Pressures © 2008 Ortho Clinical Diagnostics Why are labs changing? “I need to transform my lab!” Why? • 2X Volume • ½ the -
Review Paper on “Poka Yoke: the Revolutionary Idea in Total Productive Management” 1,Mr
Research Inventy: International Journal Of Engineering And Science Issn: 2278-4721, Vol. 2, Issue 4 (February 2013), Pp 19-24 Www.Researchinventy.Com Review Paper On “Poka Yoke: The Revolutionary Idea In Total Productive Management” 1,Mr. Parikshit S. Patil, 2,Mr. Sangappa P. Parit, 3,Mr. Y.N. Burali 1,Final Year U.G. Students, Mechanical Engg. Department,Rajarambapu Institute of Technology Islampur (Sangli),Shivaji University, Kolhapur (India) 2,P.G. Student, Electronics Engg. Department, Rajarambapu Institute of Technology Islampur (Sangli), Shivaji University, Kolhapur (India) Abstract: Poka-yoke is a concept in total quality management which is related to restricting errors at source itself. It deals with "fail-safing" or "mistake-proofing". A poka-yoke is any idea generation or mechanism development in a total productive management process that helps operator to avoid (yokeru) mistakes (poka). The concept was generated, and developed by Shigeo Shingo for the Toyota Production System. Keywords— Mistake-proofing, Total quality management, Total productive management. I INTRODUCTION In today’s competitive world any organisation has to manufacture high quality, defect free products at optimum cost. The new culture of total quality management, total productive management in the manufacturing as well as service sector gave birth to new ways to improve quality of products. By using various tools of TQM like KAIZEN, 6 sigma, JIT, JIDCO, POKA YOKE, FMS etc. organisation is intended to develop quality culture.[2,6] The paper is intended to focus basic concept of poka yoke, types of poka yoke system, ways to achieve simple poka yoke mechanism. It also covers practical study work done by various researchers . -
Define Measure Analyze Contr Ol
Lean Six Sigma BENEFITS STRATEGIC VALUE METHOD ORGANIZATION • Process improvement and • Superior cost structure • Professional and scientific • Improvement projects are led by Green redesign (manufacturing, • Competitive advantages based problem solving and Black Belts, who are familiar with the construction, financial services, on customer satisfaction • Working with precise and process and Lean Six Sigma healthcare, public sector, quantitative problem descriptions • Improvement projects follow the DMAIC high-tech industry) • Competence development in operations management, project • Starting with a data-based approach • Resulting in superior quality management and continuous diagnosis • Lean Six Sigma program management and efficiency levels improvement • Designing evidence-based coordinates projects by strategically • Structural financial impact improvement actions choosing projects and making sure that benefits are realized 0. DEFINE THE PROJECT Stakeholder analysis Lets initiative happen Legend: M oderately agains Strongly against 0: Current situation Makes initiative S I P O C X: Preferred situation Helps initiative happe Influence n Stakeholder Stake t Person 1 Person 2 Person 3 SIPOC Person 4 - Project charter - SIPOC and process flow chart - Benefit analysis - Organization (time and review board) DEFINE - Stakeholder analysis Project charter Stakeholder analysis 1. DEFINE THE CTQS 2. VALIDATE THE MEASUREMENT Operational PROCEDURES Revenue cost Pareto Chart of Problems Throughput time Processing time (min) 200 Customer 100 Personnel -
1. Lean Six Sigma This Section Provides an Introduction to Lean Six Sigma Philosophies and Techniques for Professional Accountants
MASTERING XBRL-BASED DIGITAL FINANCIAL REPORTING – PART 1: BACKGROUND – LEAN SIX SIGMA – CHARLES HOFFMAN, CPA 1. Lean Six Sigma This section provides an introduction to Lean Six Sigma philosophies and techniques for professional accountants. Accounting is a process. A kludge (or kluge) is an engineering/computer science term that describes what is best described as a workaround or quick-and-dirty solution that is typically clumsy, inelegant, inefficient, difficult to extend and hard to maintain; but it gets the job done. By contrast, elegance is beauty that shows unusual effectiveness and simplicity. Many accounting systems their related processes are kludges that are cobbled together over many years. Fewer accounting systems and processes are well- engineered. Accountants sometimes spend a lot of time improving the quality of things that should be destroyed. Idealized redesign is the notion of imagining what you would do to improve some process or system if you have no constraints. What would you do to improve your system if you were unconstrained? If you cannot answer that question and improve a system when unconstrained; you certainly cannot improve a system given the realities of constraints that you must generally live with. Another term for idealized redesign is greenfield project1. Born in manufacturing, Lean Six Sigma is just as applicable to accounting processes and accounting information systems as it is to building a physical product. 1.1. Lean Think about something. In your 40 to 60 hour work week, how much time do you get to think? How much time do you get to be proactive? To be creative? To apply what you have been trained to do2? A process is about satisfying some customer. -
Lean Six Sigma Applied to SKU Rationalization
Is Lean More Than Kaizen Events? When to use the Lean Six Sigma Project Format Mitch Millstein, CFPIM, C.P.M., CQM, CQE Supply Velocity, Inc. [email protected] (314) 406-4962 December 2009 [email protected] 1 Copyright: Supply Velocity, Inc. Abstract Many Lean Consultants promote Kaizen Events (a.k.a. Rapid Improvement Events) or Kaizen Blitzes as the method of implementing Lean. They are proponents of this method because that is how Toyota does it, and Toyota founded Lean. What these consultants overlook is that Toyota has 50+ years of experience with Lean and can do it faster than less experienced companies. In this paper we will discuss the problems with Kaizen Events and an alternate method (the Quick-Project-Format) of implementing Lean Six Sigma that achieves greater, more sustainable improvements. Lean Six Sigma Quick-Project-Format 3 – 5 Weeks in duration o 2 – 3 days per week o Team members return to work for the remainder of the week or use time to gather data and communicate updates to department employees Project Phases o Define o Analyze / Mapping o Design o Rollout Plan Education/workshop on day 1 of each week, if needed Report out to Business/Executive Sponsor 2 – 6 month Implementation Rollout o Monthly Team follow-up meetings / conference calls The Lean Six Sigma Quick-Project-Format works on projects that need a few weeks to complete the improvement. This can be due to many reasons. The scope of the project may cross multiple departments o Cannot be broken down into smaller parts or the process will be sub- optimized The team will need to gather, analyze and quality-check data before making critical decisions o Performance data or Time Study data The small Lean Six Sigma Team needs to get input from company associates who are not on the team, to ensure buy-in [email protected] 2 Copyright: Supply Velocity, Inc. -
SURFACE MINING and Subsurface Mining Requires Expensive Machinery and Equipment
PROCESS IMPROVEMENT Combining lean, Six Sigma and theory of constraints Rock creates a process improvement powerhouse . : . : . : . : . .: . .. :. :. L. : . .. .. : . : . : . .. D . : . I . 0 . .. :S . , . : . : . SURFACE MINING AND subsurface mining requires expensive machinery and equipment. A 12-ton In 50 Words front-end loader and 35-ton haul truck, for example, can Or Less • The 6TOC improvement cost $1.2 million and $350,000, respectively. A single site method employs ele- by Todd Creasy ments of Six Sigma, lean can use several pieces of equipment, with additional capi- and the theory of con- straints (TOC) to zero in tal needed for the plant’s fixed machinery, pushing the on process bottlenecks and eliminate waste and variation. up-front investment into the tens of millions of dollars. • A 10-step implemen- tation plan based on Eliyahu Goldratt’s chain project management process and Joseph M. Juran’s management principles can help any industry implement 6TOC. December 2014 • QP 45 PROCESS IMPROVEMENT These capital investments can prevent entry into and the theory of constraints (TOC).2 Its principles and in-house receiving department. Critical process flowchart for the industry and complicate efforts to grow or im- deployment steps are shown in Table 1. In the mining industry, it begins with the stone prove productivity. Because money is the language of Although this approach to process and productivity that has been blasted from the stone face. The pro- mining operation / FIGURE 1 senior management,1 site managers are careful about improvement is presented here in a case study involv- cess continues with the stone traveling to the pri- unnecessary capital expenses, and often try to focus ing a mid-southern U.S. -
Lean Manufacturing Case Study with Kanban System Implementation
CORE Metadata, citation and similar papers at core.ac.uk Provided by Elsevier - Publisher Connector Available online at www.sciencedirect.com ScienceDirect Procedia Economics and Finance 7 ( 2013 ) 174 – 180 International Conference on Economics and Business Research 2013 (ICEBR 2013) Lean Manufacturing Case Study with Kanban System Implementation Nor Azian Abdul Rahmana*, Sariwati Mohd Sharifb, Mashitah Mohamed Esac a,b,c Faculty of Business Management, Universiti Teknologi MARA, Shah Alam, 40450, Selangor, Malaysia Abstract Lean manufacturing has been the buzzword in the area of manufacturing for past few years especially in Japan. The Kanban system is one of the manufacturing strategies for lean production with minimal inventory and reduced costs. However, the Kanban system is not being implemented widely by manufacturing companies in Malaysia. Thus, the objectives of this case study are 1) to determine how does the Kanban system works effectively in multinational organization; and 2) to identify factors hindering Malaysian small and medium enterprises (SME) from implementing Kanban. Findings of the study suggest that top management commitment, vendor participation, inventory management and quality improvement are important for Kanban deployment and towards lean manufacturing. © 2013 TheThe Authors. Authors. Published Published by by Elsevier Elsevier B.V. B.V.Open access under CC BY-NC-ND license. Selection and and/or peer-review peer-review under under responsibility responsibility of ICEBR of the 2013 ICEBR 2013. Keywords: Just-in-time; lean manufacturing; kanban system; inventory management; operations strategies 1. Introduction In general, there are varieties of tools and techniques used in determining effective manufacturing system in a company. Kanban system is just one of the tools and techniques used in lean manufacturing besides other techniques like Quality Circle, 5S Housekeeping, and continuous improvement and many others. -
Theory of Constraints and Six Sigma: Investigating Differences and Similarities for Continuous Improvement
INDEPENDENT JOURNAL OF MANAGEMENT & PRODUCTION (IJM&P) http://www.ijmp.jor.br v. 5, n. 2, February – May 2014. ISSN: 2236-269X DOI: 10.14807/ijmp.v5i2.150 THEORY OF CONSTRAINTS AND SIX SIGMA: INVESTIGATING DIFFERENCES AND SIMILARITIES FOR CONTINUOUS IMPROVEMENT Diego Augusto de Jesus Pacheco University Federal of Rio Grande do Sul, UFRGS – Brazil E-mail: [email protected] Submission: 04/10/2013 Revision: 19/10/2013 Accept: 01/11/2013 ABSTRACT The main objective of this study is to analyse some points of convergence and divergence between the Theory of Constraints and Six Sigma when used in an integrated manner for the continuous improvement of operating manufacturing systems. This research also aims to advance a better understanding of the fundamental principles of such methodologies by performing a comparative analysis of critical issues. The focus of the discussion of this study is to review the literature to identify the mains similarities and differences between these two approaches when applied in an integrated way in productive systems. To conduct this research, we carry out a broad literature review of the state of the art on the topic of Operations Management. The results of this study suggest that the Theory of Constraints and Six Sigma have many complementary elements that overlap and that a vast field of research must be explored on this issue. As a result, this study conducts a comparative analysis of 28 critical criteria of the Theory of Constraints and Six Sigma to understand these approaches. Keywords: Theory of Constraints, Six Sigma, Continuous Improvement. [http://creativecommons.org/licenses/by/3.0/us/] Licensed under a Creative Commons Attribution 3.0 United States License 331 INDEPENDENT JOURNAL OF MANAGEMENT & PRODUCTION (IJM&P) http://www.ijmp.jor.br v.