Rubber Production in Liberia: an Exploratory Assessment of Living and Working Conditions, with Special Attention to Forced Labor 2 Abbreviations
Total Page:16
File Type:pdf, Size:1020Kb
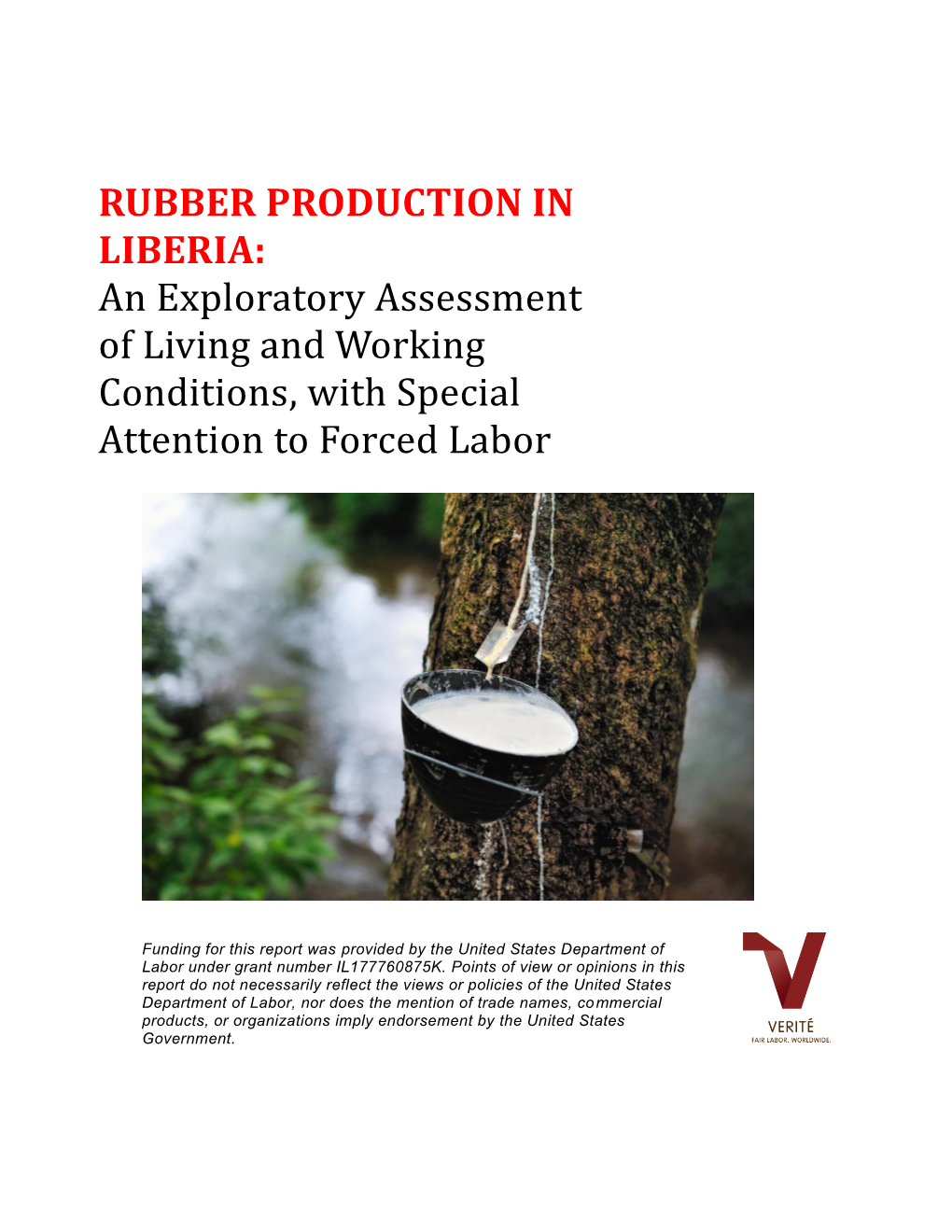
Load more
Recommended publications
-
Sefa Country Profile Template
LIBERIA: Rapid Assessment and Gap Analysis Final Report - May 2013 Table of contents SECTION 1. INTRODUCTION 6 1.1. Country Overview 8 1.2. Energy Situation 10 SECTION 2. CURRENT SITUATION WITH REGARD TO SE4ALL GOALS 18 2.1. Energy Access vis-à-vis Goal of SE4ALL 18 2.2. Energy Efficiency vis-à-vis Goal of SE4ALL 23 2.3. Renewable Energy vis-à-vis Goal of SE4ALL 24 2.4. SE4All goals 29 SECTION 3. CHALLENGES AND OPPORTUNITIES FOR ACHIEVING SE4ALL GOALS 30 3.1. Institutional and Policy Framework 30 3.2. Programs and Financing 31 3.3. Private Investment and Enabling Business Environment 40 3.4. Gaps and Barriers 42 ANNEX 1 - EXISTING PROGRAMS AND CORRESPONDING FINANCING FOR CONTRIBUTION TO SE4ALL GOALS 42 ANNEX 2 - INITIATING A SUSTAINABLE ENERGY FOR ALL INITIATIVE IN LIBERIA: SOME SUGGESTED STEPS AND MEASURES 48 ANNEX 3: SLIDES OF REPORT PRESENTATION TO STAKEHOLDERS 55 2 OBJECTIVE The purpose of Rapid Assessment and Gap Analysis is to provide: A quick brief look of the energy situation in the country (Section 1) within the context of its economic and social development and poverty eradication A good review of where the country is in terms of the three SE4ALL goals (Section 2), and A good estimate of the main challenges and opportunities vis-à-vis the three goals of SE4ALL where the major investments, policies and enabling environments will be required (Section 3) A sound basis and background for an Action Plan that may follow as part of the SE4ALL activities in the country EXECUTIVE SUMMARY General context. -
LIBERIA: Rapid Assessment and Gap Analysis Final Report
LIBERIA: Rapid Assessment and Gap Analysis Final Report - May 2013 Table of contents SECTION 1. INTRODUCTION 6 1.1. Country Overview 8 1.2. Energy Situation 10 SECTION 2. CURRENT SITUATION WITH REGARD TO SE4ALL GOALS 18 2.1. Energy Access vis-à-vis Goal of SE4ALL 18 2.2. Energy Efficiency vis-à-vis Goal of SE4ALL 23 2.3. Renewable Energy vis-à-vis Goal of SE4ALL 24 2.4. SE4All goals 29 SECTION 3. CHALLENGES AND OPPORTUNITIES FOR ACHIEVING SE4ALL GOALS 30 3.1. Institutional and Policy Framework 30 3.2. Programs and Financing 31 3.3. Private Investment and Enabling Business Environment 40 3.4. Gaps and Barriers 42 ANNEX 1 - EXISTING PROGRAMS AND CORRESPONDING FINANCING FOR CONTRIBUTION TO SE4ALL GOALS 42 ANNEX 2 - INITIATING A SUSTAINABLE ENERGY FOR ALL INITIATIVE IN LIBERIA: SOME SUGGESTED STEPS AND MEASURES 48 ANNEX 3: SLIDES OF REPORT PRESENTATION TO STAKEHOLDERS 55 2 OBJECTIVE The purpose of Rapid Assessment and Gap Analysis is to provide: A quick brief look of the energy situation in the country (Section 1) within the context of its economic and social development and poverty eradication A good review of where the country is in terms of the three SE4ALL goals (Section 2), and A good estimate of the main challenges and opportunities vis-à-vis the three goals of SE4ALL where the major investments, policies and enabling environments will be required (Section 3) A sound basis and background for an Action Plan that may follow as part of the SE4ALL activities in the country EXECUTIVE SUMMARY General context. -
Iv. Liberia's Rural Finance and Agricultural Marketing
IV. LIBERIA’S RURAL FINANCE AND AGRICULTURAL MARKETING SUB-SECTORS By Chet Aeschliman, FAO–RAF Rural Finance and Marketing Officer with contributions from Alfonso J. Wesseh, National Rural Finance and Marketing, Consultant, FAO Liberia 2007 IV. Liberia’s rural finance and agricultural marketing sub-sectors 142 CAAS-Lib Sub-Sector Reports Volume 2.2 ACRONYMS ACDB Agricultural Cooperative Development Bank of Liberia ACDI Agricultural Cooperative Development International of the United States ADB African Development Bank AFRACA African Rural & Agricultural Credit Association The United States Government’s "African Growth & Opportunity Act" programme AGOA to promote African exports to the USA BIVAC A private firm certifying the quality of exports from Liberia BNF Bureau of National Fisheries CARE Cooperative for American Relief Everywhere, an international NGO CARI Central Agricultural Research Institute of Liberia (Gbarnga, Bong Country) CBL Central Bank of Liberia CBO Community-based organizations CDA Cooperative Development Authority CLUSA Cooperative League of the United States CRS Catholic Relief Services, an international NGO CU Credit union, i.e. a savings and credit cooperative or association EAC A Liberian company formerly owning part of the LBDI ECOWAS The Economic Community of West African States EU European Union FAO Food and Agriculture Organization of the United Nations FAOR The FAO Representative or the entire Representation in Liberia FFA Farmers’ field school FX Foreign exchange GOL Government of Liberia IAS International -
The Determinants of Interest Rate Spread in Liberian Financial Sector
The Determinants of Interest Rate Spread in Liberian Financial Sector By Samwar Samzato Fallah A Research project submitted in partial fulfillment of the requirement for the award of the master degree of business administration (Finance option) of the University of Nairobi October 2012 DECLARATION I declare that this project is my original work and has not been presented for an award of a degree in any other University. Signed:………………………………. Date: ………………………….. SAMWAR SAMZATO FALLAH D61/60877/2011 This research project has been submitted for examination with my approval as the University Supervisor. Signed:………………………… Date:…………………………. Dr. Josiah O. Aduda Supervisor Department of Finance and Accounting School of Business University of Nairobi i DEDICATION This project is dedicated to my parents, Mr. Augustus N. Fallah and Mrs. Kuluku K. Fallah both of whom made my educational sojourn a success and without their parental guidance I wouldn‘t have reached this far. ii ACKNOWLEDGEMENT I express my sincere gratitude and appreciation to my Supervisor, Dr. Josiah O. Aduda for his support and guidance throughout the study. I also acknowledge the support of Mr. Rudolph T. Johnson of the Liberian Bank for Development and Investment who assisted in gathering the data for the study from Liberia. My appreciation also goes to Mr. Alps Briants Fallah and Mrs. Mary M. Fallah, whom I consider my guidance for of their numerous contributions to my education. I also acknowledge the Government of the Republic of Liberia through the General Auditing Commission of Liberia but most especially to Mr. John SembeMorlu, II, former Auditor General of the Republic of Liberia whose tireless efforts made my scholarship program at the University of Nairobi, a resounding success. -
Waifem West African Institute for Financial And
FOR FIN TE AN U C IT I WESTAFRICAN T A S L N A I N INSTITUTEFOR N D A E C C I O R FINANCIALAND F N A O T WAIFEM M S I E ECONOMIC C W MA T NAGEMEN MANAGEMENT 2009 ReportAnnual WEST AFRICANINSTITUTE FORFINANCIAL AND ECONOMICMANAGEMENT (WAIFEM) FOR FIN TE AN U C IT I T A S L N A I N N D A E C C I O R F N A O T WAIFEM M S I E C W MA T NAGEMEN ...Buildingcapacityformacro-economicandFinancialManagement 2009 ReportAnnual I WestAfricanInstituteForFinancialAndEconomicManagement(WAIFEM) TABLE OF CONTENTS Board of Governors VI Foreword VII Preface IX Principal Officers of the Institute XI 1.0 OPERATIONS OF WAIFEM 1 1.1 OVERVIEW OF PROGRAMME ACTIVITIES 1 1.2 DEBT MANAGEMENT DEPARTMENT 1 1.2.1 Regional Course On Middle Office Operations And Risk Management, Accra, Ghana, March 2 - 13, 2009. 1 1.2.2 Regional Workshop On Domestic Debt Management And Money Market Operations, Lagos, Nigeria, May 18 - 22, 2009 2 1.2.3 Sierra Leone National Debt Sustainability Analysis (DSA) Freetown, Sierra Leone July 6 - 17, 2009 2 1.2.4 WAIFEM/World Bank Government Debt Management Performance Assessment Mission To Sierra Leone July 20 - 31, 2009 4 1.2.5 The Gambia National Debt Sustainability Analysis Workshop, Banjul, The Gambia August 26 to September 8, 2009 4 1.2.6 WAIFEM/World Bank Government Debt Management Performance Assessment (DEMPA) Mission to Liberia September 7 - 16, 2009 6 1.2.7 Debt Experts Attachment November 9-20, 2009 Madrid and London 6 1.2.8 WAIFEM/MEFMI Regional Medium Term Debt Strategy Workshop (MTDs) November 16 25, 2009, Kigali, Rwanda 7 1.2.9 -
Private Enterprise Partnership for Africa (Pep Africa)
PRIVATE ENTERPRISE PARTNERSHIP FOR AFRICA (PEP AFRICA) Legal, Tax, Regulatory and Market Review of the leasing sector in Liberia by THCLR GHANA LIMITED In Association with J. Mills Lamptey & Co, Chartered Accountants, Ghana And Michael & Michael, Barristers & Solicitors, Sierra Leone (P.O. Box CT 1389 Accra –Ghana. Tel. 233-21 519586. email: [email protected]; www.thclr.com) May 2009 IFC Liberia Leasing Survey EXECUTIVE SUMMARY IFC commissioned this survey in Liberia to access the business case for leasing in the country. The study focused on the market, legislative, accounting and tax environment for leasing. The market review used the following three approaches to determine the potential size of leasing. Equipment imports Net Loans GDP Equipment Import Approach Leasing experience from some developed and emerging market suggests that 20-30% of equipment imports is financed through leases, and for developing countries, 10-20% is financed through leasing. Ghana, Kazakstan and Russia however recorded less than 10%. Since Liberia is a developing country undergoing a post-conflict transformation, we used a leasing potential of 1.0% of equipment imports for Liberia and obtained a potential market size of leasing for the first five years to be $65.5 million. Net Loan Approach It is estimated that in developed economies, approximately 15-20% of the bank loans can be attributed to leasing while in developing economies, the ratio is between 5% and 8%. From our empirical studies in Liberia, we obtained a rate of 6.1% of equipment loans to total net loans. Since Liberia has no leasing market, we based our estimate for the potential for leasing on the 6.1% and obtained a potential market size for leasing in the first five years to be $ 87.8 million. -
Liberia: Financial Diagnostic Update & Feasibility Study for the Possible
Liberia: Financial Diagnostic Update & Feasibility Study for the Possible Entry of a Third Party Cash Management Partner or Agent Aggregator 22nd April 2016 Table of Contents A. EXECUTIVE SUMMARY 4 A.1 FINANCIAL DIAGNOSTIC 4 A.2 FEASIBILITY STUDY FOR THE POSSIBLE INTRODUCTION OF A THIRD PARTY CASH MANAGEMENT PARTNER OR AGENT AGGREGATOR 7 B. LIBERIA FINANCIAL DIAGNOSTIC 9 B.1 OVERVIEW 10 B.1.1 ECONOMY 10 B.1.2 INFRASTRUCTURE 10 B.2 POLICY AND REGULATIONS 13 B.2.1 MOBILE MONEY REGULATIONS 13 B.2.2 ASSESSMENT OF POLICY AND REGULATIONS 15 B.3 FINANCIAL SECTOR 16 B.3.1 BANKING SECTOR 17 B.3.2 OTHER FINANCIAL SERVICE PROVIDERS 21 B.4 REMITTANCE AND PAYMENTS SERVICES 22 B.4.1 REMITTANCE SERVICES 23 B.4.2 PAYMENT SERVICES 24 B.4.3 ASSESSMENT OF REMITTANCE AND PAYMENT SERVICES 25 B.5 MOBILE MONEY 25 B.5.1 PROVIDERS 25 B.5.2 AGENT NETWORK 26 B.5.3 ASSESSMENT OF MOBILE MONEY SECTOR 27 B.6 HIGH VOLUME PAYMENT STREAMS 27 B.6.1 GOVERNMENT TO PERSON (G2P) 29 B.6.2 GOVERNMENT TO BUSINESS (G2B) 29 B.6.3 DEVELOPMENT PARTNERS TO GOVERNMENT (D2G) 30 B.6.4 DEVELOPMENT PARTNERS TO BUSINESS (D2B) 30 B.6.5 DEVELOPMENT PARTNERS TO PERSON (D2P) 31 B.6.6 BUSINESS TO GOVERNMENT (B2G) 31 B.6.7 BUSINESS TO BUSINESS (B2B) 31 B.6.8 BUSINESS TO PERSON (B2P) 31 B.6.9 PERSON TO GOVERNMENT (P2G) 31 B.6.10 PERSON TO BUSINESS (P2B) 32 B.6.11 PERSON TO PERSON (P2P) 32 B.6.12 ASSESSMENT OF POTENTIAL STREAMS FOR MOBILE MONEY 32 C. -
CBL Annual Report 2017 1
JANUARY 1, 2017 TO DECEMBER 31, 2017 CENTRAL BANK OF LIBERIA Office of the Executive Governor January 23, 2018 His Excellency Amb. George M. Weah PRESIDENT Republic of Liberia Mr. President: In accordance with part XI Section 49(1) of the Central Bank of Liberia (CBL) Act of 1999, I have the honor on behalf of the Board of Governors and Management of the Bank to submit, herewith, the Annual Report of the Central Bank of Liberia to the Government of Liberia for the period January 1 – December 31, 2017. Respectfully yours, Milton A. Weeks P.O. BOX 2048, LYNCH & ASHMUN STREETS, MONROVIA, LIBERIA TEL.: (231) 555 960 556 Website: https://www.cbl.org.lr ~ i ~ Table of Contents LIST OF ACRONYMS…………………………………………………………………….ii-vi FORWARD………………………………………………….……………………………..vii-viii HIGHLIGHTS……………………………………………………………………………….ix-xi MISSISON AND OBJECTIVES ............................................................................ 1 BOARD OF GOVERNORS .................................................................................. 2 CHAPTER I:GOVERNANCE AND ORGRANIZATIONAL STRUCTURE ............. 3 1.1 The Board of Governors ....................................................................................................... 3 1.2 Committees of the Board ...................................................................................................... 3 1.3 Policy Decisions by the Board .............................................................................................. 5 1.4 Internal Management Committees ..................................................................................... -
WTO Documents Online
WORLD TRADE RESTRICTED WT/ACC/LBR/3 20 April 2011 ORGANIZATION (11-2062) Working Party on the Original: English Accession of Liberia ACCESSION OF LIBERIA Memorandum on the Foreign Trade Regime In a communication circulated in document WT/ACC/LBR/1 on 25 June 2007, the Government of the Republic of Liberia applied for accession under Article XII of the Agreement Establishing the World Trade Organization (WTO). The General Council established a Working Party on 18 December 2007 (document WT/ACC/LBR/2 refers) with the following terms of reference: "To examine the application of the Government of the Republic of Liberia to accede to the WTO Agreement under Article XII, and to submit to the General Council recommendations which may include a draft Protocol of Accession." In accordance with the established procedures (document WT/ACC/1), the Secretariat is circulating the attached Memorandum on the Foreign Trade Regime received from the Government of the Republic of Liberia. WTO Members wishing to submit questions on the Memorandum are invited to do so by 20 May 2011 for transmission to the Liberian authorities. _______________ WT/ACC/LBR/3 Page i TABLE OF CONTENTS I. INTRODUCTION ....................................................................................................................1 II. ECONOMY, ECONOMIC POLICIES AND FOREIGN TRADE ......................................2 1. Economy ....................................................................................................................................2 (a) General description...................................................................................................................2 -
LIBERIA – DIAGNOSTIC TRADE INTEGRATION STUDY UPDATE Leveraging Trade for Economic Diversification and Inclusive Growth
Report No: ACS4910 (78504-LR) LIBERIA – DIAGNOSTIC TRADE INTEGRATION STUDY UPDATE Leveraging Trade for Economic Diversification and Inclusive Growth December 2013 Poverty Reduction and Economic Management 3 Africa Region Document of the World Bank REPUBLIC OF LIBERIA Government Fiscal Year July 1-June 30 Currency Equivalents Currency Unit = Liberia Dollar (LD) US 1.00 = LD 80.00 Weights and Measures Metric System Abbreviation and Acronyms ABLL Access Bank Liberia Limited Government Government of Liberia ACDI Agricultural Cooperative VOCI Development International/ Volunteers in Overseas Cooperative Assistance ACWL Advisory Centre on WTO Law GPOBA Global Partners hip on Output- Based Aid ADR Alternative Dispute Resolution GSP Generalized System of Preferences AFBLL Afriland First Bank Liberia Limited GTB Guaranty Trust Bank AfDB African Development Bank HFO Heavy Fuel Oil AfT Agenda for Trans formation HHI Herfindahl-Hirschman Index AGOA Africa Growth Opportunities Act HIPC Heavily Indebted Poor Countries ASYCUDA Automated Systems for Customs HNWI High Net Worth Individuals Data ATIBT Association Technique Internationale Des Bois Tropicaux BCE Bureau of Customs and Exercise HS Harmonized Sys tem BDV Brussels Definition of Value HSE Health & Safety Environment BIVAC Bureau of Inspection Valuation IBLL International Bank Liberia Limited Assessment Control CAETs Computer-Assisted Examination ICSID International Center for the Techniques Settlement of Investment Disputes CAR Capital Adequacy Ratio IDA International Development Association CARI -
World Bank Document
43176 v3 Public Disclosure Authorized Public Disclosure Authorized Public Disclosure Authorized Public Disclosure Authorized MINISTRY OF AGRICULTURE COMPREHENSIVE ASSESSMENT OF THE AGRICULTURE SECTOR IN LIBERIA (CAAS-Lib) Volume 2.2 - Sub-Sector Reports Liberia 2007 CAAS-Lib Sub-Sector Reports Volume 2.2 TABLE OF CONTENTS I. LAND AND WATER MANAGEMENT COMPONENT ...............................................3 EXECUTIVE SUMMARY ...................................................................................................3 1. Introduction..................................................................................................................16 2. Terms of Reference......................................................................................................16 3. Background..................................................................................................................16 4. Water Resources Legislation and Administration in Liberia.......................................18 4.1 Water resources legislation.................................................................................18 4.2 Water resources administration and institutions.................................................19 4.3 Agricultural water management..........................................................................22 4.4 Hydrometeorology ..............................................................................................23 4.5 Surface water ......................................................................................................25 -
Financial Sector Development Implementation Plan FIRST Initiative
Liberia Financial Sector Development Implementation Plan FIRST Initiative ACKNOWLEDGEMENTS The Financial Sector Development Implementation Plan (FSDIP) was produced by the Central Bank of Liberia (CBL) with technical assistance of the World Bank Group and financial support from the Financial Institutions Reform and Strengthening (FIRST) Trust Fund Initiative. This report has benefited extensively from inputs derived from reports prepared by various World Bank, International Monetary Fund (IMF), United Nations Development Program (UNDP), and United States Agency for International Development (USAID) missions to Liberia over the last year. In preparation of this report, the task team met senior officials at the CBL and government ministries including the Ministry of Finance and Development Planning, the Ministry of Commerce and Industry, the Ministry of Justice; top management officials from commercial banks, insurance firms, venture capital firms; management of private sector firms ranging from micro enterprises to the largest corporate firms in the country; representatives of microfinance companies, women’s, and professional associations; and other development partners. The CBL provided strategic direction for the FSDIP with input and guidance from government ministries and the private and social sectors. A Financial Sector Steering Committee (FSCC) composed of ex officio senior officials of the institutions listed below identified the key elements of the FSDIP described in the Roadmap for Reforms and will monitor its implementation. CBL Ministry of Finance and Development Planning Ministry of Commerce and Industry National Social Security and Welfare Corporation (NASSCORP) Liberian Bankers Association (LBA) Liberia Business Association The World Bank Group would like to thank all the government authorities and officials for the assistance, cooperation and logistical support provided, as well as the time generously donated by representatives of the private sector consulted as part of this work.