US5225095.Pdf
Total Page:16
File Type:pdf, Size:1020Kb
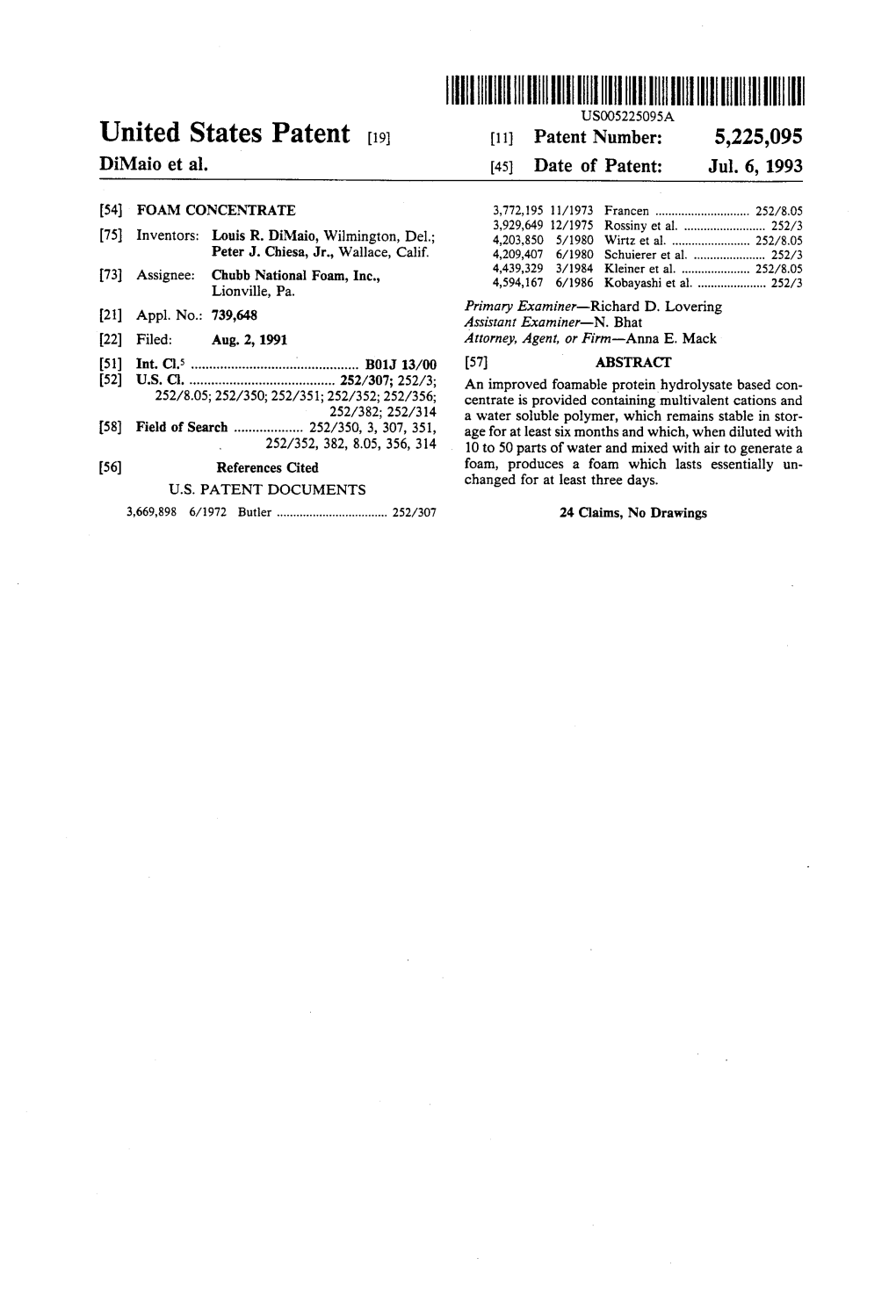
Load more
Recommended publications
-
A Single Blinded, Prospective Trial to Compare the Efficacy Of
Scholars Academic Journal of Pharmacy Abbreviated Key Title: Sch Acad J Pharm ISSN 2347-9531 (Print) | ISSN 2320-4206 (Online) Ophthalmology Journal homepage: http://saspublisher.com/sajp/ A Single Blinded, Prospective Trial to Compare the Efficacy of Rebamipide 2% And Sodium Carboxymethyl Cellulose 1% in Patients of Dry Eye Disease Rajender S Chauhan1*, Ashok Rathi2, JP Chugh3, Vikas Bansal4, Ravinder Kumar5 1Professor, Regional Institute of Ophthalmology Pt B D Sharma Postgraduate Institute of Medical Sciences Rohtak-124001, Haryana, India 2Professor, Regional Institute of Ophthalmology Pt B D Sharma Postgraduate Institute of Medical Sciences Rohtak-124001, Haryana, India 3Professor, Regional Institute of Ophthalmology Pt B D Sharma Postgraduate Institute of Medical Sciences Rohtak-124001, Haryana, India 4Resident, Regional Institute of Ophthalmology Pt B D Sharma Postgraduate Institute of Medical Sciences Rohtak-124001, Haryana, India 5Resident, Regional Institute of Ophthalmology Pt B D Sharma Postgraduate Institute of Medical Sciences Rohtak-124001, Haryana, India *Corresponding author: Rajender S Chauhan | Received: 10.04.2019 | Accepted: 18.04.2019 | Published: 30.04.2019 DOI: 10.21276/sajp.2019.8.4.3 Abstract Original Research Article Dry eye is a multifactorial disease of the tears, due to tear deficiency or excessive evaporation. Recently, Rebamipide has been introduced in the market for the treatment of dry eye disease. It is an amino acid derivative of 2- (1H) - quinolone. Only a few studies are available pertaining to its efficacy on dry eye disease. The study was conducted to compare the efficacy of Rebamipide 2% and sodium carboxymethyl cellulose 1% in patients with dry eye disease. It was a single blinded, prospective, comparative study of 100 patients randomly divided into two groups of 50 patients each. -
To Compare Efficacy of Carboxymethyl Cellulose .5% Eye Drops Versus Use
International Journal of Health and Clinical Research, 2021;4(6):207-210 e-ISSN: 2590-3241, p-ISSN: 2590-325X ____________________________________________________________________________________________________________________________________________ Original Research Article To Compare efficacy of carboxymethyl cellulose .5% eye drops versus use of 0.5% carboxymethylcellulose eye drop with combination of 0.1% tacrolimus ointment twice daily for treatment of severe dry eyes Prerana Agarwal1*, SD Tayal2, Ankur Gautum3 1Associate Professor,Department Of Ophthalmology,Saraswathi Institute of Medical Sciences,Hapur, Uttar Pradesh, India 2Professor,Department of Ophthalmology,Saraswathi Institute Of Medical Sciences,Hapur,Uttar Pradesh, India 3Senior Resident,Department Of Ophthalmology,Saraswathi Institute of Medical Sciences,Hapur, Uttar Pradesh, India Received: 10-01-2021 / Revised: 28-02-2021 / Accepted: 25-03-2021 Abstract Background: Dry eye disease is a common disorder provoking changes in tear film and ocular surface. Untreated dry eye could cause ocular infections, corneal ulcer and blindness. Only a few drugs are authorized so far for the treatment of severe dry eye disease and the possibilities of evolution in this sector are immense.Objectives: Compare efficacy of carboxy methyl cellulose .5% eye drops versus use of 0.5% carboxy methylcellulose eye drop with combination of 0.1% tacrolimus ointment twice daily for treatment of severe dry eyes.Material and Methods: 40 patient presenting with severe dry eye were selected randomly. They were divided into 2 groups. Group I received CMC.5% eye drops four times a day and group II received of 0.1%tacrolimus ointment two times daily and .5% CMC eye drops 4times a day. All patients were evaluated on day 0, 2 weeks, 1 month, 3 month and 6 month for relief in ocular symptoms and diagnostic dry eye tests.Results:The mean age in group I was 40.72 ± 6.85 years and in group II was 39.2 ± 5.28 years. -
Preparation and Characterization of Carboxymethylcellulose Hydrogel Fibers
Preparation and Characterization of CarboxymethylCellulose Hydrogel Fibers Jie Liu1, Chuanjie Zhang2, Dagang Miao1, Shuying Sui1, Fenglin Deng2, Chaohong Dong1, Lin Zhang1, Ping Zhu, PhD1 1College of Textiles and Clothing, Qingdao University, Qingdao, Shandong Province CHINA 2College of Chemistry and Chemical Engineering, Wuhan Textile University, Wuhan CHINA Correspondence to: Ping Zhu email: [email protected] ABSTRACT Carboxymethyl cellulose (CMC) hydrogel fibers sensitivity. It is used in various biomedical were prepared via a solution spinning method with applications primarily due to its easy availability, aluminum sulfate as the crosslinking agent. The high viscosity, good water solubility, nontoxicity, low preparation process of the CMC hydrogel fibers was price, biocompatibility, biodegradability, and good optimized via orthogonal experiments. FTIR, POM, film-forming ability [7-12]. SEM and TGA were used to characterize the structure and properties of the hydrogel fibers. The mechanical Hydrogels prepared via CMC crosslinking are highly properties and absorption ability of the hydrogel absorbent and have excellent physical properties and fibers were also investigated. The results indicated dynamic viscoelasticities [13]. Due to its unique that an even structure was formed in the hydrogel. properties, the CMC hydrogel is a potential candidate The mechanical properties of the hydrogel fibers for wound dressings [14]. CMC hydrogel fibers have were improved with increasing CMC degree of similar properties as CMC hydrogels. Moreover, they substitution. The hydrogel fibers had excellent can be further processed into other forms of moisture absorption performance, and are well-suited biomedical materials. Thus, the hydrogel fiber has for biomedical applications such as wound dressings. attracted increasing attention in many fields [15-16]. -
Study on the Effect of Alkali Metal Chlorides in Aqueous Solutions of Sodium Carboxymethyl Cellulose Using Ultrasound
Asian Journal of Chemistry Vol. 21, No. 8 (2009), 5929-5934 Study on the Effect of Alkali Metal Chlorides in Aqueous Solutions of Sodium Carboxymethyl Cellulose using Ultrasound K. RAJU*† and C. RAKKAPPAN Department of Physics, Annamalai University, Annamalai Nagar-608 002, India E-mail: [email protected] Measurement of ultrasonic velocity, density and viscosity were carried out for the aqueous solutions of sodium carboxymethyl cellulose with various concentrations of sodium chloride, lithium chloride and potassium chloride at different temperatures. The experimental data were used to estimate the ultrasonic parameters like adiabatic compressibility, free length, rao's constant, acoustic impedance, etc. In particular, the ionic hydration numbers for the electrolyte were estimated when the electrolyte is in polymer solutions. The results are interpreted in terms of polymer- solvent, polymer-polymer and polymer-ion interactions. Key Words: Ultrasonic velocity, Polymer-electrolyte, Hydration number. INTRODUCTION The study of the effect of organic and inorganic salt species on polymers in solutions becomes more important in the scientific and technological point of view. Mixtures of polymers and salts in aqueous solution have been utilized in several complex colloidal systems to achieve physico-chemical properties including emulsi- fication, colloidal stability of flocculation, structuring and suspending properties and rheology control. As a result, polymer-salt systems have several industrial appli- cations in diversed areas ranging from latest paint technology, food products, cosmetics and pharmaceutical applications to crop disease formulations1. Molecular interactions between small solute molecules and long chain polymers have been studied by many researchers2-5 with one of the primary objectives of measuring the binding of affinity constants of solutes to synthetic and natural macro- molecules and to correlate the constants with chemical structures of the species involved. -
Aggregation and Deposition Kinetics of Carboxymethyl Cellulose-Modified
water research 46 (2012) 1735e1744 Available online at www.sciencedirect.com journal homepage: www.elsevier.com/locate/watres Aggregation and deposition kinetics of carboxymethyl cellulose-modified zero-valent iron nanoparticles in porous media Trishikhi Raychoudhury a, Nathalie Tufenkji b, Subhasis Ghoshal a,* a Department of Civil Engineering, McGill University, Montreal, Quebec H3A 2K6, Canada b Department of Chemical Engineering, McGill University, Montreal, Quebec H3A 2B2, Canada article info abstract Article history: Transport and deposition of carboxymethyl cellulose (CMC)-modified nanoparticles of Received 6 August 2011 zero-valent iron (NZVI) were investigated in laboratory-scale sand packed columns. Received in revised form Aggregation resulted in a change in the particle size distribution (PSD) with time, and the 18 December 2011 changes in average particle size were determined by nanoparticle tracking analysis (NTA). Accepted 19 December 2011 The change in PSD over time was influenced by the CMC-NZVI concentration in suspen- Available online 30 December 2011 sion. A particleeparticle attachment efficiency was evaluated by fitting an aggregation model with NTA data and subsequently used to predict changes in PSD over time. Changes Keywords: in particle sizes over time led to corresponding changes in single-collector contact effi- Nanoparticle transport ciencies, resulting in altered particle deposition rates over time. A coupled aggregation- Groundwater remediation colloid transport model was used to demonstrate how changes in PSD can reduce the Colloid aggregation transport of CMC-NZVI in column experiments. The effects of particle concentrations in À À Colloid deposition the range of 0.07 g L 1 to 0.725 g L 1 on the transport in porous media were evaluated by Ionic strength comparing the elution profiles of CMC-NZVI from packed sand columns. -
Carboxymethyl Cellulose Sodium Salt
Catalog Number: 101278, 150560, 150561 Carboxymethyl Cellulose Sodium Salt Structure: CAS # : 9004-32-4 Synonyms: CMC; Carboxymethyl ether cellulose sodium salt; Sodium carboxymethylcellulose; Sodium cellulose glycolate; Cellulose glycolic acid sodium salt Physical Description: White to off white powder Derivation: Cellulose fiber with sodium hydroxide and chloroacetic acid. Solubility: Soluble in aqueous solution. The CMC should be added to the water carefully so that it is well dispersed. Adding the solid in portions may be necessary. Adding water to the dry solid produces clumps of solid CMC that is very difficult to dissolve. The solid should be added to the water. Stir gently or shake intermittently; do not stir constantly with a magnetic stirring bar. High heat is not needed and may actually slow down the solubilization process. A mixing device, such as an impeller-type agitator which produces a vortex would allow the powder to be drawn into the liquid, but it may produce some shearing. Note: High viscosity CMC is soluble at up to 50 mg/ml concentration but heat may be required. It is typically used at concentrations less than 20 mg/ml. Stability: Under normal conditions, the effect of temperature on solutions of CMC is reversible. Slight temperature variation has no permanent effect on viscosity. However, long periods of heating CMC solutions at high temperatures, such as autoclaving, will degrade CMC and permanently reduce viscosity. This makes CMC very difficult to sterilize. gamma-Irradiation, like heating, will degrade CMC. High viscosity CMC is more adversely affected by autoclaving and irradiation than is low viscosity CMC. Filtering CMC solutions tends to leave a gel behind because the material is fibrous. -
Bonding Between Cellulosic Fibers in the Absence and Presence of Dry-Strength Agents – a Review
REVIEW ARTICLE ncsu.edu/bioresources BONDING BETWEEN CELLULOSIC FIBERS IN THE ABSENCE AND PRESENCE OF DRY-STRENGTH AGENTS – A REVIEW Martin A. Hubbe Various hydrophilic polyelectrolytes, including cationic starch products, are used by papermakers to promote inter-fiber bonding and increase paper’s dry-strength. Thus, papermakers can meet customer require- ments with a lower net cost of materials, more recycled fibers, or higher mineral content. In the absence of polymeric additives, key mechanisms governing bond development between cellulosic fibers include capillary action, three-dimensional mixing of macromolecules on facing surfaces, conformability of the materials, and hydrogen bonding. Dry-strength additives need to adsorb efficiently onto fibers, have a hydrophilic character, and have a sufficiently high molecular mass. Though it is possible to achieve significant strength gains by optimal usage of individual polyelectrolytes, greater strength gains can be achieved by sequential addition of oppositely charged polyelectrolytes. Superior strength can be achieved by in-situ formation of polyelectrolyte com- plexes, followed by deposition of those complexes onto fiber surfaces. Polyampholytes also hold promise as efficient dry-strength additives. Opportunities for further increases in performance of dry-strength agents may involve fiber surface modification, self-assembled layers, and optimization of the dry film characteristics of dry-strength polymers or systems of polymers. Keywords: Dry strength, Adhesion, Bonding, Polyelectrolytes, Polyampholytes, Cationic starch, Cellulosic fibers, Paper, Polyelectrolyte complexes, Surface modification Contact information: Department of Forest Biomaterials Science and Engineering, North Carolina State University, Campus Box 8005, Raleigh, NC 27695-8005 USA; [email protected] INTRODUCTION Glue is not required in order to make a sheet of paper. -
Sodium Carboxymethyl Cellulose
SODIUM CARBOXYMETHYL CELLULOSE Prepared at the 28th JECFA (1984), published in FNP 31/2 (1984) and in FNP 52 (1992). Metals and arsenic specifications revised at the 55th JECFA (2000). An ADI ‘not specified’ was established for modified celluloses at the 35th JECFA (1989). SYNONYMS Sodium cellulose glycolate, Na CMC, CMC, cellulose gum, sodium CMC; INS No. 466 DEFINITION Prepared from cellulose by treatment with alkali and monochloro-acetic acid or its sodium salt. The article of commerce can be specified further by viscosity. Chemical names Sodium salt of carboxymethyl ether of cellulose C.A.S. number 9004-32-4 Chemical formula [C6H7O2(OH)x(OCH2COONa)y]n where n is the degree of polymerization x = 1.50 to 2.80 y = 0.2 to 1.50 x + y = 3.0 (y = degree of substitution) Structural formula where R = H or CH2COONa Formula weight Structural unit with a degree of substitution of 0.20: 178.14 Structural unit with a degree of substitution of 1.50: 282.18 Macromolecules: greater than about 17,000 (n about 100) Assay Not less than 99.5% of sodium carboxymethyl cellulose, calculated on the dried basis DESCRIPTION White or slightly yellowish, almost odourless hygroscopic granules, powder or fine fibres FUNCTIONAL USES Thickening agent, stabilizer, suspending agent CHARACTERISTICS IDENTIFICATION Solubility (Vol. 4) Yield viscous colloidal solution with water; insoluble in ethanol Foam test Vigorously shake a 0.1% solution of the sample. No layer of foam appears. This test distinguishes sodium carboxymethyl cellulose from other cellulose ethers and from alginates and natural gums. Precipitate formation To 5 ml of an 0.5% solution of the sample add 5 ml of a 5% solution of copper sulfate or of aluminium sulfate. -
Carboxymethyl Cellulose Produced
PEER-REVIEWED ARTICLE bioresources.com Carboxymethyl Cellulose Produced at Different Mercerization Conditions and Characterized by NIR FT Raman Spectroscopy in Combination with Multivariate Analytical Methods Heléne Almlöf Ambjörnsson,a,* Karla Schenzel,b and Ulf Germgård a Carboxymethyl cellulose (CMC) is produced commercially in a two-stage process consisting of a mercerization stage followed by an etherification stage. In this work, extended mercerization stages were used when producing CMC from a spruce dissolving pulp. Near infra-red (NIR) Fourier transform (FT) Raman spectroscopy was used to analyse the molecular structures of the CMC and the gel fractions formed in the CMC preparation. Three different CMC groups were obtained, representing backbone structures of cellulose I, cellulose II, and amorphous cellulose. By applying principal component analyses (PCA) to the spectral data, two CMC classes were identified with different degrees of substitution (DS). Thus, a low degree of substitution was obtained in the CMC if the alkaline concentration in the mercerization stage was only 9.0%, and the backbone structure was cellulose I or II. However, if the alkaline concentration was higher (18.25% or 27.5%), then the degree of substitution in the CMC was also higher, and the backbone structure was more amorphous. Keywords: Carboxymethyl cellulose; Cellulose backbone structures; Degree of substitution; Extended mercerization; Gel formation; Multivariate analytical methods; NIR FT Raman spectroscopy Contact information: a: Karlstad University, Department of Chemical Engineering, SE-651 88 Karlstad, Sweden. b: Martin Luther University Halle-Wittenberg, Department of Natural Science III, Institute of Agriculture and Nutritional Science, Betty-Heimann-Str. 5 D-06120 Halle, Germany. -
Effect of Physicochemical Properties of Carboxymethyl Cellulose on Diffusion of Glucose
nutrients Article Effect of Physicochemical Properties of Carboxymethyl Cellulose on Diffusion of Glucose Elisabeth Miehle 1,2,* , Stephanie Bader-Mittermaier 2, Ute Schweiggert-Weisz 2,3, Hans Hauner 4,5 and Peter Eisner 2,6,7 1 TUM School of Life Sciences, Technical University of Munich (TUM), 85354 Freising, Germany 2 Fraunhofer Institute for Process Engineering and Packaging (IVV), 85354 Freising, Germany; [email protected] (S.B.-M.); [email protected] (U.S.-W.); [email protected] (P.E.) 3 Institute of Nutritional and Food Sciences, University of Bonn, 53113 Bonn, Germany 4 Else Kröner-Fresenius-Center for Nutritional Medicine, School of Life Sciences, Technical University of Munich, 85354 Freising, Germany; [email protected] 5 Institute of Nutritional Medicine, School of Medicine, Technical University of Munich, 80992 Munich, Germany 6 ZIEL-Institute for Food & Health, TUM School of Life Sciences Weihenstephan, Technical University of Munich, 85354 Freising, Germany 7 Faculty of Technology and Engineering, Steinbeis-Hochschule, 01069 Dresden, Germany * Correspondence: [email protected]; Tel.: +49-8161-491-432 Abstract: Soluble dietary fibers (SDF) are known to reduce the post-prandial plasma glucose levels. However, the detailed mechanisms of this reduced glucose release in the human gut still remain unclear. The aim of our study was to systematically investigate the effect of different types of SDF on glucose release in an in vitro model as a prerequisite for the selection of fibers suitable for application Citation: Miehle, E.; Bader- in humans. Three types of carboxymethyl cellulose (CMC) were used to investigate the correlations Mittermaier, S.; Schweiggert-Weisz, between fiber concentration, molecular weight (MW), and viscosity on diffusion of glucose using a U.; Hauner, H.; Eisner, P. -
Colon Targeting of Naringin for Enhanced Cytoprotection Against Indomethacin-Induced Colitis in Rabbits
Drug Design, Development and Therapy Dovepress open access to scientific and medical research Open Access Full Text Article ORIGINAL RESEARCH Colon Targeting of Naringin for Enhanced Cytoprotection Against Indomethacin-Induced Colitis in Rabbits This article was published in the following Dove Press journal: Drug Design, Development and Therapy Eman Ebrahim El Naggar1 Background: Naringin is a promising anti-inflammatory drug against various disorders Elham including ulcerative colitis. However, its oral bioavailability is low (8%) possibly due to Abdelmonem Mohamed 2 cleavage at the upper gut. Consequently, colon targeting would be necessary for drug Thanaa Mohamed Borg2 protection at the upper gut, enhanced oral bioavailability and potentiated cytoprotection Ahmed Ramadan El-Sheakh3 against colitis. Methodology: This study involved the formulation of compression-coated tablets of nar- Mohammed Fawzy Hamed4 ingin employing mixtures of pH-sensitive Eudragit L100-55 (EUD-L100-55) and different 1Department of Pharmaceutical time-dependent polymers including ethyl cellulose (EC), sodium alginate (ALG) and sodium Technology, Faculty of Pharmacy, Horus – University, New Damietta, Eygpt; carboxymethyl cellulose (SCMC). Drug polymer interaction during release was assessed 2Department of Pharmaceutics, Faculty of using Fourier transform-infrared spectroscopy (FT-IR) and differential scanning calorimetry Pharmacy, Mansoura University, (DSC). Tablets were evaluated in vitro. Surface morphology of the optimized tablets either Mansoura, Dakahlia, Egypt; -
Synthesis and Characterization of Sodium Carboxymethyl Cellulose
ﺑﺴﻢ ﷲ اﻟﺮﺣﻤﻦ اﻟﺮﺣﯿﻢ Sudan University of Science & Technology College of Graduate Studies Synthesis and Characterization of Sodium Carboxymethyl Cellulose from the sawdust of Pine wood ﺗﺨﻠﯿﻖ وﺗﺸﺨﯿﺺ ﺻﻮدﯾﻮم ﻛﺎرﺑﻮﻛﺴﻲ ﻣﯿﺜﯿﻞ اﻟﺴﯿﻠﯿﻠﻮز ﻣﻦ ﻧﺸﺎرة ﺧﺸﺐ اﻟﺼﻨﻮﺑﺮ A Thesis submitted in Partial Fulfillment for the Requirement of the Degree of M.Sc. in Chemistry By: Sittana Ahmed Satti B.Sc. (Honors) in Chemistry Supervisor Dr. AdilElhag Ahmed 2015 1 ( .......... وَﻗُﻞ رﱠبﱢ زِدْﻧِﻲ ﻋِﻠْﻤًﺎ) (ﻃﮫ : 114) I Dedication dedicated to Soul of my father, My lovely mother My husband brothers And Sisters II Acknowledgements Thanks to Almighty Allah for giving me strength and health to accomplish this work. I would like to express my gratitude to my supervisor Dr. Adil Elhag Ahmed for continuous supervision, valuable suggestions and advice; his kind help enabled me to achieve my research goals. Thanks are also extended to the Ministry of Higher Education and Scientific research and the family of Sudan Institute for Natural Sciences for their assistance and support. Many thanks to my family, friends and colleagues at the research laboratory (Soba) for their help and encouragement. Also I would like to thank the staff of the Central Lab., Khartoum University for the IR spectral measurements and the staff of General Directorate for Petroleum Labs., Research & Studies (PLRS) for XRD measurements. III Abstract Sawdust or wood dust is a by-product of cutting, grinding, drilling, sanding, or otherwise pulverizing wood with a saw or other tool. It is composed of cellulose, hemicelluloses and lignin. This study aimed to utilize sawdust of wood for preparing sodium- carboxymethylcellulose (Na-CMC).