United States Patent (19) (11 Patent Number: 4,964,261 Benn 45) Date of Patent: Oct
Total Page:16
File Type:pdf, Size:1020Kb
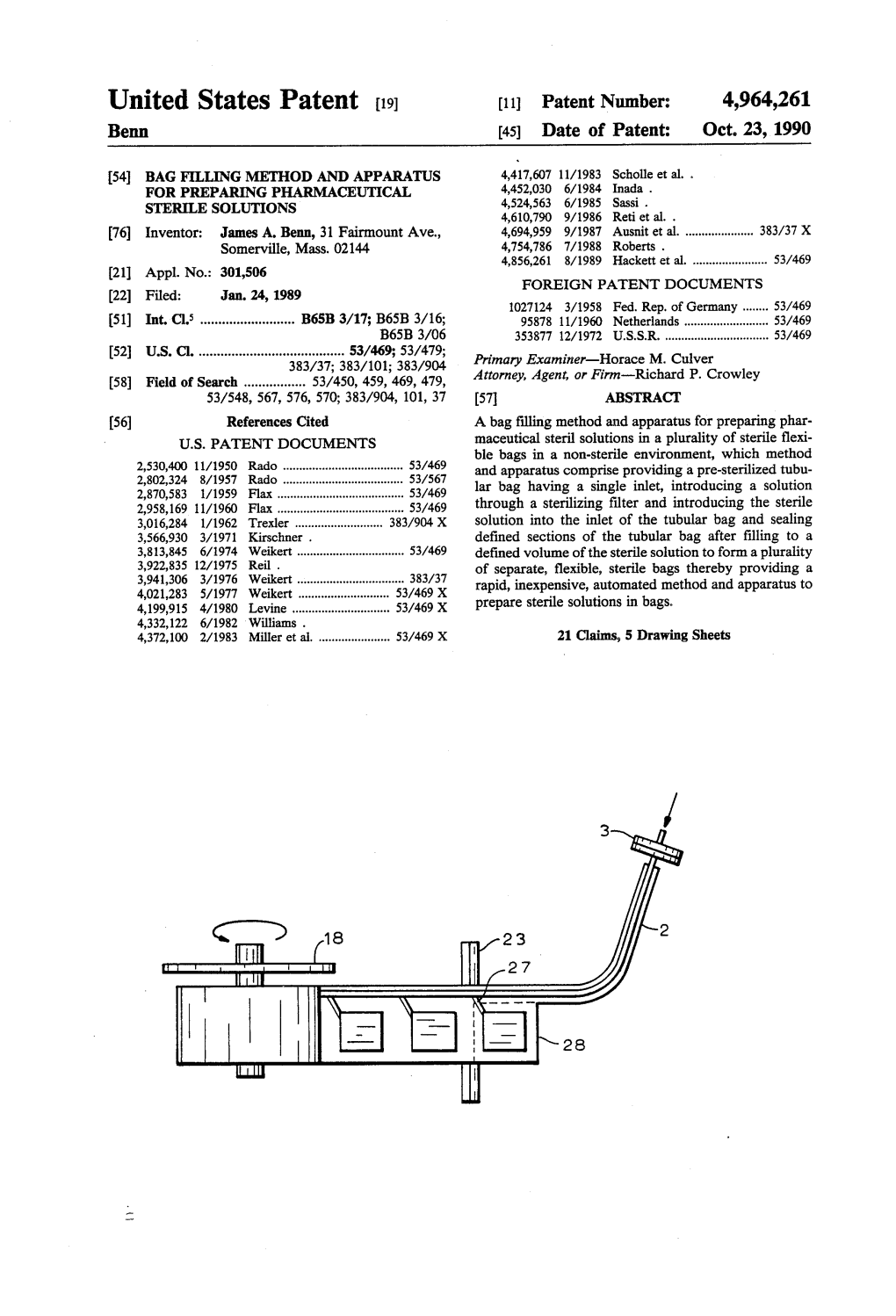
Load more
Recommended publications
-
Starview Packaging Machinery, Inc
Food Packaging Equipment MSTS SERIES MANUAL SHUTTLE FILM TO TRAY FOOD PACKAGING MACHINES • Complete machine Keypad control • Automatic film feed, seal & trim and scrap with digital display rewind for clear or random print film • Machines offered for applications that • Stainless steel wipe down design require modified atmosphere (MAP) MSTS-1214 MSTS-1012 Description Starview’s MSTS Series are designed and competitively priced for “fresh counter” packaging, typically a clear or printed lm to a preformed tray for food manufacturing companies, catering, grocery stores, delicatessens, etc. The MSTS Series is ideal for low to medium production. This series machines can adapt to seal for a wide range of product tray sizes by simply changing the tooling. The MSTS Series machines trim the lm to the prole of the tray and automatically rewind the scrap web. The MSTS Series sealers will provide years of dependable performance Specications Model MSTS-1012 MSTS/MAP-1012 Maximum sealing area: 10.4" x 12.8" 10.4" x 12.8" Open loading stations: 1 1 Vacuum pump installed: N/A Standard Prole lm trim: Standard Standard Maximum tray depth: 3.9” 3.9” Maximum lm width: 12.5” 12.5” Maximum roll diameter: 9.4" 9.4" Average cycle speed: 1-4 cpm 1-4 cpm Approximate size: 34"W x 45"D x 27"H 34"W x 45"D x 27"H Approximate weight: 250 LB. 270 LB. Model MSTS-1214 MSTS/MAP-1214 MSTS/MAP-1214B Maximum sealing area: 12.2" x 14.7" 12.2" x 14.7" 12.2" x 14.7" Open loading stations: 1 1 1 Vacuum pump installed: N/A Standard Optional Prole lm trim: Standard Standard Standard Maximum tray depth: 4.7” 4.7” 8” Maximum lm width: 14.5” 14.5” 14.5” Maximum roll diameter: 9.8" 9.8" 9.8" Average cycle speed: 1-4 cpm 1-4 cpm 1-4 cpm Approximate size: 40"W x 42"D x 54"H 40"W x 42"D x 54"H 40"W x 42"D x 54"H Approximate weight: 450 LB. -
Fully Automatic Inline Blister Packaging Machines
CBS SERIES FULLY AUTOMATIC INLINE BLISTER SEALING MACHINES CBS Series Inline machine shown with card and blister feeders, optional product detection station, light tower and finished package unloader. EXPERIENCE THE STARVIEW ADVANTAGE: A wide range of standard and custom automation features available to match customer requirements. Large format inline design to provide high volumes of nished packages and match linear plant workow congurations. ANSI Class 4 machine safety for operator protection. Automatic blister feeder, card feeder & nished package unloader provide reduced labor costs. Color touch screen HMI for the ultimate in operator convenience and accessibility. Includes storage for 99 databases and on-screen data tracking. A Starview exclusive remote access via standard Ethernet hardwire or optional Wi-Fi router gives management access to real-time process information from the machine. AC Variable frequency precision cam index conveyor drive for smooth operation and position repeatability. Uses quick-change durable aluminum tooling. Industry leading design, construction, features and customer support. DESCRIPTION: Starview’s CBS Series Automated Inline Conveyor type blister sealing machines are ideal for high volume or JIT production. Given the proper conditions these machines are capable of up to 20 cycles per minute in production. Starview’s automated inline conveyor blister sealing machines are built with the capability to feed blister(s), blister card(s) and discharge nished packages when proper tooling is installed. The CBS Series machines may be used for conventional carded blisters, trapped blisters, club store trapped packages, full face blisters and half-clamshell styles as well as some applications using Tyvek, foils and other heat sealable lidstock. -
Report on the Supply of Cigarettes and Tobacco and of Cigarette and Tobacco Machinery
Report on the Supply of Cigarettes and Tobacco and of Cigarette and Tobacco Machinery Presented to Parliament in pursuance of Section 9 of the Monopolies and Restrictive Practices {Inquiry and Control) Act, 1948 Ordered by The House of Commons to be Printed 4th July, 1961 LONDON HER MAJESTY'S STATIONERY OFFICE PRICE IOJ. 6d. NET 218 MEMBERS OF THE MONOPOLIES COMMISSION R. F. Levy, Esq., Q.C. {Chairman) Professor G. C. Allen, C.B.E. Andrew Black, Esq., C.B.E. Brian Davidson, Esq. Dr. L. T. M. Gray* I. C. Hill, Esq., C.B.E. W. E. Jones, Esq., C.B.E. Ashton W. Roskill, Esq., Q.C* Sir Frank Shires A. S. Gilbert, C.B.E. (Secretary) * Dr. Gray, because of his connections with the machiii^i^ri^idustrv and Mr ROQUIT ^use he was appointed a member during the closing staged have n^l Seen part kifte inquiry. ii CONTENTS Page INTRODUCTION 1 PART I. CIGARETTES AND TOBACCO CHAPTER 1. General Background 2 CHAPTER 2. History of the Tobacco Industry 14 CHAPTER 3. The Imperial Tobacco Company (of Great Britain and Ireland) Limited 33 CHAPTER 4. Other Manufacturers 55 CHAPTER 5. Distribution 67 CHAPTER 6. Bonus 82 CHAPTER 7. Conclusions as to the Conditions defined in the Act .. 90 PART II. MACHINERY CHAPTER 8. General Background 92 CHAPTER 9. History and Organisation of the Machinery Industry .. 97 CHAPTER 10. Molins Machine Company Limited: Financial Arrange• ments and Organisation 102 CHAPTER 11. Molins Machine Company Limited: The Supply of Machinery 107 CHAPTER 12. Conclusions as to the Conditions defined in the Act . -
Packaging Machinery Hundreds of Private Companies Are Active in the U.S
Freedonia Private Companies Report #1316 Packaging Machinery Hundreds of private companies are active in the U.S. packaging machinery industry. Packaging Machinery - Private Companies Report profiles more than 130 private U.S. packaging machinery manufacturers and distribu- tors. This information will assist in making decisions concerning acquisitions, joint ventures and cooperative agreements. Report Publication Date: August 2000 Price: $3,200 Examine the report highlights, sample pages and table of contents Pages: 268 on the following pages and see how Packaging Machinery - Private Companies Report can serve as a valuable decision making tool for your company. Brochure Index Table of Contents and List of Tables ............................................... 2 List of Companies Profiled .............................................................. 3 Sample Pages and Tables from: Private Company Profiles ............................................ 4 Market Overview ......................................................... 6 Industry Structure ........................................................ 7 Report Highlights ............................................................................. 8 About the Company ......................................................................... 9 Advantages of Freedonia Reports ..................................................... 9 Our Customers .............................................................................. 10 Related Studies and Reports from Freedonia ................................ -
Success and Failure Factors for the Adoption of Bio-Based Packaging
Success and Failure Factors for the Adoption of Bio-Based Packaging UMIT EMRE ERDOGAN Master of Science Thesis Stockholm, Sweden 2013 Success and Failure Factors for the Adoption of Bio-Based Packaging Master Thesis Report Umit Emre ERDOGAN Academic Supervisor: Michael NOVOTNY Company Supervisor: Tom LINDSTRÖM Company: Innventia Master of Science Thesis INDEK 2013:131 KTH Industrial Engineering and Management International Master in Industrial Management SE-100 44 STOCKHOLM Master of Science Thesis INDEK 2013:131 Success and Failure Factors for the Adoption of Bio-Based Packaging Umit Emre ERDOGAN Approved Examiner Supervisor 2013-June-30 Staffan Laestadius Michael Novotny-Tom Lindström Commissioner Contact person Cali Nuur Tom Lindström Abstract The purpose of this study is to provide insight into the factors that determine the willingness of key market players in the Indian food industry to adopt bio-based plastic packaging. First, the key market players are identified within the important market segments in the specified industry. After the identification of key players, the literature is surveyed in the context of eco- innovations, innovation adoption in emerging countries and Roger’s market adoption theory. In addition, the sustainability point of packaging and its perceived attributes are elaborated on and analyzed using the selected framework. Semi-structured interviews with the key market players in the food packaging industry are conducted in the context of adoption theory. The results of the survey reveal that there are only two groups in the industry, those that are currently considering bio-based plastic packaging and those that have not yet considered it. Due to the low number of completed questionnaires, advanced multivariate statistical methods cannot be used for data analysis. -
British American Tobacco Australia Limited Submission on the Tobacco Plain Packaging Bill 2011 and the Trade Marks Amendment (Tobacco Plain Packaging) Bill 2011
British American Tobacco Australia Limited Submission on the Tobacco Plain Packaging Bill 2011 and the Trade Marks Amendment (Tobacco Plain Packaging) Bill 2011 Submissions to the House of Representatives Health and Ageing Committee 22 nd July 2011 INDEX PLAIN PACKAGING EXECUTIVE SUMMARY 3 1. INTRODUCTION 7 1.1 BATA and the Australian Tobacco Market 7 1.2 BATA supports evidence-based and proportionate regulation 7 2. LEGAL BARRIERS TO MANDATING PLAIN PACKAGING 8 2.1 Introduction 8 2.2 Plain packaging violates Australian domestic law 8 2.3 Breaches of International Treaties — Paris Convention 9 2.4 Breaches of International Treaties — TRIPS Agreement 9 2.5 Breaches of International Treaties — GATT 10 2.6 Breaches of International Treaties — TBT Agreement 10 2.7 Serious ramifications can flow from breaches of Australia’s Treaty obligations 11 2.8 The Government has received legal advice regarding Plain Packaging and its impact on its international treaty obligations 11 2.9 FCTC does not impose any obligation to introduce plain packaging 12 3. EVIDENCE 14 3.1 The TPP Bill is not supported by real evidence. 14 3.2 Concerns around lack of real evidence. 14 4. POOR POLICY-MAKING PROCESS 16 5. PLAIN PACKAGING NOT IMPLEMENTED BY OTHER GOVERNMENTS 17 6. UNINTENDED CONSEQUENCES 19 6.1 Waste of taxpayers’ money in legal fees 19 6.2 Possible compensation 19 6.3 What will the impact of plain packaging be on the price of cigarettes? 19 6.4 Significant impact on illegal tobacco trade 20 6.5 Cigarettes – not just packs – subject to counterfeit 21 6.6 Tobacco counterfeiting – a serious world wide problem 21 7. -
Packaging Machinery Packaging Machinery
PACKAGING MACHINERY PACKAGING MACHINERY Interpack™ provides a machinery solution for a wide range of applications and budgets. The modular design of each case sealer combined with innovative features and materials will provide superior performance for many years to come. Standard machines are available in many drive styles and can be outfitted with our ET 2Plus taping head in either 2 or 3-inch widths. Heavy duty construction, dual column design, oversized gearmotors, and reliability are the hallmarks of the Interpack machinery line. Which Machine is Right for Me? CHOOSE THE BASICS Case Styles: RSC, OPF, Telescopic, End Load, Bliss, Other Case Size: Standard, Oversized, Other Contents: Lightweight, Unstable, Void-Filled, Overfilled Tape: Tape Grade, Adhesive (Hot Melt, Acrylic or Natural Rubber), Width (2", 3" or wider) CHOOSE OPTIONS & FEATURES Options: Pack Tables, Casters, Top Squeezers Case Forming: Automatic, Operator-Formed Case Coding: Large Character Ink Jet Coding, Print & Apply Conveyors: Infeed or Exit, Belt or Roller, Powered or Gravity 888-898-7834 | itape.com TABLE OF CONTENTS 4 USA SERIES 8 RSA SERIES Operator-fed machines Operator-fed machine that are adjustable to a that will automatically wide range of case sizes. adjust for the case width and case height of each case that is fed through the machine. 10 UA SERIES 11 CE SERIES Operator-free machines Operator-free machines that that are adjustable, will will form a knocked down fold the top four flaps of uniform sized case, fold the case and apply tape. bottom four flaps and apply tape. ® 12 TAPE HEADS 13 BETTER PACK DISPENSERS Interpack™ tape heads are Operator-run electric and available in both standard line manual tabletop water- speeds and high speed. -
Union Standard Catalog
25,000 MODERN USED & REBUILT PROCESSING & PACKAGING MACHINES EQUIPMENT VISIT OUR NEW WEB SITE www.unionmachinery.com Our Huge Inventory is now on the Web with Descriptions and Photos. NEW YORK CHICAGO MEXICO TEL: 718-585-0200 • FAX: 718-993-2650 TEL: 773-376-5400 • FAX: 773-376-0634 TEL: 5-300-3033 • FAX: 5-301-2934 801 E. 141 ST., 4248 W. 47 ST., SAN LUIS TLATILCO 6-A, COL SAN LUIS TLATILCO UNION STANDARD UNION STANDARD BRONX., NY 10454 CHICAGO, IL 60632 NAUCALPAN, EDO. DE MEXICO C.P. 53370 E-mail: [email protected] Internet: www.unionmachinery.com UNION STANDARD EQUIPMENT COMPANY UNION CONFECTIONERY MACHINERY COMPANY DIV. OF NATIONAL EQUIPMENT CORP. USED & LITY REBU UA IL Q T WORLD'S LARGEST DEALERS OF 801-825 East 141st Street Bronx, New York 10454-1917 MODERN RECONDITIONED PACKAGING & PROCESSING MACHINERY Tel: (718) 585-0200 • Fax: (718) 993-2650 E-mail: [email protected] ES 12 TABLISHED 19 WE ARE IN THE BEST POSITION EVER TO MEET YOUR MACHINERY NEEDS Established in 1912, four generations of the Greenberg family have established Union Standard and Union Confectionery as the world's largest suppliers of processing and packaging equipment with more than 25,000 machines in our New York, Chicago, Mexico D.F. and London facilities. There has never been a better time to contact us for buying and selling machinery. WE OFFER: THE WORLD'S LARGEST INVENTORY More than 25,000 processing and packaging machines in stock and available for your inspection MODERN USED & RECONDITIONED EQUIPMENT Late style equipment which can be reconditioned and set to your specifications. -
Discussion on the Control Technology in the Design of Packaging Machinery
Advances in Social Science, Education and Humanities Research (ASSEHR), volume 206 2018 International Conference on Advances in Social Sciences and Sustainable Development (ASSSD 2018) Discussion on the Control Technology in the Design of Packaging Machinery Gang Qiao 1School of Mechanical Engineering, Zhengzhou University of Industrial And Technology, 451100, China [email protected] Keywords: Packaging Machinery; Design; Control Technology Abstract: With the rapid development of China's economy, the number of enterprises in all walks of life is increasing.No matter food, daily necessities or large electrical appliances, any items should be packaged before they get out of the factory. Products of different quality and nature have different requirements for packaging. Some goods of special nature may require strict preservation of the environment. It is precisely because of the wide need for packaging, packaging has become a separate industry, and now its position is becoming more and more important in product chains. Good packaging can protect the goods from damage in the transportation and storage process, to avoid unnecessary economic losses. Packaging machinery plays an important role in the packaging process. The core content of packaging machinery, control technology, which is directly related to the quality of packaging, is fully discussed and studied in this paper. Preface Packaging machinery is an indispensable part of the packaging industry. The quality of packaging machinery is a very important factor which affects the quality of packaging and the efficiency of the factory production. The development of China's packaging industry is more backward than that in the West. The existing packaging technology and packaging machinery can not fully meet the requirements of the market for the types, quality, performance and number of packaging. -
Filling and Packaging Machinery
SUPPLIER OF PACKAGING MACHINERY Filling and Packaging Machinery Machines Catalogue CONTENTS SUPPLIER OF PACKAGING MACHINERY Do you want customers to prefer your product over the variety of other supplies on the market? If your answer is Yes, then the machine-building plant PROFITEX will help you achieve this! 1. The Linear Type The machine-building plant PROFITEX is one of the leading manufacturers of packaging and labelling machines for the food and other industries. The history of our achievements is a classic example of foundation and development that owe Packaging Machines 2 much to the right choices we made in the very beginning. Our formula of success is working for individual customer needs – the product and its packaging. Thus, our customers can get not only high-quality packing machines, but the packaging 2. The Rotary Type Packaging Machines 8 designed specially for their product. The plant offers a full range of services: from project creation to delivering the machines right to the client. We also support our customers all the way, including the after-sales services. During fourteen years of its development, PROFITEX managed to not only widen the range of produced packaging 3. Vertical Automated Packaging Machines 23 machines, but also to design and introduce labelling machines, automated filling lines, a device for sealing foil and polyethylene, conveying systems, accumulation tables, and multi-packers. We are especially proud of our laser marker 4. Multi-Packing Machines 24 designed for the quick and efficient application of any information on different types of packaging. Thanks to the continuous participation in domestic and national exhibitions, seminars, and conferences we keep moving 5. -
High-Tech Coatings Enhance the Efficiency and Performance Of
Philip Morris created for its Benson & Hedges 100’s DeLuxe Ultra Lights Spotlight Report in a flip-top box was certainly no exception. ® Packaging Machinery Packaging such boxes normally requires special attention to avoid scratches on the film and scuffs on the blank, but the unique construction of the DeLuxe Lights pack blank compounded the problem. In addition High-tech coatings enhance the efficiency to the highly reflective surface and the embossed crest, the clear and performance of packaging equipment polypropylene film had to be free of scratch marks. Adding a protective coating to the FDA, USDA, NSF & AgriCanada-compliant coatings provide hardness, corrosion packaging machine parts seemed the resistance, dry lubricity and long life for all types of metal parts on machinery. Side folding plates (left) and bottom fold plates (right) on the over-wrap machines used to obvious answer to the problems, but wrap Marcal Paper's pocket tissue packs have been protected with Magnaplate HCR® to resist wear and reduce down time. conventional coatings such as nickel, ackaging engineers face a wide chrome and similar attempts from variety of challenges when it Folding plates unit, according to a company source. past experience did not solve them. Pcomes to maintenance and Coating avoids abrasion and It would also eliminate costly down- Either the scratches in the polypropy- operation of a broad spectrum of corrects skewed overwraps time problems. machinery counted on to perform “We knew exactly what we had to such tasks as wrapping, sealing, cut- Marcal Paper Mills, Inc., Elmwood have,” said Marcal’s director of con- ting, forming, pouching, blister pack- Park, NJ, was facing the challenge of verting. -
OMAC's Effort to Standardize Packaging Machinery Automation
OMAC’s Effort to Standardize Packaging Machinery Automation: The role of OPW and PackML in development of “Gen3” packaging machinery By: Shelton Wright University of Florida – Packaging Science Program March 6, 2005 Faculty Contact: Dr. Bruce Welt University of Florida Coordinator – Packaging Science Program 111 Frazier Rogers Hall Gainesville, FL 32611-0570 Tel: 352.392.1864 x 111 Email: [email protected] INTRODUCTION An analysis of consumer behavior reveals that life cycles for packaging dimensions, materials, and designs are continuously decreasing. As a result, producers and end users of packaged goods need packaging machinery and control systems that enable them to react quickly to changing consumer demands. To address this problem, end users are requiring machinery and control suppliers to provide innovative solutions as they strive to maintain competitive advantages for packaged products. This inherent need for flexibility and efficiency is driving technological advances in packaging machinery automation and control systems. In addition to the increased responsiveness and agility needed to accommodate modern packaging, there is an increased push to make these adjustments in a “Lean Manufacturing” environment. The goal of lean production is to eliminate waste in all areas of production, increase responsiveness, and minimize costs. Ultimately, lean manufacturing demands highest levels of efficiency while achieving highest levels of quality. Successful implementation of lean manufacturing requires efficient integration of packaging machine automation and control systems into enterprise-resource planning (ERP) systems. Lack of standardization, however, limits communications and data transfer between production machinery and the supply chain. Proprietary, vendor- specific solutions may be inhibiting communications and raising interfacing costs.