(12) Patent Application Publication (10) Pub. No.: US 2011/0168425A1 Basfar Et Al
Total Page:16
File Type:pdf, Size:1020Kb
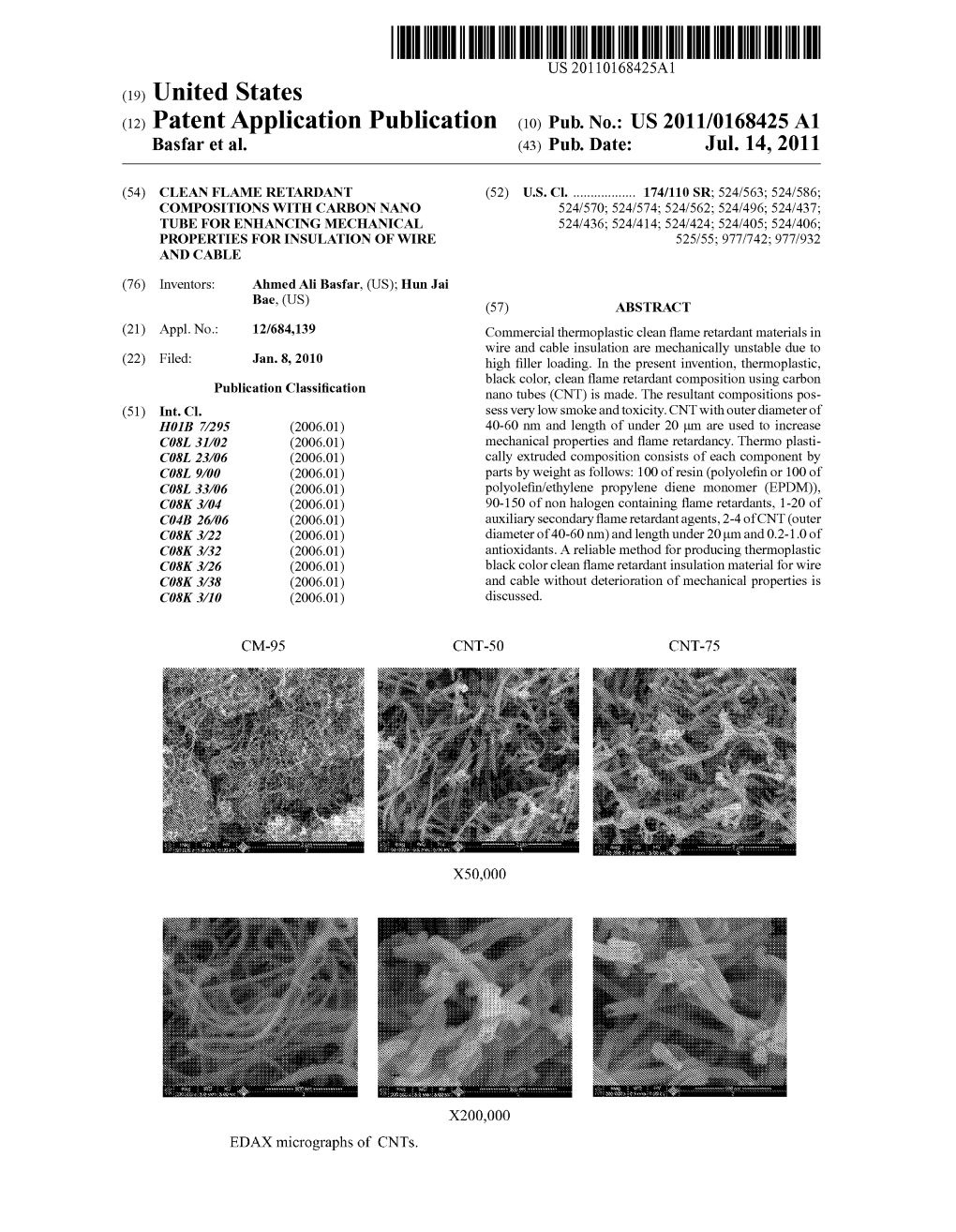
Load more
Recommended publications
-
Synergistic Effects of Zinc Borate and Aluminum Trihydrate on Flammability Behaviour of Aerospace Epoxy System
SYNERGISTIC EFFECTS OF ZINC BORATE AND ALUMINUM TRIHYDRATE ON FLAMMABILITY BEHAVIOUR OF AEROSPACE EPOXY SYSTEM A. De Fenzo1,2, Cristina Formicola1,2 , Mauro Zarrelli1,2*, Alberto Frache3 Michele Giordano1,2 and Giovanni Camino3 1 IMCB – Institute of Composite and Biomedical Materials, CNR – Research National Council, P E. Fermi 1, Portici 80055, ITALY 2 IMAST – Technological District on Polymeric and Composite Materials Engineering, P E. Fermi 1, Portici 80055, ITALY 3 Material Science and Chemical Engineering Dept., Polytechnic of Turin in Alessandria, Via Teresa Michel 5, 15100 Alessandria, ITALY *[email protected] SUMMARY Flame retardancy of mono-component epoxy resin, used for aerospace composites, treated with zinc borate (ZB), aluminum trihydrate (ATH) and their mixtures at different percentages have been investigated by morphological and thermal characterization. Cone calorimeter data reveal that peak HRR decreases when synergistic effects between additives occur. Keywords: Epoxy Resin; Fire retardancy; Zinc borate; Aluminum trihydrate; Cone calorimeter INTRODUCTION Zinc borate is an effective inorganic flame retardant and it possesses characteristic properties of flame retardancy (FR), smoke suppression, promoting charring, etc.[1-2] particularly important according to new fire standards. Zinc borate is commonly used as multifunctional flame retardant in combination with other halogenated or halogen-free flame retardant systems to boost FR properties [3-4]. Its efficacy depends upon the type of halogen source (aliphatic versus aromatic) and the used polymer root. The zinc borate can generally display synergistic effects with antimony oxide in fire retardancy. In the presence of aluminium trihydroxide (ATH) or magnesium hydroxide (Mg(OH)2), this synergy can be augmented significantly [5]. -
Solid Phase Synthesis of Anhydrous Zinc Borate from Zinc and Boron Oxide and Utilization As a Flame Retardant in Dye and Textile
Gazi University Journal of Science GU J Sci 27(3):987-991 (2014) Solid Phase Synthesis of Anhydrous Zinc Borate from Zinc and Boron Oxide and Utilization as a Flame Retardant in Dye and Textile Barış AYAR 1, Metin GÜRÜ 2, Çetin ÇAKANYILDIRIM 3,♠ 1Hitit University, Ömer Derindere Vacational High School, 19500 Osmancık, Çorum, Turkey 2Gazi University, Eng. Faculty, Chemical Eng. Depart. 06570, Maltepe-Ankara, Turkey 3 Hitit University, Eng. Faculty, Chemical Eng. Depart. 19030 Çorum, Turkey Received:30/01/2014 Revised: 01/04/2014 Accepted:17/04/2014 ABSTRACT Durability of materials against flame and stability at high temperatures are very important in order to increase the field of use. Non-flammability is not the only requirement; these materials should not have toxic gas products during the burning, also. Anhydrous zinc borate was chosen as flame retardant due to its advantages, such as; light weight, high melting point, low thermal expansion, and intrinsic smoke suppression and corrosion resistance properties. For the synthesis, metallic zinc and anhydrous boron oxide powders were mixed in the attritor working at 600 rpm. Powder product was sintered under atmospheric conditions according to the phase change temperature that was determined by TGA-DSC analyses. Synthesized zinc borate was grinned up to nanometer size by Spex type grinder. Zinc borate was introduced in binder to decrease the flammability. The properties of the produced materials were determined and compared by LOI, TGA-DSC, SEM and oven according to the zinc borate ingredients. Key Words : Zinc borate, Pigment, Flame retardant, Flame resistant dye 1. INTRODUCTION Dyes are widespread used in our lives as a coating many cases, alumina, magnesium hydroxide, antimony material to resist corrosion [1]. -
4. Inorganic Flame Retardants. Plastics Can Be Given Flame Retardant Characteristics by Introducing Elements of Organic, Inorganic and Halogen Origin
4. Inorganic Flame Retardants. Plastics can be given flame retardant characteristics by introducing elements of organic, inorganic and halogen origin. Such elements include magnesium, aluminium, phosphorous, molybdenum, antimony, tin, chlorine and bromine. Flame retardants are added in either the manufacturing step of the polymer or the compounding step of the polymeric article. Phosphorous bromine and chlorine are usually included as some organic compound. Inorganic flame retardants are usually added together with other flame retardants to provide a more efficient flame retardant action through synergism. Halogen flame retardants usually need an addition of about 40% in order to be effective, and this affects the properties of the polymer quite negatively. Structural integrity of the polymer article is often very important, and a drastic decrease in strength and other mechanical properties is simply not acceptable. The efficiency of halogen flame retardants is often enhanced by the addition of inorganic flame retardants. A smaller mass percentage halogen flame retardant is now needed, so the adverse effect on the polymer properties is also reduced (Touval, 1993) . 4.1 Antimony Compounds The antimony compounds used for flame retardancy include antimony trioxide, antimony pentoxide and antimony-metal compounds. In 1990 in the United States alone, the use of antimony trioxide amounted to 20 000 metric tons just for the flame retardancy of plastics. Antimony oxide is readily found in nature but in very impure form. This is not suitable for 29 direct use as flame retardant, so antimony oxide is often rather produced from antimony metal. There are therefore many different grades of antimony oxide that can be used for flame retardants. -
The Development of Zinc Borate Production Process
A-PDF MERGER DEMO The Development of Zinc Borate Production Process By H.Emre ELTEPE A Dissertation Submitted to the Graduate School in Partial Fulfillment of the Requirement for the Degree of MASTER OF SCIENCE Department: Chemical Engineering Major: Chemical Engineering ø]PLU,QVWLWXWHRI7HFKQRORJ\ ø]PLU7XUNH\ November, 2004 We approve the thesis of H.Emre ELTEPE Date of Signature ………………………………………….. 21.12.2004 Prof. Dr. Devrim BALKÖSE Supervisor Department of Chemical Engineering ………………………………………….. 21.12.2004 Prof. Dr. Semra ÜLKÜ Co-Supervisor Department of Chemical Engineering ………………………………………….. 21.12.2004 Prof.Dr. Tamerkan ÖZGEN Department of Chemistry ………………………………………….. 21.12.2004 Assist.Prof.Fehime ÖZKAN Department of Chemical Engineering ………………………………………….. 21.12.2004 Assist.Prof.$\VXQ62)82ö/8 Department of Chemical Engineering ………………………………………….. 21.12.2004 Prof. Dr. Devrim BALKÖSE Head of Department ACKNOWLEDGEMENT I would like to express my deepest gratefullness to my advisors Prof. Devrim BALKÖSE and Prof. Semra ÜLKÜ for their support, guidance and sharing their valuable experiences throughout the study and the preparation of the thesis which has been a very important experience for my future carreer. I would like to state my special thanks to my friends $\NXW(5'2ö'8 Sevdiye ATAKUL, Mehmet GÖNEN, gQL] %ø562< DQG <DUNÕQ g=*$5ø3 for their help, encouragement and friendship throughout this project. I would also like to thank to Gökhan (5'2ö$1, Duygu2÷X].,/,d 0LQH%$+d(&ø and Evrim YAKUT for their help for SEM, EDX and X-RAY analyses, Burcu ALP for TGA analyses and Özlem Ça÷lar DUVARCI and Filiz ÖZMIHÇI for FTIR analysis ùHULIH ùDKLQ g=$/3 DQG %HOJLQ TUNÇEL for their help throughout the experiments. -
Hydrated Zinc Borates and Their Industrial Use
Review Hydrated Zinc Borates and Their Industrial Use David M. Schubert AvidChem LLC, Lone Tree, CO, 80124 USA; [email protected] Received: 17 June 2019; Accepted: 26 June 2019; Published: 30 June 2019 Abstract: Zinc borates are important chemical products having industrial applications as functional additives in polymers, bio-composites, paints and ceramics. Of the thirteen well documented hydrated binary zinc borates, Zn[B3O4(OH)3] (2ZnO∙3B2O3∙3H2O) is manufactured in the largest quantity and is known as an article of commerce as 2ZnO∙3B2O3∙3.5H2O. Other hydrated zinc borates in commercial use include 4ZnO∙B2O3∙H2O, 3ZnO∙3B2O3∙5H2O and 2ZnO∙3B2O3∙7H2O. The history, chemistry, and applications of these and other hydrated zinc borate phases are briefly reviewed, and outstanding problems in the field are highlighted. Keywords: borate; zinc; polymer additive; fire retardant; bio-composite 1. Introduction Zinc borates rank in the top ten boron-containing industrial chemicals in terms of global production and use [1]. Tens of thousands of tons of zinc borates are used annually in various applications utilizing their special properties. The family of binary zinc borates of general composition aZnO∙bB2O3∙cH2O, where c is >0, contains at least thirteen unique crystalline compounds; the most important these is 2ZnO∙3B2O3∙3H2O, or Zn[B3O4(OH)3], which is usually referred to in commerce as 2ZnO∙3B2O3∙3.5H2O, owing to an early error in characterization. Major applications of zinc borates include lending durability to bio-composite building materials and improving fire performance and electrical properties of polymers. Zinc borates also serve as corrosion inhibitors, fire retardants and preservatives in coatings, fluxes in ceramic bodies and glazes, hosts for scintillation compounds, and ingredients in agricultural micronutrients. -
FLAME RETARDANTS in PRINTED CIRCUIT BOARDS Chapter 3
FLAME RETARDANTS IN PRINTED CIRCUIT BOARDS Chapter 3 FINAL REPORT August 2015 EPA Publication 744-R-15-001 3 Chemical Flame Retardants for FR-4 Laminates This chapter summarizes the general characteristics of flame retardants and associated mechanisms of flame retardancy. The flame-retardant chemicals currently used in printed circuit boards (PCBs) are also briefly introduced, with more detailed information about their potential exposure pathways, toxicity, and life-cycle considerations presented in later chapters. 3.1 General Characteristics of Flame-Retardant Chemicals Fire occurs in three stages: (a) thermal decomposition, where the solid, or condensed phase, breaks down into gaseous decomposition products as a result of heat, (b) combustion chain reactions in the gas phase, where thermal decomposition products react with an oxidant (usually air) and generate more combustion products, which can then propagate the fire and release heat, and (c) transfer of the heat generated from the combustion process back to the condensed phase to continue the thermal decomposition process (Hirschler, 1992; Beyler and Hirschler, 2002). In general, flame retardants decrease the likelihood of a fire occurring and/or decrease the undesirable consequences of a fire (Lyons, 1970; Cullis and Hirschler, 1981). The simplest way, in theory, of preventing polymer combustion is to design the polymer so that it is thermally very stable. Thermally stable polymers are less likely to thermally degrade, which prevents combustion from initiating. However, thermally stable polymers are not typically used due to cost and/or other performance issues such as mechanical and electrical properties incompatible with end-use needs for the finished part/item. -
Fire Retardant (Fr) Systems and Techniques
FIRE RETARDANT: c o n t i n u e d 2 FIRE RETARDANT: c o n t i n u e d 3 FIRE RETARDANT: c o n t i n u e d 4 FIRE RETARDANT: c o n t i n u e d 5 A strong push is toward low smoke compounding. Minimum smoke emission requires that no Adding 5-10 phr Zinc Borate helps either system. One half as much antimony can be used if Zinc weight, solid Akrochlor R-70 resin can be used at 25-30 phr in EPDM. Make sure R-70 is melted It also provides filler that helps prevent “drips” and sticky rubber forming if the compound burns or fire retardant (fr) systems and halogens or antimony oxide be used. Ideally, other burnable materials like black and petroleum Borate is present. Use of a bromine halogen donor in place of the chlorine donor allows less FR during mixing (220°F minimum). Mill-mixing R-70 sometimes results in molding flaws and melts. Drips are typically more of a plastic concern than rubber. oils are minimized. Besides providing less burnable material, non-black fillers tend to reduce smoke material to be used. The Br radical reacts 2300 times faster and is more efficient than Cl but the poorer flame resistance. In general, good dispersion of the flame retarders is essential. Imagine Smoke and Flame Resistance: techniques generation vs. carbon black. Use of halogens creates an acidic smoke that in a closed space (train Cl is usually less expensive overall. Br is used mostly in plastics where they take advantage of the two identical compounds, one with finely dispersed ingredients; the other with poor dispersion: car, mines, underground subway, and tunnels) can be deadly. -
Effect of Zinc Borate on Flammability of PET Woven Fabrics
Hindawi Advances in Polymer Technology Volume 2019, Article ID 7150736, 13 pages https://doi.org/10.1155/2019/7150736 Research Article Effect of Zinc Borate on Flammability of PET Woven Fabrics Mustafa E. Üreyen 1,2 and Elif Kaynak 3 1 Department of Fashion and Textile Design, Eskis¸ehir Technical University, Eskis¸ehir 26470, Turkey 2Civil Aviation Research Centre, Anadolu University, Eskis¸ehir 26555, Turkey 3Chemical Engineering Department, Eskis¸ehir Technical University, Eskis¸ehir 26555, Turkey Correspondence should be addressed to Mustafa E. Ureyen;¨ [email protected] Received 28 October 2018; Revised 6 February 2019; Accepted 11 February 2019; Published 7 March 2019 Academic Editor: Camino Giovanni Copyright © 2019 Mustafa E. Ureyen¨ and Elif Kaynak. Tis is an open access article distributed under the Creative Commons Attribution License, which permits unrestricted use, distribution, and reproduction in any medium, provided the original work is properly cited. Zinc borate (ZnB) has been used as a fame retardant, a smoke suppressant, and an antitracking agent in several applications. It may show synergistic efects with antimony oxide and metal hydroxides in fre retardant systems. In this work, the efect of ZnB on the fame retardancy of PET (poly(ethylene terephthalate)) woven fabrics was investigated. In order to provide the homogenous application of ZnB to the fabrics, the particle size of ZnB powders was reduced from 9 �m to submicron scale by wet-milling with zirconia balls followed by high shear fuid processing. ZnB dispersion was mixed with low-formaldehyde melamine resin based cross-linking agent and it was applied to PET fabrics by pad dry cure method. -
The Development of Synergistic Heat Stabilizers for PVC from Zinc Borate – Zinc Phosphate
A-PDF MERGER DEMO The Development of Synergistic Heat Stabilizers for PVC from Zinc Borate – Zinc Phosphate By C.Aykut ERDODU A Dissertation Submitted to the Graduate School in Partial Fulfillment of the Requirement for the Degree of MASTER OF SCIENCE Department: Chemical Engineering Major: Chemical Engineering zmir Institute of Technology zmir, Turkey August, 2004 We approve the thesis of C.Aykut ERDODU Date of Signature ………………………………………….. 30.08.2004 Prof. Dr. Devrim BALKÖSE Supervisor Department of Chemical Engineering ………………………………………….. 30.08.2004 Prof. Dr. Semra ÜLKÜ Co-Supervisor Department of Chemical Engineering ………………………………………….. 30.08.2004 Prof.Dr. Tamerkan ÖZGEN Department of Chemistry ………………………………………….. 30.08.2004 Assist.Prof.Dr.Funda TIHMINLIOLU Department of Chemical Engineering ………………………………………….. 30.08.2004 Assist.Prof. Dr. Fikret NAL Department of Chemical Engineering ………………………………………….. 30.08.2004 Prof. Dr. Devrim BALKÖSE Head of Chemical Engineering Department ACKNOWLEDGEMENT The financial support of this project by 2003-IYTE-39 is gratefully acknowledged. I would like to express my sincere gratitude to my advisors Prof. Devrim BALKÖSE and Prof. Semra ÜLKÜ for their support, guidance and encouragement during this study and the preparation of the thesis. I am very grateful to Sevdiye ATAKUL, Mehmet GÖNEN, Öniz BRSOY and Yarkın ÖZGARP for their help, encouragement and friendship throughout this project. I want to express my thanks to Gökhan ERDOAN for his help for SEM and EDX analyses, Burcu ALP for TGA analyses and Özlem Çalar DUVARCI and Filiz ÖZMIHÇI for FTIR analysis. I also present my deepest thanks to my officemate, Emre ELTEPE and my managers in Pigment Sanayi A.. Kadri ELTEPE and A.Kemal YALNIZ and all other friends for their friendship, encouragement and understandings during this study. -
Report on the Use of Flame Retardants in Plastic Shipping Pallets Maine Department of Environmental Protection
Maine State Library Digital Maine Department of Environmental Protection Documents Environmental Protection 3-23-2011 Report on the Use of Flame Retardants in Plastic Shipping Pallets Maine Department of Environmental Protection Follow this and additional works at: https://digitalmaine.com/dep_docs Recommended Citation Maine Department of Environmental Protection, "Report on the Use of Flame Retardants in Plastic Shipping Pallets " (2011). Environmental Protection Documents. 66. https://digitalmaine.com/dep_docs/66 This Text is brought to you for free and open access by the Department of Environmental Protection at Digital Maine. It has been accepted for inclusion in Environmental Protection Documents by an authorized administrator of Digital Maine. For more information, please contact [email protected]. STATE OF MAINE DEPARTMENT OF ENVIRONMENTAL PROTECTION PAUL R. LEPAGE DARRYL N. BRO\VN GOVERNOR COMMISSIONER March 23, 2011 Senator Thomas B. Saviello, Chair Representative James M. Hamper, Chair Committee on Environment and Natural Resources I 25th Maine State Legislature 100 State House Station Augusta Maine 04333-0100 Dear Senator Saviello, Representative Hamper and Members of the Committee: Enclosed please find a report on the use of flame retardants in plastic shipping pallets. The report was commissioned by the Department of Environmental Protection pursuant to An Act to Ciarify Maine's Phaseout ofPolybrominated Diphenyl Ethers (herein "the Act").1 Section 9 of the Act authorizes the D EP to supervise a study assessing the availability of safer alternatives to the use of decabrominated diphenyl ether ( decaBDE) in shipping pallets. The Act further authorized pallet manufacturers to voluntarily fund the study, which the pallet rental company iGPS agreed to do. -
Development of Synergistic Heat Stabilizers for Pvc from Zinc Borate-Zinc Phosphate
View metadata, citation and similar papers at core.ac.uk brought to you by CORE provided by DSpace@IZTECH Institutional Repository Chemical Engineering Communications ISSN: 0098-6445 (Print) 1563-5201 (Online) Journal homepage: http://www.tandfonline.com/loi/gcec20 DEVELOPMENT OF SYNERGISTIC HEAT STABILIZERS FOR PVC FROM ZINC BORATE-ZINC PHOSPHATE Cem Aykut Erdoğdu , Sevdiye Atakul , Devrim Balköse & Semra Ülkü To cite this article: Cem Aykut Erdoğdu , Sevdiye Atakul , Devrim Balköse & Semra Ülkü (2008) DEVELOPMENT OF SYNERGISTIC HEAT STABILIZERS FOR PVC FROM ZINC BORATE- ZINC PHOSPHATE, Chemical Engineering Communications, 196:1-2, 148-160, DOI: 10.1080/00986440802293148 To link to this article: http://dx.doi.org/10.1080/00986440802293148 Published online: 20 Oct 2008. Submit your article to this journal Article views: 537 View related articles Citing articles: 4 View citing articles Full Terms & Conditions of access and use can be found at http://www.tandfonline.com/action/journalInformation?journalCode=gcec20 Download by: [Izmir Yuksek Teknologi Enstitusu] Date: 20 November 2016, At: 23:05 Chem. Eng. Comm., 196:148–160, 2009 Copyright # Taylor & Francis Group, LLC ISSN: 0098-6445 print/1563-5201 online DOI: 10.1080/00986440802293148 Development of Synergistic Heat Stabilizers for PVC from Zinc Borate-Zinc Phosphate CEM AYKUT ERDOG˘ DU,1 SEVDIYE ATAKUL,2 DEVRIM BALKO¨ SE,2 AND SEMRA U¨ LKU¨ 2 1Pigment Sanayi A. S¸., I˙zmir, Turkey 2Department of Chemical Engineering, I˙zmir Institute of Technology, I˙zmir, Turkey The importance of flame-retardant and smoke-suppressed poly(vinyl chloride) (PVC) compositions is increasing gradually in the polymer industry since PVC releases smoke and toxic gases (hydrogen chloride, HCl) during heating at tempera- tures above 140C with the result of dehydrochlorination reaction. -
Synergies of Metal Molybdates and Metal Hydroxides in Fire Retardant Polyolefin Compounds
1 Synergies of Metal Molybdates and Metal Hydroxides in Fire Retardant Polyolefin Compounds Alex Isarov, David Temples, Mark Herndon, Tong Chen J.M. Huber Corporation Fairmount, GA 30139 USA 23rd Annual BCC Conference: Recent Advances on Flame Retardancy of Polymeric Materials FIRE RETARDANT ADDITIVES May 21-23, 2012 2 Background Information J.M. Huber Corporation acquired the Kemgard® product line from The Sherwin Williams Company in August 2010. Kemgard materials are smoke suppressants and char formers based on molybdenum and phosphorous chemistries. Currently, the main application for Kemgard products is in PVC formulations (rigid, flexible, plastisols). Huber is investigating Kemgard performance benefits in other polymer systems including polyolefin-based formulations. Objective – review available data related to FR performance of metal molybdates as fire retardants/char formers in polyolefin based formulations. 23rd Annual BCC Conference: Recent Advances on Flame Retardancy of Polymeric Materials FIRE RETARDANT ADDITIVES May 21-23, 2012 3 Presentation Outline Review of Kemgard technology – precipitation of active phase on the surface of particulate core. Example – zinc molybdate/zinc borate complex. Molybdates as char formers in thermoplastic EVA. Molybdates as char formers in EVA/LDPE blends (thermoplastic and peroxide cross linked). Zinc phosphate/zinc oxide complex as char former in peroxide cross linked EVA/LDPE blends. Conclusions. 23rd Annual BCC Conference: Recent Advances on Flame Retardancy of Polymeric Materials FIRE RETARDANT ADDITIVES May 21-23, 2012 4 Kemgard® Engineered Molybdates Precipitation of molybdates (Ca, Zn) onto the surface of a ppgyarticulate core significantly increases the active surface area of the molybdate phase resulting in enhanced FR efficacy. Inert core: Calcium Carbonate core – Kemgard 911A Talc core – Kemgard 911C, Kemgard 1100 Zinc Oxide core – Kemgard 911B FR-active core Magnesium Hydroxide core – Kemgard MZM, Kemgard HPSS.