Research Status and Progress of Welding Technologies for Molybdenum and Molybdenum Alloys
Total Page:16
File Type:pdf, Size:1020Kb
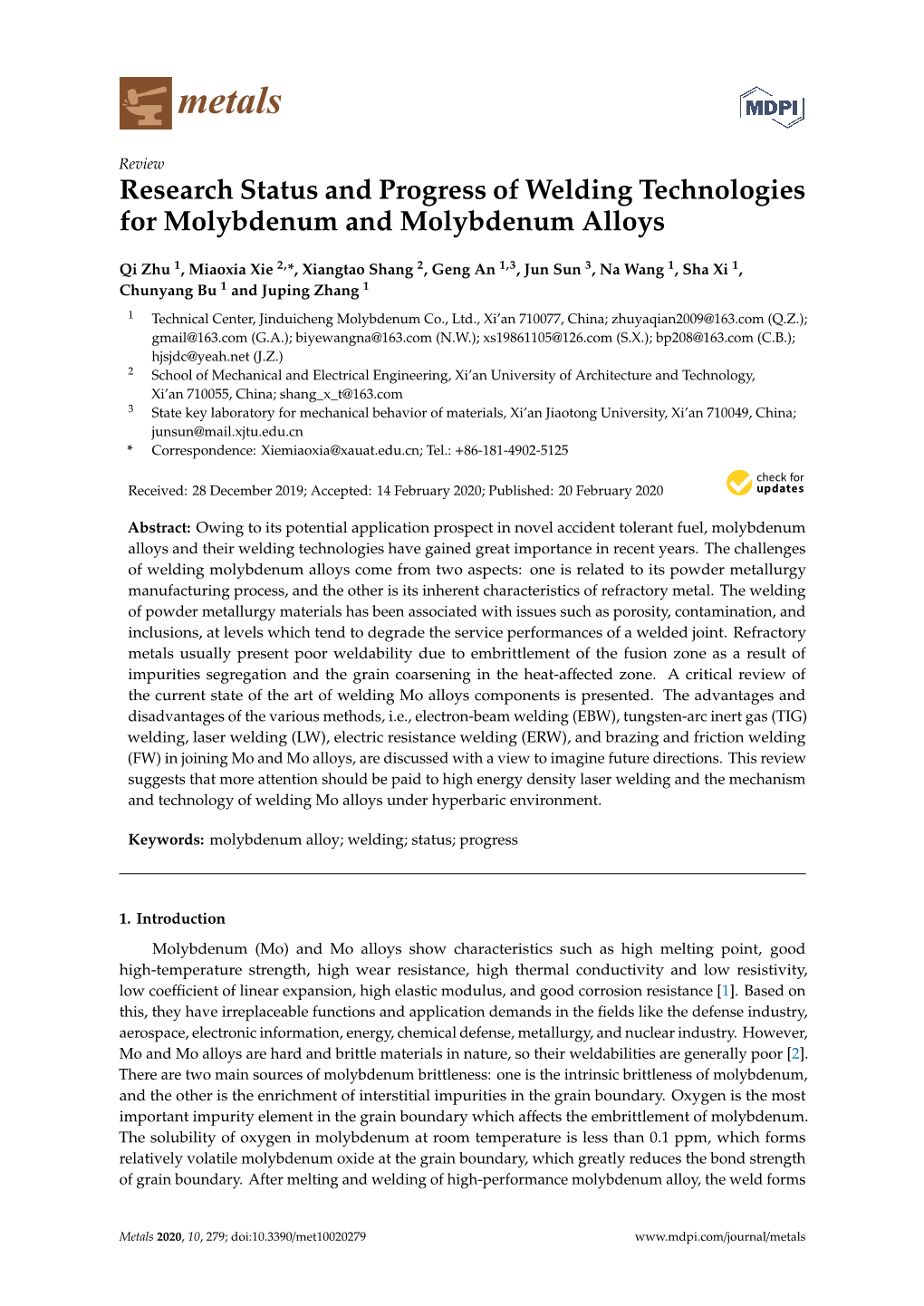
Load more
Recommended publications
-
The Mineral Industry of China in 2016
2016 Minerals Yearbook CHINA [ADVANCE RELEASE] U.S. Department of the Interior December 2018 U.S. Geological Survey The Mineral Industry of China By Sean Xun In China, unprecedented economic growth since the late of the country’s total nonagricultural employment. In 2016, 20th century had resulted in large increases in the country’s the total investment in fixed assets (excluding that by rural production of and demand for mineral commodities. These households; see reference at the end of the paragraph for a changes were dominating factors in the development of the detailed definition) was $8.78 trillion, of which $2.72 trillion global mineral industry during the past two decades. In more was invested in the manufacturing sector and $149 billion was recent years, owing to the country’s economic slowdown invested in the mining sector (National Bureau of Statistics of and to stricter environmental regulations in place by the China, 2017b, sec. 3–1, 3–3, 3–6, 4–5, 10–6). Government since late 2012, the mineral industry in China had In 2016, the foreign direct investment (FDI) actually used faced some challenges, such as underutilization of production in China was $126 billion, which was the same as in 2015. capacity, slow demand growth, and low profitability. To In 2016, about 0.08% of the FDI was directed to the mining address these challenges, the Government had implemented sector compared with 0.2% in 2015, and 27% was directed to policies of capacity control (to restrict the addition of new the manufacturing sector compared with 31% in 2015. -
UNITED STATES SECURITIES and EXCHANGE COMMISSION Form SD Echostar Corporation
UNITED STATES SECURITIES AND EXCHANGE COMMISSION Washington, D.C. 20549 Form SD Specialized Disclosure Report EchoStar Corporation (Exact name of registrant as specified in its charter) Nevada 001-33807 26-1232727 (State or Other Jurisdiction of Incorporation or (Commission File Number) (I.R.S. Employer Identification No.) Organization) 100 Inverness Terrace East, Englewood, Colorado 80112-5308 (Address of Principal Executive Offices) (Zip Code) Dean A. Manson Executive Vice President, General Counsel and Secretary (303) 706-4000 (Name and telephone number, including area code, of person to contact in connection with this report) Check the appropriate box to indicate the rule pursuant to which this form is being filed, and provide the period to which the information in this form applies: x Rule 13p-1 under the Securities Exchange Act (17 CFR 240.13p-1) for the reporting period from January 1, 2014 to December 31, 2014. SECTION 1—CONFLICT MINERALS DISCLOSURE ITEM 1.01. Conflict Minerals Disclosure and Report Conflict Minerals Disclosure This Specialized Disclosure Report on Form SD (“Form SD”) of EchoStar Corporation (the “Company”) is filed pursuant to Rule 13p-1 (the “Rule”) promulgated under the Securities Exchange Act of 1934, as amended, for the reporting period of January 1, 2014 to December 31, 2014. The Rule was adopted by the Securities and Exchange Commission (“SEC”) to implement reporting and disclosure requirements related to certain specified minerals as directed by the Dodd-Frank Wall Street Reform and Consumer Protection Act of 2010. The specified minerals are gold, columbite-tantalite (coltan), cassiterite and wolframite, including their derivatives, which are limited to tantalum, tin and tungsten (the “Conflict Minerals”). -
China Molybdenum Co (3993 HK)
China Thursday , 25 January 2018 INITIATE COVERAGE BUY China Molybdenum Co (3993 HK) An Emerging Global Mining Giant; Riding On Cobalt And Copper Momentum Share Price HK$5.97 China Molybdenum Co has evolved into one of the world’s leading mining Target Price HK$6.78 companies with diversified resources exposure. We forecast 40%+ EPS CAGR in Upside +13.0% 2017-20, given: a) our positive view on copper and cobalt in the medium to long term, b) the likelihood of tungsten and molybdenum’s high-margin advantage COMPANY DESCRIPTION persisting, and c) the niobium and phosphate segments providing stable cash flows. Initiate coverage with BUY and target price of HK$6.78 on DCF life-of-mine valuation. China Molybdenum Co is a mineral mining and exploration company engaged in the Copper: Positive outlook in the medium term on solid fundamentals. From a global mining and processing of molybdenum, perspective, we favour copper among base metals for the next 2-3 years given: a) supply tungsten, copper, cobalt, niobium and constraint due to under-investment, mines’ grade declines and elevated mine strike risks; phosphate minerals. and b) demand supported by traditional consumption and rising adoption of electric vehicles (EV). We expect LME copper prices to stay high at US$7,000-7,200/tonne in STOCK DATA 2018-20. China Molybdenum Co (CMOC) owns two world-class copper mines Tenke GICS sector Materials Fungurume Mining S.A (Tenke) and Northparkes Mine (Northparkes) with a combined Bloomberg ticker: 3993 HK mined copper production of 240k-260k tpa. Shares issued (m): 3,933.5 Market cap (HK$m): 200,112.6 Cobalt: Riding on EV momentum. -
The Mineral Industry of China in 2007
2007 Minerals Yearbook CHINA U.S. Department of the Interior December 2009 U.S. Geological Survey THE MINERAL INDUS T RY OF CHINA By Pui-Kwan Tse After three decades of economic development, China probably have some impact on the global commodity prices has become one of the leading economic and trade powers (Batson and King, 2008). in the world, one of the top destinations for foreign direct investment, and an export destination of choice. During the Minerals in the National Economy past several years, the Government’s economic policy was to prevent economic slowdown and fight inflation. In 2007, China is rich in mineral resources and was the world’s China’s economic growth rate was 11.9% and represented the leading producer of aluminum, antimony, barite, bismuth, coal, fifth consecutive year of double-digit expansion. Industrial fluorspar, gold, graphite, iron and steel, lead, phosphate rock, production increased by 18.5% compared with that of 2006. rare earths, talc, tin, tungsten, and zinc in 2007. It ranked among The consumer price index (a measurement of inflation) rose to the top three countries in the world in the production of many a decade high of 4.8%. To prevent economic “overheating,” the other mineral commodities. China was the leading exporter Government raised interest rates and the People’s Bank of China of antimony, barite, coal, fluorspar, graphite, rare earths, and (the central bank) required commercial banks to increase the tungsten in the world. The country’s demand for chromium, reserve-requirement ratio 11 times to 11.5% at yearend 2007. -
United States Securities and Exchange Commission Washington, D.C
UNITED STATES SECURITIES AND EXCHANGE COMMISSION WASHINGTON, D.C. 20549 FORM SD SPECIALIZED DISCLOSURE REPORT SONUS NETWORKS, INC. (Exact Name of Registrant as Specified in its Charter) DELAWARE 001-34115 04-3387074 (State or Other Jurisdiction (Commission File Number) (IRS Employer of Incorporation) Identification No.) 4 TECHNOLOGY PARK DRIVE, WESTFORD, MASSACHUSETTS 01886 (Address of Principal Executive Offices) (Zip Code) Jeffrey M. Snider Senior Vice President, Chief Administrative Officer, General Counsel and Secretary (978) 614-8100 (Name and telephone number, including area code, of the person to contact in connection with this report) Check the appropriate box to indicate the rule pursuant to which this form is being filed, and provide the period to which the information in this form applies: x Rule 13p-1 under the Securities Exchange Act (17 CFR 240.13p-1) for the reporting period from January 1 to December 31, 2015. Section 1 — Conflict Minerals Disclosure Item 1.01. Conflict Minerals Disclosure and Report Sonus Networks, Inc. (the “Company,” “Sonus,” “we,” or “our”) has determined that some of the products that Sonus manufactures or contracts to manufacture include gold, columbite-tantalite (coltan), cassiterite and wolframite, including their derivatives, tantalum, tin and tungsten (“Conflict Minerals” or “3TG”), and that these Conflict Minerals are necessary to the functionality or production of these products. The Company conducted a Reasonable Country of Origin Inquiry (“RCOI”) to determine whether any of the Conflict Minerals in its products originated in the Democratic Republic of the Congo or an adjoining country (“Covered Country”) and whether the Conflict Minerals are from recycled or scrap sources. -
Project Proposals (In Chinese)
13 August 2015 Final Extended Report Assessment of the normative and policy framework governing the Chinese economy and its impact on international competition For: AEGIS EUROPE Cross-sector Alliance Representing European Manufacturing Brussels Belgium THINK!DESK China Research & Consulting Prof. Dr. Markus Taube & Dr. Christian Schmidkonz GbR Merzstrasse 18 81679 München Tel.: +49 - (0)89 - 26 21 27 82 [email protected] www.thinkdesk.de This report has been prepared by: Prof. Dr. Markus Taube Peter Thomas in der Heiden © THINK!DESK China Research & Consulting 2015 Seite 2 Contents Executive Summary ························································································· 12 1. Introduction ······························································································ 28 Part I: The Management of the Chinese Economy: Institutional Set-up and Policy Instruments 2. Centralised Planning and Market Forces in the Chinese Economy ··················· 33 2.1 The Role of Planning in the Chinese Economy ············································ 33 2.1.1 Types of Plans ··············································································· 33 2.1.2 Plans and Complementary Documents················································ 42 2.2 Dedicated Government Programmes for Industry Guidance ··························· 46 2.2.1 Subsidies – An Overview ································································· 46 2.2.1.1 Examples for Preferential Policies and Grant Giving Operations by Local Governments -
The Mineral Industry of China in 2011
2011 Minerals Yearbook CHINA U.S. Department of the Interior September 2013 U.S. Geological Survey THE MINERAL INDUSTRY OF CHINA By Pui-Kwan Tse China ranked second behind the United States as the world’s one child policy in the latter part of the 20th century. China’s leading economic power and was a leading mineral producing investment-to-GDP ratio was high (49.7% in 2011) compared and consuming country. In 2011, China’s economy remained with that of the Republic of Korea, 29.5%; Taiwan, 21.1%; strong even as most of the developed countries in the West were Japan, 19.9%; and the United States, 15.9%. Also, the country trying to recover from recession. During the past two decades, was likely to be confronted with social and environmental China’s economic growth was created by a combination issues that had been ignored during the past two decades of of trade and investment, which greatly affected the global development (Citigroup Global Market Inc., 2012a, p. 7; commodity market. China imported significant amounts of National Bureau of Statistics of China, 2012a, p. 1–9). raw materials and transformed the materials into products for export. The country’s demand for energy, minerals, and metals Minerals in the National Economy was particularly strong. During the 1980s and 1990s, China’s China is rich in mineral resources and was the world’s leading commodity exports went primarily to the United States and producer of aluminum, antimony, barite, bismuth, cement, Europe; however, during the past several years, intraregional trade coal, fluorspar, gold, graphite, iron and steel, lead, magnesium, in Asia increased significantly, which benefited other emerging mercury, molybdenum, phosphate rock, rare earths, salt, talc, economies in Asia, especially those that exported raw materials to tin, tungsten, and zinc in 2011. -
One Belt One Road – a Monumental Opportunity for Stainless Steel (Simultaneous Translation Provided)
One Belt One Road – A monumental Opportunity for Stainless Steel (Simultaneous translation provided) DAY ONE Wednesday, 27 June 08:00 Registration desk opens MODULE 1 Stainless Steel Market Trends - Impact of One Road One Belt (OROB) for Stainless Steel by Product Form - Global Trends and Outlook - Consolidation in Asia - 4-in-1 – risk or opportunity for Asian mills? - Overcapacity: Closures versus new capacities? - Profitability 2018 vs 2017 Chairman’s opening remarks 08:50 Markus Moll, Managing Director, SMR – Steel and Metals Market Research, Austria 09:00 Stainless Steel in 2018 – what is hot, what is not? Markus Moll, Managing Director, SMR – Steel and Metals Market Research, Austria Chinese stainless steel market and industry: current status and future outlook 09:20 Li Xinchuang, President, China Metallurgical Industry Planning and Research Institute, and Vice Chairman, China Iron and Steel Association, China 09:40 Jointly promoting quality development of stainless steel industrial chain Gao Jianbing, General Manager, Shanxi Taigang Stainless Steel Co Ltd, China Thinking on the development of stainless steel cold rolling in China 10:00 Huang Qingzhou, General Manager, Beihai Chengde Stainless Steel Group, China Panel Discussion Moderator Markus Moll, Managing Director, SMR – Steel and Metals Market Research, Austria 10:15 Panelists - Li Xinchuang, President, China Metallurgical Industry Planning and Research Institute, and Vice Chairman, China Iron and Steel Association, China - Gao Jianbing, General Manager, Shanxi Taigang Stainless -
C-Shares CSI 300 Index ETF Semi-Annual Report 2016
Semi-Annual Report (Unaudited) CHINA UNIVERSAL INTERNATIONAL ETF SERIES – C-SHARES CSI 300 INDEX ETF (A Sub-Fund of China Universal International ETF Series, an umbrella unit trust established under the laws of Hong Kong) For the period from 1 January 2016 to 30 June 2016 CHINA UNIVERSAL INTERNATIONAL ETF SERIES – C-SHARES CSI 300 INDEX ETF (A Sub-Fund of China Universal International ETF Series) CONTENTS Pages MANAGEMENT AND ADMINISTRATION 1 STATEMENT OF FINANCIAL POSITION 2 STATEMENT OF COMPREHENSIVE INCOME 3 STATEMENT OF CHANGES IN NET ASSETS ATTRIBUTABLE TO UNITHOLDERS 4 INVESTMENT PORTFOLIO (Unaudited) 5 - 12 MOVEMENTS IN INVESTMENT PORTFOLIO (Unaudited) 13 - 23 PERFORMANCE RECORD (Unaudited) 24 CHINA UNIVERSAL INTERNATIONAL ETF SERIES –C-SHARES CSI 300 INDEX ETF (A Sub-Fund of China Universal International ETF Series) MANAGEMENT AND ADMINISTRATION MANAGER AND RQFII HOLDER SERVICE AGENT OR CONVERSION AGENT China Universal Asset Management (Hong Kong) Company HK Conversion Agency Services Limited Limited 1/F One & Two Exchange Square 3710-11, Two International Finance Centre 8 Connaught Place 8 Finance Street Central, Hong Kong Central Hong Kong AUDITORS Ernst & Young DIRECTORS OF THE MANAGER 22/F, CITIC Tower LI Wen 1 Tim Mei Avenue WAN Qing Central ZHANG Hui Hong Kong ADVISER TRUSTEE China Universal Asset Management Company Limited BOCI-Prudential Trustee Limited 22/F, Aurora Plaza 12/F & 25/F, Citicorp Centre No. 99 Fucheng Road 18 Whitfield Road Pudong District Causeway Bay Shanghai 200120 Hong Kong China CUSTODIAN RQFII CUSTODIAN -
View Annual Report
Annual 2010 Report Contents 2 Corporate Profile 6 Corporate Information 9 Financial Summary 15 Directors, Supervisors, Senior Management and Staff 30 Particulars and Changes of Shareholding Structure, and Details of Substantial Shareholders 39 Chairman’s Statement 48 Management’s Discussion and Analysis of Financial Conditions and Results of Operations 58 Directors’ Report 67 Report of the Supervisory Committee 72 Report on Corporate Governance and Internal Control 94 Significant Events 99 Connected Transactions 119 Independent Auditor’s Report 121 Statements of Financial Position 125 Consolidated Statement of Comprehensive Income 127 Consolidated Statement of Changes in Shareholders’ Equity 129 Consolidated Cash Flow Statement 131 Notes to the Consolidated Financial Statements Corporate Profile Aluminum Corporation of China Limited (“Chalco” or the “Company”) is a joint stock limited company established in the People’s Republic of China (the “PRC”); its shares are listed on the New York Stock Exchange, The Stock Exchange of Hong Kong Limited (the “Hong Kong Stock Exchange”) and the Shanghai Stock Exchange respectively. The Company and its subsidiaries (collectively referred to as the “Group”) are principally engaged in mining of bauxite; the production and sales of alumina, primary aluminum and aluminum fabrication products; and trading of other non-ferrous metal products. The Group is the largest producer of alumina, primary aluminum and aluminum fabrication products in the PRC, and also the second largest producer of alumina as well as the third largest producer of primary aluminum in the world. The competitiveness of the Group is mainly reflected in: • its leading strategic position in the alumina, primary aluminum and aluminum fabrication markets in the PRC; • its ownership of adequate and stable supply of bauxite resources as well as refining technology; and • its comprehensive industry chain with better resistance to market risks. -
MSP-REFRAM-D2.2-State-Of-The-Art
MSP-REFRAM Coordination and Support Action (CSA) This project has received funding from the European Union's Horizon 2020 research and innovation programme under grant agreement No 688993. Start date : 2015-12-01 Duration : 19 Months State of the art on the recovery of refractory metals from primary resources Authors : Pr. Jason YANG (GTK) David Arcos (AMPHOS21), Florent Bourgeois (LGC), Kathy Bru (BRGM), Antti Häkkinen (LUT), Eugen Andreiadis and Daniel Meyer (CEA), Quentin Bellier (ERAMET), Hans-Jörg Bart (UNIKL), Sami Virolainen (LUT), Jean-Marie Lambert (ERAMET), Katarzyna Leszczynska-Sejda and Witold Kurylak (IMN), Lena Sundqvist and Guozhu Ye (MEFOS), Yiongxiang Yang (TUDELFT) MSP-REFRAM - D2.2 - Issued on 2016-05-06 13:29:02 by GTK MSP-REFRAM - D2.2 - Issued on 2016-05-06 13:29:02 by GTK MSP-REFRAM - Contract Number: 688993 Multi-Stakeholder Platform for a Secure Supply of Refractory Metals in Europe Document title State of the art on the recovery of refractory metals from primary resources Pr. Jason YANG David Arcos (AMPHOS21), Florent Bourgeois (LGC), Kathy Bru (BRGM), Antti Häkkinen (LUT), Eugen Andreiadis and Daniel Meyer (CEA), Quentin Bellier (ERAMET), Author(s) Hans-Jörg Bart (UNIKL), Sami Virolainen (LUT), Jean-Marie Lambert (ERAMET), Katarzyna Leszczynska-Sejda and Witold Kurylak (IMN), Lena Sundqvist and Guozhu Ye (MEFOS), Yiongxiang Yang (TUDELFT) Number of pages 112 Document type Deliverable Work Package WP2 Document number D2.2 Issued by GTK Date of completion 2016-05-06 13:29:02 Dissemination level Public Summary State of the art on the recovery of refractory metals from primary resources The mining and mines of refractory metals, tungsten, tantalum, molybdenum, niobium and rhenium in Europe and the world are described and the existing technologies of mining, mineral processing and extractive metallurgy (hydrometallurgy and pyrometallurgy) are reviewed on recovery of refractory metals from primary resources. -
Measuring the Market Impact of the Shanghai-Hong Kong Stock Connect Program
Measuring the Market Impact of the Shanghai-Hong Kong Stock Connect Program: An Event Study Analysis By Sonya Nicole Rice A Research project Submitted to Saint Mary’s University, Halifax, Nova Scotia in Partial Fulfillment of the Requirements for the Degree of Master of Finance. September, 2015, Halifax, Nova Scotia © Sonya Nicole Rice, 2015 Approved: Dr. J. Colin Dodds MFin Director Approved: Dr. J. Colin Dodds Supervisor Date: 14th September 2015 Acknowledgements First of all, I would like to extend my gratitude to my supervisor, Dr. Dodds, for his timely advice and guidance throughout the research process. I would also like to thank Dr. Boabang for his direction during the preliminary stages. I thank the Master of Finance faculty for all of the financial knowledge they have shared during this intensive program. I also thank my Chinese professor, Dr. Beaupré, for sharing his cultural knowledge and personal experiences in China with me throughout my undergraduate Chinese Studies. I want to thank Manbir Kaur for teaching me how to use Python to retrieve data efficiently and Ni Bintuo for always being there to discuss China and statistical issues. Lastly, I want to thank my friends and family for their support and understanding throughout this demanding time. ii Abstract Measuring the Market Impact of the Shanghai-Hong Kong Stock Connect Program: An Event Study Analysis by Sonya Nicole Rice Financial liberalization in the PRC has been a gradual process. The most recent liberalization effort was the Shanghai-Hong Kong Stock Connect program which represents the first program allowing direct access between the Shanghai Stock Exchange and the Stock Exchange of Hong Kong.