Powering LED Lighting for Horticulture Lowering Costs and Improving Results with the Right Power Supply for Your Horticultural Lighting
Total Page:16
File Type:pdf, Size:1020Kb
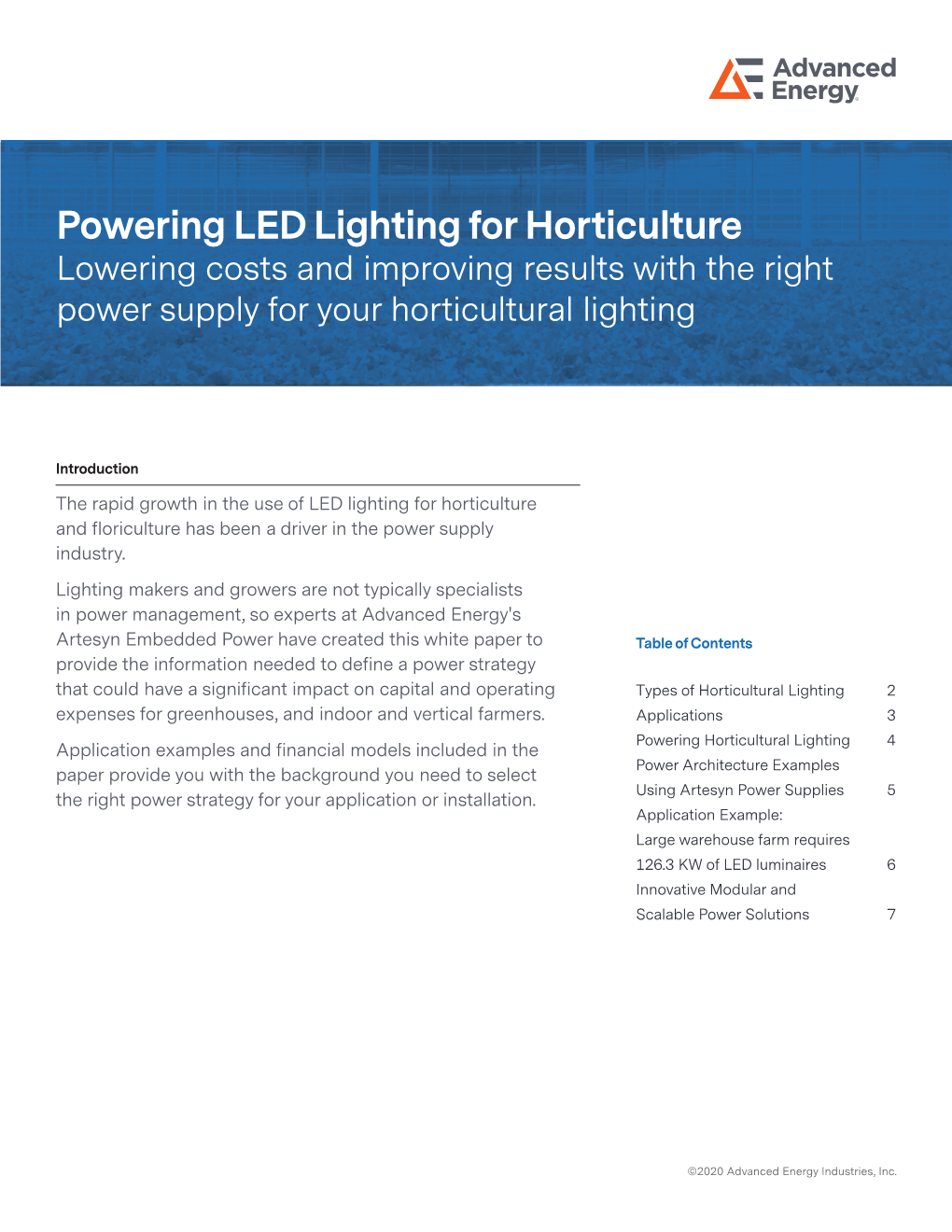
Load more
Recommended publications
-
Linda Sierra
Jason D. Licamele, Ph.D. P.O. Box 25035 / Scottsdale, AZ 85255 [email protected] Agriculture & Biological Systems Engineer Keywords: biotechnology, agriculture, aquaculture, fisheries, plant production, natural products, bioenergy, bioprocessing, ecosystems, food science, greenhouse engineering, horticulture, hydroponics, fisheries, algae, environment, natural resources, water resources, bioprospecting, sustainability - Biological systems engineer, marine biologist, ecologist, environmental scientist, and biotechnologist with commercial operations and research experience leading, designing, developing, executing, and managing projects. - Innovative applied scientist and engineer with a multitude of skills, a patent portfolio, over 20 years of commercial experience in the aquaculture, agriculture, food, and bioenergy industries with a focus on environmental sustainability and resource management. - Experienced entrepreneur and consultant effectively developing global relationships with business, legal, non- governmental organizations, academic, and government organizations via strong communication, interpersonal skills, leadership qualities, and dedication to mission. - Skilled in project design, project management, experimental design, data management, and data translation with a unique ability to critically analyze and effectively communicate information to all levels of audiences. - Professional scientist and engineer with experience in business, production, research and development, intellectual property development, technology -
Trends in Aquaponics
Trends in Aquaponics Chris Hartleb University of Wisconsin-Stevens Point Northern Aquaculture Demonstration Facility Aquaponics Innovation Center Aquaponics • Integrated & soilless • Continuous year-round • Free of biocides production • Conservative use of water, space & • Meets socio-economic challenges labor – Urban, peri-urban, rural • Produces both vegetable & protein crop – Locavore movement Aquaponic Systems UVI Design Fish tanks Raft tank Water pump Clarifier (solids filter) Degassing tank Mineralization tanks & biofilter Air pump Plant Production Systems • Raft (Revised agriculture float technology) – Deep water culture • Large volume water • Root aeration • Nutrient uptake: High • Media based – Biofiltration in media – Clogging & cleaning present – Nutrient uptake: High • Nutrient film technique – Low volume water – Less system stability – Nutrient uptake: Low Modified Designs • Vertical farming – Living walls – Vertical • Robotics • Complete artificial light Who’s Growing using Aquaponics? Love, Fry, Li, Hill, Genello, Simmons & Thompson. 2015. Commercial aquaponics production and profitability: Findings from an international survey. Aquaculture 435:67-74. How Many is That? • Limited survey response • Most likely underestimated number and location Types of Aquaponics • Scalable: – Hobby and Home food production – Farmers market food production – Social & Community systems – Commercial food production – Education – Research Aquaculture North America January/February 2018 • Trends driving the seafood sector – Climate change impact -
Review Article Suitable Substrate for Optimal Crop Growth Under
Journal of Scientific Agriculture 2018,2: 62-65 doi: 10.25081/jsa.2018.v2.860 http://updatepublishing.com/journals/index.php/jsa ISSN: 2184-0261 R E VIEW A RTICLE SUITABLE SUBSTRATE FOR OPTIMAL CROP GROWTH UNDER PROTECTED FARMS–AN ASSESSMENT AMARESH SARKAR*, MRINMOY MAJUMDER Department of Civil Engineering, National Institute of Technology, Agartala, PIN-799046, Tripura, India ABSTRACT An attempt has been made in this paper, to review crop growing substrates for protected farms. Optimal substrate type and volume for different crops cultivar is different. Substrate selection is a critical factor for optimal production of high-quality vegetables. Crop root orientation and depth determine the type and volume of substrate required which is very important for optimal crop growth and maximum profit. Growing crops on substrates in protected skyscrapers would not only mitigate the need for more land, it produces growing space vertically. Keywords: Substrate, Nutrient solution, Controlled environment agriculture INTRODUCTION structure can also be constructed on non-cultivable soil and urban roof-tops [21]. The amount of solar radiation, Food need is increasing globally as the inhabitants are which provides the energy to evaporate moisture from the increasing. Protected farming is a popular technique for substrate and the plant, is the major factor. Other growing vegetables all seasons regardless of location and important factors include air temperature, wind speed, and climate. The most innovative technology for plants humidity level [11]. The plant canopy size and shape growing in greenhouses is growing plants in mineral influences light absorption, reflection, and the rate at substrates such as rock wool, vermiculite, perlite, zeolite, which water evaporates from the soil. -
LED Lighting Systems for Horticulture: Business Growth and Global Distribution
sustainability Review LED Lighting Systems for Horticulture: Business Growth and Global Distribution Ivan Paucek 1, Elisa Appolloni 1, Giuseppina Pennisi 1,* , Stefania Quaini 2, Giorgio Gianquinto 1 and Francesco Orsini 1 1 DISTAL—Department of Agricultural and Food Sciences and Technologies, Alma Mater Studiorum—University of Bologna, 40127 Bologna, Italy; [email protected] (I.P.); [email protected] (E.A.); [email protected] (G.G.); [email protected] (F.O.) 2 FEEM—Foundation Eni Enrico Mattei, 20123 Milano, Italy; [email protected] * Correspondence: [email protected] Received: 4 August 2020; Accepted: 5 September 2020; Published: 11 September 2020 Abstract: In recent years, research on light emitting diodes (LEDs) has highlighted their great potential as a lighting system for plant growth, development and metabolism control. The suitability of LED devices for plant cultivation has turned the technology into a main component in controlled or closed plant-growing environments, experiencing an extremely fast development of horticulture LED metrics. In this context, the present study aims to provide an insight into the current global horticulture LED industry and the present features and potentialities for LEDs’ applications. An updated review of this industry has been integrated through a database compilation of 301 manufacturers and 1473 LED lighting systems for plant growth. The research identifies Europe (40%) and North America (29%) as the main regions for production. Additionally, the current LED luminaires’ lifespans show 10 and 30% losses of light output after 45,000 and 60,000 working hours on average, respectively, while the 1 vast majority of worldwide LED lighting systems present efficacy values ranging from 2 to 3 µmol J− (70%). -
Vertical Farming Sustainability and Urban Implications
Master thesis in Sustainable Development 2018/32 Examensarbete i Hållbar utveckling Vertical Farming Sustainability and Urban Implications Daniela Garcia-Caro Briceño DEPARTMENT OF EARTH SCIENCES INSTITUTIONEN FÖR GEOVETENSKAPER Master thesis in Sustainable Development 2018/32 Examensarbete i Hållbar utveckling Vertical Farming Sustainability and Urban Implications Daniela Garcia-Caro Briceño Supervisor: Cecilia Mark-Herbert Evaluator: Daniel Bergquist Copyright © Daniela Garcia-Caro Briceño, Published at Department of Earth Sciences, Uppsala University (www.geo.uu.se), Uppsala, 2018 Content 1. INTRODUCTION .............................................................................................................................. 1 1.1 PROBLEM FORMULATION ............................................................................................................... 1 1.2 AIM ................................................................................................................................................. 2 1.3 OUTLINE ......................................................................................................................................... 3 2. METHODS ......................................................................................................................................... 4 2.1 RESEARCH APPROACH AND DESIGN ............................................................................................... 4 2.2 RESEARCH DELIMITATIONS ........................................................................................................... -
Aquaponic Growers
TOP TEN MISTAKES MADE BY aquaponic growers BRIGHT Copyright © 2015 TABLE OF CONTENTS IS THIS E-BOOK RIGHT FOR ME? ....................................3 ABOUT THE AUTHOR ......................................................4 ABOUT BRIGHT AGROTECH ..........................................5 THE TOP 10 MISTAKES: 1) UNUSABLE OR HARD-TO-USE FARMS ..........................................6 2) INADEQUATE CIRCULATION/SOLIDS REMOVAL/OR BSA .........7 3) POOR QUALITY WATER ................................................................9 4) UNDERESTIMATING PRODUCTION AND SYSTEM COSTS .........10 5) BIOLOGICAL VIABILITY VS. ECONOMIC VIABILITY....................11 6) CHOOSING THE WRONG CROPS..............................................12 7) SYSTEMS THAT HAVE POOR TRACK RECORDS..........................14 8) LACK OF PEST CONTROL STRATEGY..........................................16 9) GROWERS GET GREEDY .............................................................18 10) FAILURE TO APPROACH MARKETS CREATIVELY......................19 CONCLUSION.................................................................21 2 Back to Top IS THIS EBOOK RIGHT FOR ME? The learning curve of aquaponics is littered with the remains of failed aquaponic ventures and millions of dollars in lost investments. This e-book acts as a guide for beginning aquaponic growers who are interested in operating successful aquaponic systems- whether commercial or hobby systems. This guide will detail 10 of the obstacles which I have encountered again and again on this learning curve -
The Vertical Farm: a Review of Developments and Implications for the Vertical City
buildings Review The Vertical Farm: A Review of Developments and Implications for the Vertical City Kheir Al-Kodmany Department of Urban Planning and Policy, College of Urban Planning and Public Affairs, University of Illinois at Chicago, Chicago, IL 60607, USA; [email protected] Received: 10 January 2018; Accepted: 1 February 2018; Published: 5 February 2018 Abstract: This paper discusses the emerging need for vertical farms by examining issues related to food security, urban population growth, farmland shortages, “food miles”, and associated greenhouse gas (GHG) emissions. Urban planners and agricultural leaders have argued that cities will need to produce food internally to respond to demand by increasing population and to avoid paralyzing congestion, harmful pollution, and unaffordable food prices. The paper examines urban agriculture as a solution to these problems by merging food production and consumption in one place, with the vertical farm being suitable for urban areas where available land is limited and expensive. Luckily, recent advances in greenhouse technologies such as hydroponics, aeroponics, and aquaponics have provided a promising future to the vertical farm concept. These high-tech systems represent a paradigm shift in farming and food production and offer suitable and efficient methods for city farming by minimizing maintenance and maximizing yield. Upon reviewing these technologies and examining project prototypes, we find that these efforts may plant the seeds for the realization of the vertical farm. The paper, however, closes by speculating about the consequences, advantages, and disadvantages of the vertical farm’s implementation. Economic feasibility, codes, regulations, and a lack of expertise remain major obstacles in the path to implementing the vertical farm. -
Hydroponic Vertical Farming — Helping Feed Our Growing Population
Chapter 3: Hydroponic Vertical Farming — Helping Feed Our Growing Population Hydroponic Vertical Farming: Helping Feed Our Growing Population Brief Description: • Barbed valves By 2050, it's estimated that 80 percent of the world's 9.2 billion • Plastic lex net cups population will live in urban areas. In this lesson students will • Seeds or seedlings gain an understanding of what a seed needs in order to grow • Hydroponic fertilizer into a healthy plant, and what a vertical farm is by comparing • Optional: grow lights, pH test kit, thermometer and contrasting this method of food production with conven- tional farming methods. Students will design their own rubric; Background: research best practices; create blueprints; and modify and build he impact that humans have had on Earth include deforesta- a working model of an indoor vertical hydroponic farm through tion, urbanization, desertiication, erosion, poor air and water collaborative eforts using recycled materials. his closed system quality, and changing the low of water. hrough innovative 3: Chapter should last six or more months, which allows students time for techniques such as hydroponic vertical gardening, we can miti- relection, entertainment and a healthy snack. gate some of the efects of urban sprawl. Objective: Hydroponics is a method of growing edible crops in soilless, Lessons Garden Up Your STEMming Students will: nutrient-rich water. Advantages of hydroponic gardening 1. Understand what a seed needs to grow into a healthy include: reduction in runof; less water usage; crops can be plant. grown indoors year-round; plants require less space, and can 2. Know what a vertical farm is and compare and contrast have higher yields. -
Vertical Farming
Module 1 HISTORY AND TRENDS • Unit 1 PAST, PRESENT AND FUTURE VERTICAL FARMING 1 Choose the correct words for the following text. Vertical farming is a revolutionary and more (1) ................................................. method of agriculture, particularly if you need to produce food in environments (2) ................................................. arable land is unavailable or rare. In short, it is the practice of producing food in vertically stacked layers, commonly integrated into other structures like a skyscraper, shipping container or repurposed warehouse. (3) ................................................. main goals are: • to produce more foods per square meter • to perfectly combine natural and artificial lights • to spare soil by replacing it with (4) ................................................. growing mediums (aeroponic, aquaponic or hydroponic mediums) • to guarantee a (5) ................................................. footprint: as less land is used, existing horizontal farmland can be returned to its natural ecosystem • to spare energy resources and water (70-95 % (6) ................................................. than required for normal cultivation). Additional advantages of this farming innovation are: • it provides a greater certainty of harvest output throughout the year, not being affected by ACTIVITIES unfavourable weather conditions • it allows an increased production of organic crops, thanks to a well-controlled indoor environment • it is human and environmentally friendly: farmers are -
Sustainability Certification for Indoor Urban and Vertical Farms a Sustainable Approach to Addressing Growth in Vertical Farming
SUSTAINABILITY CERTIFICATION FOR INDOOR URBAN AND VERTICAL FARMS A SUSTAINABLE APPROACH TO ADDRESSING GROWTH IN VERTICAL FARMING CLIENT Association for Vertical Farming TEAM Jasim Almeer, Tracy Baldwin, Michelle Bostwick, Maya Ezzeddine, Glen Halperin, Anna Harutyunyan, Adam Levinson, Katharine Macdonald, Kiley Miller, Shawn Peterson, Derrick Sullivan, Donata Tavoraite, Katherine Vera and Mingjie Yuan ADVISOR Susanne DesRoches Association for Vertical Farming | Columbia University SPS | Earth Institute Association for Vertical Farming | Columbia University SPS | Earth Institute 1 The report was developed by students of the Masters of Science in Sustainability Management Fall 2015 Capstone Workshop at the Columbia University School for Professional Studies in association with the Earth Institute. It was made possible by contributions from Jasim Almeer, Tracy Baldwin, Michelle Bostwick, Maya Ezzeddine, Glen Halperin, Anna Harutyunyan, Adam Levinson, Katharine Macdonald, Kiley Miller, Shawn Peterson, Derrick Sullivan, Donata Tavoraite, Katherine Vera and Mingjie Yuan, and with guidance from Susanne DesRoches. Association for Vertical Farming | Columbia University SPS | Earth Institute 2 CONTENTS EXECUTIVE SUMMARY 5 INTRODUCTION: THE NEED FOR URBAN AND VERTICAL FARMING 10 Challenges to Traditional Agriculture & Food Supply 10 Benefits of Urban and Vertical Farming 11 Urban and Vertical Farming Challenges 12 The Need for Standards and Sustainability Certification 13 Client Background and Objectives 14 New York City and Urban and Vertical Farming -
From out of the Blue, Green Farming
From Out of the Blue, Green Farming May 2013 About Recirculating Farms Coalition About Us The Recirculating Farms Coalition is a nationally focused, non-profit collaborative group of farmers, educators, organizations and many others committed to building local sources of healthy, accessible food. Our Mission Through research, education and advocacy, we work together to support the development of eco-efficient farms that use clean recycled water without soil as the basis to grow food. We believe these recirculating farms can create stable green jobs and supply sustainably-grown food – fruits, vegetables, herbs and humanely-raised seafood – in diverse communities nationwide, and someday, worldwide. Our Challenge Today one of every six people in the U.S. is struggling to buy food. As consumers become savvier, so have their requests increased for clean, safe, local food produced in an eco-friendly way. The U.S. government, in response to the public’s growing complaints about our troubled food system, continues to explore various ways to boost domestic food production. Unfortunately, most of the proffered solutions encourage further industrialization and poor quality food. Our challenge is to promote an alternative to this model, one that establishes healthy, sustainable, and local ways to provide food in every community. Our Vision We envision a movement toward community-based food production. This can provide safer, better quality food and domestic green job opportunities. A different way of growing, “recirculating farming,” is emerging nationwide and can meet these goals. Our vision is for communities across the country to build recirculating farms as a source of local, healthy fresh food and stable jobs in a green business, and eventually to expand these same benefits globally. -
Life Cycle Assessment on Vertical Farming
Eero Hallikainen Life Cycle Assessment on Vertical Farming Thesis is submitted in a partial fulfillment of the requirements for the degree of Master of Science in Technology Helsinki 23.12.2018 Supervisor: Assistant professor Matti Kummu Advisor: Associate professor Hanna Tuomisto Aalto-yliopisto, PL 11000, 00076 AALTO www.aalto.fi Diplomityön tiivistelmä Tekijä Eero Hallikainen Työn nimi Elinkaariarvionti kerrosviljelylle Maisteriohjelma Vesi- ja ympäristötekniikka Koodi ENG29 Työn valvoja TkT Matti Kummu Työn ohjaaja FT Hanna Tuomisto Päivämäärä 23.12.2018 Sivumäärä 39+1 Kieli Englanti Tiivistelmä Väestönkasvu, ilmastonmuutoksen vaikutukset sekä kehittyvissä maissa tapahtuva ruokavalion muutos kohti lisääntyvää lihan, hedelmien ja vihannesten kulutusta aiheuttavat merkittävää painetta nykyiselle ruoantuotantoteknologialle. Kasvavan väestön ruokkiminen ennustettavan ruokavalion mukaisesti edellyttää nykyisten ruoantuotantomenetelmien maankäytön tehostamista sekä uusia resurssitehokkaita ruoantuotantoteknologioita. Kerrosviljely edustaa modernia tuotantomenetelmää, jossa perinteisiin kasvatusmenetelmiin verrattuna erittäin korkea maankäytön tehokkuus mahdollistaa kasvatuksen tuomisen lähelle ihmistä. Urbaanista ruoantuotannosta onkin puhuttu 2000-luvun megatrendinä. Tämä tutkimus käsittelee kerrosviljelyä resurssitehokkuuden ja ympäristövaikutusten näkökulmasta. Tutkimukset osoittavat, että suljettuna systeeminä kerrosviljelmä kuluttaa tavanomaista viljeljelytekniikkaa vähemmän vettä, hiilidioksidia ja lannoitteita. Toisaalta fotosynteesin