US5610255.Pdf
Total Page:16
File Type:pdf, Size:1020Kb
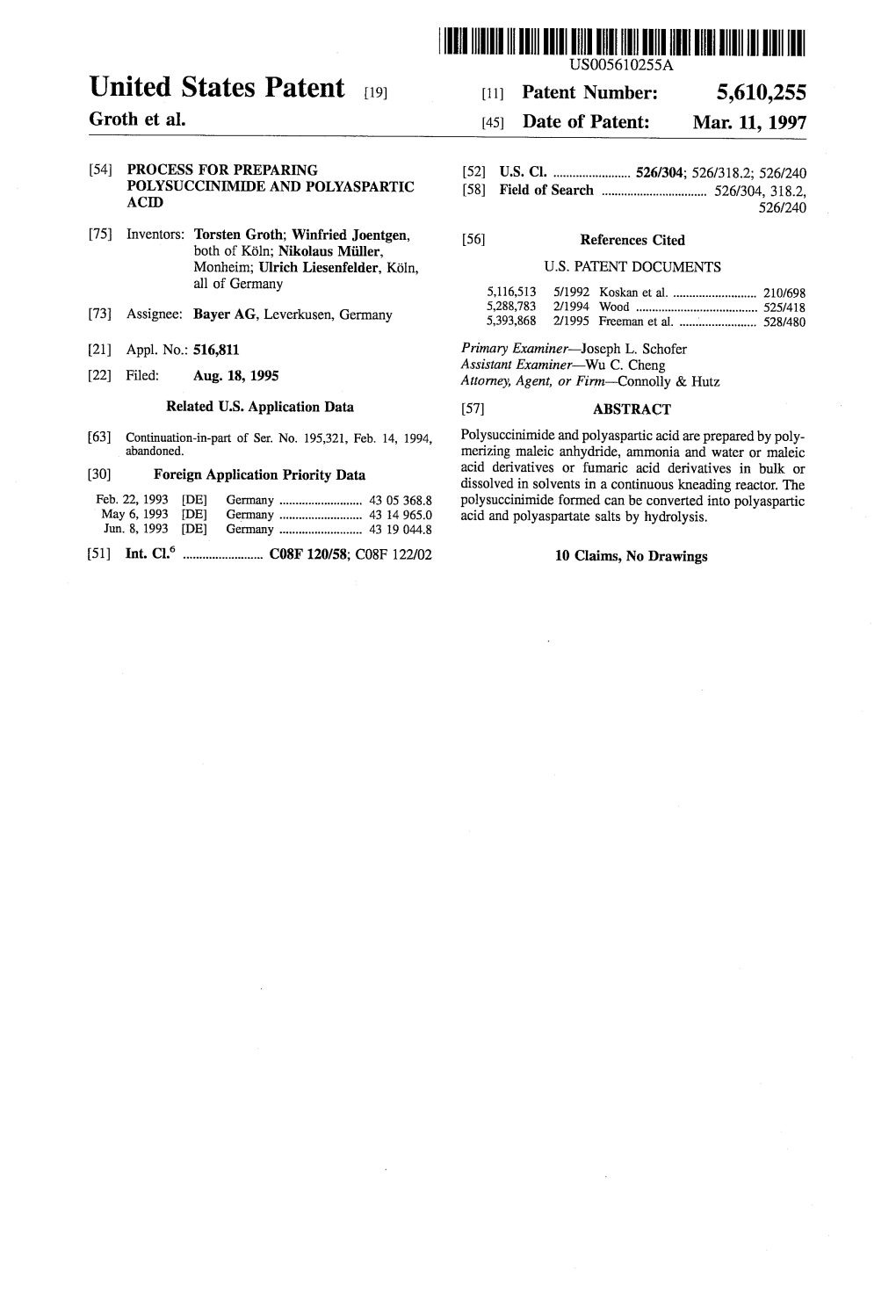
Load more
Recommended publications
-
United States Patent (19) 11 Patent Number: 5,858,244 Tang Et Al
USOO5858244A United States Patent (19) 11 Patent Number: 5,858,244 Tang et al. (45) Date of Patent: Jan. 12, 1999 54 USE OF BIODEGRADABLE POLYMERS IN 4,868,287 9/1989 Sikes et al.. PREVENTION SCALE BUILD-UP 4,906,383 3/1990 Chen et al. ............................. 210/697 5,041,291 8/1991 Bader et al. ............................ 424/426 75 Inventors: Jiansheng Tang, Naperville; Ronald V. 5,051,401 9/1991 Sikes. Davis, Geneva, both of Ill. 5,116,513 5/1992 Koskan et al. 5,247,068 9/1993 Donachy et al.. 73 Assignee: Nalco Chemical Company, Naperville, 5,284.9365,260,272 11/19932/1994 Donachy et al.. III. 5,328,690 7/1994 Sikes. 5,496,914 3/1996 Wood et al. ............................ 528/328 21 Appl. No.: 944,281 5,506,335 4/1996 Uhr et al. ................................ 528/322 5,527,863 6/1996 Wood et al. ............................ 525/432 22 Filed: Oct. 6, 1997 5,658,464 8/1997 Hann et al. ............................. 210/697 5,776,875 7/1998 Tang et al. .............................. 510/247 Related U.S. Application Data Primary Examiner Peter A. Hruskoci 62) Division of Ser. No. 683,001, Jul 16, 1996, Pat. No. Attorney, Agent, Or Firm Hill & Simpson 5,776.875. 57 ABSTRACT (51)52 U.S.Int. Cl.Cl. .................................................................... 210,698. 252/180: CO2F5/12 210,700 Albiodegradable scale inhibitor- - - - - and dispersant is provided. 58 Field of Search ..................................... 210/698-701; The scale inhibitor includes a copolymer comprising at least 252/180, 181,510/24. one of N-oxygenated hydrocarbonamide monomers and at s s least one of amino acid monomers. -
Stimuli-Responsive Poly(Aspartamide) Derivatives and Their Applications As Drug Carriers
International Journal of Molecular Sciences Review Stimuli-Responsive Poly(aspartamide) Derivatives and Their Applications as Drug Carriers Guangyan Zhang 1,2,* , Hui Yi 1 and Chenhui Bao 1 1 School of Materials and Chemical Engineering, Hubei University of Technology, Wuhan 430068, China; [email protected] (H.Y.); [email protected] (C.B.) 2 Hubei Provincial Key Laboratory of Green Materials for Light Industry, Hubei University of Technology, Wuhan 430068, China * Correspondence: [email protected] Abstract: Poly(aspartamide) derivatives, one kind of amino acid-based polymers with excellent biocompatibility and biodegradability, meet the key requirements for application in various areas of biomedicine. Poly(aspartamide) derivatives with stimuli-responsiveness can usually respond to external stimuli to change their chemical or physical properties. Using external stimuli such as tem- perature and pH as switches, these smart poly(aspartamide) derivatives can be used for convenient drug loading and controlled release. Here, we review the synthesis strategies for preparing these stimuli-responsive poly(aspartamide) derivatives and the latest developments in their applications as drug carriers. Keywords: poly(aspartamide) derivatives; stimuli-responsive; drug carrier; nanoparticles; hydrogel; polymer-drug conjugate; drug-loading; controlled drug release Citation: Zhang, G.; Yi, H.; Bao, C. Stimuli-Responsive Poly(aspartamide) Derivatives and 1. Introduction Their Applications as Drug Carriers. Though the carbon-carbon backbone is conducive to the stability of polymers, it also Int. J. Mol. Sci. 2021, 22, 8817. limits the applications of these polymers in biomedical fields due to its low biocompat- http://doi.org/10.3390/ijms22168817 ibility and non-biodegradability. In the past decades, the interest in amino acid-based biodegradable polymers has increased significantly in biomedicine due to their good Academic Editors: Ádám Juhász and biocompatibility, biodegradability and non-toxicity of their degradation products. -
Llllllllllllli|||Ll|||Ll|L|L||||L|L|||Lll|||||Lllllllllilllllllllllllllllll US005478919A United States Patent [19] [11] Patent Number: 5,478,919 Koskan Et Al
llllllllllllli|||ll|||ll|l|l||||l|l|||lll|||||lllllllllilllllllllllllllllll US005478919A United States Patent [19] [11] Patent Number: 5,478,919 Koskan et al. [45] Date of Patent: Dec. 26, 1995 v [54] ASPARTIC ACID COPOLYMERS AND THEIR 3,846,380 10/1972 Fujimoto et a1. ..................... .. 528/363 PREPARATION 5,292,858 3/1994 Wood .................... .. 528/345 5,357,004 10/1994 Calton m1. ......................... .. 525/435 [75] Inventors: Larry P. Koskan, Orland Park; James Primary Examiner_sheney A Dodson F. Kneller, LaGrange Park; Daniel A. A t F _P ' R Bah Batzel, Skokie, all 01:111. Attorney’ gen’ or m" cm ' n [57] ' ABSTRACT [ 73 ] A’Sslgnee :Dlon ar Corporatlon’‘ Bed fPk,I11.0rd aI Aspartic.. acld precursors such as mono and diammomum. maleate, maleamic acid, ammonium maleamate, ammonium [21] Appl' No‘: 283’268 malate and mixtures of these and other precursors are [22] Filed; JuL 29’ 1994 copolycondensed thermally with a variety of mono, di and multifunctional monomers containing amino, hydroxyl and Int. Cl-6 ................................................... .. carboxyl functional groups_ The resulting condensation [52] US. Cl. ........................ .. 528/363; 525/418; 525/419; copolymers and terpolymers contain succinimide units 525/420; 528/328; 528/332; 528/335; 528/345 derived from aspartic acid precursors, condensed with other [58] Field of Search ................................... .. 525/418, 419, functional group monomers usually though amide and ester 525/420; 528/328, 363, 332, 335, 345 linkages. Hydrolysis of the polysuccinimide copolymers and 7 terpolymers with alkali, alkaline earth and ammonium [56] References Cited ' hydroxide produces aspartic acid copolymer and terpolymer U.s. PATENT DOCUMENTS Salts‘ 2,306,918 2/1940 Weiss et a1. -
Properties of Copolymers of Aspartic Acid and Aliphatic Dicarboxylic Acids Prepared by Reactive Extrusion
Properties of Copolymers of Aspartic Acid and Aliphatic Dicarboxylic Acids Prepared by Reactive Extrusion Randal L. Shogren,1 J. L. Willett,1 David Westmoreland,2 Sergio O. Gonzalez,1* Kenneth M. Doll,1 Graham Swift2 1Plant Polymer Unit, National Center for Agricultural Utilization Research, USDA/ARS, Peoria, Illinois 2Folia, Inc., Birmingham, Alabama Received 30 April 2008; accepted 24 June 2008 DOI 10.1002/app.28944 Published online 10 September 2008 in Wiley InterScience (www.interscience.wiley.com). ABSTRACT: Aspartic acid is prepared chemically or only about 5 min. Mw generally increased with aspartic/ by the fermentation of carbohydrates. Currently, low mo- diacid ratio but melt viscosities became very high and lecular weight polyaspartic acids are prepared commer- processing became difficult at ratios >16. Most of the cially by heating aspartic acid at high temperatures copolymers exhibited inhibition of calcium carbonate (>220C) for several hours in the solid state. In an effort precipitation at concentrations similar to that of pure to develop a more rapid, continuous, melt polymeriza- polyaspartic acid and thus may find application as anti- tion scheme, aspartic acid was copolymerized with scalants. VC 2008 Wiley Periodicals, Inc. J Appl Polym Sci 110: adipic, azelaic, sebacic, and dodecanedioic acids using a 3348–3354, 2008 vented twin-screw extruder. Copolymers having ratios of aspartic/diacid 16 and Mw up to 9100 were prepared Key words: biodegradable; copolymerization; extrusion; at temperatures of 240–260C and residence times of polyamides INTRODUCTION to the high temperatures and long times required for such a solid state polyamidation. Recently, the use of biobased products to replace To accelerate the reaction, a number of different those made from increasingly costly imported petro- solvents such as toluene, mesitylene, DMF, sulfolane, leum has gained momentum.1–4 For example, there tetralin12 and catalysts such as phosphoric acid, sul- is considerable interest in replacing polyacrylic acid, furic acid, and salts thereof13 have been studied. -
Synthesis of Indocyanine Green Functionalized Comblike Poly(Aspartic Acid) Derivatives for Enhanced Cancer Cell Ablation by Targeting Endoplasmic Reticulum
Electronic Supplementary Material (ESI) for Polymer Chemistry. This journal is © The Royal Society of Chemistry 2018 Synthesis of indocyanine green functionalized comblike poly(aspartic acid) derivatives for enhanced cancer cell ablation by targeting endoplasmic reticulum Jiaxun Wan,a Luyan Sun,a Pan Wu,a Fang Wang,a Jia Guo,a Jianjun Cheng,b and Changchun Wang*a †State Key Laboratory of Molecular Engineering of Polymers and Department of Macromolecular Science, Fudan University, Shanghai 200433, P.R. China., §Department of Materials Science and Engineering, University of Illinois at Urbana– Champaign, Urbana, Illinois 61801, USA. S1 Materials. Phosphoric acid, sulfolane, L-aspartic acid, 2-(2-chloroethoxy)ethanol, sodium hydride, triphenylphosphine, methoxypoly(ethylene glycol) (Mn~1000), p- toluenesulfonyl, ethyl iodide, 1-Bromo-6-chlorohexane, sodium iodide and Cremophor® EL were obtained from Aladdin (Shanghai, China). NaCl, Na2SO4, MgSO4, NH4Cl, sodium hydroxide, HCl, diethyl ether, methanol, ethanol, ethyl acetate, tetrahydrofuran, dichloromethane, pyridine, trimethylamine, acetone, dimethyl formamide, acetonitrile, acetic anhydride were purchased from Sinopharm Chemical Reagent Co., Ltd. (Shanghai, China). Mesitylene and 1,1,2-trimethylbenz[e]indole were purchased from Energy Company (Shanghai, China). Propargyl bromide was purchased from Tokyo Chemical Industry (Shanghai, China). Glutaconaldehyde dianil hydrochloride was purchased from J&K Chemical Ltd. (Shanghai, China). Paclitaxel (PTX) was purchased from Adamas Reagent, Ltd. -
Lignocellulosic Biomass: a Sustainable Platform for Production of Bio-Based Chemicals and Polymers
Lignocellulosic Biomass: A Sustainable Platform for Production of Bio-Based Chemicals and Polymers Furkan H. Isikgora, C. Remzi Becer*b a Department of Chemistry, Boğaziçi University, Bebek, 34342 İstanbul, Turkey b School of Engineering and Materials Science, Queen Mary University of London, Mile End Road, E1 4NS London, United Kingdom The demand for petroleum dependent chemicals and materials has been increasing despite the dwindling of their fossil resources. As the dead-end of petroleum based industry has started to appear, today’s modern society has to implement alternative energy and valuable chemical resources immediately. Owing to the importance of lignocellulosic biomass for being the most abundant and bio-renewable biomass on earth, this critical review provides insights into the potential of lignocellulosic biomass as an alternative platform to fossil resources. In this context, over 200 value-added compounds, which can be derived from lignocellulosic biomass by using various treatment methods, are presented with their references. Lignocellulosic biomass based polymers and their commercial importance are also reported mainly in the frame of these compounds. The review article aims to draw the map of lignocellulosic biomass derived chemicals and their synthetic polymers, and to reveal the scope of this map in today’s modern chemical and polymer industry. cheaper than any other commodity products. However, the 1. Introduction. competitive price advantage of fossil fuels during the last century has disappeared.5 After crossing the oil production peak, the Modern industrial polymerization technologies make it possible dwindling of fossil resources will further boost the oil price and to produce versatile polymers with highly tunable properties and this situation will drastically impact the cost-effectiveness and broad range of applications. -
B COMMISSION REGULATION (EU) No 231/2012 of 9 March 2012 Laying Down Specifications for Food Additives Listed in Annexes II A
02012R0231 — EN — 18.08.2017 — 016.001 — 1 This text is meant purely as a documentation tool and has no legal effect. The Union's institutions do not assume any liability for its contents. The authentic versions of the relevant acts, including their preambles, are those published in the Official Journal of the European Union and available in EUR-Lex. Those official texts are directly accessible through the links embedded in this document ►B COMMISSION REGULATION (EU) No 231/2012 of 9 March 2012 laying down specifications for food additives listed in Annexes II and III to Regulation (EC) No 1333/2008 of the European Parliament and of the Council (Text with EEA relevance) (OJ L 83, 22.3.2012, p. 1) Amended by: Official Journal No page date ►M1 Commission Regulation (EU) No 1050/2012 of 8 November 2012 L 310 45 9.11.2012 ►M2 Commission Regulation (EU) No 25/2013 of 16 January 2013 L 13 1 17.1.2013 ►M3 Commission Regulation (EU) No 497/2013 of 29 May 2013 L 143 20 30.5.2013 ►M4 Commission Regulation (EU) No 724/2013 of 26 July 2013 L 202 11 27.7.2013 ►M5 Commission Regulation (EU) No 739/2013 of 30 July 2013 L 204 35 31.7.2013 ►M6 Commission Regulation (EU) No 816/2013 of 28 August 2013 L 230 1 29.8.2013 ►M7 Commission Regulation (EU) No 817/2013 of 28 August 2013 L 230 7 29.8.2013 ►M8 Commission Regulation (EU) No 1274/2013 of 6 December 2013 L 328 79 7.12.2013 ►M9 Commission Regulation (EU) No 264/2014 of 14 March 2014 L 76 22 15.3.2014 ►M10 Commission Regulation (EU) No 298/2014 of 21 March 2014 L 89 36 25.3.2014 ►M11 Commission Regulation -
(3) Assignee Rolar Corporation, Bedford Park, E 7, "O2 Primary Examiner-Morton Foelak 21) Appl
USOOS373O88A United States Patent (19) 11 Patent Number: 5,373,088 Koskan et al. 45 Date of Patent: Dec. 13, 1994 54 PRODUCTION OF POLYASPARTIC ACID (56) References Cited FROM MALEICACD AND AMMONA U.S. PATENT DOCUMENTS 75 Inventors: Larry P. Koskaa, Orland Park; Abdul 5,286,810 2/1994 Wood .................................. 525/421 R. Y. Meah, Justice, both of Ill. 5,288,783 2/1994 Wood ........... ....... 525/48 (3) Assignee Rolar Corporation, Bedford Park, E 7, "O2 Primary Examiner-Morton Foelak 21) Appl. No.: 188,539 Assistant Examiner-Shelley A. Dodson 22 Filed: Jan. 28, 1994 Attorney, Agent, or Firm-Olson & Hierl, Ltd. 57 ABSTRACT Related U.S. Application Data (63) Continuation-in-part- of Ser. No. 947,712, Sep. 18, 1992, ofPolyaspartic annonium acid maleate is produced derived by from thermal maleic condensation acid and Pat. No. 5,296,578. ammonia. Solid ammonium maleate in particulate form 511 Int. Cl............................................... CO8G 69/00 is heated to a temperature of at least about 170° C. to 52 U.S. C. .................................... 528/363; 525/418; effect thermal condensation to a polysuccinimide which 525/419, 525/420, 528/328 is then base hydrolyzed to a polyaspartic acid salt. 58) Field of Search ................ 528/363, 328; 525/418, 525/419, 420 14 Claims, No Drawings 5,373,088 2 hours is preferred. More preferably, the reaction time is PRODUCTION OF POLYASPARTIC ACD FROM about 7 to about 10 hours. MALE CACID AND AMMONA Maleic acid and ammonia are present in the aforesaid aqueous medium in a mole ratio of at least about 1:1, CROSS-REFERENCE TO RELATED 5 usually in a respective mole ratio in the range of about APPLICATIONS 1:1 to about 1:12, preferably in a respective mole ratio of This application is a continuation-in-part of copend about 1:1 to about 1:5. -
Production of Polysuccinimide by Thermal Polymerization of Maleamic Acid
Europaisches Patentamt .19) European Patent Office Office europeen des brevets © Publication number : 0 593 1 87 A1 12 EUROPEAN PATENT APPLICATION © Application number : 93307858.6 © int. ci.5 : C08G 69/10, C08G 73/10, C11D 1/00 © Date of filing : 01.10.93 © Priority : 13.10.92 US 960070 (72) Inventor : Freeman, Michael Bennett 830 Church Road Harleysville, Pennsylvania 19438 (US) @ Date of publication of application : Inventor : Paik, Yi Hyon 20.04.94 Bulletin 94/16 3 Exeter Court Princeton, New Jersey 08540 (US) Inventor : Simon, Ethan Scott © Designated Contracting States : 2114 Lincoln Drive East AT BE CH DE DK ES FR GB GR IE IT LI LU NL Ambler, Pennsylvania 19002 (US) PT SE Inventor : Swift, Graham 901 Cross Lane Blue Bell, Pennsylvania 19422 (US) © Applicant : ROHM AND HAAS COMPANY Independence Mall West Philadelphia Pennsylvania 19105 (US) (74) Representative : Smith, Julian Philip Howard et al Rohm and Haas (UK) Limited, European Operations Patent Dept., Lennig House, 2 Masons Avenue Croydon CR9 3NB (GB) © Production of polysuccinimide by thermal polymerization of maleamic acid. © A method for producing polysuccinimide is provided. Thermal polymerization of maleamic acid at a temperature of from about 160°C to about 330°C produces polysuccinimide. The reaction is optionally conducted in the presence of one or more processing aids, solvents or diluents. The polysuccinimide is particularly useful as a detergent additive. 00 CO If) LU Jouve, 18, rue Saint-Denis, 75001 PARIS EP 0 593 187 A1 The present invention relates to a process for preparing polysuccinimide by the thermal polymerization of maleamic acid. This invention also relates to the use of polysuccinimide prepared from the thermal polymer- ization of maleamic acid as a detergent additive. -
Presidential Green Chemistry Challenge: Award Recipients, 1996
The Presidential Green Chemistry Challenge Award Recipients 1996—2014 Contents Introduction................................................................................................................1 2014 Winners Academic Award: Professor Shannon S. Stahl, University of Wisconsin-Madison .......................................................................2 Small Business Award: Amyris..................................................................................................................... 3 Greener Synthetic Pathways Award: Solazyme, Inc. ....................................................................................................... 4 Greener Reaction Conditions Award: QD Vision, Inc. ..................................................................................................... 5 Designing Greener Chemicals Award: The Solberg Company...........................................................................................6 2013 Winners Academic Award: Professor Richard P. Wool, University of Delaware ........................................................................................7 Small Business Award: Faraday Technology, Inc........................................................................................ 8 Greener Synthetic Pathways Award: Life Technologies Corporation ............................................................................. 9 Greener Reaction Conditions Award: The Dow Chemical Company...............................................................................10 -
0 CITRUS BIOTECHNOLOGY in the 21ST CENTURY by SHAUN PAUL
CITRUS BIOTECHNOLOGY IN THE 21ST CENTURY By SHAUN PAUL JENSEN A THESIS PRESENTED TO THE GRADUATE SCHOOL OF THE UNIVERSITY OF FLORIDA IN PARTIAL FULFILLMENT OF THE REQUIREMENTS FOR THE DEGREE OF MASTER OF SCIENCE UNIVERSITY OF FLORIDA 2017 0 © 2017 Shaun Jensen To my wife, daughter, and mother ACKNOWLEDGMENTS I thank my wife for all the time, effort, and love she has spent in helping me get to this point in my career and education. I thank my parents for always being supportive of my decisions and my life goals. I thank my all my sisters for helping me learn valuable life skills without having to experience them. Truly, my whole family is wonderful. 4 TABLE OF CONTENTS page ACKNOWLEDGMENTS .................................................................................................. 4 LIST OF TABLES ............................................................................................................ 8 LIST OF ABBREVIATIONS ........................................................................................... 11 ABSTRACT ................................................................................................................... 15 CHAPTER 1 INTRODUCTION .................................................................................................... 17 Citrus on the Global Stage ...................................................................................... 17 Citrus Characteristics .............................................................................................. 19 Citrus Plant Structure ...................................................................................... -
Presidential Green Chemistry Challenge Awards Program Summary of 1996 Award Entries and Recipients
United States Office of Pollution EPA744-K-96-001 Environmental Protection Prevention and Toxics July 1996 Agency (7406) 1EPA The Presidential Green Chemistry Challenge Awards Program Summary of 1996 Award Entries and Recipients 2 Printed on paper that contains at least 20 percent postconsumer fiber. The Presidential Green Chemistry Challenge Awards Program Contents Awards . .2 Alternative Synthetic Pathways Award . .2 Alternative Solvents/Reaction Conditions Award . .3 Designing Safer Chemicals Award . .4 Small Business Award . .5 Academic Award . .7 Entries . .8 Entries from Academia . .8 Entries from Small Businesses . .12 Entries from Industry and Government . .16 Index . .45 The Presidential Green Chemistry Challenge Awards Program Summary of 1996 Award Entries and Recipients President Clinton announced the Green Chemistry Challenge on March 16, 1995, as one of his Reinventing Environmental Regulations Initiatives. According to President Clinton, the Green Chemistry Challenge was estab- lished to “promote pollution prevention and industrial ecology through a new U.S. Environmental Protection Agency (EPA) Design for the Environment partnership with the chemical industry.” More specifically, the program was established to recognize and support fundamental and innova- tive chemical methodologies that are useful to industry and that accomplish pollution prevention through source reduction. EPA Administrator Carol Browner announced the Green Chemistry Challenge Awards Program on October 30, 1995. She described the program as an opportunity for individuals, groups, and organizations “to compete for Presidential awards in recognition of fundamental breakthroughs in cleaner, cheaper, smarter chemistry.” The Green Chemistry Challenge Awards Program provides national recognition for technologies that incorporate green chemistry principles into chemical design, manufacture, and use. Entries received for the 1996 Presidential Green Chemistry Challenge Awards were judged by an independent panel of technical experts convened by the American Chemical Society.