(12) Patent Application Publication (10) Pub. No.: US 2014/0370242 A1 Constantz Et Al
Total Page:16
File Type:pdf, Size:1020Kb
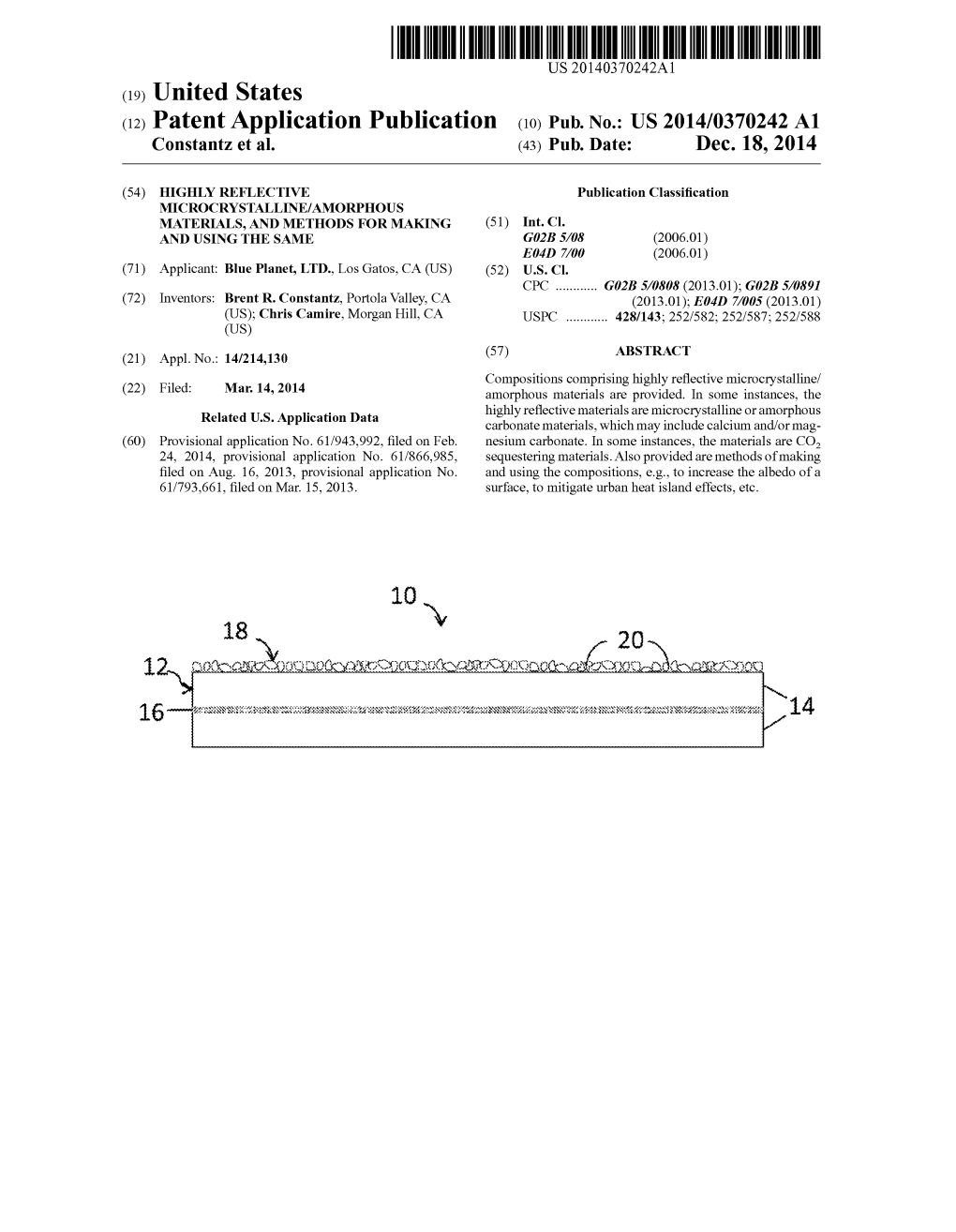
Load more
Recommended publications
-
Watercolor Basics with Susan Donohoe
Watercolor Basics with Susan Donohoe BASICS SUPPLY LIST FOR - TECHNIQUES - Day 1 The lists are long, beginners should bring what they have. They SHOULD NOT go out and buy supplies just to have them. I will bring supplies that they can use to fill in the blanks. Better for them to learn in the workshop what is best for them to buy instead of wasting their money. Personal Needs for each day: Please bring any of these items that you will require. A cushion for your chair, the day can get long for your backside. Your lunch each day. There is a microwave and a small refrigerator for your use. Keep it simple. Hydration-bring plenty of liquid to stay hydrated. A sweater or work shirt to stay comfortable as the room temperature may fluctuate throughout the day. Brushes: Preferred brands: Escoda, Holbein, Cheap Joe’s, Loew-Cornell, Da Vinci, Halcyon One of each if you have them: Round: #6, #10, #14, #18+ (the biggest round brush you own - no need to buy one.) Flat: 1/2”, 1”, 2”, Hake (if you have one) Scrubber brushes: assorted sizes. (These brushes can be purchased at Michael’s or JoAnn’s. They are stiff brushes similar to oil painting brushes. They are sometimes called fabric brushes.) Paper: Arches #140 - Cold Press - 1 full sheet. If you know how and wish to do so prior to class, you can tear the full sheet into 4 equal 1/4 sheet pieces. Paint: Artist Grade Paint only!!!! Preferred Brands: Holbein, Daniel Smith, Mission, Aquarelle Sennelier, M. -
Tucson Art Academy Online Skip Whitcomb
TUCSON ART ACADEMY ONLINE SKIP WHITCOMB PAINTS WHITE Any good to professional quality Titanium or Titanium/Zinc White in large tubes(150-200ML) size. Jack Richeson Co., Gamblin, Vasari, Utrecht, Winsor & Newton are all good brands, as are several other European manufacturers. I strongly recommend staying away from student grade paints, they do not mix or handle the same as higher/professional grade paints. YELLOWS Cadmium Yellow Lemon Cadmium Yellow Lt. (warm) Cad. Yellow Medium or Deep Indian Yellow ORANGES Cadmium Yellow Orange (optional) Cadmium Orange REDS Cadmium Red Light/ Pale/ Scarlet (warm) Cadmium Red Deep Permanent Alizarin Crimson Permanent Rose (Quinacridone) BLUES Ultramarine Blue Deep or Dark Cobalt Blue Prussian Blue or Phthalo Blue GREENS Viridian Viridian Hue (Phthalo Green) Chrome Oxide Green Olive Green Sap Green Yellow Green VIOLETS Mauve Blue Shade (Winsor&Newton) Dioxazine Violet or Purple EARTH COLORS Yellow Ochre Raw Sienna Raw Umber Burnt Sienna Terra Rosa Indian Red Venetian Red Burnt Umber Van Dyke Brown BLACKS Ivory Black Mars Black Chromatic Black Blue Black MARS COLORS Mars Yellow Mars Orange Mars Red Mars Violet IMPORTANT TO NOTE!! Please don’t be intimidated by this list! You will not be required to have all these colors on hand for our class. This is intended to be a recommendation for the studio. Specific colors on this list will come in handy for mixing in certain color plans. I will be happy to make suggestions along the way A good working palette for the studio would be: Cad. Yellow Lemon, Cad. Yellow Pale(warm), and/or Cad. -
Pale Intrusions Into Blue: the Development of a Color Hannah Rose Mendoza
Florida State University Libraries Electronic Theses, Treatises and Dissertations The Graduate School 2004 Pale Intrusions into Blue: The Development of a Color Hannah Rose Mendoza Follow this and additional works at the FSU Digital Library. For more information, please contact [email protected] THE FLORIDA STATE UNIVERSITY SCHOOL OF VISUAL ARTS AND DANCE PALE INTRUSIONS INTO BLUE: THE DEVELOPMENT OF A COLOR By HANNAH ROSE MENDOZA A Thesis submitted to the Department of Interior Design in partial fulfillment of the requirements for the degree of Master of Fine Arts Degree Awarded: Fall Semester, 2004 The members of the Committee approve the thesis of Hannah Rose Mendoza defended on October 21, 2004. _________________________ Lisa Waxman Professor Directing Thesis _________________________ Peter Munton Committee Member _________________________ Ricardo Navarro Committee Member Approved: ______________________________________ Eric Wiedegreen, Chair, Department of Interior Design ______________________________________ Sally Mcrorie, Dean, School of Visual Arts & Dance The Office of Graduate Studies has verified and approved the above named committee members. ii To Pepe, te amo y gracias. iii ACKNOWLEDGMENTS I want to express my gratitude to Lisa Waxman for her unflagging enthusiasm and sharp attention to detail. I also wish to thank the other members of my committee, Peter Munton and Rick Navarro for taking the time to read my thesis and offer a very helpful critique. I want to acknowledge the support received from my Mom and Dad, whose faith in me helped me get through this. Finally, I want to thank my son Jack, who despite being born as my thesis was nearing completion, saw fit to spit up on the manuscript only once. -
A New Evaluation of the Colors of the Sky for Artists and Designers
Sky Blue, But What Blue? A New Evaluation of the Colors of the Sky for Artists and Designers Ken Smith* Faculty of Art and Design, Monash University, Melbourne, Victoria, Australia Received 28 April 2006; accepted 21 June 2006 Abstract: This study describes a process of relating the solid that is capable of representing most of the colors of perceptual analysis of the colors of the terrestrial atmos- the sky using four of these pigments is proposed. phere to currently available pigments used in artists’ painting systems. This process sought to discover how the colors of the sky could be defined and simulated by these AN EMPIRICAL METHOD FOR ANALYZING pigments. The author also describes how confusion over SKY COLOR the bewildering choice of suitable pigments on offer in the market place can be clarified. Ó 2006 Wiley Periodicals, Science can explain why the earth’s atmosphere appears Inc. Col Res Appl, 32, 249 – 255, 2007; Published online in Wiley Inter- blue, the preferential scattering by air molecules of short 2 Science (www.interscience.wiley.com). DOI 10.1002/col.20291 wavelength light photons emitted from the sun. For artists the consequential questions are often more likely to Key words: art; design; sky color; perceived color; envi- be not why, but rather what; what are the blue colors that ronment; pigments; painting systems are perceived in the sky? These were the fundamental questions that lead to a reappraisal of how the colors of the sky can be represented by the pigments used in con- INTRODUCTION temporary painting systems. Before attempting to answer this question, a number of parameters had to be created. -
Gamblin Provides Is the Desire to Help Painters Choose the Materials That Best Support Their Own Artistic Intentions
AUGUST 2008 Mineral and Modern Pigments: Painters' Access to Color At the heart of all of the technical information that Gamblin provides is the desire to help painters choose the materials that best support their own artistic intentions. After all, when a painting is complete, all of the intention, thought, and feeling that went into creating the work exist solely in the materials. This issue of Studio Notes looks at Gamblin's organization of their color palette and the division of mineral and modern colors. This visual division of mineral and modern colors is unique in the art material industry, and it gives painters an insight into the makeup of pigments from which these colors are derived, as well as some practical information to help painters create their own personal color palettes. So, without further ado, let's take a look at the Gamblin Artists Grade Color Chart: The Mineral side of the color chart includes those colors made from inorganic pigments from earth and metals. These include earth colors such as Burnt Sienna and Yellow Ochre, as well as those metal-based colors such as Cadmium Yellows and Reds and Cobalt Blue, Green, and Violet. The Modern side of the color chart is comprised of colors made from modern "organic" pigments, which have a molecular structure based on carbon. These include the "tongue- twisting" color names like Quinacridone, Phthalocyanine, and Dioxazine. These two groups of colors have unique mixing characteristics, so this organization helps painters choose an appropriate palette for their artistic intentions. Eras of Pigment History This organization of the Gamblin chart can be broken down a bit further by giving it some historical perspective based on the three main eras of pigment history – Classical, Impressionist, and Modern. -
Color Chart Rates and Transparencies.Indd
COLOR CHART KEY LIST OF COLORS ALPHABETICALLY COLOR NAME Color Index# TR DR ALIZARIN CRIMSON PR83 ST D IRIDESCENT PEWTER SO C chemical composition 1,2 dihydroxy anthraquinone on alumina base metal oxides on mica ALIZARIN ORANGE PY83 + PR177 T E IRIDESCENT SILVER OD TR = TRANSPARENCIES indian yellow + anthraquinone metal oxides on mica O = OPAQUE AZURE BLUE OD IVORY BLACK PBlk9 SO D phthalo blue + ultramarine blue + titanium-zinc white carbon from charred bone SO = SEMI-OPAQUE BLENDING STICK TE JAUNE BRILLANT OE ST = SEMI-TRANSPARENT contains no pigment cadmium orange and yellow + iron oxide + titanium-zinc white T = TRANSPARENT BLENDING STICK WITH DRIER TA KING’S BLUE OC contains no pigment cobalt blue + titanium-zinc white DR = PIGMENT STICK DRYING RATES BRILLIANT YELLOW X-PALE OE LAMP BLACK PBlk6 O E+ titanium-zinc white + cadmium yellow carbon from oil fl ame STROKE LIGHT FIRM IMPASTO BROWN PINK PR101 ST C MANGANESE VIOLET PV16 ST B A = Very Fast 1 - 2 Days 1 - 2 Days 2 - 4 Days transparent iron oxide manganese ammonium phosphate BURNT SIENNA PBr7 ST B MANGANESE BLUE HUE TE B = Fast 2 - 4 Days 3 - 7 Days 5 - 10 Days natural earth, calcined cerulean blue + phthalo blue + zinc sulfi de C = Medium 6 - 9 Days 7 - 12 Days 14 - 17 Days BURNT UMBER PBr7 SO A MARS BLACK PBlk11 O C D = Slow 7 - 12 Days 12 - 16 Days 15 - 27 Days natural earth, calcined ferroso-ferric oxide CADMIUM GREEN PG18 + PY37 SO B MARS ORANGE PR101 O C E = Very Slow 10 - 12 Days 16 - 30 Days 28 - 50 Days viridian + cadmium yellow synthesized iron oxide, calcined E+ = Off Chart 45 Days 70 Days 90 Days or more CADMIUM GREEN PALE PG18 + PY37 O C MARS RED PR101 O C viridian + cadmium yellow synthesized iron oxide, calcined CADMIUM LEMON PY37 O C MARS VIOLET PR101 O C c.p. -
Colour Chart.Indd
The Paints, Past and Present Details and Descriptions of Colours This section gives assessments for certain determinable characteristics of all the colours presently in my range, as well as a few informal remarks on their qualities and idiosynchrasies when used. Following the pattern already laid out on all my tube and can labels, and on my more recent colour charts, I give: (1) The Colour Index Number: This is an international system for classifying and identifying pigments solely by their (often very complex) chemical formulae( e.g P(igment) R(ed) 106, Mercuric Sulphide known as Genuine Vermilion). The use of vague traditional or invented colour names is thus clarifi ed, and so, in theory at least, is the vexed matter of what pigments manufacturers actually put into their paints. If a colourman is honest, each constituent pigment in a paint can be specifi ed precisely, and the practice of secretly adulterating or even completely substituting cheaper alternatives is made impossible. Assuming, that is, the colourman is honest…I can certainly state that there are no secret additions to any of the paints in my range. What you read as the C.I number on the label is what you get. (2) Estimated Relative Drying Speed: Bearing in mind that all drying speeds will be affected by temperature, humidity and light levels, these give a broad calibration of comparative speeds, from the Very Fast, such as the Umbers, many of which, if used neat, will be touch dry within a hot summer day, to the Very Slow, which in unmixed state, might take up to a week. -
2Bbb2c8a13987b0491d70b96f7
An Atlas of Rare & Familiar Colour THE HARVARD ART MUSEUMS’ FORBES PIGMENT COLLECTION Yoko Ono “If people want to make war they should make a colour war, and paint each others’ cities up in the night in pinks and greens.” Foreword p.6 Introduction p.12 Red p.28 Orange p.54 Yellow p.70 Green p.86 Blue p.108 Purple p.132 Brown p.150 Black p.162 White p.178 Metallic p.190 Appendix p.204 8 AN ATLAS OF RARE & FAMILIAR COLOUR FOREWORD 9 You can see Harvard University’s Forbes Pigment Collection from far below. It shimmers like an art display in its own right, facing in towards Foreword the glass central courtyard in Renzo Piano’s wonderful 2014 extension to the Harvard Art Museums. The collection seems, somehow, suspended within the sky. From the public galleries it is tantalising, almost intoxicating, to see the glass-fronted cases full of their bright bottles up there in the administra- tive area of the museum. The shelves are arranged mostly by hue; the blues are graded in ombre effect from deepest midnight to the fading in- digo of favourite jeans, with startling, pleasing juxtapositions of turquoise (flasks of lightest green malachite; summer sky-coloured copper carbon- ate and swimming pool verdigris) next to navy, next to something that was once blue and is now simply, chalk. A few feet along, the bright alizarin crimsons slake to brownish brazil wood upon one side, and blush to madder pink the other. This curious chromatic ordering makes the whole collection look like an installation exploring the very nature of painting. -
Daniel Smith Cielab Spreadsheet
DANIEL SMITH Watercolors - CIELab Cool/Warm Rating WARMEST COLORS WARM COLORS COOL COLORS COOLEST COLORS Alizarin Crimson Monte Amiata Natural Sienna Amazonite Genuine Amethyst Genuine Blue Apatite Genuine Alvaro's Caliente Grey Mummy Bauxite Aureolin (Cobalt Yellow) Carbazole Violet Cerulean Blue Anthraquinoid Red Naphthamide Maroon Azo Yellow Cobalt Blue Violet Cerulean Blue Chromium Anthraquinoid Scarlet Naples Yellow Bismuth Vanadate Yellow Cobalt Violet Cobalt Blue Aussie Red Gold New Gamboge Black Tourmaline Genuine Cobalt Violet Deep Cobalt Teal Blue Bloodstone Genuine Nickel Azo Yellow Cadmium Yellow Light Hue French Ultramarine Cobalt Turquoise Bordeaux Olive Green Cascade Green Imperial Purple Jane's Grey Bronzite Genuine Organic Vermilion Chinese White Indanthrone Blue Kyanite Genuine Buff Titanium Perinone Orange Chromium Green Oxide Indigo Lapis Lazuli Genuine Burgundy Red Ochre Permanent Alizarin Crimson Cobalt Green Lavender Lunar Blue Burgundy Yellow Ochre Permanent Brown Cobalt Green Pale Lunar Violet Manganese Blue Hue Burnt Bronzite Genuine Permanent Orange Deep Sap Green Mayan Violet Mayan Blue Genuine Burnt Sienna Permanent Red Diopside Genuine Moonglow Mayan Dark Blue Burnt Sienna Light Permanent Red Deep Fuchsite Genuine Opera Pink Payne's Blue Gray Burnt Tiger's Eye Genuine Permanent Yellow Deep Green Apatite Genuine Permanent Violet Payne's Gray Burnt Umber Perylene Maroon Green Gold Purpurite Genuine Phthalo Blue (Green Shade) Burnt Yellow Ochre Perylene Red Hansa Yellow Light Quinacridone Lilac Phthalo Blue -
From Artist Materials to High-Heat Applications Say Goodbye to the Moody Blues, and Hello to Shepherd's High Performance Blues
From Artist Materials to High-Heat Applications Say Goodbye to the Moody Blues, and Hello to Shepherd's High Performance Blues One of the primary colors, lying between violet and green, is The Shepherd Color Company's roots originate in the the beautiful Blue hue. From the sky to the deep blue sea, 1920s in the ceramic industry, where we supplied colors to a shiny sapphire, blue is the color of trust, excellence, for porcelain enamels. It's no surprise that Blue has been and performance in business. Blue can also be associated one of our first inorganic color pigments. From Blue 299, to sadness, as everyone has felt a little blue at times. This which is the standard “Cobalt Blue” used in artist materials, color can also be perceived as calm and cooling, a lot like to our newest Blue 10G513, better known as YInMn Blue, Shepherd Color’s Arctic® pigments. which expands the range of colors available for building manufacturers that keep products cooler when exposed to An important color in art and ancient times, Ultramarine the sun, Shepherd Color has a blue pigment to meet your Blue was created by lapis lazuli and was mainly mined in high-performance application. Afghanistan and extremely expensive. The invention of synthetic Ultramarine Blue pigments had interesting color, With a vast array of red-shade to green-shade blue pigments but inadequate exterior durability limits its use. available from Shepherd, all have high temperature stability, are resistant to acids, bases, and solvents, and have Cobalt Blue historically has been a excellent weathering, opacity, and reflectivity. -
College Acrylic
College The assortment® ACRYLIC 2019 – Künstler-Acrylfarben Artists’ acrylic colours Made in Germany ACRYLIC College® ACRYLIC – The assortment 2019 • Artists‘ acrylic colours in student quality • 36 colours in 75 ml plastic tubes, 24 colours also in 200 ml tubes and 750 ml jars, 5 acrylic mediums in 200 ml-tubes (College® MEDIUMS) • Good lightfastness • Satin-mat surface Tube 75 ml 36 colours Tube 200 ml 24 colours Jar 750 ml 24 colours 33100013 white 33100014 white 33100030 white 33200013 ivory 33200014 ivory 33200030 ivory 33210013 lemon yellow 33210014 lemon yellow DISCONTINUED 33220013 college yellow 33220014 college yellow 33220030 college yellow 33230013 Indian yellow 33230014 Indian yellow 33230030 Indian yellow 33240013 orange 33240014 orange 33240030 orange 33250013 red orange 33250014 red orange DISCONTINUED 33300013 vermilion red 33300014 vermilion red 33300030 vermilion red 33310013 permanent red 33310014 permanent red 33310030 permanent red 33320013 carmine red 33320014 carmine red 33320030 carmine red 33340013 Bordeaux 33340014 Bordeaux 33340030 Bordeaux NEW 33350013 college magenta 33350014 college magenta 33350030 college magenta 33360013 lavender 33360014 lavender DISCONTINUED 33370013 violet 33370014 violet 33370030 violet NEW 33400013 indigo 33400014 indigo 33400030 indigo NEW 33410013 ultramarine blue 33410014 ultramarine blue 33410030 ultramarine blue 33420013 cobalt blue hue 33420014 cobalt blue hue DISCONTINUED 33430013 college cyan 33430014 college cyan 33430030 college cyan 33440013 azure blue light 33440014 azure -
Pigments, Pigment Preparations, Dyes and Light Stabilizers for Coatings, Plastics, Printing Inks and Specialty Industries
Pigments, pigment preparations, dyes and light stabilizers for coatings, plastics, printing inks and specialty industries Section 0 – Introduction EVP 1007 e, September 2007 supersedes EVP 1007 e, May 2007 editorial deadline: September 25, 2007 This document gives you a survey of all global Please note that all products listed are manufactur- This document is divided into six sections: standard products of BASF's Performance Chemi- ed on an industrial scale and may contain traces of cals for Coatings, Plastics and Specialties business impurities which cannot be avoided. Therefore, this introduction and table of contents unit . BASF does not recommend any of the products information on trademarks, safety and disclaimer, listed for application in foodstuffs, pharmaceuti- product list Listed are organic as well as inorganic pigments, cals, cosmetics or for medical appliances or available technical literature effect pigments, hybrid and stir-in pigments, pig- devices that are to come in contact with body fluids information on approvals for food-contact ment preparations, soluble dyestuffs, light stabili- or viscera. However, BASF offers products that are applications, zers and additives. approved for food-contact applications under cross reference Colour Index to colorant various legislations. Please refer to section 4 of this Not listed in this document are the tailor-made document for additional information. The special preparations for the coloration of plastics, master- requisitions of the European pharma copoeia apply batches. Please