Stochastic Spray and Chemically Reacting Flow in LS-DYNA®
Total Page:16
File Type:pdf, Size:1020Kb
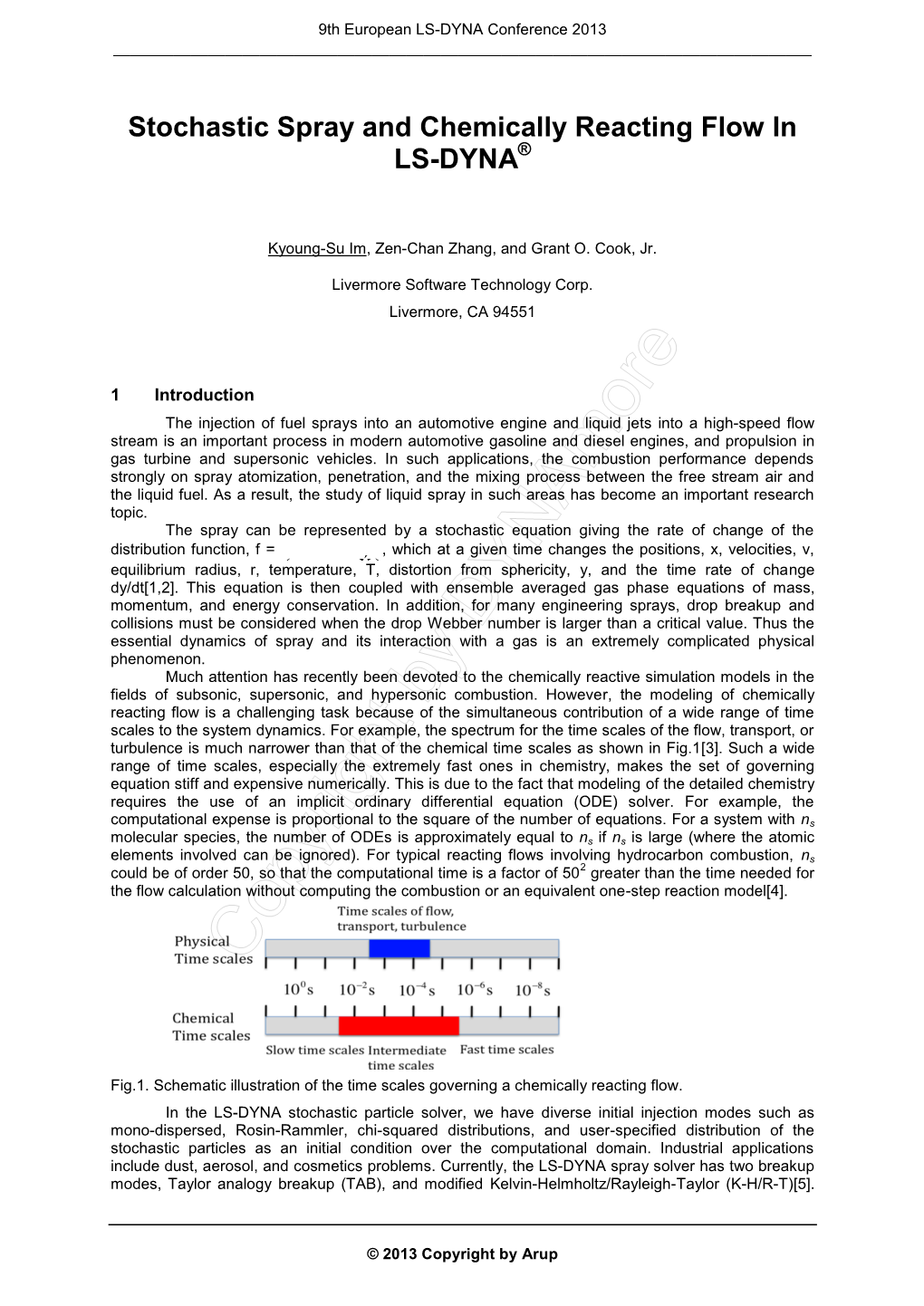
Load more
Recommended publications
-
What Technology Wants / Kevin Kelly
WHAT TECHNOLOGY WANTS ALSO BY KEVIN KELLY Out of Control: The New Biology of Machines, Social Systems, and the Economic World New Rules for the New Economy: 10 Radical Strategies for a Connected World Asia Grace WHAT TECHNOLOGY WANTS KEVIN KELLY VIKING VIKING Published by the Penguin Group Penguin Group (USA) Inc., 375 Hudson Street, New York, New York 10014, U.S.A. Penguin Group (Canada), 90 Eglinton Avenue East, Suite 700, Toronto, Ontario, Canada M4P 2Y3 (a division of Pearson Penguin Canada Inc.) Penguin Books Ltd, 80 Strand, London WC2R 0RL, England Penguin Ireland, 25 St. Stephen's Green, Dublin 2, Ireland (a division of Penguin Books Ltd) Penguin Books Australia Ltd, 250 Camberwell Road, Camberwell, Victoria 3124, Australia (a division of Pearson Australia Group Pty Ltd) Penguin Books India Pvt Ltd, 11 Community Centre, Panchsheel Park, New Delhi - 110 017, India Penguin Group (NZ), 67 Apollo Drive, Rosedale, North Shore 0632, New Zealand (a division of Pearson New Zealand Ltd) Penguin Books (South Africa) (Pty) Ltd, 24 Sturdee Avenue, Rosebank, Johannesburg 2196, South Africa Penguin Books Ltd, Registered Offices: 80 Strand, London WC2R 0RL, England First published in 2010 by Viking Penguin, a member of Penguin Group (USA) Inc. 13579 10 8642 Copyright © Kevin Kelly, 2010 All rights reserved LIBRARY OF CONGRESS CATALOGING IN PUBLICATION DATA Kelly, Kevin, 1952- What technology wants / Kevin Kelly. p. cm. Includes bibliographical references and index. ISBN 978-0-670-02215-1 1. Technology'—Social aspects. 2. Technology and civilization. I. Title. T14.5.K45 2010 303.48'3—dc22 2010013915 Printed in the United States of America Without limiting the rights under copyright reserved above, no part of this publication may be reproduced, stored in or introduced into a retrieval system, or transmitted, in any form or by any means (electronic, mechanical, photocopying, recording or otherwise), without the prior written permission of both the copyright owner and the above publisher of this book. -
Experiences Tuning a J90 for Engineering
ExperiencesExperiences TuningTuning aa J90J90 forfor EngineeringEngineering ApplicationsApplications Sharan Kalwani [email protected] CUG 1997, San Jose MotivationMotivation ● Why do sites choose a J90? – Cost is usually the primary consideration – Computational needs satisfied by J90 – Starting point for future growth – Resources are also a major factor MotivationMotivation (contd...)(contd...) ● Field experience revealed: – Several sites out there (250+) – Site profiles were all different , eg: ● Human resources often limited ● Expertise scarce ● Learning curve was steep ● Balancing act of system versus “real” work BenefitsBenefits ● Share useful tips and techniques ● Gain insight into other possible scenarios ● Learn what works ● Learn what may NOT work CaveatCaveat EmptorEmptor ● Target Audience – Engineering Applications ● Computational Fluid Dynamics (CFD) – STAR-CD, KIVA-2, CHAD ● Metal Deformation Codes – (LS-DYNA) ● Finite Element Analysis (FEA) – NASTRAN, etc... TypicalTypical J90J90 EnvironmentEnvironment ● Usually small systems: – 4 to 8 CPUs – 64 Mwords – Single IOS – SCSI disks (sometimes also IPI disks) – small disk farm – no large online tapes (4 or 8mm only) J90J90 EnvironmentEnvironment (contd)(contd) ● Staff at sites: – single, but multi-tasking person :-) – has a real job in addition to Cray work – usually sophisticated end user, but – not a “pure” systems type TuningTuning RegionsRegions ● UNICOS Kernel ● Memory and ● Process Scheduling ● Disk Drive Strategy Tuning:Tuning: J90J90 KernelKernel ArenaArena ● UNICOS Kernel -
Mechanical Engineering Magazine Will (Subject Line "Letters and Comments")
Mechanical THE MAGAZINE OF ASME ENGINEERING No. 07 139 Technology that moves the world SMALL BUT MIGHTY Robots are boosting warehouse productivity. FASTEST WOMAN ON TWO WHEELS PAGE 18 FLEXIBLE POWER SUIT PAGE 38 BRAIN-CONTROLLED PROSTHETICS PAGE 44 ASME.ORG JULY 2017 GREAT NEWS! Thanks to our partnership with one of the leading engineering professional liability insurance carriers, Beazley Insurance &RPSDQ\ΖQF\RXKDYHDFFHVVWRDQH[SHUWUHVRXUFHIRU\RXUȴUPȇV professional liability needs. And because of this partnership, if you are an ASME member you are eligible for a 10% premium discount* exclusively through our program. ASME PROFESSIONAL LIABILITY PROGRAM DESIGNED SPECIFICALLY FOR ASME 7KH3URIHVVLRQDO/LDELOLW\3URJUDPLVRHUHGWKURXJKDSURYHQ industry leader in the engineering professional liability marketplace: ASME MEMBER EXCLUSIVE COVERAGE BENEFITS: Beazley is one of the top engineering insurance carriers that understands the unique risks engineers face. That’s why the ȏ 10% premium discount* through 3URIHVVLRQDO/LDELOLW\3URJUDPLQFOXGHVȵH[LEOHSROLF\OLPLWV our program DQGGHGXFWLEOHRSWLRQVΖWFRYHUVȴUPVRIDOOVL]HVDVZHOODV ȏ Consent to settle enhancement VHOIHPSOR\HGLQGLYLGXDOV ȏ Early resolution deductible credit Call today at 1.800.640.7637 or visit www.asmeinsurance.com/pl *Based on state filed minimum premium requirements. Administered by Mercer Health & Benefits Administration LLC In CA d/b/a Mercer Health & Benefits Insurance Services LLCt CA Insurance License #0G39709 t AR Insurance License #100102691 This plan is underwritten by Beazley Insurance Company, Inc. t CA Insurance License #0G55497 t WA Insurance License #1298 79128 (7/17) Copyright 2017 Mercer LLC. All rights reserved. LOG ON ASME.ORG MECHANICAL ENGINEERING 01 | JULY 2017 | P. For these articles and other content, visit asme.org. Hybrid Cars Compete for Speed The Formula Hybrid competition is entering its second decade, giving developers and students an opportunity to race hybrid and electric vehicles for speed and endurance. -
Spray Combustion Cross-Cut Engine Research
Spray Combustion Cross-Cut Engine Research Lyle M. Pickett, Scott A. Skeen Sandia National Laboratories FY 2017 DOE Vehicle Technologies Office Annual Merit Review Project ACS005, 11:30 AM, Wed. 7 June 2017 Sponsor: DOE Vehicle Technologies Office Program Managers: Gurpreet Singh and Leo Breton This presentation does not contain any proprietary, confidential, or otherwise restricted information. Overview Timeline Barriers ● Project provides fundamental ● Engine efficiency and emissions research that supports DOE/ ● Understanding direct-injection industry advanced engine sprays development projects. ● CFD model improvement for ● Project directions and engine design/optimization continuation are evaluated annually. Partners ● 15 Industry partners in MOU: Budget Advanced Engine Combustion ● Project funded by DOE/VTO: ● Engine Combustion Network FY17 - $950K – >20 experimental + >20 modeling – >100 participants attend ECN5 ● Project lead: Sandia – Lyle Pickett (PI), Scott Skeen 2 Engine efficiency gains require fuel (DI spray) delivery optimization ● Barriers for high-efficiency gasoline – Particulate emissions 8-hole, gasoline 80° total angle – Engine knock ~15mm – Slow burn rate or partial burn – Heat release control when using compression ignition – Lack of predictive CFD tools ● Barriers for high-efficiency diesel – Particulate emissions 573 K, 3.5 kg/m3 573 K, 3.5 kg/m3 – Heat release rate and phasing – Lack of predictive CFD, particularly for short and multiple injections θ=22.5° I/I0 0.8-1.0 High-speed microscopy at nozzle exit 3 Project -
Improved Solvers for Advanced Engine Combustion Simulation
Lawrence Livermore National Laboratory Improved Solvers for Advanced Engine Combustion Simulation M. J. McNenly (PI), S. M. Aceves, D. L. Flowers, N. J. Killingsworth, G. M. Oxberry, G. Petitpas and R. A. Whitesides Project ID # ACE076 2014 DOE Vehicle Technologies Program Annual Merit Review and Peer Evaluation Meeting June 17, 2014 - Washington, DC This presentation does not contain any proprietary, confidential or otherwise restricted information This work performed under the auspices of the U.S. Department of Energy by LLNL-PRES-653560 Lawrence Livermore National Laboratory under Contract DE-AC52-07NA27344 Overview Timeline Barriers . Ongoing project with yearly . Lack of fundamental knowledge of direction from DOE advanced engine combustion regimes . Lack of modeling capability for combustion and emission control . Lack of effective engine controls Budget Partners . FY12 funding: $340K . Ford, GM, Bosch, Volvo, Cummins, . FY13 funding: $340K Convergent Sciences & NVIDIA . FY14 funding: $475K . Argonne NL, Sandia NL, Oak Ridge NL . UC Berkeley, U. Wisc., U. Mich., LSU, Indiana U. & RWTH Aachen . FACE working group, AEC MOU, SAE, Combustion Inst., GPU Tech. Conf. & NSF HPC software planning Lawrence Livermore National Laboratory McNenly, et al. LLNL-PRES-653560 2 Relevance – Enhanced understanding of HECC requires expensive models that fully couple detailed kinetics with CFD Objective We want to use… Create faster and more accurate Detailed chemistry combustion solvers. Ex. Biodiesel component C20H42 (LLNL) Accelerates R&D on three major 7.2K species challenges identified in the VT multi- 53K reaction steps year program plan: A. Lack of fundamental knowledge in highly resolved 3D simulations of advanced engine combustion regimes C. Lack of modeling capability for combustion and emission control D. -
Large Eddy Simulation of Dispersed Multiphase Flow
Michigan Technological University Digital Commons @ Michigan Tech Dissertations, Master's Theses and Master's Dissertations, Master's Theses and Master's Reports - Open Reports 2012 Large Eddy Simulation of dispersed multiphase flow Yejun Gong Michigan Technological University Follow this and additional works at: https://digitalcommons.mtu.edu/etds Part of the Applied Mathematics Commons, and the Mechanical Engineering Commons Copyright 2012 Yejun Gong Recommended Citation Gong, Yejun, "Large Eddy Simulation of dispersed multiphase flow", Dissertation, Michigan Technological University, 2012. https://doi.org/10.37099/mtu.dc.etds/729 Follow this and additional works at: https://digitalcommons.mtu.edu/etds Part of the Applied Mathematics Commons, and the Mechanical Engineering Commons LARGE EDDY SIMULATION OF DISPERSED MULTIPHASE FLOW By Gong, Yejun A DISSERTATION Submitted in partial fulfillment of the requirements for the degree of DOCTOR OF PHILOSOPHY (Computational Science & Engineering) MICHIGAN TECHNOLOGICAL UNIVERSITY 2012 c 2012 Gong, Yejun This dissertation, "Large Eddy Simulation of Dispersed Multiphase Flow," is hereby ap- proved in partial fulfillment of the requirements for the Degree of DOCTOR OF PHILOS- OPHY IN COMPUTATIONAL SCIENCE & ENGINEERING. Department of Mathematical Science Signatures: Dissertation Advisor Dr. Tanner, Franz X Committee Member Dr. Feigl, Kathleen A Committee Member Dr. Yang, Song Lin Committee Member Dr. Kolkka, Robert W Department Chair Dr. Gockenbach, Mark S Date Dedication "Large Eddy Simulation of Dispersed Multiphase Flow" Ph.D. thesis by Yejun Gong, Dedicated to My parents and teachers and friends and in loving memory of my grandparents! . Contents List of Figures ..................................... xi List of Tables ...................................... xv Acknowledgments ...................................xvii ABBREVIATIONS ..................................xviii Abstract .........................................xxiii 1 Introduction ................................... -
Notes on the Kiva-Ii Software and Chemically Reactive Fluid Mechanics
NOTES ON THE KIVA-II SOFTWARE AND CHEMICALLY REACTIVE FLUID MECHANICS MICHAEL J. HOLST Numerical Mathematics Group Computing & Mathematics Research Division Lawrence Livermore National Laboratory Livermore, California NOTES ON THE KIVA-II SOFTWARE AND CHEMICALLY REACTIVE FLUID MECHANICS∗ Michael J. Holst Numerical Mathematics Group Computing & Mathematics Research Division Lawrence Livermore National Laboratory August 1, 1992 Abstract This report represents a set of working notes regarding the mechanics of chemically reactive fluids with sprays, and their numerical simulation with the KIVA-II software. KIVA-II is a large FORTRAN program developed at Los Alamos National Laboratory for internal combustion engine simulation. It is our hope is that these notes summarize some of the necessary background material in fluid mechanics and combustion, explain the numerical methods currently used in KIVA-II and similar combustion codes, and provide an outline of the overall structure of KIVA-II as a representative combustion program, in order to aid the researcher in the task of implementing KIVA-II or a similar combustion code on a massively parallel computer. The notes are organized into three parts as follows. In Part I, we give a brief intro- duction to continuum mechanics, to fluid mechanics, and to the mechanics of chemically reactive fluids with sprays. In Part II, we take a close look at the governing equations of KIVA-II, and discuss the methods employed in the numerical solution of these equations. We draw some conclusions and make some observations in Part III. ∗These notes were written while the author was visiting Lawrence Livermore National Laboratory during the summer of 1992, on loan from the Numerical Computing Group in the Department of Computer Science at the University of Illinois, Urbana-Champaign. -
Download Article (PDF)
International Conference on Intelligent Control and Computer Application (ICCA 2016) Grid generation research for intake-exhaust closing internal combustion engine using KIVA software Zhao Tianpena Liu Yongfengb*, Shi Yanc Beijing Research Centre of Sustainable Energy and Building Beijing Research Centre of Sustainable Energy and Building Beijing University of Civil Engineering and Architecture Beijing University of Civil Engineering and Architecture Beijing 100044, China Beijing 100044, China [email protected] [email protected], [email protected] Abstract—In order to simulate the combustion process of the of simple blocks. Therefore, the program can calculate very internal combustion engine, a new grid generation was carried. complex geometries. It can not only save the storage space, This paper developed the KIVA-3V software to establish a but also improves the calculation speed. In 1997, KIVA-3V gasoline engine combustion chamber model. Firstly, the which is KIVA-3's improved version was complete. KIVA-3V schematic of grid generation and block of combustion zone is increased oil film flow model, turbulent combustion model given out. The data file (IPREP) and other files are built up, and and soot model. the grid data of gasoline engine combustion chamber is obtained. Secondly, the output files are obtained by running the KIVA-3V. The development of simulation technology in China is Finally, the new three dimensional grids of the intake-exhaust relatively late. Two dimensional simulation is first applied. closing internal combustion engine are obtained. It gives a new The most representative is Professor Wang Rongsheng and way to build up simulation grid for internal engine. Professor Xie Maozhao of Dalian University of Technology. -
The Projection Method Truegrid® Meshes Are Formed More Quickly and Easily Using the Projection Method
Trademarks: are registered trademarks of Dassault Systems. CADDS™ is a trademark and Pro/ENGINEER® is a registered trademark of PTC. ANSYS®, AUTODYN®, and FLUENT® are registered trademarks of ANSYS, Inc. TASCflow® is a registered trademark of Advanced Scientific Computing, Ltd. NASTRAN® is a registered trademark of NASA. MSC NASTRAN® and PATRAN® are registered trademarks MSC.Software Corporation. Solid Edge® is a registered trademark Siemens Corporation. NX is a trademark or registered trademark of Siemens Product Lifecycle Management Software, Inc. LS-DYNA® is a registered trademark Livermore Software Technology Corporation. Windows® is a registered trademark of Microsoft Corporation. SolidWorks® is a registered trademark of Dassault Systems SolidWorks Corporation. SurfCam® CAD/CAM is a registered trademark of Surfware, Inc. Sun® and Solaris® are registered trademarks of Sun Microsystems, Inc. FIDAP™ is a trademark of Fluent, Inc. STAR-CD® is a registered trademark of CD-adapco. Unix® is a registered trademark of X/Open Company Limited. IBM® and AIX™ are trademarks or registered trademarks of IBM Corporation. DEC® is a registered trademark of Hewlett- Packard. CFX is a trademark of Sony Corporation. Intel® and Itanium® are registered trademarks of Intel Corporation. Red Hat® is a registered trademark of Red Hat, Inc. Apple® is a registered trademark of Apple, Inc. AMD™ and Opteron™ are trademarks of Advanced Micro Devices Inc. SUSE™ is a trade mark of NOVELL Inc. LINUX® is a registered trademark owned by Linus Torvalds. All other brand, product, service and feature names or trademarks are the property of their respective owners. The TrueGrid® Advantage TrueGrid® software is advanced meshing technology for FEA and CFD simulation codes. -
NASA Numerical and Experimental Evaluation of UTRC Low Emissions Injector
NASA Numerical and Experimental Evaluation of UTRC Low Emissions Injector Yolanda R. Hicks,1 Sarah A. Tedder,2 Robert C. Anderson,3 and Anthony C. Iannetti4 NASA Glenn Research Center, Cleveland, Ohio, 44135, USA Lance L. Smith5 and Zhongtao Dai6 United Technologies Research Center, East Hartford, CT, 06108, USA Computational and experimental analyses of a PICS—Pilot-In-Can-Swirler technology injector, developed by United Technologies Research Center (UTRC) are presented. NASA has defined technology targets for near term (called “N+1”, circa 2015), midterm (“N+2”, circa 2020) and far term (“N+3”, circa 2030) that specify realistic emissions and fuel efficiency goals for commercial aircraft. This injector has potential for application in an engine to meet the Pratt & Whitney N+3 supersonic cycle goals, or the subsonic N+2 engine cycle goals. Experimental methods were employed to investigate supersonic cruise points as well as select points of the subsonic cycle engine; cruise, approach, and idle with a slightly elevated inlet pressure. Experiments at NASA employed gas analysis and a suite of laser-based measurement techniques to characterize the combustor flow downstream from the PICS dump plane. Optical diagnostics employed for this work included Planar Laser-Induced Fluorescence of fuel for injector spray pattern and Spontaneous Raman Spectroscopy for relative species concentration of fuel and CO2. The work reported here used unheated (liquid) Jet-A fuel for all fuel circuits and cycle conditions. The initial tests performed by UTRC used vaporized Jet-A to simulate the expected supersonic cruise condition, which anticipated using fuel as a heat sink. Using the National Combustion Code a PICS-based combustor was modeled with liquid fuel at the supersonic cruise condition. -
2016 KIVA-Hpfe Development: a Robust and Accurate Engine Modeling Software David Carrington Los Alamos National Laboratory June 7, 2016 3:15 P.M
2016 DOE Merit Review 2016 KIVA-hpFE Development: A Robust and Accurate Engine Modeling Software David Carrington Los Alamos National Laboratory June 7, 2016 3:15 p.m. This presentation does not contain any proprietary, confidential, or otherwise restricted information LA-UR-16-22144 Project ID # ACE014 UNCLASSIFIED Operated by Los Alamos National Security, LLC for the U.S. Department of Energy's NNSA 2016 DOE Overview Merit Review Timeline Barriers . Improve understanding of the fundamentals of fuel injection, fuel-air mixing, thermodynamic . 10/01/09 combustion losses, and in-cylinder combustion/ emission formation processes over a range of . combustion temperature for regimes of interest by 9/31/18 adequate capability to accurately simulate these processes . 85% complete (the last 10% in CFD . Engine efficiency improvement and engine-out development takes the most effort) emissions reduction . Minimization of time and labor to develop engine technology – User friendly (industry friendly) software, robust, accurate, more predictive, & quick meshing Budget Partners • Total project funding to date: • Dr. Jiajia Waters, LANL – 4000K • University of New Mexico- Dr. Juan Heinrich – 705K in FY 16 • University of Purdue, Calumet - Dr. Xiuling Wang – Contractor (Universities) share • Informal collaboration Reactive-Design/ANSYS ~15% • Informal collaboration GridPro Inc. Slide 2 UNCLASSIFIED Operated by Los Alamos National Security, LLC for the U.S. Department of Energy's NNSA Objectives 2016 DOE FY 10 to FY 15 KIVA-Development Merit Review -
Bridging the Gap Between Fundamental Physics And
BridgingBridging thethe GapGap betweenbetween FundamentalFundamental PhysicsPhysics andand ChemistryChemistry andand AppliedApplied ModelsModels forfor HCCIHCCI EnginesEngines Dennis N. Assanis DEER Conference August 20-25, 2005 Chicago, IL HCCI Engine Grand Challenges Physics Experiments Chemical Models Kinetics HCCI Combustion Sensors, Enabling Actuators, Technologies Control Bridging the Gap Between HCCI Fundamentals and Applied Models A University Consortium on Homogeneous Charge Compression Ignition Engine Research - Gasoline University of Michigan Dennis Assanis (PI), Arvind Atreya, Zoran Filipi, Hong Im, George Lavoie, Volker Sick, Margaret Wooldridge Massachusetts Institute of Technology Wai Cheng, William Green Jr., John Heywood Stanford University Tom Bowman, David Davidson, David Golden, Ronald Hanson, Chris Edwards University of California, Berkeley Jyh-Yuan Chen, Robert Dibble, Karl Hedrick HCCI University Consortium Acknowledgements Bridging the Gap Between HCCI Fundamentals and Applied Models Objectives Bridge the gap between fundamental HCCI physics and chemistry considerations and applied models ─ Balance model fidelity with computational expediency and ultimate goal in mind Demonstrate a cascade sequence where high fidelity models and experiments feed phenomenogical models appropriate for systems analysis Apply system models to assess candidate control schemes Multi-Variable RPM Engine Controller Requested Torque IN OUT SIGNALS IN: 1. Coolant temperature sensor 2. "Combustion" sensor : SIGNALS OUT: pressure transducer; or 1. Camless intake valve(s) timing novel SOC probe; or 2. Spark plug for DGI mode ionization probe 3. Fuel injector timing 3. Air mass flow sensor 4. Camless exhaust valve(s) timing 4. Intake manifold temperature sensor 5. EGR control valve 5. Intake manifold pressure sensor 6. Controllable water pump 6. Exhaust manifold temperature sensor 7. Exhaust manifold pressure sensor 8.