Oct. 9, 1962 D
Total Page:16
File Type:pdf, Size:1020Kb
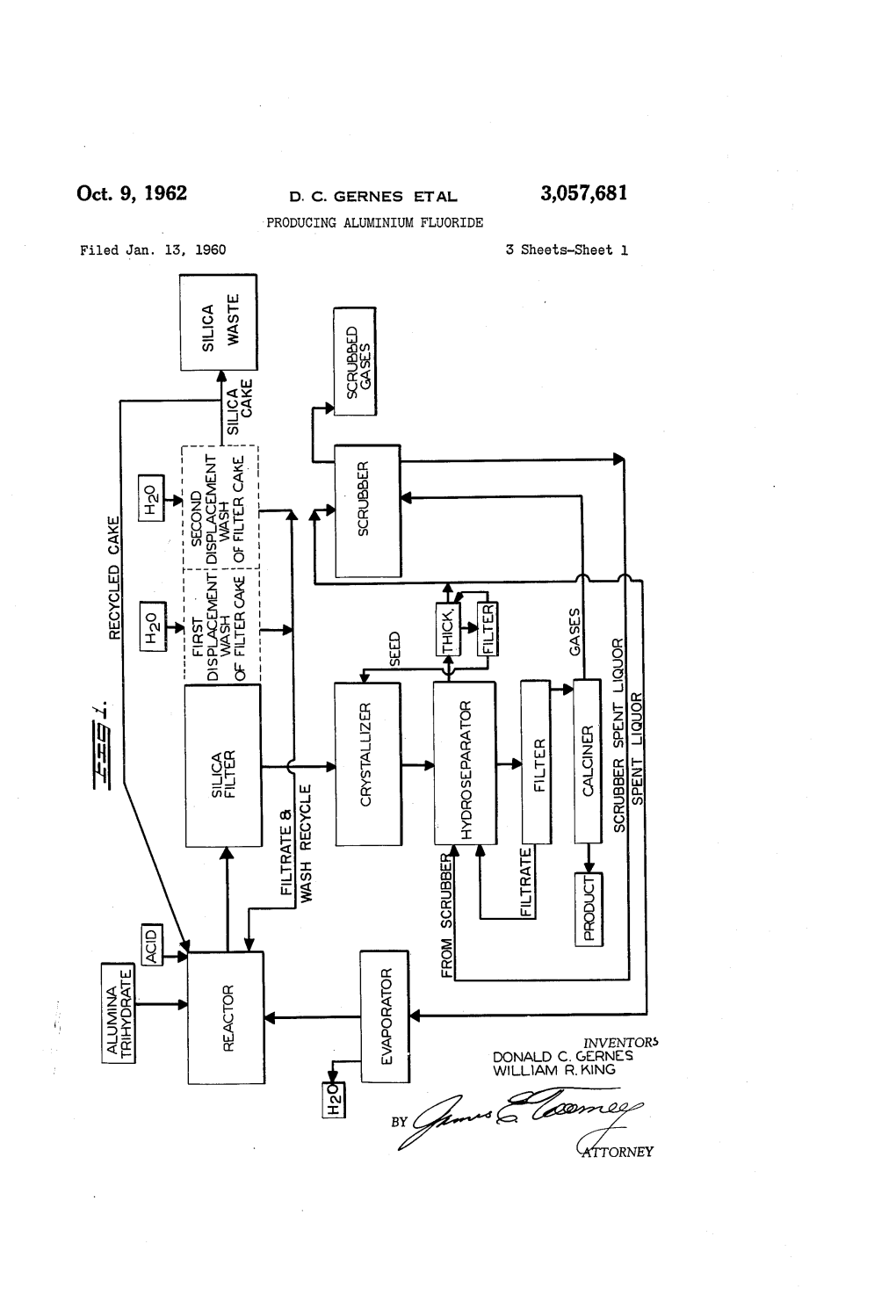
Load more
Recommended publications
-
Trisodium Hexafluoroaluminate Product Stewardship Summary February 2011
Trisodium hexafluoroaluminate Product Stewardship Summary February 2011 Na3AlF6 Chemical Name: Trisodium hexafluoroaluminate Chemical Category (if applicable): Alkali Metal Halide Synonyms: Aluminate (3-), hexafluoro-, trisodium; Aluminium trisodium hexafluoride; Sodium aluminium fluoride; and Sodium hexafluoroaluminate; Icestone; Synthetic cryolite CAS Number: 13775-53-6 CAS Name: Aluminate(3-), hexafluoro-, trisodium, (OC-6-11)- EC (EINECS) Number: 237-410-6 Document Number: GPS0046 V1.0 Trisodium hexafluoroaluminate (synthetic cryolite) is primarily used a flux agent or bath material by aluminum smelters in the production of aluminum. It is also used in the production of synthetic resins for abrasives and in the manufacture of cutting or grinding discs. Minor uses are as a coloring agent (opacifier) in the glass, ceramic and pyrotechnic industries, and as a component of insecticides in the U.S. Exposure can occur at either a synthetic cryolite manufacturing facility or at other manufacturing, packaging or storage facilities that handle synthetic cryolite. Persons involved in maintenance, sampling and testing activities, or in the loading and unloading of synthetic cryolite packages are at risk of exposure, but worker exposure can be controlled with the use of proper general mechanical ventilation and personal protective equipment. Workplace exposure limits for fluoride ion have been established for use in worksite safety programs. When synthetic cryolite is a component of consumer products, users should follow manufacturer’s use and/or label instructions. Synthetic cryolite dusts released to the atmosphere and deposited in soil or surface water in the vicinity of production sites have negligible impact on the environment. Please see the MSDS for additional information. Synthetic cryolite is a nonflammable solid that is stable under normal conditions. -
The Solubility of Aluminium in Melts Containing Aluminium Halides
THE SOLUBILITY OF ALUMINIUM IN MELTS CONTAINING ALUMINIUM HALIDES A Thesis presented for the degree of Doctor of Philosophy in the University of London by John Dyson Usher London, May 1965 ABSTRACT A technique for measuring the solubility of aluminium in NaF-A1F3 and Nall-A1F3+5%A1203 melts has been developed using a refractory titanium boride- carbide crucible and a gas volumetric method of analysis. Experiments were conducted at 10209 1100 and 1180°C; in both systems no change in solubility limit was detected over the experimental composition range of 25.6 - 36.6 and 25.8 - 31.9 mol % AlF3 respectively. The figures in the pure fluoride are 0.022 0.041 and 0.072 wt %; in the alumina melts 0.073, 0.121 and 0.169 wt %. Solution mechanisms have been suggested which account for the observed behaviour, and an attempt has been made to interpret the current inefficiency process in the reduction cell in terms of the results. CONTENTS 1. INTRODUCTION Page 1.1 Aluminium Reduction Cell - Brief Description 1 1.2 Current Efficiency 3 1.2.1 Measurement 3 1.2.2 Cell Variables and Current Efficiency 5 1.2.2 Postulated Mechanisms of Metal Lose 6 1.3 Origins of Present Work 7 1.3.1 Information Required 7 1.3.A Preliminary Theoretical Approach 9 1.4 Metal-Molten Salt Solutions 11 1.4.1 General 11 1.4.2 Nature of Metal-Molten Salt Solutions 16 1.4.3 Extent of Solubility 19 1.4.4 Effect of Foreign Ions on Metal Solubility 23 1.5 Structure of Cryolite and Cryolite-Alumina Melts 25 1.5.1 Pure Molten Cryolite 25 1.5.2 Cryolite-Alumina Melts 33 1.6 Thermodynamics of Aluminium+Cryolite 40 1.6.1 Equilibrium 1.6(i): Experimental 40 1.6.2 Equilibrium 1.6(i): Calculations 42 1.6.3 Equilibrium 1.6(ii) 45 1.7 Previous Experimental Work 46 1.7.1 Analysis by Metal Weight Loss 48 1.7.2 Gas Volumetric Method 52 2. -
The Effect of Various Hydroxide and Salt Additives on the Reduction of Fluoride Ion Mobility in Industrial Waste
sustainability Article The Effect of Various Hydroxide and Salt Additives on the Reduction of Fluoride Ion Mobility in Industrial Waste Tadas Dambrauskas 1,* , Kestutis Baltakys 1, Agne Grineviciene 1 and Valdas Rudelis 2 1 Department of Silicate Technology, Kaunas University of Technology, LT-50270 Kaunas, Lithuania; [email protected] (K.B.); [email protected] (A.G.) 2 JSC “Lifosa”, LT-57502 Kedainiai, Lithuania; [email protected] * Correspondence: [email protected] Abstract: In this work, the influence of various hydroxide and salt additives on the removal of F− ions from silica gel waste, which is obtained during the production of AlF3, was examined. The leaching of the mentioned ions from silica gel waste to the liquid medium was achieved by the application of different techniques: (1) leaching under static conditions; (2) leaching under dynamic conditions by the use of continuous liquid medium flow; and (3) leaching in cycles under dynamic conditions. It was determined that the efficiency of the fluoride removal from this waste depends on the w/s ratio, the leaching conditions, and the additives used. It was proven that it is possible to reduce the concentration of fluorine ions from 10% to <5% by changing the treatment conditions and by adding alkaline compounds. The silica gel obtained after the leaching is a promising silicon dioxide source. Keywords: fluorine ions; silica gel waste; leaching; hydroxide additives Citation: Dambrauskas, T.; Baltakys, K.; Grineviciene, A.; Rudelis, V. The 1. Introduction Effect of Various Hydroxide and Salt Waste management and the reduction of pollution are the priority areas of environ- Additives on the Reduction of mental protection in the World [1–4]. -
Ffinmffiffih$Nry3fhrt
aaourlll q*{Jl}ll ol:f,Ul Arab lnt'|. Organization ,i*If, i*fr* .it*^ Srab Fertilizers ft ssociation Since: L975 flrf*r* ffinmffiffih$nry3Fhrt AFA P FluJsilisic acid: Recovery System and Aluminum Fluoride production Prepared by Eng. Kamal SAMRANE, R&D Direction, OCP Group Eng. Mohammad Al-hjouj - EHS Manager - JPMC Revised by Eng. Faisal Doudin Technical advisor to the Chairman JPMC Dr. Abdelaali KOSSIR R&D Director - OCP Group acid: Recovery Fluosilisic ffiliilrTi roride production l. lntroduction Fluosilisic acid (HrSiFu) is mainly produced as a by-product from the wet process of Phosphoric Acid production from fluorapatite. Phosphate rock always contains fluorine. For F/P2O5 ratios, the fluorine content in rock of sedimentary origin ranges in general from 0.10 to 0.14. Rock of igneous origin shows lower ratios, from 0.04 to 0.006. About 50kg of fluorine (as H2SiF6) per tonne of phosphoric acid (as P2O5) is evolved with the concentration of phosphoric acid in the evaporation step. Currently, most of this evolved fluorine is absorbed into the cooling pond water causing alarge environmental problem.The phosphoric and hydrofluoric acids are liberated from Phosphate rock by the action of sulfuric acid. Some of the HF in turn reacts with silicate minerals, which are an unavoidable constituent of the mineral feedstock, to give silicon tetrafluoride. Thus the formed silicon tetrafluoride reacts further with HF. The net process can be described as: SiO, + 6 HF <-- H2SiF6 + ZH.-O - ------) Neutralization of solutions of fluosilisic acid with alkali metal bases produces the corresponding alkali metal fluorosilicate salts: H2SiF6 + 2 NaOH ) NarSiFu + 2HrO The resulting salt Na2SiF6 is mainly used in water fluoridation. -
Aluminium Fluoride Summary Risk Assessment Report
S421_0803_ENV ALUMINIUM FLUORIDE CAS No: 7784-18-1 EINECS No: 232-051-1 SUMMARY RISK ASSESSMENT REPORT (ENVIRONMENT) Final report, 2008 The Netherlands FINAL APPROVED VERSION Rapporteur for the risk assessment of Aluminiumfluoride is the Ministry of Housing, Spatial Planning and the Environment (VROM) in consultation with the Ministry of Social Affairs and Employment (SZW) and the Ministry of Public Health, Welfare and Sport (VWS). Responsible for the risk evaluation and subsequently for the contents of this report is the rapporteur. Contact point: Bureau REACH P.O. Box 1 3720 BA Bilthoven The Netherlands Date of Last Literature Search: 2004 Review of report by MS Technical Experts finalised: March 2008 Final report: 2008 © European Communities, [ECB: year of publication] PREFACE This report provides a summary, with conclusions, of the risk assessment report of the substance Aluminium fluoride that has been prepared by the Netherlands in the context of Council Regulation (EEC) No. 793/93 on the evaluation and control of existing substances. For detailed information on the risk assessment principles and procedures followed, the underlying data and the literature references the reader is referred to the comprehensive Final Risk Assessment Report (Final RAR) that can be obtained from the European Chemicals Bureau1. The Final RAR should be used for citation purposes rather than this present Summary Report. 1 European Chemicals Bureau – Existing Chemicals – http://ecb.jrc.it III CONTENTS 1 GENERAL SUBSTANCE INFORMATION ............................................................................................ -
United States Patent 19 11 Patent Number: 5,397,375 O'donnell Et Al
USOO5397375A United States Patent 19 11 Patent Number: 5,397,375 O'Donnell et al. (45) Date of Patent: Mar. 14, 1995 54 PROCESS FOR THE PRODUCTION OF 52 U.S.C. ........................................ 75/368; 75/617; METALLICTTANUMAND 75/619 INTERMEDIATES USEFUL IN THE 58) Field of Search .......................... 75/617,619, 368 PROCESSING OF LMENTE AND RELATED MNERALS 56) References Cited 75) Inventors: Thomas A. O'Donnell, Burwood; U.S. PATENT DOCUMENTS John Besida, Yarraville; Tersesa K. 2,647,826 8/1953 Jordan ................................... 75/368 H. Pong, Coburg; David G. Wood, St. 2,986,462 5/1961 Wright .................................. 75/617 Kilda, all of Australia 3,825,415 7/1974 Johnston ............................... 75/619 73 Assignee: The University of Melbourne, 3,847,596 11/1974 Holland ................................. 75/619 Parkville, Australia Primary Examiner-Peter D. Rosenberg 21 Appl. No.:w 107,787 Attorney,Macpeak Agent,& Seas or Firm-Sughrue, Mion, Zinn, 22 PCT Filed: Feb. 21, 1992 57 ABS CT 86 PCT No.: PCT/AU92/00062 The invention relates to a process for the production of S371 Date: Oct. 22, 1993 metallic titanium, characterized in that the process com S 102(e) Date: Oct. 22, 1993 prises reducing a titanium-fluorine compound selected from titanium tetrafluoride and any hexafluorotitanate 87 PCT Pub. No.: WO92/14851 soluble in a molten fluoroaluminate, with metallic alu PCT Pub. Date: Sep. 3, 1992 minum in a molten fluoroaluminate. A process for the 30 Foreign Application Priority Data production of intermediates useful in the processing ilmenite and related minerals is also described. Feb. 21, 1991 AU Australia .............................. PK4721 5ll int. -
Manufacture of Aluminium Fluoride of High Density and Anhydrous Hydrofluoric Acid from Fluosilicic Acid
Available online at www.sciencedirect.com Procedia Engineering 46 ( 2012 ) 255 – 265 1st International Symposium on Innovation and Technology in the Phosphate Industry [SYMPHOS 2011] Manufacture of Aluminium Fluoride of High Density and Anhydrous Hydrofluoric Acid from Fluosilicic Acid Alain Drevetona,* AD Process Strategies Sarl, Rue Chaponnière 9, CH-1201 Geneva, Switzerland Abstract New process technologies are disclosed to manufacture aluminium fluoride of high density and anhydrous hydrofluoric acid starting from fluosilicic acid as raw material which is obtained during acidulation of phosphate rock in the manufacture of phosphatic fertilizers. An overview of the relevant process technologies used commercially to consume this fluosilicic acid is provided in this paper. The new process technologies which shall be implemented to satisfy market demand in fluorochemicals (production of aluminium fluoride of high density from fluosilicic acid and production of anhydrous hydrofluoric acid from fluosilicic acid) and overcome some technical issues as well are described. © 2012 TheThe Authors.Authors. Published Published by by Elsevier Elsevier Ltd. Ltd. Selection Selection and/or and/or peer-review peer-review under under responsibility responsibility of the of theSelection Scientifi and c /or peer-reviewCommittee ofunder SYMPHOS responsibility 2011 of the scientific committee of SYMPHOS 2011. Keywords: aluminium fluoride, hydrofluoric acid, fluorine technology, fluosilicic acid, fluorochemical, silicon tetrafluoride, sodium silicofluoride, -
Safety Data Sheet Acc
Page 1/6 Safety Data Sheet acc. to OSHA HCS Printing date 01/23/2014 Reviewed on 06/26/2013 1 Identification Product identifier Product name: Aluminium fluoride trihydrate Stock number: 11496 CAS Number: 15098-87-0 EC number: 232-051-1 Relevant identified uses of the substance or mixture and uses advised against. No further relevant information available. Identified use: SU24 Scientific research and development Details of the supplier of the safety data sheet Manufacturer/Supplier: Alfa Aesar, A Johnson Matthey Company Johnson Matthey Catalog Company, Inc. 30 Bond Street Ward Hill, MA 01835-8099 Tel: 800-343-0660 Fax: 800-322-4757 Email: [email protected] www.alfa.com Information Department: Health, Safety and Environmental Department Emergency telephone number: During normal hours the Health, Safety and Environmental Department at (800) 343-0660. After normal hours call Carechem 24 at (866) 928-0789. 2 Hazard(s) identification Classification of the substance or mixture Classification according to Regulation (EC) No 1272/2008 GHS06 Skull and crossbones Acute Tox. 3 H301 Toxic if swallowed. GHS07 Skin Irrit. 2 H315 Causes skin irritation. Eye Irrit. 2A H319 Causes serious eye irritation. STOT SE 3 H335 May cause respiratory irritation. Classification according to Directive 67/548/EEC or Directive 1999/45/EC Xn; Harmful R22: Harmful if swallowed. Xi; Irritant R36/37/38: Irritating to eyes, respiratory system and skin. Information concerning particular hazards for human and environment: Not applicable Hazards not otherwise classified No information known. Label elements Labelling according to Regulation (EC) No 1272/2008 The substance is classified and labeled according to the CLP regulation. -
(12) United States Patent (10) Patent No.: US 6,921,519 B2 Draper Et Al
USOO6921519B2 (12) United States Patent (10) Patent No.: US 6,921,519 B2 Draper et al. (45) Date of Patent: Jul. 26, 2005 (54) DECOMPOSITION OF FLUORINE 5,417,948 A 5/1995 Iwata et al. CONTAINING COMPOUNDS 5,649.985. A 7/1997 Imamura ..................... 96/275 5,817.284 A 10/1998 Nakano et al. 5,879,646 A 3/1999 Orihara et al. (75) Inventors: Lee Colin Draper, Flintshire (GB); 6,004,377 A 12/1999 Tamata et al. John David Scott, Cheshire (GB) 6,069,291. A 5/2000 Rossin et al. ............... 588/316 6,077.482 A 6/2000 Kanno et al. (73) Assignee: Ineos Fluor Holdings Limited (GB) 6,110,436 A 8/2000 Scholz et al. (*) Notice: Subject to any disclaimer, the term of this 6,602,480 B1 * 8/2003 Mori ............. ... 423/240 S patent is extended or adjusted under 35 6,673,326 B1 * 1/2004 Rossin et al. ..... ... 423/240 S U.S.C. 154(b) by 49 days. 2001/0001652 A1 5/2001 Kanno et al. ............ 423/240 S (21) Appl. No.: 10/466,997 FOREIGN PATENT DOCUMENTS EP O 885. 648 A1 12/1998 (22) PCT Filed: Jan. 24, 2002 EP O898 999 A2 3/1999 (86) PCT No.: PCT/GB02/00264 EP O 916 388 A2 5/1999 GB 2 295 101 A 5/1996 S371 (c)(1), JP 61. 204025 A 9/1986 (2), (4) Date: Dec. 8, 2003 JP 63 200820 A 8/1988 JP O6 047234 A 2/1994 (87) PCT Pub. No.: WO02/058824 JP O7 39721 A 2/1995 PCT Pub. -
Aluminium Fluoride
Chemicals for all ALUMINIUM FLUORIDE Mainchin Chemicals Group, is one of the leading global supplier of Aluminium Fluoride (AlF3) in both LBD and HBD grades. We are one Stop Shop for Aluminium Fluoride (LBD and HBD). Aluminium Fluoride (AlF3) – LBD and HBD is one of the important key material and used as flux in the production of primary Aluminium metal and manufactured through dry process using Fluorspar and Aluminium Hydrate as a raw material. In this process, high density Aluminium fluoride is produced which is preferred for modern Aluminium smelters in world. This is of critical importance as it lowers electricity consumption during the smelting process. Consequently, primary Aluminium Smelters are the biggest users of Aluminium Fluoride. It is also used in few locations as an additive to Aluminium Metal crucible before entering into the cast house furnaces to reduce alkali metals like Sodium and/or Lithium, and Ceramic industries. Our Aluminium Fluoride can improve the quality of aluminium ingots and reduce production costs because of their high fluorine content and low impurity content. We can supply Aluminium Fluoride as per customers requirement and the product specifications given below for HBD and LBD grade is for reference and further customisation can be possible. Product Description Aluminium Fluoride is colourless solid inorganic compounds with the formula AlF3·xH2O. Other Name : Aluminium Trifluoride, Aluminium Fluoride Anhydrous, Aluminium Fluoride LBD, Aluminium Fluoride HBD Chemical Formula : AlF3 CAS Registry Number -
Safety Data Sheet
SAFETY DATA SHEET 1. Identification Product identifier ALF BLEND Other means of identification Brand Code 005C Recommended use For Industrial Use Only Recommended restrictions None known. Manufacturer/Supplier information Manufacturer Company name HarbisonWalker International Address 1305 Cherrington Parkway, Suite 100 Moon Township, Pennsylvania 15108 US Telephone General Phone: 412-375-6600 Website www.thinkHWI.com Emergency phone number CHEMTREC 24 HOUR 1-800-424-9300 EMERGENCY # 2. Hazard(s) identification Physical hazards Not classified. Health hazards Not classified. Environmental hazards Not classified. OSHA defined hazards Not classified. Label elements Hazard symbol None. Signal word None. Hazard statement The mixture does not meet the criteria for classification. Precautionary statement Prevention Observe good industrial hygiene practices. Response Wash hands after handling. Storage Store away from incompatible materials. Disposal Dispose of waste and residues in accordance with local authority requirements. Hazard(s) not otherwise None known. classified (HNOC) Supplemental information None. 3. Composition/information on ingredients Mixtures Chemical name Common name and synonyms CAS number % Aluminium Oxide (Non-Fibrous) 1344-28-1 40 - 60 TRADE SECRET* Proprietary* 40 - 60 Other components below reportable levels 1 - 2.5 *Designates that a specific chemical identity and/or percentage of composition has been withheld as a trade secret. 4. First-aid measures Inhalation Move to fresh air. Call a physician if symptoms develop or persist. Skin contact Wash off with soap and water. Get medical attention if irritation develops and persists. Eye contact Do not rub eyes. Rinse with water. Get medical attention if irritation develops and persists. Ingestion Rinse mouth. Get medical attention if symptoms occur. -
Synthetic Cryolite Or Sodium Aluminium Fluoride, Trisodium Hexafluoroaluminate
Products List 1. Sodium Cryolite (Synthetic Cryolite or Sodium Aluminium Fluoride, Trisodium Hexafluoroaluminate) 2. Potassium Cryolite (Potassium Aluminium Fluoride or Tripotassium Hexafluoroaluminate) 3. Aluminium Fluoride (Aluminium Trifluoride) 4. Sodium Fluoride 5. Sodium Silico Fluoride ( Sodium fluorosilicate, Disodium Hexafluorosilicate) 6. Sodium BiFluoride 7. Potassium BiFluoride 8. Potassium Fluoride 9. Potassium Titanium Fluoride (Dipotassium Hexafluorotitanate) 10. Potassium Fluoborate (Potassium Tetrafluoroborate) 11. Potassium Zirconium Fluoride (Dipotassium Hexafluorozirconate) 12. Potassium Silico Fluoride (Dipotassium hexafluorosilicate) 13. Magnesium Silico Fluoride 14. Fluotitanic Acid (Hexafluorotitanic acid) 15. Fluozirconic Acid (Hexafluorozirconic acid) 16. Fluoboric Acid (Tetrafluoboric Acid) 17. Lead Fluoborate (Lead Tetrafluoborate) 18. Tin Fluoborate (Stannous Tetrafluoborate) Aluminium Fluoride (Aluminium Trifluoride) SPECIFICATION Name of Product : Aluminium Fluoride, Aluminium Trifluoride Formula : AlF 3 Mol. Wt : 83.97 PHYSICAL PROPERTIES Appearance : Solid, White free flowing crystals Solubility : Insoluble in water Bulk density : 600 - 750 Kg/m3 (Low Bulk Density) pH (1% Aqueous solution) : 3 pH Sieve Analysis +18 BSS (853 µm): Nil +100 BSS (150 µm): 1 % Max +200 BSS (75 µm): 8.0% -200 BSS (75 µm): 92 % CHEMICAL PROPERTIES % AlF3 : 90 – 95 % % Fluorine : 61 % Min. % Aluminium : 30 % % SiO2 : 1.0 % Max % Al2O3 : 6 % Max % P2O5 : 0.05 % Max % H2O : 4 % Max %SO3 : 0.10 % Max % Fe2O3 : 0.08 % Max PACKING