Pre-Feasibility Report
Total Page:16
File Type:pdf, Size:1020Kb
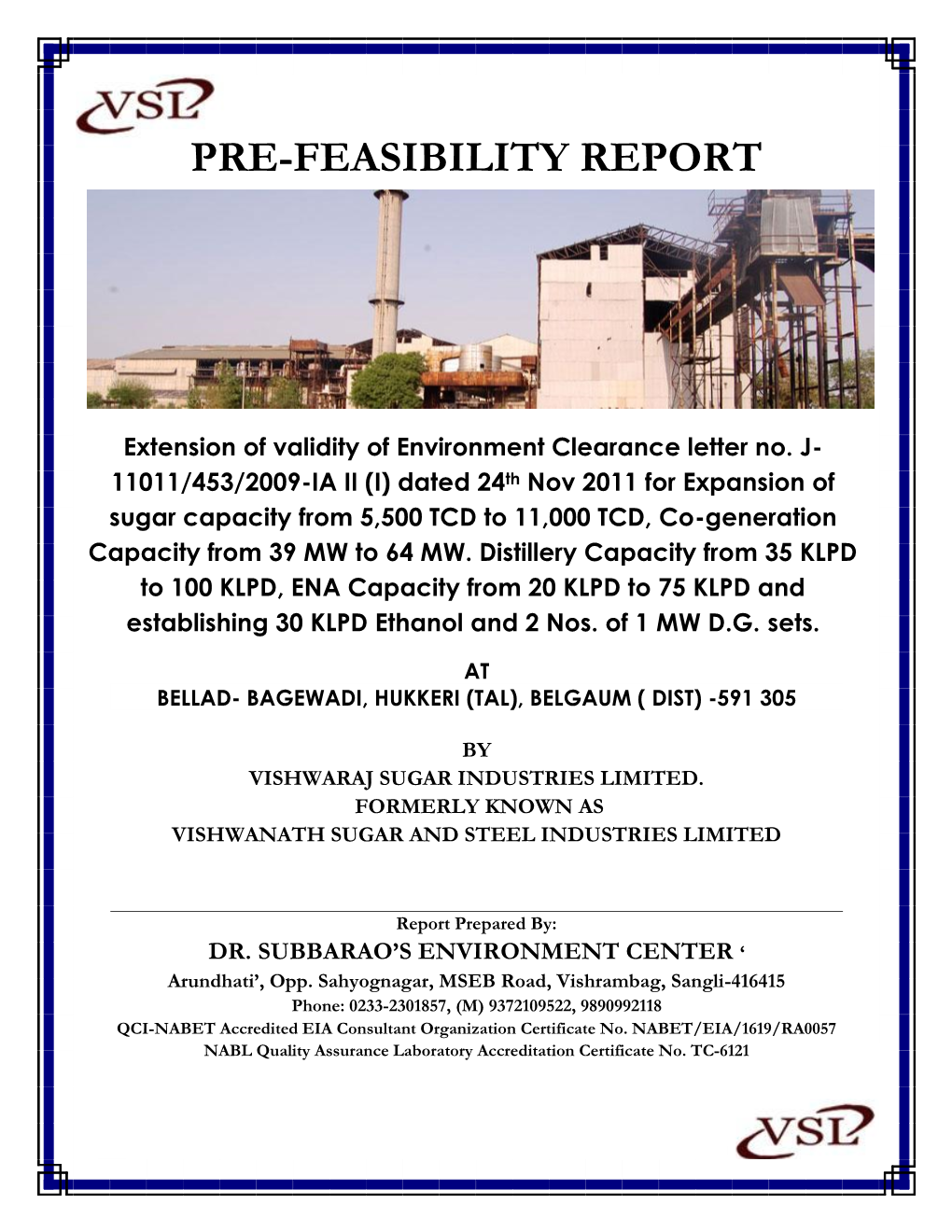
Load more
Recommended publications
-
Prl. District and Session Judge, Belagavi. Sri. Chandrashekhar Mrutyunjaya Joshi PRL
Prl. District and Session Judge, Belagavi. Sri. Chandrashekhar Mrutyunjaya Joshi PRL. DISTRICT AND SESSIONS JUDGE BELAGAVI Cause List Date: 19-12-2020 Sr. No. Case Number Timing/Next Date Party Name Advocate 11.00 AM-02.00 PM 1 SC 122/2018 State of Karnataka R/by P P PP (SUMMONS) Belagavi. Vs S N PATTAR Suvarna alias Shivakka Neelappa Ganagi Age 37 yrs R/o Aralikatti Tq Dt Belagavi. 1/1 Prl. District and Session Judge, Belagavi. Sri. Chandrashekhar Mrutyunjaya Joshi PRL. DISTRICT AND SESSIONS JUDGE BELAGAVI Cause List Date: 19-12-2020 Sr. No. Case Number Timing/Next Date Party Name Advocate 11.00 AM-02.00 PM 1 COMM.O.S 93/2020 The Union Bank of India D.R.Joshi (NOTICE) ,Central Office,Near Forest Office,Bailhonal ,BGV R/by M.A.Kalkut R/o BGV. Vs Sahadev Durgappa Budannavar Age. 42 years R/o Ramapur , Murgod , Saundatti , Belagavi. 2 COMM.O.S 91/2020 VIJAYA BANK now BANK OF A S BALIKAI (SUMMONS) BARODA, Ramdev Galli Branch, Belagavi R/by its Manager Vijay Jambagi Rajesh K. S/o. Madanlal Vs Mr. RAju S/o Rashwanath Magadum, Age 42 yrs, R/o.H.No. 516, Kulkarni Galli, Belagavi 3 COMM.O.S 46/2020 State Bank of India R/by A S BALIKAI (EVIDENCE) Ravindra G Kulkarni age 57 yrs R/o Belagavi Vs Mr. Shashikant Bhimarav Jeerage age 61 yrs R/o H.No.8 Goa road Belagavi LOK ADALATH 4 COMM.O.S 61/2020 The Karnataka Bank Ltd AJAY SUNALKAR, (A.D.R.) Udyambag Belagavi R/by V.B.Vardhamane age 48 yrs R/o B. -
Prl. District and Session Judge, Belagavi. Sri. Chandrashekhar Mrutyunjaya Joshi PRL
Prl. District and Session Judge, Belagavi. Sri. Chandrashekhar Mrutyunjaya Joshi PRL. DISTRICT AND SESSIONS JUDGE BELAGAVI Cause List Date: 22-09-2020 Sr. No. Case Number Timing/Next Date Party Name Advocate 11.00 AM-02.00 PM 1 Crl.Misc. 1405/2020 Gurusidda Shanker Chandaragi Patil A.R. (HEARING) Age 39yrs R/o yattinkeri Tq Kittur Dt Belagavi Vs The State of Karnataka R/by P.P. Belagavi 2 Crl.Misc. 596/2020 Kasimsab Sultansab Nadaf Age. V.S.Karajagi (NOTICE) 33 years R/o Sankeshwar ,Tal. Hukkeri, Belagavi. Vs Salma W/o Kasimsab Nadaf Age. 31 years R/o M.G Colony, Bailhongal, Belagavi. 3 SC 102/2017 State of Karnataka R/by PP SPL.PP (EVIDENCE) Belagavi. Vs Najim Nilawar @ Mahammad Najim Nilawar age 51yrs R/o Bandar Road Batkal Dt Uttar Kannada. 4 SC 141/2019 The State of Karnataka R/by PP, PP (F.D.T.) Belagavi. Vs I Y Chobri Kareppa Basappa Nayik Age. 33 years R/o Budraynoor,Tal.Belagavi. 5 SC 380/2019 The State of Karnataka PP (HBC) Vs Bharmappa alias Bharma Chandru Kurabagatti age 20 yrs R/o Sahyadri colony Jaitun Mal Udyambhag BGV 6 SC 47/2020 The State of Karnataka R/by PP, PP (ISSUE NBW TO Belagavi. ACCUSED) Vs Raj Shravan Londe Age. 21 years R/o Gyangawadi, Shivabasav Nagar, Belagavi. 7 Crl.Misc. 1442/2020 Vaibhav Rajendra Patil Age Shaikh M.M. (OBJECTION) 29yrs R/o Sai Anand Bungalow Sant Gnyaneshwar Nagar, Majagaon Belagavi Vs The State of Karnataka R/by Public Prosecutor Belagavi. 8 Crl.Misc. -
Prl. District and Session Judge, Belagavi. SHRI.G. NANJUNDAIAH II ADDL
Prl. District and Session Judge, Belagavi. SHRI.G. NANJUNDAIAH II ADDL. DISTRICT AND SESSIONS JUDGE BELAGAVI Cause List Date: 25-11-2020 Sr. No. Case Number Timing/Next Date Party Name Advocate 11.00 AM-02.00 PM 1 SPL.C 20/2017 State of Karnataka R/by P P (Summans to accd) Belagavi. Vs Shivakumar Lingayya Hiremath Age 38 yrs R/o Amrut Nagar, Ammingad , Tq Hunagund Dt Bagalkot. 2 SC 107/2019 The State of Karnataka R/by PP, PP (NBW) Belagavi. Vs Mohan Rama Sambrekar Age.41 years R/o H.No. 484 Sarswati Nagar Ganeshpur,Belagavi. 3 SC 170/2019 The State of Karnataka by P.P. (ISSUE NBW TO Market PS ACCUSED) Vs Sharuq Rafiq Shekh Age 19yrs R/o Panji Baba, Shivaji Nagar Dt Belagavi 1/1 Prl. District and Session Judge, Belagavi. SHRI.G. NANJUNDAIAH II ADDL. DISTRICT AND SESSIONS JUDGE BELAGAVI Cause List Date: 25-11-2020 Sr. No. Case Number Timing/Next Date Party Name Advocate 11.00 AM-02.00 PM 1 M.V.C. 1273/2017 Mahaling Hanamant Magadum S R Naragatti (HEARING) age 43 yrs R/o Koligudda Tq Raibag Dt Belagavi Vs Basappa Bhimappa Sanvaganv age 39 yrs, R/o Darur Tq Athani Dt Belagavi 2 M.V.C. 1145/2017 Parasharam Balu Kadolkar Age Shashikant (EVIDENCE) 45 yrs R/o I Cross, Shivaji .R.KAMATE Nagar, Belagavi. Vs Asagar Dastgeer Mulla Nadaf Age major R/o Hattargi village Tq Hukkeri Dt Belagavi. 3 M.V.C. 1274/2017 Chandrabhaga Kedari P S Patil (EVIDENCE) Devalatkar age 35 yrs R/o Kudremani Tq Belagavi Dt Belagavi Vs Bhiku Tukaram Gawade, age major R/o Naganwadi Tq Chandgad Dt Kolhapur 4 M.V.C. -
Saurashtra University Re – Accredited Grade ‘B’ by NAAC (CGPA 2.93)
Saurashtra University Re – Accredited Grade ‘B’ by NAAC (CGPA 2.93) Odedra, Nathabhai K., 2009, “Ethnobotany of Maher Tribe In Porbandar District, Gujarat, India”, thesis PhD, Saurashtra University http://etheses.saurashtrauniversity.edu/id/eprint/604 Copyright and moral rights for this thesis are retained by the author A copy can be downloaded for personal non-commercial research or study, without prior permission or charge. This thesis cannot be reproduced or quoted extensively from without first obtaining permission in writing from the Author. The content must not be changed in any way or sold commercially in any format or medium without the formal permission of the Author When referring to this work, full bibliographic details including the author, title, awarding institution and date of the thesis must be given. Saurashtra University Theses Service http://etheses.saurashtrauniversity.edu [email protected] © The Author ETHNOBOTANY OF MAHER TRIBE IN PORBANDAR DISTRICT, GUJARAT, INDIA A thesis submitted to the SAURASHTRA UNIVERSITY In partial fulfillment for the requirement For the degree of DDDoDoooccccttttoooorrrr ooofofff PPPhPhhhiiiilllloooossssoooopppphhhhyyyy In BBBoBooottttaaaannnnyyyy In faculty of science By NATHABHAI K. ODEDRA Under Supervision of Dr. B. A. JADEJA Lecturer Department of Botany M D Science College, Porbandar - 360575 January + 2009 ETHNOBOTANY OF MAHER TRIBE IN PORBANDAR DISTRICT, GUJARAT, INDIA A thesis submitted to the SAURASHTRA UNIVERSITY In partial fulfillment for the requirement For the degree of DDooooccccttttoooorrrr ooofofff PPPhPhhhiiiilllloooossssoooopppphhhhyyyy In BBoooottttaaaannnnyyyy In faculty of science By NATHABHAI K. ODEDRA Under Supervision of Dr. B. A. JADEJA Lecturer Department of Botany M D Science College, Porbandar - 360575 January + 2009 College Code. -
1995-96 and 1996- Postel Life Insurance Scheme 2988. SHRI
Written Answers 1 .DECEMBER 12. 1996 04 Written Answers (c) if not, the reasons therefor? (b) No, Sir. THE MINISTER OF STATE IN THE MINISTRY OF (c) and (d). Do not arise. RAILWAYS (SHRI SATPAL MAHARAJ) (a) No, Sir. [Translation] (b) Does not arise. (c) Due to operational and resource constraints. Microwave Towers [Translation] 2987 SHRI THAWAR CHAND GEHLOT Will the Minister of COMMUNICATIONS be pleased to state : Construction ofBridge over River Ganga (a) the number of Microwave Towers targated to be set-up in the country during the year 1995-96 and 1996- 2990. SHRI RAMENDRA KUMAR : Will the Minister 97 for providing telephone facilities, State-wise; of RAILWAYS be pleased to state (b) the details of progress achieved upto October, (a) whether there is any proposal to construct a 1906 against above target State-wise; and bridge over river Ganges with a view to link Khagaria and Munger towns; and (c) whether the Government are facing financial crisis in achieving the said target? (b) if so, the details thereof alongwith the time by which construction work is likely to be started and THE MINISTER OF COMMUNICATIONS (SHRI BENI completed? PRASAD VERMA) : (a) to (c). The information is being collected and will be laid on the Table of the House. THE MINISTER OF STATE IN THE MINISTRY OF RAILWAYS (SHRI SATPAL MAHARAJ) : (a) No, Sir. [E nglish] (b) Does not arise. Postel Life Insurance Scheme Railway Tracks between Virar and Dahanu 2988. SHRI VIJAY KUMAR KHANDELWAL : Will the Minister of COMMUNICATIONS be pleased to state: 2991. SHRI SURESH PRABHU -
Village Code NAME of STATE, DISTRICTS, SUB-DISTTS
State District Sub-District Village Code NAME OF STATE, DISTRICTS, SUB-DISTTS. & VILLAGES Code Code Code 2001 29 00 0000 00000000 KARNATAKA 29 01 0000 00000000 Belgaum 29 01 0001 00000000 Chikodi 29 01 0001 00000100 Hadnal 29 01 0001 00000200 Sulagaon 29 01 0001 00000300 Mattiwade 29 01 0001 00000400 Bhatnaganur 29 01 0001 00000500 Kurli 29 01 0001 00000600 Appachiwadi 29 01 0001 00000700 Koganoli 29 01 0001 00000800 Hanabarawadi 29 01 0001 00000900 Hanchinal (K.S.) 29 01 0001 00001000 Benadi 29 01 0001 00001100 Bolewadi 29 01 0001 00001200 Akkol 29 01 0001 00001300 Padlihal 29 01 0001 00001400 Lakhanapur 29 01 0001 00001500 Jatrat 29 01 0001 00001600 Adi 29 01 0001 00001700 Bhivashi 29 01 0001 00001800 Naganur 29 01 0001 00001900 Yamagarni 29 01 0001 00002000 Soundalga 29 01 0001 00002100 Budihal 29 01 0001 00002200 Kodni 29 01 0001 00002300 Gayakanawadi 29 01 0001 00002400 Shirguppi 29 01 0001 00002500 Pangeri (B) 29 01 0001 00002600 Budulmukh 29 01 0001 00002700 Shendur 29 01 0001 00002800 Gondikuppi 29 01 0001 00002900 Yarnal 29 01 0001 00003000 Nippani (Rural) 29 01 0001 00003100 Amalzari 29 01 0001 00003200 Gavan 29 01 0001 00003300 Tavadi 29 01 0001 00003400 Manakapur 29 01 0001 00003500 Kasanal 29 01 0001 00003600 Donewadi 29 01 0001 00003700 Boragaon 29 01 0001 00003800 Boragaonwadi 29 01 0001 00003900 Sadalaga (Rural) 29 01 0001 00004000 Janwad 29 01 0001 00004100 Shiradwad 29 01 0001 00004200 Karadaga 29 01 0001 00004300 Barwad 29 01 0001 00004400 Mangur 29 01 0001 00004500 Kunnur 29 01 0001 00004600 Gajabarwadi 29 01 0001 00004700 Shivapurawadi 29 01 0001 00004800 Bhoj 29 01 0001 00004900 Hunnaragi Page 1 of 1117 State District Sub-District Village Code NAME OF STATE, DISTRICTS, SUB-DISTTS. -
Prl. District and Session Judge, Belagavi. Sri
Prl. District and Session Judge, Belagavi. Sri. Chandrashekhar Mrutyunjaya Joshi PRL. DISTRICT AND SESSIONS JUDGE BELAGAVI Cause List Date: 05-09-2020 Sr. No. Case Number Timing/Next Date Party Name Advocate 11.00 AM-02.00 PM 1 R.A. 64/2020 Sidram Vaijanaik Shivanaikar B.B. (NOTICE) age 40 yrs R/o No. 356 M Block Lakkannavar IA/1/2020 Ramappa nagar Mysore IA/2/2020 Vs Usharani Chandrashekhar Kenganur age 65 yrs R/o Kabbur Tq /Dt Dharwad 2 COMM.O.S 47/2020 Jayashri C Konnur age 42 yrs V.A.chandargi (NOTICE) R/o Laxmi Badawane Gokak Vs Vijay B. Bhutda R/o Wali Shield Products Belagavi 3 COMM.O.S 7/2020 M/s Sairaj Builders and R.B.Deshpande (A.D.R.) Developers 356/1A MG road Tilakwadi Belagavi Vs Govind Mahadev Raut age 77 yrs R/o P.No.2 Swami Vivekanand Colony Tilakwadi Belagavi 4 R.A. 63/2020 Yallappa Balu More age 65 yrs M.M.Shaikh (ARGUMENTS) R/o H.No.5/B Chavat galli IA/1/2020 Kavallawadi Tq /Dt Belagavi IA/2/2020 Vs Appasaheb Tavanappa Desai age 54 yrs R/o H.No.51 Kutalwadi Tq/Dt Belagavi 5 A.S. 16/2019 Shri Bhakti construction Pvt Satish G (Steps) Ltd,R/by R.S.Patil,Eknath Biradar IA/3/2019 Hunnargikar R/o.1809/3,Kelkar IA/1/2019 Bag Belagavi IA/2/2019 Vs Shreemata Co Op Credit Society Ltd (Multi State) O/at. New Goodshed Rd,Belagavi,R/by Umesh S Gavade 6 A.S. -
Government of Karnataka Revenue Village, Habitation Wise
Government of Karnataka O/o Commissioner for Public Instruction, Nrupatunga Road, Bangalore - 560001 RURAL Revenue village, Habitation wise Neighbourhood Schools - 2015 Habitation Name School Code Management Lowest Highest Entry type class class class Habitation code / Ward code School Name Medium Sl.No. District : Chikkodi Block : ATHANI Revenue Village : ATHANI 29300100124 29300100135 Govt. 1 5 Class 1 MOTAGI TOT U.L.P.S MOTGITOT SHIVYOGINAGAR 18 - Urdu 1 29300100124 29300109105 Govt. 1 5 Class 1 MOTAGI TOT K.L.P.S MAHANTESH NAGAR 05 - Kannada 2 29300100124 29300100120 Govt. 1 8 Class 1 MOTAGI TOT K.H.P.S.MOTAGITOT 05 - Kannada 3 Revenue Village : AWARKHOD 29300100201 29300100203 Govt. 1 7 Class 1 LOKUR TOT K.H.P.S LOKUR TOT 05 - Kannada 4 29300100202 29300100201 Govt. 1 8 Class 1 AVARKHOD K.H.P.S.AWARKHOD. 05 - Kannada 5 29300100203 29300100202 Govt. 1 8 Class 1 AWARKHOD TOT K.H.P.S.AWARKHODTOT 05 - Kannada 6 29300100203 29300100205 Pvt Unaided 1 5 LKG AWARKHOD TOT RGASS Primary School Awarkhod Tot 05 - Kannada 7 Revenue Village : ANANTPUR 29300100301 29300100304 Govt. 1 7 Class 1 ANANTAPUR TOT K.H.P.S.ANANTPUR TOT. 05 - Kannada 8 29300100302 29300100306 Govt. 1 7 Class 1 JIRGYAL TOT K.H.P.S.JIRIGYAL TOT. 05 - Kannada 9 29300100303 29300100320 Govt. 1 5 Class 1 CHANDRAPPAWADI K.L.P.S CHANDRAPPA WADI 05 - Kannada 10 29300100304 29300100301 Govt. 1 8 Class 1 ANANTAPUR K.H.P.S.ANANTPUR 05 - Kannada 11 29300100304 29300100303 Govt. 1 8 Class 1 ANANTAPUR U.H.P.S.ANANTPUR 18 - Urdu 12 29300100304 29300100313 Pvt Unaided 1 5 LKG ANANTAPUR K.L.P.S MALLIKARJUN E.SOCIETY 05 - Kannada 13 29300100305 29300100310 Govt. -
Karnataka Name of Graduates' Constituency : Karnataka North West Graduates
Table of Content of Graduates' Constituency of Legislative Council Electoral Roll of the Year 2015 Name Of State: Karnataka Name of Graduates' Constituency : Karnataka North West Graduates DETAILS OF REVISION Year of revision : 2015 Type of revision : Summary Qualifying date : 01-11-2015 Date of publication : 18-01-2016 (a).Name of Graduates' Constituency : Karnataka North West Graduates Karnataka North West Graduates (b).Districts in which the aforesaid Constituency is located : Belgaum,Bagalkot,Bijapur. (c) No. and Name of Assembly Constituency Comprised within the All the Assembly Constituencies in the districts of aforesaid Graduates' Constituency : Belgaum,Bagalkot,Bijapur. TOTAL NO. OF PARTS IN THE CONSTITUENCY : 150. COMPONENTS OF THE ROLL. (A) Mother roll (B) Supplement-1 (C) Supplement-2 NET NUMBER OF ELECTORS : Male Female Others Total 141286 37801 11 179098 Part No : 21 Electoral Rolls,2015 of North West Graduates Constituency of Karnataka Legislative Council District : Belgaum Taluk/Town/City : Gokak Area : Gokak,SugarFactory,Lolsur,Adibatti,Chigadolli,Melavanki,Hadiganal,Kalarkoppa,Udagatti, Maladinni,Bena chinmardi(M),Shingalapur, Sl No Name of the Elector Name of Address (Place of Ordinary Qualification Business Age Sex EPIC Photo of Father/Mother/Husband Residence) Number the elector 1 2 3 4 5 6 7 8 9 10 1 A.Geeta Pandurang hattiholli chawl,gokak B.A 44 F Photo Not Available 2 Sujata Mannapur Jagadeesh 177/3A/2,Vidya nagar gokak, B.E. Employee 41 F TMB1517523 Gokak, 591307 3 Uday Ajari Babaurao 3200,bus stand road gokak, -
Prl. District and Session Judge, Belagavi. Sri. Chandrashekhar Mrutyunjaya Joshi PRL. DISTRICT and SESSIONS JUDGE BELAGAVI Cause List Date: 12-10-2020
Prl. District and Session Judge, Belagavi. Sri. Chandrashekhar Mrutyunjaya Joshi PRL. DISTRICT AND SESSIONS JUDGE BELAGAVI Cause List Date: 12-10-2020 Sr. No. Case Number Timing/Next Date Party Name Advocate 11.00 AM-02.00 PM 1 SC 213/2019 The State of Karnataka R/by PP, Belagavi. PP (EVIDENCE) Vs Shravani Vinod Aralikatti R/o Plot No. 14 B J Gangai Alakapuri,Ramkrishnapurum,Kotapet,Haidrabad. 2 P.C.R. 7/2019 Manisha Ramesh Singh Thakur Age52yrs R/o M.M. SHAIKH (EVIDENCE) B.C No.1 Fort, Belagavi Vs Aashraya Infra Co-Ltd R/by Venkatesh Arjunrao Hishobkar R/o No.322 Roy road Tilakwadi Bgv 3 SC 327/2019 The State of Karnataka by Ramdurg PS PP (HBC) Vs Nagaraj Dyamanna Mali Age 39 yrs R/o Kankanawadi,Tq.Ramdurg,Dt.Belagavi. 4 SPL.C 1118/2019 The State of Karnataka R/by PP, Belagavi. PP (HBC) Vs Maruti Bhimappa Hulloli R/o Shindhikurabet, Tal.Gokak, Dt.Belagavi. 5 SC 21/2020 The State of Karnataka R/by PP, Belagavi. PP (Summans to accd) Vs Nikab @ Nikya Dastageerasab Peerajade Age. 36 years R/o Ashok Nagar, Belagavi. 6 Crl.Misc. 1532/2020 Krushnat @ Pintu S/o Rajaram Ghatage Age SRI. R. C. (OBJECTION) 32Yrs R/o Hanchinal K.S. Tq Nipani Dist INGALGI, Belagavi. Vs The State of karnataka Thorugh PSI Nippani Rural P.S. Nippani, R/by Learned P.P. Belagavi 7 Crl.Misc. 1586/2020 Arun S/o Channvaarayy Hiremath Age 25Yrs R/o Pattar (OBJECTION) Nirmal Nagar, Modaga, Belagavi. Shamsundar N Vs The State of Karnataka R/by P.P. -
District Census Handbook, Belgaum, Part XII-B, Series-11
CENSUS OF INDIA 1991 Series ·11 KARNATAKA DISTRICT CENSUS HANDBOOK BELGAUM DISTIUCf PART XII·B VILLAGE AND TOWN WISE PRIMARY CENSUS ABSTRACT SOBHA NAMBISAN Director or Census Operations, Kamataka CONTENTS • ..ge No. FOREWORD v - vi PREFACE vii-viii IMPORTA..W STATISTICS ix - xii ANALYTICAL NOTE 1 - 37 Explanatory Notes 41 - 44 A. District Primary Census Abstract 46-63 (i) Village/l'own~ Primary Census Abstract Alphabetical List of Villages - Athni C.D.Block 67 - 69 Primary CeQ$us Abstract - Athni C.D.Block 70 - 81 Alphabetical Lis1 of Villages - Belgaum C.D.Block 85-88 Primary Census Abstract - Belgaum C.D.Block 90 - 109 Alphabetical List of Villages - Chikodi CD.Block 113 - 115 P~ Census Abstract - Chikodi C.D.Block 116 - 131 Alphabetical List of Villages - Gokak C.D.Block 135 - 137 Primary Census Abstract - Gokak C.D.Block 138 - 153 Alphabetical List of Villages - Hukeri C.D.Block 157 - 160 Primary Census Abstract - Hukeri C.D.Block 162 - In Alphabetical List of Villages - Kbanapur C.D.Block 181 - 186 Primary Census Abstract - .Kbanapur C.D.Block 188 - 215 Alphabetical List of Villages - Parasgad C.D.Block· 219 - 221 Primary Census Abstract - Parasgad C.D.Block 222 - 237 : . Alphabetical List P~ Villages - R.ybag C.D.Block 241 - 242 Primary CensUs Abstract - Raybag C.D.Block 244 - 251 Alphabetical List of Villages - Ramdurg C.D.Block 255 - 257 Primary Ceqsus Abstract - Ramdurg C.D.Block 258 - 273 i Alphabetical List oLVillages - Sampgaon CD:Block m - '1PIJ Primary Census Abstract -- Sampgaon C.D.Block m - '1!:1T (iii) Page No. (ii) Town Primary Census Abstract (Wardwise) Alphabetic:al List of Towns in the District 301 Athni 302 - 305 Bailhoagal 302 - 303 Chikodi 302 - 305 Dhupdal 302 - 305 Gobk 302 - 305 , Gokak FaDs (NAC) 306 - 309 . -
15 Annual Report 2018-19
Punyashlok Ahilyadevi Holkar Solapur University, Solapur (Former Solapur University, Solapur) NAAC Accredited-2015 ‘B’ Grade (CGPA 2.62) 1155th AAnnnnuuaall RReeppoorrtt 2018-19 (1st July, 2018 to 30th June, 2019) The 15th Annual Report of Punyashlok Ahilyadevi Holkar Solapur University, Solapur providing the information of the work completed during the period from 1st July 2018, to 30th June, 2019. The present report has been prepared as per vide Maharashtra Public Universities, Act 2016, Section 136 (1), under the guidance of the Management Council of Punyashlok Ahilyadevi Holkar Solapur University, Solapur. 1 Publisher Dr. V. B. Ghute Registrar Punyashlok Ahilyadevi Holkar Solapur University, Solapur – 413 255 Annual Report Committee 2018 – 2019 1. Dr. Mahendra Kadam Principal, Vitthalrao Shinde Art’s Mahavidyalaya, Tembhurni Chairman 2. Dr. Prakash Thorat Principal, Shri Shivaji Mahavidyalaya, Barshi Vice-Chairman 3. Dr. Deepak Nanaware Associate Professor, Member D. A.V. Velnkar College of Commerce, Solapur 4. Dr. Suhas Pujari Associate Professor, Sangmeshwar College, Solapur Member 5. Dr. Rajivkumar Mente Assistant Professor, School of Computational Sciences, Member Punyashlok Ahilyadevi Holkar Solapur University, Solapur 6. Mr. Laxman Kadam Member Secretary Section Officer, Statistics Section, Punyashlok Ahilyadevi Holkar Solapur University, Solapur Office Assistance Mr. Mukhtar Shaikh Statistical Assistant Editor & Translator 1. Dr. Deepak Nanaware D. A.V. Velnkar College of Commerce, Solapur 2. Dr. Netaji Kokate Vitthalrao Shinde