Graphene Oxide-Based Membrane for Liquid and Gas
Total Page:16
File Type:pdf, Size:1020Kb
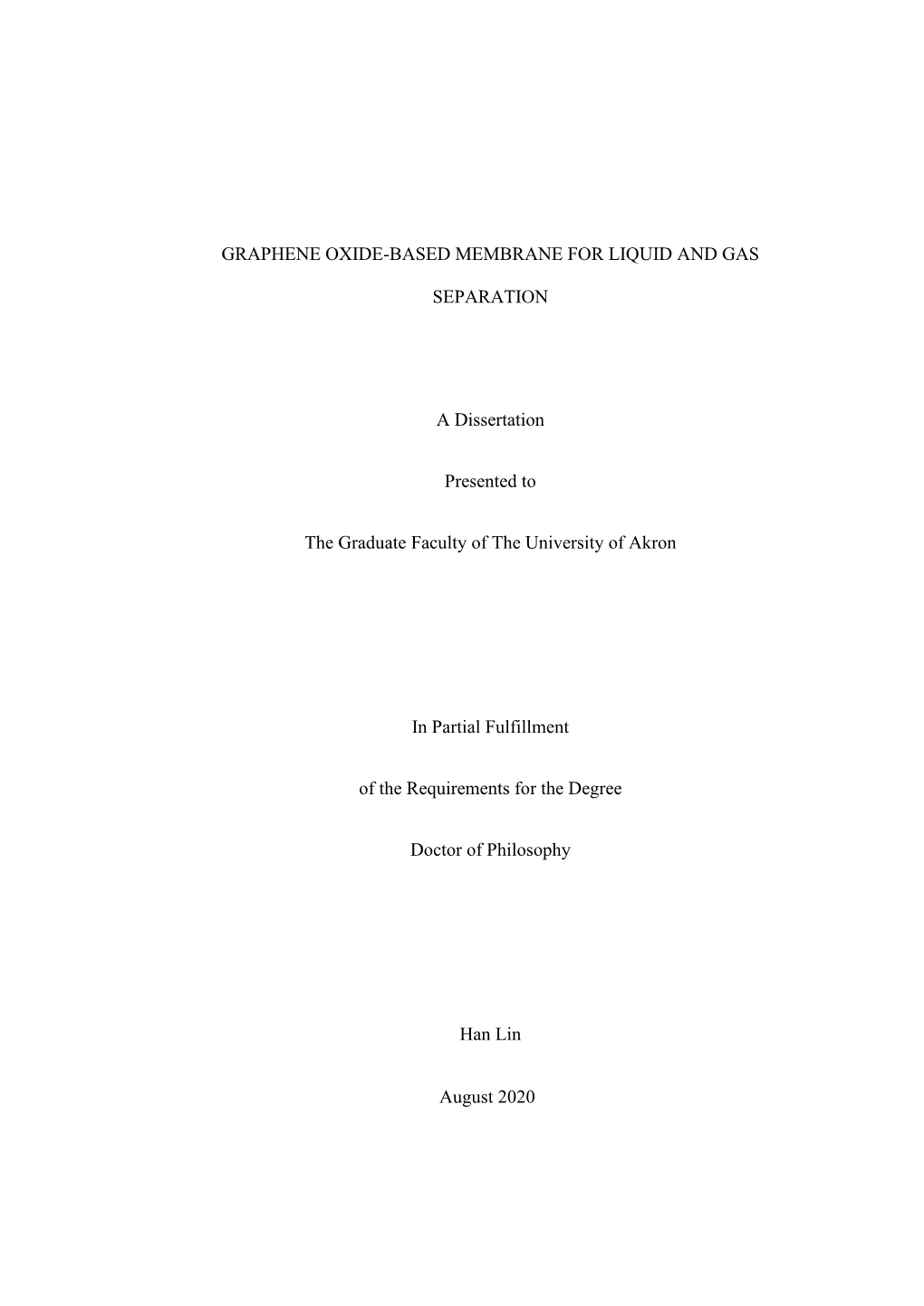
Load more
Recommended publications
-
Free-Standing Graphene Oxide and Carbon Nanotube Hybrid Papers with Enhanced Electrical and Mechanical Performance and Their Synergy in Polymer Laminates
International Journal of Molecular Sciences Article Free-Standing Graphene Oxide and Carbon Nanotube Hybrid Papers with Enhanced Electrical and Mechanical Performance and Their Synergy in Polymer Laminates Manoj Tripathi 1,* , Luca Valentini 2 , Yuanyang Rong 1, Silvia Bittolo Bon 2, 3 4,5,6 3, 3,4 Maria F. Pantano , Giorgio Speranza , Roberto Guarino y , David Novel , Erica Iacob 4, Wei Liu 4, Victor Micheli 4, Alan B. Dalton 1 and Nicola M. Pugno 3,7,* 1 Department of Mathematics and Physical Sciences, University of Sussex, Brighton BN1 9QH, UK; [email protected] (Y.R.); [email protected] (A.B.D.) 2 Department of Civil and Environmental Engineering, University of Perugia and INSTM Research Unit, Strada di Pentima 4, 05100 Terni, Italy; [email protected] (L.V.); [email protected] (S.B.B.) 3 Laboratory of Bio-Inspired, Bionic, Nano, Meta Materials & Mechanics, Department of Civil, Environmental and Mechanical Engineering, University of Trento, via Mesiano 77, 38123 Trento, Italy; [email protected] (M.F.P.); [email protected] (R.G.); [email protected] (D.N.) 4 Centre for Materials and Microsystems, Fondazione Bruno Kessler, via Sommarive 18, 38123 Trento, Italy; [email protected] (G.S.); [email protected] (E.I.); [email protected] (W.L.); [email protected] (V.M.) 5 Department of Industrial Engineering, University of Trento, via Sommarive 9, 38123 Trento, Italy 6 Istituto di Fotonica e Nanotecnologie, IFN-CNR, via alla Cascata 56/C, 38123 Trento, Italy 7 School of Engineering and Materials Science, Queen Mary University of London, Mile End Road, London E1 4NS, UK * Correspondence: [email protected] (M.T.); [email protected] (N.M.P.) Present address: École Polytechnique Fédérale de Lausanne (EPFL), Swiss Plasma Center (SPC), y CH-5232 Villigen PSI, Switzerland. -
Graphite Oxide: Structure, Reduction and Applications
RICE UNIVERSITY Graphite Oxide: Structure, Reduction and Applications by Wei GAO A THESIS SUBMITTED IN PARTIAL FULF'ILLMENT OF THE REQUTREMTNTS F'OR THE DEGREE Doctor of Philosophy dRPROVED, Tt IE,SIS COMM t'ft'EE i - --1.4" i,-',! z'- I'ullickcl M. Ajayan, C-'hair Benjamin M. and Mary Greenwood Anderson Prolessor, Mechanical Enginecring and Material Science & Chemistry 7, 8rr,"2'brt^*, R. Bruce Weisman Prof-essor of Chemistry Enrique V.fBarrera Prof-essor of Mechanical Engineering and Material Science HOUSI'ON, TEXAS March 2012 ABSTRACT Graphite Oxide: Structure, Reduction and Applications by Wei GAO This thesis proposes a modified structure model for graphite oxide (GO), an important precursor in graphene chemistry, develops a new strategy to convert GO back to graphene-like structure, and demonstrates its possible applications in both water purification and supercapacitor technologies. GO, a nontraditional compound first obtained from graphite oxidation over 150 years ago, is now becoming an important player in the production of graphene-based materials, which has high technological relevance. GO structure and reduction have been vigorously investigated, but its precise chemical structure still remains obscure, and the complete restoration of the sp2 carbon lattice has not yet been achieved. In our work, solid state 13C NMR (MAS) analysis offered a piece of evidence for five or six- membered ring lactol structure existing in GO that had never been assigned before, leading to a modified Lerf-Klinowski model for GO. A three-step reduction strategy, involving sodium borohydride (NaBH4), sulfuric acid, and high temperature thermal annealing, described in the thesis, successfully reduced GO back to chemically converted graphene (CCG) with the lowest heteroatom abundance among all those previously reported. -
Physical Properties and Device Applications of Graphene Oxide
Physical properties and device applications of graphene oxide Xiaoming Huang1, Lizhao Liu2,3*, Si Zhou3*, Jijun Zhao3 1School of Ocean Science and Technology, Dalian University of Technology, Panjin 124221, China 2School of Mathematical and Physical Sciences, Dalian University of Technology, Panjin 124221, China 3Key Laboratory of Materials Modification by Laser, Ion and Electron Beams (Dalian University of Technology), Ministry of Education, Dalian 116024, China Graphene oxide (GO), the functionalized graphene with oxygenated groups (mainly epoxy and hydroxyl), has attracted resurgent interests in the past decade owing to its large surface area, superior physical and chemical properties, and easy composition with other materials via surface functional groups. Usually, GO is used as an important raw material for mass production of graphene via reduction. However, under different conditions, the coverage, types, and arrangements of oxygen- containing groups in GO can be varied, which give rise to excellent and controllable physical properties, such as tunable electronic and mechanical properties depending closely on oxidation degree, suppressed thermal conductivity, optical transparency and fluorescence, and nonlinear optical properties. Based on these outstanding properties, many electronic, optical, optoelectronic, and thermoelectric devices with high performance can be achieved on the basis of GO. Here we present a comprehensive review on recent progress of GO, focusing on the atomic structures, fundamental physical properties, and related device applications, including transparent and flexible conductors, field-effect transistors, electrical and optical sensors, fluorescence quenchers, optical limiters and absorbers, surface enhanced Raman scattering detectors, solar cells, light-emitting diodes, and thermal rectifiers. Keywords graphene oxide, mechanics, electronics, thermal properties, nonlinear optics * Corresponding authors. -
Separation and Purification Using GO and R-GO Membranes
RSC Advances View Article Online REVIEW View Journal | View Issue Separation and purification using GO and r-GO membranes Cite this: RSC Adv.,2018,8,23130 J. Lyu,a X. Wen, a U. Kumar, a Y. You,a V. Chen b and R. K. Joshi *a Many materials with varied characteristics have been used for water purification and separation applications. Recently discovered graphene oxide (GO), a two-dimensional derivative of graphene has been considered as a promising membrane material for water purification due to its excellent hydrophilicity, high water permeability, and excellent ionic/molecular separation properties. This review is focussed on the possible versatile applicability of GO membranes. It is also known that selective reduction of GO results in Received 13th April 2018 membranes with a pore size of 0.35 nm, ideally suited for desalination applications. This article Accepted 14th June 2018 presents the applicability of graphene-based membranes for multiple separation applications. This is DOI: 10.1039/c8ra03156h indeed the first review article outlining a comparison of GO and r-GO membranes and discussing the rsc.li/rsc-advances suitability for applications based on the porosity of the membranes. Creative Commons Attribution-NonCommercial 3.0 Unported Licence. 1 Introduction In comparison to ceramic and polymeric membranes, the new class of membranes based on the recently discovered graphene Membrane technology is a separation process which allows oxide (GO) offers superior properties, such as high hydrophilicity, certain species to pass through the membrane while restricting outstanding dispersion in water, nanopores, and excellent the others depending on the properties of the membrane mechanical behaviour.9 Moreover, reduced graphene oxide (r-GO), material. -
Plasma Assisted Reduction of Graphene Oxide Films
nanomaterials Review Plasma Assisted Reduction of Graphene Oxide Films Sri Hari Bharath Vinoth Kumar *, Ruslan Muydinov and Bernd Szyszka Institute of High-Frequency and Semiconductor System Technologies, Technische Universität Berlin, HFT 5-2, Einsteinufer 25, 10587 Berlin, Germany; [email protected] (R.M.); [email protected] (B.S.) * Correspondence: [email protected] Abstract: The past decade has seen enormous efforts in the investigation and development of reduced graphene oxide (GO) and its applications. Reduced graphene oxide (rGO) derived from GO is known to have relatively inferior electronic characteristics when compared to pristine graphene. Yet, it has its significance attributed to high-yield production from inexpensive graphite, ease of fabrication with solution processing, and thus a high potential for large-scale applications and commercialization. Amongst several available approaches for GO reduction, the mature use of plasma technologies is noteworthy. Plasma technologies credited with unique merits are well established in the field of nanotechnology and find applications across several fields. The use of plasma techniques for GO development could speed up the pathway to commercialization. In this report, we review the state-of-the-art status of plasma techniques used for the reduction of GO-films. The strength of various techniques is highlighted with a summary of the main findings in the literature. An analysis is included through the prism of chemistry and plasma physics. Keywords: graphene oxide; plasma treatment; reduction 1. Introduction Citation: Vinoth Kumar, S.H.B.; Muydinov, R.; Szyszka, B. Plasma The term “graphene” was coined by Boehm et al. in 1985, which refers to a two- Assisted Reduction of Graphene dimensional single layer of carbon atoms in a honeycomb lattice [1]. -
Synthesis, Properties and Applications of Graphene Oxide: an Overview
Available online at www.worldscientificnews.com WSN 143 (2020) 17-27 EISSN 2392-2192 Synthesis, properties and applications of graphene oxide: an overview Saswati Nanda*, Atirek Gaur, Rajendra Kumar Duchaniya Department of Metallurgical and Materials Engineering, Malaviya National Institute of Technology, JLN Marg, Jaipur - 302017, India *E-mail address: [email protected] ABSTRACT This paper introduces different methods of synthesis of graphene oxide, properties, and applications of graphene oxide (GO). Unique structural, optical, mechanical, thermal, electrical, barrier properties, excellent biocompatibility Broaden the applications of GO in several fields of science and technology. GO a versatile material is a two-dimensional structure contains oxygen-based functional groups. Hydrophilic nature, Corrosion resistance property of GO makes it a hot area of research in nanocomposite coating fields. Keywords: Graphene Oxide, Brodie’s method, Staudenmaier method, Hummer’s method, Modified Hummer’s method 1. INTRODUCTION Carbon can able to form different allotropes such as Diamond, graphite, buckminsterfullerene, nanotubes, nano buds, and nanoribbons because of its valency. Diamond, graphite, buckminsterfullerene, nanotubes, nanobuds, and nanoribbons are the allotropes of carbon. Diamond and graphene are existing in a solid-state. In diamond, carbon atoms are bonded to form a tetrahedral lattice while in graphite, carbon atoms bonded to form a hexagonal lattice. Because of stable allotropes and its exceptional electronics, carbon can form sp, sp2, sp3 ( Received 08 February 2020; Accepted 23 February 2020; Date of Publication 24 February 2020 ) World Scientific News 143 (2020) 17-27 network. In sp hybridization s orbital overlaps with p orbital to form two new sp orbitals where the ratio of mixing of s and p orbitals are 1:1 (s:p), hence new hybrid orbital has 50 % of s orbital characteristics and 50 % of p orbital characteristics having bond angle 180 degrees. -
Processing Graphene Oxide and Carbon Nanotubes: Routes to Self- Assembly of Designed Architectures for Energy Storage Applications
University of Wollongong Research Online University of Wollongong Thesis Collection 1954-2016 University of Wollongong Thesis Collections 2014 Processing graphene oxide and carbon nanotubes: routes to self- assembly of designed architectures for energy storage applications Seyed Hamed Aboutalebi University of Wollongong Follow this and additional works at: https://ro.uow.edu.au/theses University of Wollongong Copyright Warning You may print or download ONE copy of this document for the purpose of your own research or study. The University does not authorise you to copy, communicate or otherwise make available electronically to any other person any copyright material contained on this site. You are reminded of the following: This work is copyright. Apart from any use permitted under the Copyright Act 1968, no part of this work may be reproduced by any process, nor may any other exclusive right be exercised, without the permission of the author. Copyright owners are entitled to take legal action against persons who infringe their copyright. A reproduction of material that is protected by copyright may be a copyright infringement. A court may impose penalties and award damages in relation to offences and infringements relating to copyright material. Higher penalties may apply, and higher damages may be awarded, for offences and infringements involving the conversion of material into digital or electronic form. Unless otherwise indicated, the views expressed in this thesis are those of the author and do not necessarily represent the views of the University of Wollongong. Recommended Citation Aboutalebi, Seyed Hamed, Processing graphene oxide and carbon nanotubes: routes to self- assembly of designed architectures for energy storage applications, Doctor of Philosophy thesis, Australian Institute for Innovative Materials, University of Wollongong, 2014. -
Graphene and Derivatives – Synthesis Techniques, Properties and Their Energy Applications
City Research Online City, University of London Institutional Repository Citation: Dasari, B. L., Nouri, J. M., Brabazon, D. and Naher, S. (2017). Graphene and derivatives – Synthesis techniques, properties and their energy applications. Energy, 140(1), pp. 766-778. doi: 10.1016/j.energy.2017.08.048 This is the accepted version of the paper. This version of the publication may differ from the final published version. Permanent repository link: https://openaccess.city.ac.uk/id/eprint/18333/ Link to published version: http://dx.doi.org/10.1016/j.energy.2017.08.048 Copyright: City Research Online aims to make research outputs of City, University of London available to a wider audience. Copyright and Moral Rights remain with the author(s) and/or copyright holders. URLs from City Research Online may be freely distributed and linked to. Reuse: Copies of full items can be used for personal research or study, educational, or not-for-profit purposes without prior permission or charge. Provided that the authors, title and full bibliographic details are credited, a hyperlink and/or URL is given for the original metadata page and the content is not changed in any way. City Research Online: http://openaccess.city.ac.uk/ [email protected] *Manuscript Click here to view linked References GRAPHENE and DERIVATIVES - SYNTHESIS TECHNIQUES, PROPERTIES AND THEIR ENERGY APPLICATIONS Bhagya Lakshmi Dasari1, Jamshid M Nouri1, Dermot Brabazon2 and Sumsun Naher1 * 1Department of Mechanical Engineering and Aeronautics, City, University of London, London, UK 2 Advanced Processing Technology Research Centre, School of Mechanical and Manufacturing Engineering, Dublin City University, Dublin, Ireland ABSTRACT 2D nanomaterials with exceptional electrical, mechanical and thermal properties are promising reinforcing materials for fabricating high-performance composite materials. -
A Roadmap to High Quality Chemically Prepared Graphene Régis Y N Gengler, Konstantinos Spyrou, Petra Rudolf
A roadmap to high quality chemically prepared graphene Régis y N Gengler, Konstantinos Spyrou, Petra Rudolf To cite this version: Régis y N Gengler, Konstantinos Spyrou, Petra Rudolf. A roadmap to high quality chemically pre- pared graphene. Journal of Physics D: Applied Physics, IOP Publishing, 2010, 43 (37), pp.374015. 10.1088/0022-3727/43/37/374015. hal-00569706 HAL Id: hal-00569706 https://hal.archives-ouvertes.fr/hal-00569706 Submitted on 25 Feb 2011 HAL is a multi-disciplinary open access L’archive ouverte pluridisciplinaire HAL, est archive for the deposit and dissemination of sci- destinée au dépôt et à la diffusion de documents entific research documents, whether they are pub- scientifiques de niveau recherche, publiés ou non, lished or not. The documents may come from émanant des établissements d’enseignement et de teaching and research institutions in France or recherche français ou étrangers, des laboratoires abroad, or from public or private research centers. publics ou privés. Confidential: not for distribution. Submitted to IOP Publishing for peer review 13 May 2010 A r oadmap to high quality chemically prepared graphene Régis Y.N. Gengler*, Ko nstantinos Spyrou and Petra Rudolf* Zernike Institute for Advanced Materials , University of Groningen, Nijenborgh 4, 9747AG Groningen, The Netherlands. E-mail: [email protected] ; [email protected] Abstract Graphene was discovered half a decade ago and proved the existence of a two -dimensional system which becomes stable as a result of 3D corrugation . I t appeared very quickly that this exceptional material ha d truly outstanding electronic, mechanical, thermal and optical properties . -
Ti3c2tx Mxene-Reduced Graphene Oxide Composite Electrodes for Stretchable Supercapacitors Yihao Zhou, Kathleen Maleski, Babak Anasori, James O
Article www.acsnano.org Ti3C2Tx MXene-Reduced Graphene Oxide Composite Electrodes for Stretchable Supercapacitors Yihao Zhou, Kathleen Maleski, Babak Anasori, James O. Thostenson, Yaokun Pang, Yaying Feng, Kexin Zeng, Charles B. Parker, Stefan Zauscher, Yury Gogotsi, Jeffrey T. Glass,* and Changyong Cao* Cite This: ACS Nano 2020, 14, 3576−3586 Read Online ACCESS Metrics & More Article Recommendations *sı Supporting Information ABSTRACT: The development of stretchable electronics requires the invention of compatible high-performance power sources, such as stretchable supercapacitors and batteries. In this work, two-dimensional (2D) titanium fl carbide (Ti3C2Tx) MXene is being explored for exible and printed energy storage devices by fabrication of a robust, stretchable high-performance supercapacitor with reduced graphene oxide (RGO) to create a composite electrode. The Ti3C2Tx/RGO composite electrode combines the superior electrochemical and mechanical properties of fl Ti3C2Tx and the mechanical robustness of RGO resulting from strong nanosheet interactions, larger nano ake size, fl and mechanical exibility. It is found that the Ti3C2Tx/RGO composite electrodes with 50 wt % RGO incorporated prove to mitigate cracks generated under large strains. The composite electrodes exhibit a large capacitance of 49 mF/cm2 (∼490 F/cm3 and ∼140 F/g) and good electrochemical and mechanical stability when subjected to cyclic uniaxial (300%) or biaxial (200% × 200%) strains. The as-assembled symmetric supercapacitor demonstrates a Downloaded via MICHIGAN STATE UNIV on July 12, 2021 at 19:34:00 (UTC). specific capacitance of 18.6 mF/cm2 (∼90 F/cm3 and ∼29 F/g) and a stretchability of up to 300%. The developed approach offers an alternative strategy to fabricate stretchable MXene-based energy storage devices and can be See https://pubs.acs.org/sharingguidelines for options on how to legitimately share published articles. -
Investigation on the Use of Graphene Oxide As Novel Surfactant To
Kazi et al. Nanoscale Research Letters (2015) 10:212 DOI 10.1186/s11671-015-0882-7 NANO IDEA Open Access Investigation on the use of graphene oxide as novel surfactant to stabilize weakly charged graphene nanoplatelets Salim Newaz Kazi1*, Ahmad Badarudin1, Mohd Nashrul Mohd Zubir1, Huang Nay Ming2, Misni Misran3, Emad Sadeghinezhad1, Mohammad Mehrali4 and Nur Ily Syuhada2 Abstract This paper presents a unique synergistic behavior between a graphene oxide (GO) and graphene nanoplatelet (GnP) composite in an aqueous medium. The results showed that GO stabilized GnP colloid near its isoelectric point and prevented rapid agglomeration and sedimentation. It was considered that a rarely encountered charge-dependent electrostatic interaction between the highly charged GO and weakly charged GnP particles kept GnP suspended at its rapid coagulation and phase separation pH. Sedimentation and transmission electron microscope (TEM) micrograph images revealed the evidence of highly stable colloidal mixtures while zeta potential measurement provided semi-quantitative explanation on the mechanism of stabilization. GnP suspension was confirmed via UV-vis spectral data while contact angle measurement elucidated the close resemblance to an aqueous solution indicating the ability of GO to mediate the flocculation prone GnP colloids. About a tenfold increase in viscosity was recorded at a low shear rate in comparison to an individual GO solution due to a strong interaction manifested between participating colloids. An optimum level of mixing ratio between the two constituents was also obtained. These new findings related to an interaction between charge-based graphitic carbon materials would open new avenues for further exploration on the enhancement of both GO and GnP functionalities particularly in mechanical and electrical domains. -
Detailed Thermal Reduction Analyses of Graphene Oxide Via In-Situ TEM/EELS Studies
Detailed thermal reduction analyses of Graphene Oxide via in-situ TEM/EELS studies M. Pelaez-Fernandez1,2, A. Bermejo1,2, A.M. Benito3, W.K. Maser3, R. Arenal1,2,4* 1Laboratorio de Microscopias Avanzadas (LMA), Universidad de Zaragoza, 50018 Zaragoza, Spain 2Instituto de Nanociencia y Materiales de Aragon (INMA), CSIC-Universidad de Zaragoza, 50009 Zaragoza, Spain 3 Instituto de Carboquimica (ICB-CSIC), 50018 Zaragoza - Spain 4Fundacion ARAID, 50018 Zaragoza, Spain * Corresponding author: Tel: +34 976 762 985, E-mail address: [email protected] Keywords Graphene oxide, reduced graphene oxide, in-situ transmission electron microscopy, thermal reduction. Abstract We report an in-depth study of the reduction of graphene oxide (GO) by in-situ thermal transmission electron microscopy (TEM) analysis. In-situ heating high-resolution TEM (HRTEM) imaging and electron energy-loss spectroscopy (EELS) measurements have been combined to identify the transformations of different oxygen functional groups, the desorption of physisorbed and chemisorbed water and the graphitization as a function of the temperature in the range from 70 up to 1200°C. A model for the general removal of water and OFGs is proposed based on different chemical and physical parameters that have been monitored. All this unique information provides a detailed roadmap of the thermal behaviour of GO at an extended range of temperature. This is not only of interest to understand the thermal reduction process of GO but also of critical relevance to the response of GO in applications when exposed to thermal effects. 1. Introduction Since the first production of isolated graphene in 2004 [1, 2], 2D nanomaterials have experienced unprecedented interest in research, due to their promising mechanical [3], thermal [4], and electrical properties [5, 6, 7].