Modelling and Analysis of a Motorcycle Wheel Rim
Total Page:16
File Type:pdf, Size:1020Kb
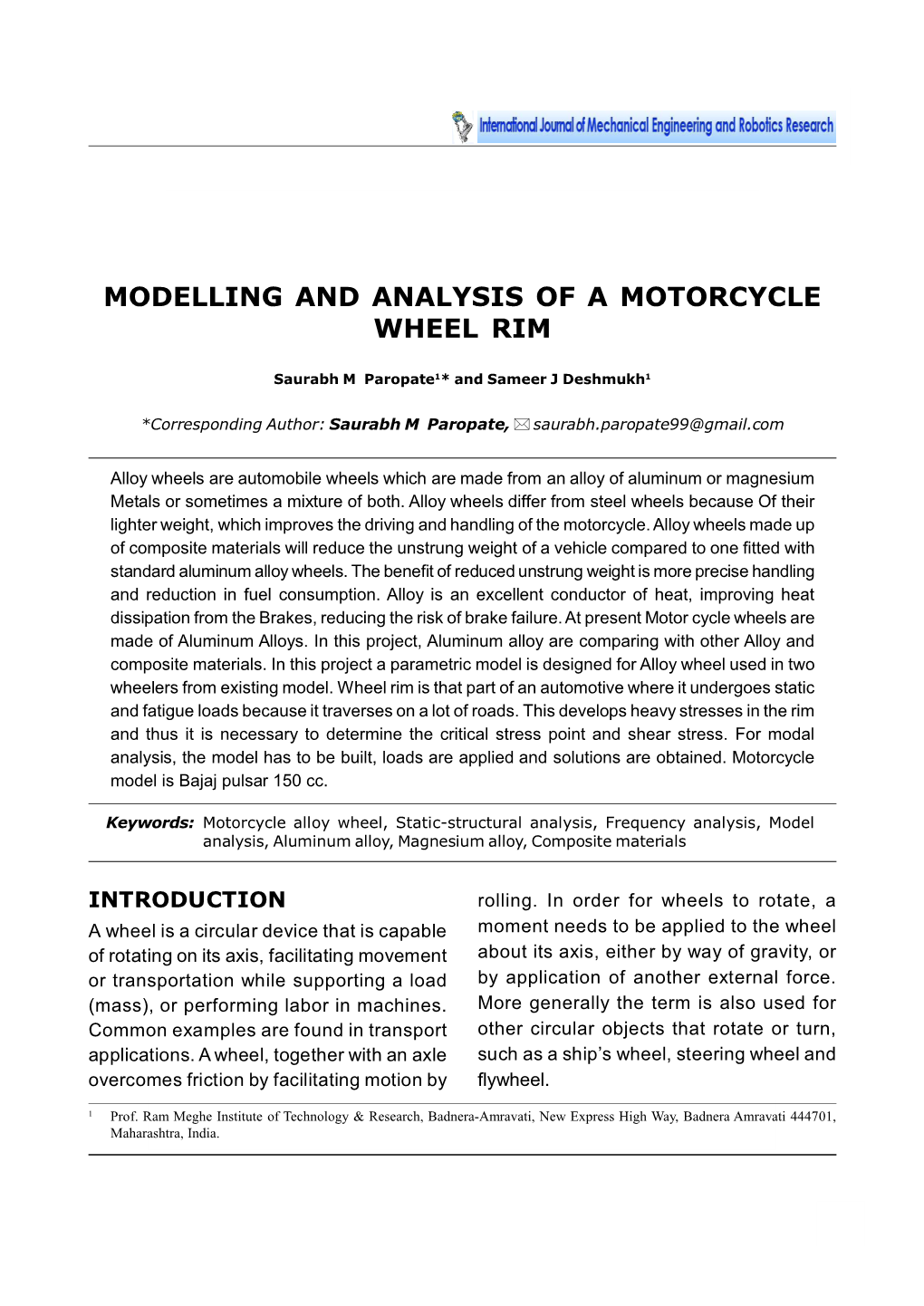
Load more
Recommended publications
-
Bmw R 1200 Gs (04 - 12) / R 1200 Gs Adventure (08 - 13)
Bikegear Motorcycle Accessories for South African bikers SENA 50S MOTORCYCLE INTERCOM HEADSET: SINGLE OR DUAL RIDERS The 50S is Sena's flagship model with a host of industry firsts & legendary jog dial operation . A Single Kit is for 1 Rider A Dual kit is for 1 Rider & 1 Pillion Free Courier delivery. Read More Variations Kits Price Dual R 9,300.00 Single R 5,400.00 Price: R 5,400.00 – R 9,300.00 SENA 50R BLUETOOTH HELMET COMMUNICATION FOR SINGLE OR DUAL RIDERS The 50R is Sena's flagship model with a host of industry firsts . A Single Kit is for 1 Rider supplied with 1 unit & mounting hardware for 1 Helmet. A Dual Kit is for 1 Rider & 1 Pillion supplied with 2 units & mounting hardware for 2 Helmets. Free courier delivery. Read More Variations Kits Price Single R 5,400.00 Dual R 9,300.00 Price: R 5,400.00 – R 9,300.00 Bikegear Motorcycle Accessories for South African bikers SW-MOTECH QUICK-LOCK TANKRING FOR BMW R 1100 GS / R 1150 GS / R 1150 GSA (94 - 04) & R 1200 GS / GSA (04 - 07) Quick-Lock Tankring for BMW 1150 / 1150 / 1150 GSA / 1200 GS 2004 - 2007 by SW-Motech makes mounting Quick-Lock Tankbags a breeze. Read More Price: R 360.00 DESERT FOX EZSLEEP CAMPING BED STRETCHER & LOUNGER An ultralight camping bed designed for rugged use, setting new standards for comfort Read More Price: From: R 1,840.00 12V OFF ROAD AIR COMPRESSOR A compact and VERY powerful 12 V Air Compressor, tailor made for tough off-road conditions. -
2008-2009 Design and Fabrication of a SAE Baja Race Vehicle
2008-2009 Design and Fabrication of a SAE Baja Race Vehicle A Major Qualifying Project Report Submitted to the Faculty of WORCESTER POLYTECHNIC INSTITUTE In partial fulfillment of the requirements for the Degree of Bachelor of Science By: ____________________________ Derek Britton ____________________________ Jessy Cusack ____________________________ Alex Forti ____________________________ Patrick Goodrich ____________________________ Zachary Lagadinos ____________________________ Benjamin Lessard ____________________________ Wayne Partington ____________________________ Ethan Wyman Date: April 29,2009 ____________________________ Kenneth Stafford, Advisor ____________________________ James Van De Ven, Advisor ____________________________ Torbjorn Bergstrom, Advisor 1 Table of Contents List of Figures ..................................................................................................................... 5 List of Tables ...................................................................................................................... 9 Introduction ....................................................................................................................... 10 Design Goals ..................................................................................................................... 11 Chassis .............................................................................................................................. 13 Ergonomics................................................................................................................... -
Optimization of a Motorcycle Wheel Rim Using CAD and CAE Software's
© 2019 JETIR April 2019, Volume 6, Issue 4 www.jetir.org (ISSN-2349-5162) Optimization of a Motorcycle Wheel Rim Using CAD and CAE Software’s Deshabhakt Gavali#1, Harshwardhan Dhumal#2, Niranjan Dindore#3,Parag Betgeri#4, P.H. Lokhande#5 #Department of Mechanical Engineering, Sinhgad College of Engineering, SPPU, Pune-41. Abstract - Wheel Rims form a vital part of two wheeler vehicles. There are two main types of motorcycle rims, namely, Solid Wheels and Spoked Wheels. Solid wheels are the ones in which both the rim and the spokes are manufactured from the same material. While Spoked wheels are the ones in which the motorcycle rim is laced with a number of high tension spokes. This project mainly deals with the optimization of the spoked wheel rim with respect to its weight. The design of the rim is created in a suitable CAD software while, a CAE software is used for analysing the rims for critical conditions. Loading conditions like tyre pressure, radial load and bending load are simulated during the finite element analysis of the component. The geometry of the wheel is optimized until satisfactory results of stress and displacements are obtained. This optimization includes varying the number of spokes and removal of material from the spokes and hub area. ETRTO manual and AIS 073 (Part 2), these standards are referred during the design and analysis stage. Four different models are analysed and compared with each other. The fully optimized model is found to be ’23.587 %’ lighter than the basic design. While it is also found to be safe in all the testing conditions. -
Brakes, Wheel Assemblies, and Tires By
Study Unit Brakes, Wheel Assemblies, and Tires By Ed Abdo About the Author Edward Abdo has been actively involved in the motorcycle and ATV industry for more than 25 years. He received factory training from Honda, Kawasaki, Suzuki, and Yamaha training schools. He has worked as a motorcycle technician, service manager, and Service/Parts department director. After being a chief instructor for several years, Ed is now the Curriculum Development Manager for the Motorcycle Mechanics Institute in Phoenix, Arizona. He is also a contract instructor and administrator for American Honda’s Motorcycle Service Education Department. All terms mentioned in this text that are known to be trademarks or service marks have been appropriately capitalized. Use of a term in this text should not be regarded as affecting the validity of any trademark or service mark. Copyright © 1998 by Thomson Education Direct All rights reserved. No part of the material protected by this copyright may be reproduced or utilized in any form or by any means, electronic or mechanical, including photocopying, recording, or by any information storage and retrieval system, without permission in writing from the copyright owner. Requests for permission to make copies of any part of the work should be mailed to Copyright Permissions, Thomson Education Direct, 925 Oak Street, Scranton, Pennsylvania 18515. Printed in the United States of America Reprinted 2002 iii Preview In this study unit, you’ll learn about the brake systems, wheels, and tires used on motorcycles and ATVs. You’ll begin by learning about the different types of brakes. We’ll describe how each type of brake operates and identify its components. -
Technical Rules Track Racing Règlements Techniques Courses Sur Pistes
TECHNICAL RULES TRACK RACING 2021 RÈGLEMENTS TECHNIQUES COURSES SUR PISTES Technical Rules Track Racing 2021 Règlements Techniques Courses sur Pistes Version 0 Applicable as from 01.01.2021 1 YEAR 2021 Version Applicable as from Modified paragraphs 0 01.01.2021 31.06, 01.38, 47.04, 01.57, 01.63, 01.68, 01.70, 01.76, 25.05 2 Table of contents 01.01 INTRODUCTION ................................................................................................ 5 01.03 FREEDOM OF CONSTRUCTION ...................................................................... 5 01.05 CATEGORY AND GROUPS .............................................................................. 5 01.07 CLASSES ........................................................................................................... 6 01.11 MEASUREMENT OF CAPACITY ....................................................................... 7 01.17 SUPERCHARGING ............................................................................................ 8 01.18 TELEMETRY ...................................................................................................... 8 01.19 MOTORCYCLE WEIGHTS ................................................................................. 8 01.21 DESIGNATION OF MAKE .................................................................................. 9 01.23 DEFINITION OF A PROTOTYPE ....................................................................... 9 01.25 GENERAL SPECIFICATIONS ........................................................................... -
Forged Wheels
Since 1989 RC Components has been recognized as the premier manufacturer of motorcycle wheels serving both the aftermarket and custom bike builder. We continue to grow our dealer base worldwide in more than 36 countries. Our brand is known for innovative wheel designs, quality and un-matched 7 year chrome warranty. All of our products are designed, engineered and manufactured under one roof in Bowling Green, KY. Quality starts on the inside, and because we control the process we control the quality. Our customer service and passion for our products and the industry in which we serve is second to none. We are committed to 100% customer satisfaction with the goal of exceeding our customer’s expectations and will stop at nothing to deliver the finest quality products for the motorcycle enthusiast of today. While most customers have known and seen us for our wheels, many are now hearing us for our RCX exhaust line. We have an extensive product line for Touring, Softail, Dyna, and Sportster applications. If you are looking for the total package, just add one of our Airstrike Air Cleaners and RCX-celerator fuel management systems. Whether you simply want to add some sound or increase your horsepower, we encourage you to check us out. The same enthusiasm and drive for excellence that has made us the leader in motorcycle wheels is the benchmark you can expect from RCX RC Components can now provide our customers with both sound and performance along with great style and design to customize your ultimate riding machine. T A B L E O F forged wheels -
United States Patent (19) 11) 3,982,610 Campagnolo (45) Sept
United States Patent (19) 11) 3,982,610 Campagnolo (45) Sept. 28, 1976 54 CONICAL SHAPED DISC BRAKE FOR A 3,498,417 3/1970 Schmid............................ 88/96 P WEHICLE 3,776,597 2/1973 Camps.................................. 88/26 76 Inventor: Tullio Campagnolo, Corso Padova, 3,858,692 1/1975 Luchier et al.................... 1881 18 A 168, 36100 Vicenza, Italy FOREIGN PATENTS OR APPLICATIONS 22 Filed: Feb. 5, 1975 641,486 8/1950 United Kingdom................ 18817.8 21) Appl. No.: 547,251 Primary Examiner-Stephen G. Kunin Assistant Examiner-Edward R. Kazenske (30) Foreign Application Priority Data Attorney, Agent, or Firm-Young & Thompson Feb. 5, 1974 Italy.................................. 20177/74 June. 7, 1974 Italy.................................. 23719,174 (57) ABSTRACT A disk brake, of the type embodying the brake disk in (52 U.S. Cl................................. 188/18 A; 188/26; the hub of the vehicle wheel and especially a motorcy 188173.2; 188/366; 192/70.15 cle wheel, having: at least one brake disk, the braking 51 Int. Cl.'............................................ B60T 1106 surface of which is a conical surface, which brake disk 58 Field of Search.................. 188/18 R, 18 A, 26, connects the actual hub of the wheel with the spokes 188/71.8, 72.4, 366, 368, 369, 196 P, 73.2; carrying flange of the wheel itself, and at least one 192/70. 15, 85 AA, 85 CA non-rotating brake plate, placed to the side of the hub and provided with friction pads lying on a conical sur 56) References Cited face adapted to engage with the braking surface of the UNITED STATES PATENTS disk, said brake plate being slidable along the wheel 2,102,406 12/1937 Cohen................................, 881366 axis in order to establish or interrupt braking engage 2,364, 83 2/1944 Ash.................................. -
MOTORCYCLE WHEEL Blanks, Hoops & Wheels
MOTORCYCLE WHEEL Blanks, hoops & wheels CATALOGUE 2021 FORGED BLANKS As one of the best material to make motorbike wheels, FORGED blanks is produced from Aluminum 6061 billet, providing free customized wheel design and better mechanical performances. JASTOO makes blanks from 16" to 30" , rim hoops for spoked wheels use, customized design wheels as well as hub parts for most popular motorbike models use. All products are made according to "THE TIRE AND RIM ASSOCIATION" standard. www.jastoowheel.com Blank SIZE CHART 16 " 17 " 18 " 19 " 21 " 23 " 26 " 30 " 1 .85 16 x1 .85 17 x1 .85 18 x1 .85 19 x1 .85 21 x1 .85 23 x1 .85 26 x1 .85 30 x1 .85 2.15 16 x2.15 17 x2.15 18 x2.15 19 x2.15 21 x2.15 23 x2.15 26 x2.15 30 x2.15 2.5 16 x2.5 17 x2.5 18 x2.5 19 x2.5 21 x2.5 23 x2.5 26 x2.5 30 x2.5 2.75 16 x2.75 17 x2.75 18 x2.75 19 x2.75 21 x2.75 23 x2.75 26 x2.75 30 x2.75 3.0 16 x3.0 17 x3.0 18 x3.0 19 x3.0 21 x3.0 23 x3.0 26 x3.0 30 x3.0 3.5 16 x3.5 17 x3.5 18 x3.5 19 x3.5 21 x3.5 23 x3.5 26 x3.5 30 x3.5 3.75 16 x3.75 ▬ 18 x3.75 ▬ 21 x3.75 23 x3.75 26 x3.75 30 x3.75 4.0 16 x4.0 ▬ 18 x4.0 ▬ 21 x4.0 23 x4.0 ▬ 30 x4.0 4.25 16 x4.25 ▬ 18 x4.25 ▬ 21 x4.25 21 x4.25 ▬ ▬ 4.5 16 x4.5 ▬ 18 x4.5 ▬ 21 x4.5 21 x4.5 ▬ ▬ 5.5 16 x5.5 ▬ 18 x5.5 ▬ 21 x5.5 23 x5.5 ▬ ▬ 8.5 ▬ ▬ 18 x8.5 ▬ ▬ ▬ ▬ ▬ 10 .5 ▬ ▬ 18 x10 .5 ▬ ▬ ▬ ▬ ▬ hybrid 2D * all sizes are standard 2D blank design, sizes in red have hybrid blanks www.jastoowheel.com RIM HOOPS JASTOO only provide forged rim hoops for spoked wheels assembly plant. -
Fit and Adjust a Sidecar on Your Motorcycle; Three-Wheeling
How to Fit and Adjust a Sidecar on your Motorcycle; Three-wheeling. D. A. Hobbs About the author Daryl Hobbs has been a qualified motorcycle mechanic for over twenty years. During that time he has patched, tuned, fixed, repaired, reconditioned and restored over 70 makes of motorcycle – of course this number has been assisted by owning over 20 makes. Occasionally he would buy one just because he hadn’t worked on that make or model. As a mechanic, accurate and useful information has always been important and the one area that doesn’t seem to have been catered for that well is information on fitting and adjusting sidecars. The authors baptism into the world of sidecars was attaching a second had box to a Russian made Ural. Aware that he would have to readjust just about everything; the adjustments were left a little loose on ride number one. Unfortunately the first left hand corner was in front of a pub with the usual company assembled on the front verandah. The sidecar, realising there were spectators, took a bow (toward the ground) that veered the outfit into the weeds on the wrong side of the road. If you own an outfit, tighten everything. The second outfit was a safer bet having been securely attached for over 30 years, it was a BSA M21 road painters outfit and very good indeed. The sidecar frame had comparable springing to the bike (not much), a comparable third motorcycle wheel that provides a good rolling and steering ability; you just had to leave a little earlier than everyone else to get places. -
Analysis of Design Modification of Motor Cycle Wheel Spokes A.Anand Swaroop P
Analysis of Design Modification of Motor Cycle Wheel Spokes A.Anand Swaroop P. Satya Lakshmi Department of Mechanical Engineering, Department of Mechanical Engineering, Visakha Technial Campus, Visakha Technial Campus, Andhra Pradesh 530027, India. Andhra Pradesh 530027, India. ABSTRACT suspension. Wheels, and anything directly connected to Spoke is one of some number of rods radiating from them, are considered to be unsprung mass. Traditionally the center of a wheel connecting the hub with the motorcycles used wire-spoked wheels with inner tubes round traction surface. The term originally referred to and pneumatic tyres [1]. Although cast wheels were first portions of a log which had been split lengthwise into used on a motorcycle in 1927, it would not be until the four or six sections. The radial members of a wagon 1970s that mainstream manufacturers would start to wheel were made by carving a spoke into their finished introduce cast wheels on their road going motorcycles. shape. Eventually, the term spoke was more commonly Spoked wheels are usually made using steel spokes with applied to the finished product of the wheelwright's steel or aluminium rims. Cast wheels are predominantly work, than to the materials he used. made from an aluminium-alloy, but can also be made from more-exotic materials, such as magnesium content A double control forming technology of motorcycle alloy or carbon fibre [2]. wheel was firstly developed to form the complex parts with high mechanical properties. The Materials used for alloy wheels AZ91D Magnesium alloy and AM60B alloy are used and compared and while form double control forming. -
(12) Patent Application Publication (10) Pub. No.: US 2006/0048990 A1 Civitell0 (43) Pub
US 200600.48990A1 (19) United States (12) Patent Application Publication (10) Pub. No.: US 2006/0048990 A1 Civitell0 (43) Pub. Date: Mar. 9, 2006 (54) FAT TIRE ASSEMBLY (57) ABSTRACT (76) Inventor: Paul Julio Civitello, Waterbury, CT The purpose of my invention the Fat-Tire Kit is to allow a Shaft-drive motorcycle to have a 300 mm tire mounted on (US) the motorcycle rear wheel. A 250 mm or 280 mm tire could Correspondence Address: also be installed if desired. The rear motorcycle wheel with Paul Julio Civitello the 250 mm, 280 mm or 300 mm tire mounted will remain 35 Harpersferry Rd. in the center of the motorcycle with no off-set, because of Waterbury, CT 06705 (US) my Special Swing-arm with the transmission case incorpo rated into it. My Fat-Tire invention will allow the simple Appl. No.: 10/935,932 installation of a Fat-Tire. The ability to remain in the center (21) of the motorcycle will allow the rider to have the same (22) Filed: Sep. 7, 2004 control of the motorcycle as a factory Stock rear wheel and tire which is in the center of the motorcycle. The Fat-Tire Publication Classification invention is a unique System that allows you to have the capability of having a larger tire mounted on the rear of the (51) Int. Cl. motorcycle that is cosmetically appealing and has Superior B62M 7700 (2006.01) traction while the wheel and tire stay in the center of the (52) U.S. Cl. .............................................................. 180/226 motorcycle where it belongs. Patent Application Publication Mar. -
Frames, Steering, and Suspension By
Study Unit Frames, Steering, and Suspension By Ed Abdo About the Author Edward Abdo has been actively involved in the motorcycle and ATV industry for more than 25 years. He received factory training from Honda, Kawasaki, Suzuki, and Yamaha training schools. He has worked as a motorcycle technician, service manager, and Service/Parts department director. After being a chief instructor for several years, Ed is now the Curriculum Development Manager for the Motorcycle Mechanics Institute in Phoenix, Arizona. He is also a contract instructor and administrator for American Honda’s Motorcycle Service Education Department. All terms mentioned in this text that are known to be trademarks or service marks have been appropriately capitalized. Use of a term in this text should not be regarded as affecting the validity of any trademark or service mark. Copyright © 1998 by Thomson Education Direct All rights reserved. No part of the material protected by this copyright may be reproduced or utilized in any form or by any means, electronic or mechanical, including photocopying, recording, or by any information storage and retrieval system, without permission in writing from the copyright owner. Requests for permission to make copies of any part of the work should be mailed to Copyright Permissions, Thomson Education Direct, 925 Oak Street, Scranton, Pennsylvania 18515. Printed in the United States of America Reprinted 2002 iii Preview This study unit introduces motorcycle and ATV frame design, motorcycle wheel alignment, and front and rear suspension designs. You’ll start by learning the design and description of frames and suspension systems, including motorcycle wheel-alignment checks.