Albright and Wilson Oldbury Works
Total Page:16
File Type:pdf, Size:1020Kb
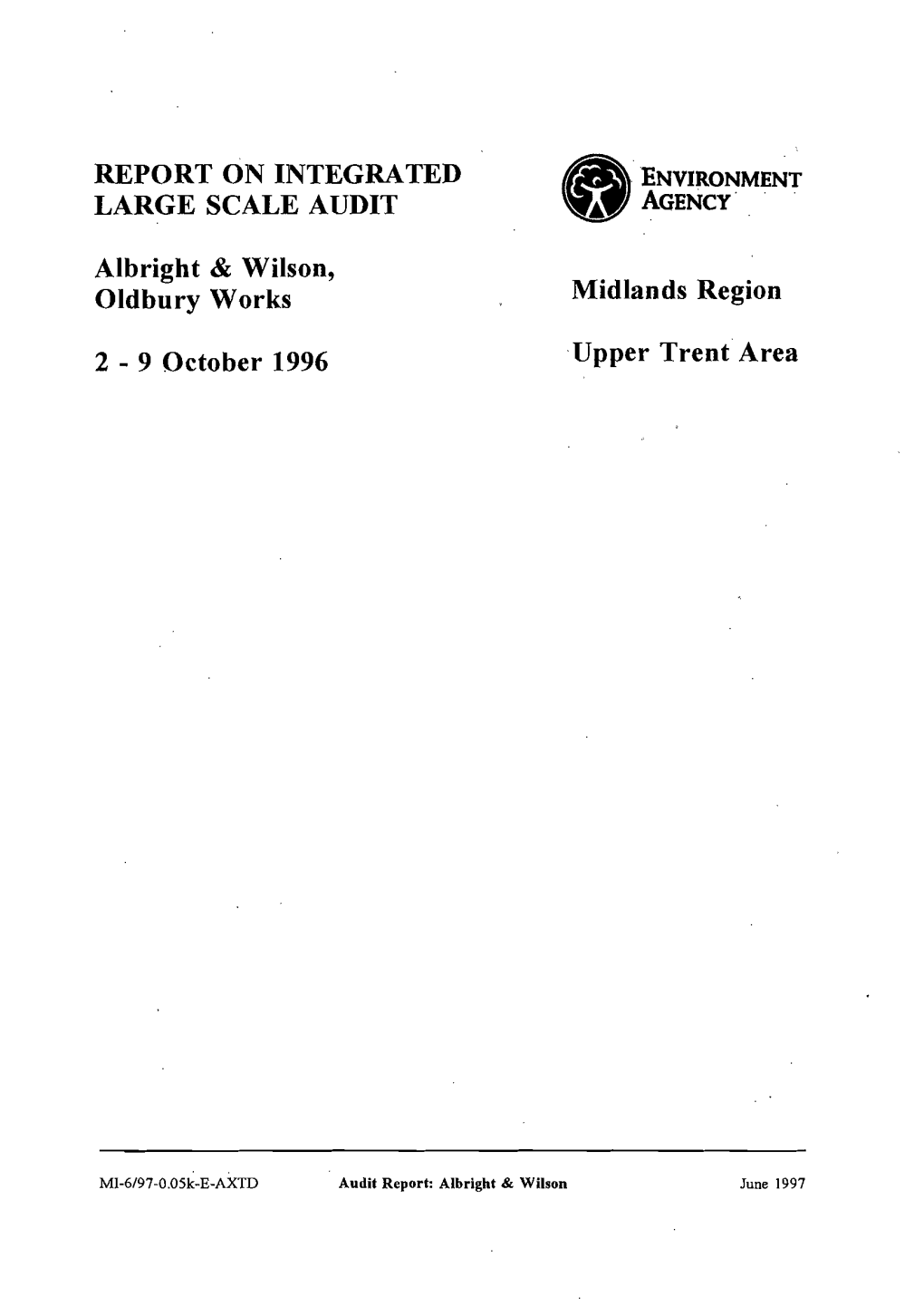
Load more
Recommended publications
-
Application Dossier for the Proposed Black Country Global Geopark
Application Dossier For the Proposed Black Country Global Geopark Page 7 Application Dossier For the Proposed Black Country Global Geopark A5 Application contact person The application contact person is Graham Worton. He can be contacted at the address given below. Dudley Museum and Art Gallery Telephone ; 0044 (0) 1384 815575 St James Road Fax; 0044 (0) 1384 815576 Dudley West Midlands Email; [email protected] England DY1 1HP Web Presence http://www.dudley.gov.uk/see-and-do/museums/dudley-museum-art-gallery/ http://www.blackcountrygeopark.org.uk/ and http://geologymatters.org.uk/ B. Geological Heritage B1 General geological description of the proposed Geopark The Black Country is situated in the centre of England adjacent to the city of Birmingham in the West Midlands (Figure. 1 page 2) .The current proposed geopark headquarters is Dudley Museum and Art Gallery which has the office of the geopark coordinator and hosts spectacular geological collections of local fossils. The geological galleries were opened by Charles Lapworth (founder of the Ordovician System) in 1912 and the museum carries out annual programmes of geological activities, exhibitions and events (see accompanying supporting information disc for additional detail). The museum now hosts a Black Country Geopark Project information point where the latest information about activities in the geopark area and information to support a visit to the geopark can be found. Figure. 7 A view across Stone Street Square Dudley to the Geopark Headquarters at Dudley Museum and Art Gallery For its size, the Black Country has some of the most diverse geology anywhere in the world. -
Environment Agency Plan
g A . \m a d la M>S ce?vfs- ?ox local environment agency plan WEST MIDLANDS-TAME CONSULTATION REPORT MARCH 1998 Brownhills Tamworth Wolverhampton Aldridge Sutton Coldfield Atherst Kingsbury West Bromwich Nuneaton Birrplngham Fillongley Meriden C oven Solihull B alsall Common Dorridge En v ir o n m e n t Agency Your Views What is this report about? This report is about the environment of Birmingham, Solihull, much of the Black Country and parts of Warwickshire, what we call the West Midlands - Tame area. It is all the land that drains to the River Tame up to Kingsbury, just upstream of the River Purification Lakes at Lea Marston. The report looks at the physical environment of land, air, water, wildlife and heritage. It highlights the current quality of the environment, the natural resources of the area and how they can be protected. It also identifies specific environmental problems in the area and how they can be tackled. Why should I read it? The Environment Agency wants to hear your views on the issues facing the environment of the area and what you think should be done about them. Telling us your views will enable you to contribute to environmental protection and improvement and influence what the Environment Agency and others do. We will be pleased to receive any comments that you wish to make but in particular we are very keen to know: o what you think should be done about them? o how important do you think the issues are? o What you think of our proposals? o are there problems or opportunities that we have not included? o whether you can help to tackle any of the issues. -
Albright of Charlbury
Descendants of William Albright Charles E. G. Pease Pennyghael Isle of Mull Descendants of William Albright 1-William Albright William married Mary. They had one son: William. 2-William Albright,1 son of William Albright1 and Mary1, was born on 31 Dec 1745 in Woburn and died on 2 Nov 1820 in Charlbury, Oxfordshire at age 74. Noted events in his life were: • He worked as a Draper of Charlbury. William married Rachel Marshall, daughter of Nicholas Marshall and Priscilla. They had three children: William, Mary, and Nicholas. 3-William Albright1,2,3,4,5,6 was born on 11 Oct 1776 in Charlbury, Oxfordshire and died on 27 Jun 1852 in Charlbury, Oxfordshire at age 75. Noted events in his life were: • He worked as a Grocer, Draper & Glovemaker in Charlbury, Oxfordshire. • He worked as a Quaker Elder. William married Rachel Tanner,1,2,3,5,6 daughter of William Tanner1,5 and Hannah Curtis, in 1801. Rachel was born in 1776 and died on 26 Jul 1867 in Charlbury, Oxfordshire at age 91. They had nine children: Mary, William Tanner, Lydia, Joseph, Arthur, Hannah, John Marshall, Rachel, and Francis. Noted events in her life were: • She worked as a Quaker Elder. • Miscellaneous: Helped her husband establish the British School at Charlbury, 1815. 4-Mary Albright was born on 24 Sep 1803 in Charlbury, Oxfordshire and died on 29 Jan 1876 in Charlbury, Oxfordshire at age 72. Mary married William Pollard,7 son of Samuel Pollard7,8 and Catherine Hughesdon,7 on 12 Jul 1849 in FMH Charlbury. William was born on 20 Feb 1794 in Horsham, West Sussex and died on 9 Jan 1878 in Charlbury, Oxfordshire at age 83. -
How to Make Phosphorus
How to Make Phosphorus Phosphorous was invented by accident by alchemist Hennig Brandt In 1669, while trying to make a philosopher's stone (a mythical substance which could turn base metal into gold).Since the time of Brandt, newer methods for producing phosphorus have been discovered, but they require much higher temperatures and more sophisticated equipment than the average individual possesses. This article will describe how to make phosphorous the old-fashioned way. Things You'll Need • Urine • Charcoal dust • Cinnamon powder Glass retortGlass containerWaterEye protectionBreathing maskGlovesButane torchTripod for glass retortShow (8) More Instructions 1. How to Make Phosphorus o 1 Allow urine to sit in an open container for 7 days. o 2 Mix two tablespoons of finely-powdered charcoal and two tablespoons of powdered cinnamon into the urine and stir. o 3 Pour the urine/charcoal dust and cinnamon mixture into a glass retort with a glass tube leading into a second beaker filled with plain water. o 4 Heat the retort containing the urine mixture using your torch. Be sure to wear protective clothing, eye protection and a breathing mask. o 5 Allow the vapors from the urine mixture to bubble through the plain water. A yellow or white waxy substance will collect in the bottom of your water beaker. This is phosphorous. Do not expose it to the air or it may ignite spontaneously. After being exposed to light your phosphorous should glow very brightly in the dark for several hours. Tips & Warnings • Over time your white phosphorous will change into a red phosphorous if left in your water-filled beaker. -
Nicholas Burton Richard Turnbull Editors
CSR, Sustainability, Ethics & Governance Series Editors: Samuel O. Idowu · René Schmidpeter Nicholas Burton Richard Turnbull Editors Quakers, Business and Corporate Responsibility Lessons and Cases for Responsible Management CSR, Sustainability, Ethics & Governance Series editors Samuel O. Idowu, London Metropolitan University, London, United Kingdom René Schmidpeter, Cologne Business School, Cologne, Germany More information about this series at http://www.springer.com/series/11565 Nicholas Burton • Richard Turnbull Editors Quakers, Business and Corporate Responsibility Lessons and Cases for Responsible Management Editors Nicholas Burton Richard Turnbull Newcastle Business School Centre of Markets, Enterprise & Ethics Northumbria University Oxford, UK Newcastle, UK ISSN 2196-7075 ISSN 2196-7083 (electronic) CSR, Sustainability, Ethics & Governance ISBN 978-3-030-04033-8 ISBN 978-3-030-04034-5 (eBook) https://doi.org/10.1007/978-3-030-04034-5 Library of Congress Control Number: 2018966594 © Springer Nature Switzerland AG 2019 This work is subject to copyright. All rights are reserved by the Publisher, whether the whole or part of the material is concerned, specifically the rights of translation, reprinting, reuse of illustrations, recitation, broadcasting, reproduction on microfilms or in any other physical way, and transmission or information storage and retrieval, electronic adaptation, computer software, or by similar or dissimilar methodology now known or hereafter developed. The use of general descriptive names, registered names, trademarks, service marks, etc. in this publication does not imply, even in the absence of a specific statement, that such names are exempt from the relevant protective laws and regulations and therefore free for general use. The publisher, the authors and the editors are safe to assume that the advice and information in this book are believed to be true and accurate at the date of publication. -
Flame Retardants: Tris(2-Butoxyethyl) Phosphate, Tris(2-Ethylhexyl) Phosphate and Tetrakis(Hydroxymethyl) Phosphonium Salts
This report contains the collective views of an international group of experts and does not necessarily represent the decisions or the stated policy of the United Nations Environment Programme, the International Labour Organisation, or the World Health Organization. Environmental Health Criteria 218 FLAME RETARDANTS: TRIS(2-BUTOXYETHYL) PHOSPHATE, TRIS(2-ETHYLHEXYL) PHOSPHATE AND TETRAKIS(HYDROXYMETHYL) PHOSPHONIUM SALTS Please note that the layout and pagination of this web version are not identical with the printed document First draft prepared by Dr G.J. van Esch, Bilthoven, the Netherlands Published under the joint sponsorship of the United Nations Environment Programme, the International Labour Organisation, and the World Health Organization, and produced within the framework of the Inter-Organization Programme for the Sound Management of Chemicals. World Health Organization Geneva, 2000 The International Programme on Chemical Safety (IPCS), established in 1980, is a joint venture of the United Nations Environment Programme (UNEP), the International Labour Organisation (ILO), and the World Health Organization (WHO). The overall objectives of the IPCS are to establish the scientific basis for assessment of the risk to human health and the environment from exposure to chemicals, through international peer review processes, as a prerequisite for the promotion of chemical safety, and to provide technical assistance in strengthening national capacities for the sound management of chemicals. The Inter-Organization Programme for the Sound Management of Chemicals (IOMC) was established in 1995 by UNEP, ILO, the Food and Agriculture Organization of the United Nations, WHO, the United Nations Industrial Development Organization, the United Nations Institute for Training and Research, and the Organisation for Economic Co-operation and Development (Participating Organizations), following recommendations made by the 1992 UN Conference on Environment and Development to strengthen cooperation and increase coordination in the field of chemical safety. -
5. Transport and Accessibility
5. TRANSPORT AND ACCESSIBILITY TRAN1 Priorities for the Development of the Transport Network Spatial Objectives The delivery of an improved and integrated transport network both within the Black Country and in links with regional and national networks is fundamental to achieving the Vision (p18) and in helping to transform the area, deliver housing growth and improve economic performance, and achieving Spatial Objective 7 (p20). Policy The development of transport networks in the Black Country is focused on a step change in public transport provision serving and linking centres, improving sustainable transport facilities and services across the area, improving connectivity to national networks and improving the efficiency of strategic highway routes. Land needed for the implementation of priority transport projects will be safeguarded in order to assist in their future implementation. All new developments will address the transport network and provide adequate access for all modes, including walking, cycling and public transport. Residential development will be expected to meet the accessibility standards set out in Policy HOU2. Given uncertainty over the availability of future funding for major transport infrastructure over the longer term, continuing priority will be given to improving transport in key corridors through the roll out of the Smarter Routes initiative that embraces a range of techniques for improving public transport, traffic management (including localised junction improvements), road safety and facilities for cyclists -
Edition 209 Summer 2015
Boundary Edition 209 Summer Post 2015 Daniel Penn is one of the latest volunteers to crew Atlas & Malus. At 13 years of age he is also the youngest. We are so keen to encourage such young people to share an interest in the boats and in the canal in general. We look forward to seeing Daniel along with his Dad Jon enjoying this experience. Photo Jon Penn The Journal of the Birmingham Canal Navigations Society Free to members 50p when sold bcnsociety.com Boundary Post Summer2015 Edition 209 Boundary Post Summer 2015 Edition 209 Council Members - 2014 - 2015 President : Martin O’Keeffe Vice-Presidents: Ron Cousens, Phil Clayton, Cllr. David Sparks, Rob Starkey, Chairman & web man: Press & Publicity: CHARLEY JOHNSTON 07825816623 Kath O’’Keeffe [email protected] [email protected] Vice Chair & Rally Organiser Press & Publicity Assistant BARRIE JOHNSON 0121 422 4373 Martin O’Keeffe [email protected] [email protected] Treasurer: Sales: DAVE DENT REBECCA SMITH KEARY 38 Greenland Mews, London, SE8 5JW [email protected] 01562 850234 020 8691 9190 [email protected] Health & Safety Secretary: & Planning Officer ARTHUR FARGE tel: 0121 745 4266 IVOR CAPLAN email: [email protected] tel: 07778685764 [email protected] Supporting members to Council Membership ALAN VENESS tel: 0121 355 4732 Talks and Presentations 43 Pilkington Ave, Sutton Coldfield, B72 PHIL CLAYTON 07890921413 1LA email: [email protected] [email protected] Work Party Co-ordinator: Work Party Administrator MIKE ROLFE 07763 171735 Michael -
Professor Stanley Greenfield Cchem FRSC
Professor Stanley Greenfield CChem FRSC 25 March 1920 - 4 September 2019 Professor Stanley Greenfield, a Past President of the Analytical Division, died on 4 September 2019: he was in his 100th year, having been born in Walsall on 25 March 1920. His father died when he was quite young, and he left school at 14 to take a variety of jobs before starting work in the laboratories of Stewarts and Lloyds at the large Bilston steelworks in 1938. He also enrolled at Wednesbury Technical College to study metallurgy. Day release for this purpose was not available in those days, so Stan had to combine arduous shift work at the steelworks (and, on the outbreak of war, membership of a medical rescue team there) with study at home and at weekends - by no means an easy life. After studying metallurgy for four years, winning some student prizes and becoming a Licentiate of the Institute of Metallurgists, he turned his enthusiasm to chemistry, with further classes at technical colleges in Wolverhampton and Birmingham. He remained in the steel industry for 13 years, finishing at the GKN Group Research Laboratories: in his role as a Research Officer there he gained experience of a wide variety of analytical methods. In 1951 Stan moved to Albright and Wilson to begin his long and remarkable association with that company. He started in the Phosphorus Development Department, looking at all aspects of phosphorus manufacture: he later published in conjunction with Martin Clift the book Analytical Chemistry of the Condensed Phosphates. This was a varied and interesting field, but it was when he moved a few years later to the Research Department as the leader of the Analytical Group that his most important work began. -
Matches-The Manufacture of Fire Jaime Wisniak Department of Chemical Engineering, Ben-Gurion University of the Negev, Beer-Sheva, Israel 84105
Indian Journal of Chemical Technology Vol. 12, May 2005, pp. 369-380 Matches-The manufacture of fire Jaime Wisniak Department of Chemical Engineering, Ben-Gurion University of the Negev, Beer-Sheva, Israel 84105 The phosphorus match represents the culmination of the efforts to manufacture fire by friction at will, which started with the rubbing of two wood sticks. The modern cigarette lighter corresponds to the next evolutionary step in the process. Frazer’s book Myths of the Origin of Fire1 gives a drilling a hole in wood gave human beings the idea fascinating description of the legends about the origin of for producing fire, but interestingly enough, making fire in different regions of the world. From the entry Fire of fire by friction was discovered by people in widely in the encyclopedias2,3 we learn that fire is one of the separated parts of the world. The most widespread human’s race essential tools, control of which helped method for igniting fire was through the conversion of start it on the path toward civilization. The original muscular energy into heat through friction. The fire source of fire undoubtedly was lightning, a chance event drill, a wooden rod placed in a pit in a fireboard which remained the only source of fire for many years. adjacent to tinder, was the commonly used The use of fire is one of man’s earliest habits, so when implement. The initial fire was initiated by a rapid an obvious fireplace with ashes and charcoal is found rotatory motion imparted by spinning the drill near such a skull, it is pronounced human. -
Some Quaker Firms of the Nineteenth
Some Quaker Firms of the Nineteenth Century HE contribution of Friends to the Industrial Revolu tion is well known, and has been competently and Tsympathetically studied by Isabel Grubb and Arthur Raistrick.1 Ordinary textbooks of economic history record the activities of the Darbys of Coalbrookdale, the Lloyds of Birmingham, the Peases of Darlington, and other pioneers of metallurgical industry. The prominence in banking of the Barclays, Hoares, Gurneys, Backhouses and other families is conspicuous and well appreciated. The Victorian period has been less explored, though the dominance of cocoa and chocolate manufacture by the Frys, Cadburys and Rowntrees is a commonplace. Interesting notes on various well-known firms of Quaker origin appeared in Paul Emden's Quakers in Commerce (1940). The following article is largely an expan sion of some of these, and deals with eleven firms Albright & Wilson, Carrs, Fox Roy, Friends' Provident Institution, Gray Dunn, Harrisons & Crosfield, Huntley & Palmer, Jacobs, Montserrat Company, Richardsons, Sturges. Of these, six are primarily manufacturers (two, chemicals and four, biscuits), three are merchants and one an insurance company. Two are Irish and one Scottish. ALBRIGHT & WILSON AND J. & E. STURGE The first group comprises the two firms of Albright & Wilson and J. and E. Sturge, closely related in location and personnel as well as in type of product, and the Montserrat Company, which is linked to them by business and family ties. John Sturge (1799-1840), younger brother of the more noted Joseph, commenced the manufacture of chemicals at Bewdley in 1822. The role of chemistry in industrial progress has until recently been less realized than that of physics;2 the varied technological applications of this science were in the early nineteenth century offering opportunities for rapid 1 Isabel Grubb, Quakerism and industry before 1800 (1930); A. -
For the Victims of Industrial Pollution
Dear prospective councillor, Re Stop the Garden City proposals ruining Sheepwash Nature Reserve and the wildlife corridor at Temple Way. I write to you as secretary of The Friends Of Sheepwash Local nature Reserve, wildlife and environmental campaigner and on behalf of over 400 users of the site and residents of the Temple Way Estate who delivered a petition to Sandwell council in 2017 opposing elements of the so called “Dudley port Supplementary planning document”, and in respect of the Sandwell site allocations around hazardous waste and historic landfill sites. There is a long history to the land to which I allude, and you will have to bear with me in explaining it, as without this background knowledge, one cannot make an informed opinion of how history is being blurred to conjure up and recycle a scheme from the days of the dubious Black Country Development Corporation, some 30 years previously. Those behind this , including individuals it seems from within SMBC hope that people have forgotten with the passage of time, the fraud and lies that were told with regard to those proposals, but I have put much of it in the public domain with my blog what lies beneath rattlechain lagoon. What Lies Beneath Rattlechain Lagoon? | For the victims of Industrial Pollution This website is a chronical of the struggle to prove that birds were being poisoned by white phosphorus, dumped by Oldbury firm Albright and Wilson, later Rhodia, and now Solvay, who still own the site. I am inviting you to answer questions as part of a blog post concerning this subject, and am keen, as I am sure residents and users of the site are to know what your views are? Adjacent to this hazardous waste site is another tip which also formed part of the former Rattlechain brickworks, though most of the land around this was agricultural, and never “brownfield”.