Baseline Mapping Report Baseline Mapping Report
Total Page:16
File Type:pdf, Size:1020Kb
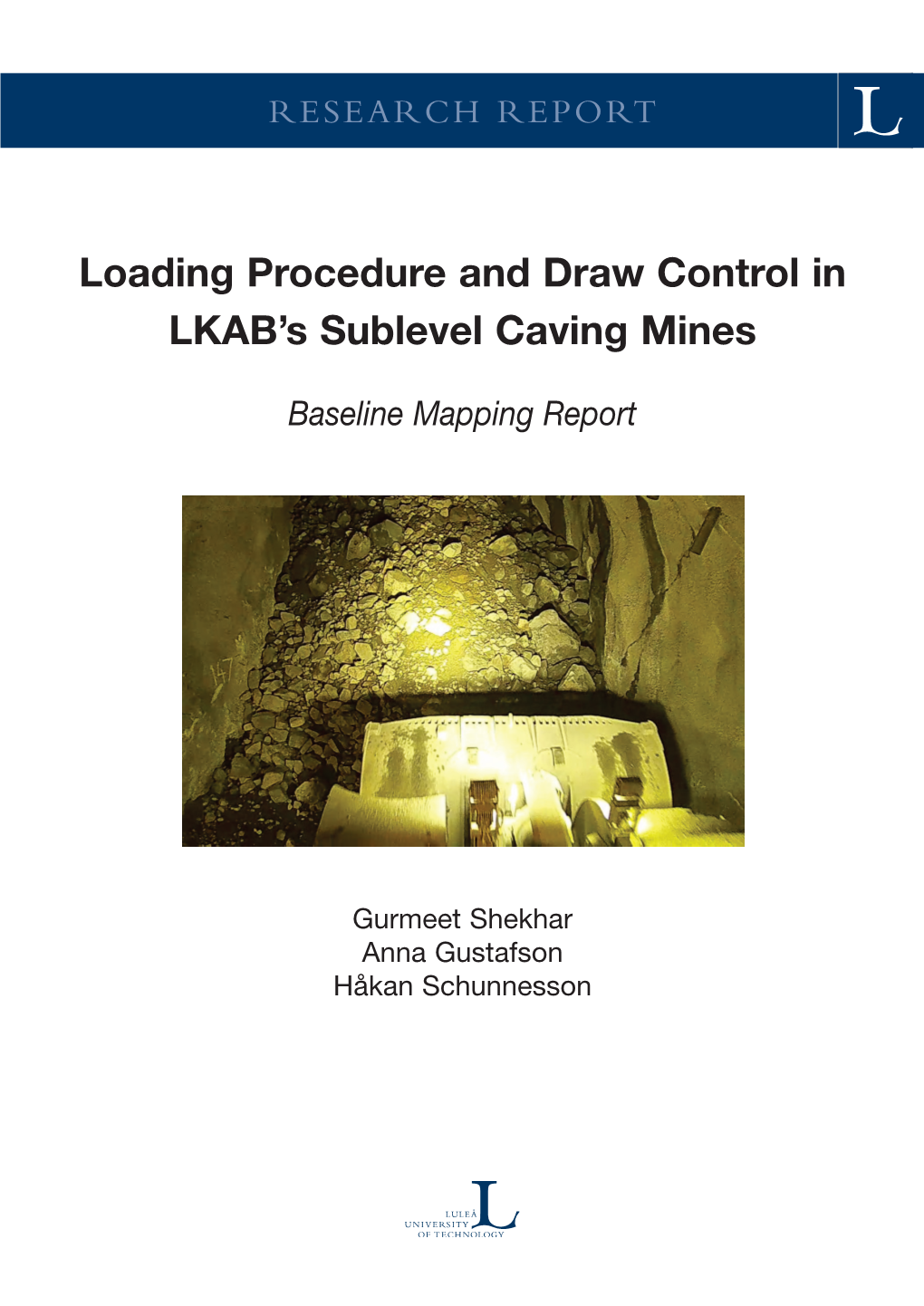
Load more
Recommended publications
-
Fire and Smoke Spread in Underground Mines
Site inventory of operational mines– fire and smoke spread in underground mines. Rickard Hansen Studies in Sustainable Technology 2010:01 Mälardalen University Summary This report is part of the research project “Concept for fire and smoke spread prevention in mines”, conducted by a research group at Mälardalen University. The project is aimed at improving fire safety in mines in order to obtain a safer working environment for the people working for the mining companies in Sweden or for visitors in mines open to the public. This report deals with the second step in the project: the site inventory in operational mines. The main purposes of the inventory are: - To get a clear picture of the risks in the different mines. - To get a clear picture of the protective measures of each mine. - Optimize the choice of design fires for each mine. To find out what the present situation was at the operational mines, a site inventory was conducted at the two LKAB mines. The site inventories were conducted through actual visits to the specific sites and through e-mail correspondence with LKAB personnel responsible for the different sections and areas. During the inventories, predefined forms for each type of item were used in order to facilitate the work. The following items were examined: - Combustible materials in general, for example large amounts of wood. - Vehicles - Cables - Fire barriers - Ventilation systems - Extinguishing systems Besides the above items, earlier fires and fire incidents were also examined. As the two LKAB mines are tremendously large with a large amount of equipment etc, only the most common vehicles were listed and examined further. -
080515 Lindahl Bukarest II
Sustainable Mining in Europe – The Nordic experience Lars-Åke Lindahl SveMin (Swedish Association of mines, mineral and metal producers) Non-energy mining industry in Europe Bucharest, 15 May 2008 Outline • Introduction • The three pillars of sustainable development/sustainable mining – Economic – Social – Ecology/Environment • Concluding comments Health & Safety Energy Environment Exploration Metalprod. access to land Swedish Association of Mines, issues Mineral and Metal Producers EU- Competence Treaties monitoring with unions The three pillars of Sustainable development • Economic • Social • Ecology/Environment Source: SGU Source: SGU Mines in Sweden Swedish mine production 2006 Metal Production Part of EU Place production Iron 23.3 Mt 89.6 % 1st Gold 6.8 t 32.8 % 1st Silver 292 t 16.9 % 2nd Iron (Poland) Sulphide Gold Zinc 210 Kt 25.4 % 2nd Industrial Minerals (Ireland) Operating Planned Lead 55.6 Kt 30.8 % 2nd (Ireland) Copper 86.7 Kt 12.4 % 2nd (Poland) Source: SGU (Swedish Geological Survey) KIRUNA MINE (LKAB) Automated drillrig, Kiruna mine Remote Controlled Electrical Loader, Kiruna mine THE AITIK MINE (Boliden) Source: SGU Source: SGU The three pillars of Sustainable development • Economic • Social • Ecology/Environment 70 60 Swedish Mining and Mineral Industry (all employees) Lost Day Injury Frequency Rate 1988-2007 50 Occupational Accidents 40 30 20 No. per 1 million worked hours 10 0 1988 1989 1990 1991 1992 Under ground 1993 Surface Total 1994 1995 1996 1997 1998 1999 2000 2001 2002 2003 2004 2005 2006 2007 Mining Industry -
Annual Report and Sustainability Report
ANNUAL REPORT AND LKAB SUSTAINABILITY REPORT ANNUAL REPORT AND SUSTAINABILITY REPORT AND SUSTAINABILITY ANNUAL REPORT CONTENTS Events in brief 2 The LKAB Manifesto 3 Overview of the past year 4 President’s report 6 Group strategies 9 LKAB 2009 11 Economic trends, market 13 Steel demands iron ore 16 International trade 17 The iron ore mines 18 Prospecting, ore reserves 19 From iron ore to pellets 20 Production 2009 21 Research and development 22 Human resources 23 Investments 24 The industrial minerals business 25 Subsidiaries 26 2009 SUSTAINABILITY REPORT 27 Stakeholders and sustainability issues 28 Value creation 29 Control of sustainability activities 30 Urban transformation 31 Environment 34 Co-workers 44 Involvement in local communities 49 About LKAB’s Sustainability Report for 2009 106 GRI index 106 Auditors’ statement of assurance 108 CORPORATE GOVERNANCE REPORT 50 Board of Directors and Group Management 55 FINANCE 58 Group overview 58 Contents, financial statements 59 Report of the Directors 60 Financial reports and notes 68 LKAB, BOX 952, SE-971 28 LULEÅ, SWEDEN Proposed disposition of unappropriated earnings 104 www.lkab.com Auditors’ Report 105 Glossary 109 Addresses 110 Annual General Meeting 20092009 and financial information 111 ANNUAL REPORT AND LKAB SUSTAINABILITY REPORT ANNUAL REPORT AND SUSTAINABILITY REPORT AND SUSTAINABILITY ANNUAL REPORT CONTENTS Events in brief 2 The LKAB Manifesto 3 Overview of the past year 4 President’s report 6 Group strategies 9 LKAB 2009 11 Economic trends, market 13 Steel demands iron ore 16 -
Iron Ore in 1997, an Increase of 4.6% Compared with the 1996-97 Production Increased by 0.5%
IRON ORE By William S. Kirk Iron ore is essential to the economy and national security of the U.S. production data for iron ore are developed by the U.S. United States. As the basic raw material from which iron and Geological Survey (USGS) from two separate, voluntary surveys steel is made, its supply is critical to any industrial country. Scrap of domestic operations. The annual “Iron Ore” survey (1066-A) is used as a supplement in steelmaking, but is limited as a major provides 100% of total production shown in tables 1 through 4. feed material because the supply of high-quality scrap is limited. This information is supplemented by employment data, mine Virtually all (about 98%) iron ore is consumed by the steel inspection reports, and information from consumers. The industry. American Iron Ore Association (AIOA) provided data on ore Domestic and international iron ore production levels rose in shipments from loading docks on the upper Great Lakes as well as 1997, with international production reaching a record level of receipts at transfer docks and furnace yards nationwide. The dock 1,035.9 million metric tons. Domestically, shipments exceeded and steel plant data were compiled jointly by AIOA and the those of 1996 by 1.0% although consumption fell slightly. American Iron and Steel Institute (AISI). Companhia Vale do Rio Doce (CVRD), the world’s largest iron Although iron ore was produced by 14 companies, 9 of them ore producer, was privatized, reversing Brazilian Government accounted for 99.5% of all domestic production. The 14 policy that had been in effect for more than 50 years. -
This-Is-Lkab.Pdf
THIS IS LKAB PERFORMANCE IN IRONMAKING IT STARTS WITH THE IRON 1696 The ore-rich mountains 1912 Kiruna Church is completed, 1982 LKAB takes the decision 2010 LKAB earmarks a budget Luossavaara and Kiirunavaara, a gift from the company to the to introduce large-scale sub-level of billions of kronor for future after which LKAB was named, parish. The church will be moved caving, increasing productivity urban transformations in Kiruna are mentioned for the first time to the new centre of Kiruna as part noticeably. LKAB develops olivine and Malmberget. in a document by Samuel Mört, of the urban transformation. pellets, which prove to be a highly a bookkeeper at the Kengis works. competitive pellet product. 2011 LKAB makes record profits. 1940 Narvik is invaded by the The same year the LKAB Academy 1888 The first ore train rolls Germans and the port is blown up. 1989 The subsidiary Minelco, foundation is established to along the Ore Railway from Malm- Ore traffic focuses on Luleå until now LKAB Minerals, is estab- secure future recruitment. berget to Luleå. the port of Narvik is rebuilt. lished. Its task is to develop markets for the iron ore outside 2015 LKAB celebrates 125 1890 The company 1955 LKAB’s first pelletising of the steel industry. years and publishes a book about Luossavaara-Kiirunavaara plant – the first such plant in the company’s history. Aktiebolag – LKAB – is formed. Europe – is taken into operation 1997 Wireless communication in Malmberget, increasing the is introduced into LKAB’s under- 2018 The starting shot for the 1898 Hjalmar Lundbohm is degree to which the iron ore is ground mines using the Wireless SUM (Sustainable Underground appointed as local manager in upgraded and thus also the value Underground Communication Mining) initiative to develop a new Kiruna. -
LKAB 2019 Annual and Sustainability Report
2019 ANNUAL AND SUSTAINABILITY REPORT LKAB aims to create prosperity by being one of the most innovative, resource-efficient and responsible mining and minerals companies in the world. 02 LKAB ANNUAL AND SUSTAINABILITY REPORT 2019 CONTENTS INTRODUCTION RESPONSIBILITY AND GOVERNANCE The year in brief 2 Sustainable enterprise 50 Comments by the President and CEO 4 Risks and risk management 51 How we create value 8 Comments by the Chairman of the Board 58 Objectives for sustainable development 10 Corporate governance report 59 Board of Directors 66 BUSINESS CONTEXT AND STRATEGY Executive management team 68 Global context 13 Strategic priorities 16 FINANCIAL RESULTS Group overview 70 PRODUCTS AND MARKETS Financial statements 73 Customer offering 21 Notes 83 Drivers and trends 22 The Board’s attestation 121 Market development 24 Auditor’s report 122 OPERATIONS SUSTAINABILITY NOTES Exploration 27 Notes to the sustainability report 126 Mining 31 Auditor’s Limited Assurance Report Processing 33 on the Sustainability Report 144 Transport 34 OTHER INFORMATION Suppliers 35 Mineral reserves and mineral resources 146 Employees 36 Ten-year overview 150 Social responsibility 40 Terms and definitions 151 Environmental responsibility 44 Annual General Meeting and financial information 153 Impact in the value chain 48 Addresses lkab.com Administration report pages 2–3, 8–14, 35–72 and 121. Sustainability report pages 8–14, 35–41, 44–47, 50–56 and 125–143. RAIL TRANSPORT PORTS ABOUT LKAB’S ANNUAL AND SUSTAINABILITY REPORT 2019 The Board of Directors and the President hereby submit the annual and sustainability report for Luossavaara-Kiirunavaara AB (publ), corporate identity number 556001-5835, for the calendar year 2019. -
The Mineral Industry of Sweden in 2015
2015 Minerals Yearbook SWEDEN [ADVANCE RELEASE] U.S. Department of the Interior August 2019 U.S. Geological Survey The Mineral Industry of Sweden By Alberto Alexander Perez Sweden is located in northern Europe and shares the production of minerals and mineral products; of this amount, Scandinavian Peninsula with Norway (which borders it to 71% was employed in the production of steel and other refinery the west and north) and Finland (which borders it to the products, about 15.8% was employed in the mining sector, and north and east). Sweden also shares its southern border with the remainder (13.2%) worked in the industrial minerals, ballast, Denmark. Sweden is underlain by Precambrian rocks that are and dimension stone production sector (Geological Survey of part of an area known as the Baltic Shield (or Fennoscandian Sweden, 2017b). Shield). Archaean rocks occur only to a limited extent in In 2015, Sweden exported mostly machinery, motor vehicles, the northernmost part of the country. The rocks in the rest paper products, pulp and wood, iron and steel products, and of the north of Sweden and in the eastern and southern chemicals, and its main export trading partners were Norway parts of the country were formed, and were in many cases (which received about 10.3% of Sweden’s exports), Germany also metamorphosed, in connection with the Svecokarelian (10.3%), the United States (7.7%), the United Kingdom (7.2%), orogeny. In contrast, the bedrock in southwestern Sweden Denmark (6.8%), Finland (6.7%), the Netherlands (5.2%), was metamorphosed during the Sveconorwegian orogeny. Belgium (4.4%), and France (4.2%). -
Condition and Performance Control of Mine Hoist LKAB's Kiruna Mine
Service reference case description Condition and performance control of mine hoist LKAB’s Kiruna mine LKAB Kiruna mine ABB delivered its first complete mine Luossavaara-Kiirunavaara AB (LKAB) is an international high-tech minerals group, one of the world’s leading hoist in 1937. Since then, more than producers of upgraded iron ore products for the steel industry 600 units all over the world have been and a growing supplier of industrial minerals products to installed. High speed and heavy loads other sectors. with high safety and performance, Most of the iron ore products are sold to European steel- demand advanced technology for drive, works. Other important markets are North Africa, the Middle control and brake systems. Qualified East and Southeast Asia. Industrial minerals are sold mainly maintenance personnel and fast in Europe but also to growing markets in Asia and the USA. LKAB has around 3,700 employees, of which about 600 are access to competence is necessary to outside Sweden. maintain high safety, high performance and availability. ABB offers mine hoist Both LKAB’s mines in Kiruna and Malmberget are among the world’s most modern, thanks to investments in advanced services for condition and performance technology and large-scale production systems. control to maintain the equipment in the “as commissioned” condition. The production at Kiruna, Sweden’s northernmost city, is fully automatic from loading to unloading pocket in the head frame. The yearly output of the plant is 30 million tons of iron ore products. ABB has a unique capability to engineer, deliver, install and provide after sale service for entire mechanical and electrical mine hoist systems of all types. -
Draw Control Strategies in Sublevel Caving Mines — a Baseline Mapping of LKAB’S Malmberget and Kiirunavaara Mines by G
http://dx.doi.org/10.17159/2411-9717/2018/v118n7a6 Draw control strategies in sublevel caving mines — A baseline mapping of LKAB’s Malmberget and Kiirunavaara mines by G. Shekhar*, A. Gustafson*, P. Boeg-Jensen†, L. Malmgren†, and H. Schunnesson* objectives of reducing dilution while improving $86(474 ore recovery are difficult to understand and complicated to apply. In SLC, the five The Malmberget and Kiirunavaara mines are the two largest underground parameters used to measure drawpoint iron ore operations in the world. Luossavaara-Kiirunavaara AB (LKAB) uses performance are drawpoint dimensions, final sublevel caving (SLC) to operate the mines while maintaining a high level of productivity and safety. The paper enumerates the loading criteria and extraction ratio, loading stoppage issues, loading constraints at the mines and outlines details of mine design, layout, fragmentation, and ore grade (Shekhar et al., and geology affecting the draw control. A study of the various draw control 2016). Fragmentation is difficult to measure strategies used in sublevel caving operations globally has also been done to continuously, while drawpoint dimensions establish the present state-of-the-art. An analysis of the draw control and tend to remain constant. Therefore the loading operations at the Malmberget and Kiirunavaara mines is remaining parameters – final extraction ratio, summarized using information collected through interviews, internal ore grades, and stoppage issues are vital to an documents, meetings, and manuals. An optimized draw control strategy is analysis of drawpoint performance in an vital for improving ore recovery and reducing dilution in SLC. Based on the operating mine. Previous work cited in the literature review and baseline mapping study, a set of guidelines for literature and other results from physical designing a new draw control strategy is presented. -
The Norrbotten Technological Megasystem: Impact on Society and Environment
The Norrbotten Technological Megasystem: Impact on Society and Environment Jessica Malmberg [email protected] James Buckland [email protected] August 15, 2015 The Kaptensgropen at Malmberget. Contents 1 Introduction 4 1.1 Norrbotten at Present . 4 1.2 A History of Norrbotten . 4 1.3 A History of Industry in Norrbotten . 4 1.4 Defining the Norrbotten Megasystem . 5 1.5 The Place of Community and Environment in the Norrbotten Technolog- ical Megasystem . 5 2 Community 8 2.1 Adapting to a Megasystem . 8 2.2 The Norrbotten Community . 8 2.2.1 A Short History of Kiruna . 8 2.2.2 A Controlling Interest . 9 2.3 Kiruna, G¨allivare/Malmberget, and Aitik . 9 2.3.1 The Relocation of Kiruna . 9 2.3.2 The Slow Malmberget Disaster and Relocation to G¨allivare . 10 2.3.3 The Relative Tranquility of Aitik . 12 2.4 Megasystemic Repercussions of the Norrbotten Megasystem . 12 2.4.1 Disease and Mortality amongst the Mining Community . 12 2.4.2 Indigenous Peoples in Norrbotten . 14 2.4.3 Mining Jobs in Norrbotten . 14 2.4.4 Conclusions on Megasystemic Repercussions . 14 2.5 Industrial Resistance to the Norrbotten Megasystem . 16 2.5.1 Environmental protests . 16 2.5.2 Unionization in Norrbotten . 16 2.5.3 Diversification of Industry in Kiruna . 16 3 Environment 18 3.1 Lule˚aharbour . 18 3.2 Porjus . 20 3.3 Malmberget - Kiirunavaara - LKAB . 22 3.4 Aitik - Boliden . 22 3.5 The environmental aspect of mining from different parties . 24 3.5.1 Geological Survey of Sweden . -
Kiruna Mine, Sweden Iron Ore Extraction Under Challenging Conditions Iron Ore Extraction Under Challenging Conditions
SIKA AT WORK KIRUNA MINE, SWEDEN IRON ORE EXTRACTION UNDER CHALLENGING CONDITIONS IRON ORE EXTRACTION UNDER CHALLENGING CONDITIONS PROJECT DESCRIPTION A reliable supply of consumeables such as the Sika Sigunit® With an ore body 4 km long, 80 m thick and reaching a depth the Sika plasticizers and retarders as well as a range of other of 2 km, LKAB’s Kiruna is the world’s largest, most modern products are absolutely critical to keep this operation going on underground iron ore mine. Since exploitation began at the a daily basis and to secure the large throughput rates of the site over 100 years ago, LKAB has produced over 950 mil- concrete batch plants on surface. lion tons of ore, yet only one third of the ore body has been extracted. PROJECT REQUIREMENTS The extraction-process requires large amounts of sprayed Sprayed concrete must have concrete to secure the mine development. Since 2008 Sika is ́ Early strength of 4 MPa at 4h (Hilti method) the main supplier for admixtures and underground construc- ́ 28 days strength > 40 MPa tion technologies at Kiruna. Located in Swedish Lapland, ́ A maximum dosage of accelerator of 10% north of the arctic circle, the challenges in terms of logistics, ́ A product stability of minimum six months admixture storage and concrete production are manyfold. ́ Open time > 4h Sika, together with its partner LKAB took on the challenge ́ Energy absorption according to ASTM 1550-05 of 490 J many years ago and today the LKAB operations are a show piece of best mining practice for many, large, block cave proj- SIKA SOLUTION ects all around the world. -
European Union & Critical Metals
Critical Metals for Europe www.criticalmetals.eu Critical Metals – Introduction . Aiming to supply high purity critical metals into Europe including lithium, cobalt, vanadium, nickel, copper, manganese and alumina. Focussed on the rapidly growing EU rechargeable battery market principally Lithium Ion Batteries (LiB) and Vanadium REDOX Flow Batteries. Aiming to establish a LiB recycling plant in Sweden and thereafter produce battery chemicals for supply to precursor manufacturers or cell manufacturers in Europe. Advancing a diversified portfolio of battery metals mining projects in the Nordic region to control battery metals feedstock for our own battery chemical production facility. 2 Critical Metals – Northern Sweden & Finland . Skellefteå – home to proposed Northvolt Giga factory, Boliden recycling facility / refinery and proposed Critical Metals LiB recycling facility. Luleå – home to Facebook’s European servers. Malå – home to Critical Metals. White Boxes – Critical Metals Project Pipeline. 3 European Union & Critical Metals – Macro Theme . The European Union (EU) needs between 10 and 20 Lithium Ion Battery (LiB) Giga factories. €20 Bn is required to fund this growth. 1st Giga factory expected to be built in northern Sweden, by Northvolt. EU faces intense global competition for critical metals to supply the Giga factories. Substantially more critical metals need to be sourced from within the EU. LiBs are powering electric vehicles (EVs) and stationary storage devices. EU member countries are now legislating the changeover to EVs . Forecast growth of EVs is massive. Waste generated from end-of-life LiBs will be large and must be recycled. Nordic region already has high EV penetration and advanced waste collection system. 4 Critical Metals – Our Strategy .