2 Laser Interference Lithography (Lil) 9
Total Page:16
File Type:pdf, Size:1020Kb
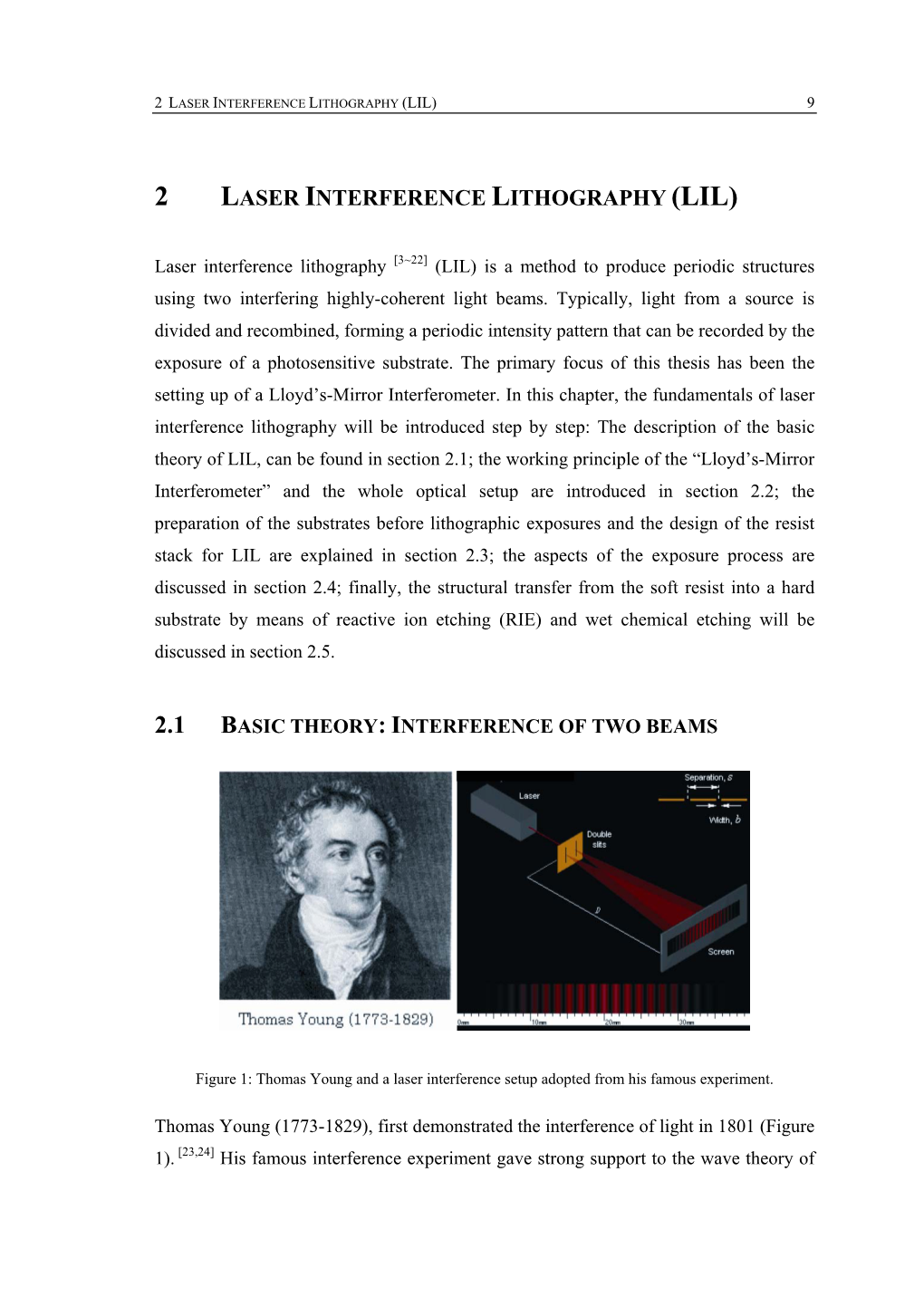
Load more
Recommended publications
-
Towards the Ultimate Resolution in Photolithography
Towards the ultimate resolution in photolithography Yasin Ekinci Paul Scherrer Institute 5232 Villigen PSI, Switzerland E-mail: [email protected] Optical lithography has been the driving force of semiconductor device manufacturing for the past 50 years, due to its high throughput, yield, and scalability. As feature sizes shrink and device density increases, predicted and guided by Moore’s Law, new lithography methods are needed to increase the resolution. Currently, optical patterning approaches such as multiple patterning and DUV immersion are reaching their technological and physical limits. Extreme ultraviolet (EUV) lithography at the wavelength of 13.5 nm is the most promising candidate for the future technology nodes [1-2]. Much research has been done on efficient optics, sources, and photoresists for this wavelength. An important tool in this respect is interference lithography (EUV-IL), which is able to pattern features at single digit nm resolution, enabling research for the timely development of EUV resists. Lithographic pattern resolution is ultimately limited by the wavelength of light used. By decreasing the wavelength down to 13.5 nm, the theoretical patterning limit becomes 3.4 nm. Using EUV light, the XIL-II beamline at the Swiss Light Source, Paul Scherrer Institute, is able to pattern features down to 6 nm half-pitch [3-5]. Spatially coherent light with 4% bandwidth from a synchrotron undulator source is incident upon a transmission mask. The mask is composed of diffraction gratings made of metal or inorganic photoresist and a zeroth order photon stop, supported on a silicon nitride membrane. The diffracted beams from the mask then interfere to produce a sinusoidal areal image, which can then be recorded in a photoresist. -
Laser Interference Lithography
In: Lithography: Principles, Processes and Materials ISBN: 978-1-61761-837-6 Editor: Theodore C. Hennessy, pp. 133-148 © 2011 Nova Science Publishers, Inc. The exclusive license for this PDF is limited to personal printing only. No part of this digital document may be reproduced, stored in a retrieval system or transmitted commercially in any form or by any means. The publisher has taken reasonable care in the preparation of this digital document, but makes no expressed or implied warranty of any kind and assumes no responsibility for any errors or omissions. No liability is assumed for incidental or consequential damages in connection with or arising out of information contained herein. This digital document is sold with the clear understanding that the publisher is not engaged in rendering legal, medical or any other professional services. Chapter 5 LASER INTERFERENCE LITHOGRAPHY Henk van Wolferen and Leon Abelmann MESA+ Research Institute for Nanotechnology, University of Twente, Enschede, The Netherlands ABSTRACT In this chapter we explain how submicron gratings can be prepared by Laser Interference Lithography (LIL). In this maskless lithography technique, the standing wave pattern that exists at the intersection of two coherent laser beams is used to expose a photosensitive layer. We show how to build the basic setup, with special attention for the optical aspects. The pros and cons of different types of resist as well as the limitations and errors of the setup are discussed. The bottleneck in Laser Interference Lithography is the presence of internal reflection in the photo-resist layer. These reflections can be reduced by the use of antireflection coatings. -
Extreme Ultraviolet Interference Lithography with Incoherent Light
Extreme ultraviolet interference lithography with incoherent light Patrick P. Naulleau,1 Christopher N. Anderson,2 and Stephen F. Horne 3 1 Center for X-Ray Optics, Lawrence Berkeley National Laboratory, Berkeley, CA 94720 2 Applied Science & Technology Department, University of California, Berkeley, CA 94720 3 Energetiq Technology Inc., Woburn, MA 01801 ABSTRACT In order to address the crucial problem of high-resolution low line-edge roughness resist for extreme ultraviolet (EUV) lithography, researchers require significant levels of access to high-resolution EUV exposure tools. The prohibitively high cost of such tools, even microfield tools, has greatly limited this availability and arguably hindered progress in the area of EUV resists. To address this problem, we propose the development of a new interference lithography tool capable of working with standalone incoherent EUV sources. Although EUV interference lithography tools are currently in operation, presently used designs require illumination with a high degree of spatial and/or temporal coherence. This, in practice, limits current systems to being implemented at synchrotron facilities greatly restricting the accessibility of such systems. Here we describe an EUV interference lithography system design capable of overcoming the coherence limitations, allowing standalone high-power broad sources to be used without the need for excessive spatial or temporal filtering. Such a system provides promising pathway for the commercialization of EUV interference lithography tools. Keywords: extreme ultraviolet, lithography, interferometry, coherence 1. INTRODUCTION One of the largest challenges facing the commercialization of EUV lithography [1] is the development of high resolution EUV resists. Progress in this area has been hampered in large part due to the scarcity in availability of high-resolution EUV tools. -
Interference Lithography
Interference Lithography Personnel M. Walsh, J. M. Carter, R. C. Fleming, T. A. Savas, M. L. Schattenburg, and H. I. Smith Sponsorship DARPA and ARO Interference lithography (IL) is the preferred method for satellite applications, gratings produced with this tool fabricating periodic and quasi-periodic patterns that have flown on numerous missions, most notably the must be spatially coherent over large areas. IL is a con- Chandra x-ray astronomy satellite launched in August ceptually simple process where two coherent beams of 1999, which included hundreds of matched, high- interfere to produce a standing wave, which can be precision gratings. recorded in a photoresist. The spatial-period of the grat- ing can be as fine as half the wavelength of the interfer- We operate another system similar to the one shown in ing light, allowing for structures on the order of 100nm Figure 26 based on the 325 nm line of a HeCd laser. This from UV wavelengths, and features as small as 30-40 system functions both as an exposure tool with capabili- nm using a deep UV ArF laser. ties comparable to those described above as well as an analysis tool. Using a technique known as Holographic The NanoStructures Lab has been developing IL tech- Phase-Shifting Interferometry (HPSI), the linearity and nology for close to 30 years. We currently operate 4 dif- spatial phase of gratings produced in this system can be ferent IL systems for a wide variety of applications. One quantitatively measured and mapped with an accuracy system, shown schematically in Figure 26, is run in on the order of parts per million. -
Fabrication of Photonic Nanostructures for Light Harvesting in Solar Cells
Fabrication of photonic nanostructures for light harvesting in solar cells by Amalraj Peter Amalathas BSc (Hons) with First Class in Physics, University of Jaffna A thesis submitted in partial fulfilment of the requirements for the degree of Doctor of Philosophy Department of Electrical and Computer Engineering University of Canterbury Christchurch, New Zealand May 2017 Dedicated to my father, mother, sisters, and brothers for their love, endless support and encouragement. i Abstract Reducing optical losses in the solar cells has always been a key challenge in enhancing the power conversion efficiency of the solar cells without increasing significantly the cost. In order to enhance the power conversion efficiency of the solar cells, a number of light trapping schemes have been investigated to manipulate the light inside the absorber layer and to increase the effective optical path length of the light within the absorber layer of a solar cell. In this work, periodic nanopyramid structures were utilized as the light trapping nanostructures in order to improve the performance of the solar cells using low cost maskless laser interference lithography (LIL) and UV nanoimprint lithography (UV- NIL). In addition, a superhydrophobic property of the nanopyramids was explored to add a self-cleaning functionality to the front encapsulation. Firstly, the inverted nanopyramid structures were fabricated on Si substrate by laser interference lithography and subsequent pattern transfer by combined reactive ion etching and KOH wet etching. Maskless LIL was employed as a high-throughput, high resolution and low cost for the fabrication of large scale periodic nanostructures. The periodic inverted nanopyramid structures on a silicon substrate were used as a master mold substrate for the imprint process. -
Pattern-Integrated Interference Lithography
PATTERN-INTEGRATED INTERFERENCE LITHOGRAPHY: SINGLE-EXPOSURE FORMATION OF PHOTONIC-CRYSTAL LATTICES WITH INTEGRATED FUNCTIONAL ELEMENTS A Thesis Presented to The Academic Faculty by Guy Matthew Burrow In Partial Fulfillment of the Requirements for the Degree Doctor of Philosophy in the School of Electrical and Computer Engineering Georgia Institute of Technology August 2012 PATTERN-INTEGRATED INTERFERENCE LITHOGRAPHY: SINGLE-EXPOSURE FORMATION OF PHOTONIC-CRYSTAL LATTICES WITH INTEGRATED FUNCTIONAL ELEMENTS Approved by: Professor Thomas K. Gaylord, Advisor Professor Muhannad S. Bakir School of Electrical and Computer School of Electrical and Computer Engineering Engineering Georgia Institute of Technology Georgia Institute of Technology Professor Miroslav M. Begovic Dr. Donald D. Davis School of Electrical and Computer School of Electrical and Computer Engineering Engineering Georgia Institute of Technology Georgia Institute of Technology Professor Zhuomin Zhang Date Approved: 29 May 2012 School of Mechanical Engineering Georgia Institute of Technology ACKNOWLEDGEMENTS Over the course of nearly three years at Georgia Tech, numerous people have impacted my life and proven instrumental to the research presented in this thesis. It is with great appreciation and humility that I acknowledge their support and contributions. First and foremost, I want to express my sincere thanks to my advisor, Professor Thomas K. Gaylord. I am grateful to have had the chance to learn and develop under his expert guidance. Having served for more than 20 years in the Army, I have found no better example of a true professional. Thank you, sir, for being such a great mentor and leader to us all. I would also like to recognize the other members of my thesis committee: Professor Muhannad S. -
Large-Area Nanoimprint Lithography and Applications
Chapter 3 Large-Area Nanoimprint Lithography and Applications Hongbo Lan Additional information is available at the end of the chapter http://dx.doi.org/10.5772/intechopen.72860 Abstract Large-area nanoimprint lithography (NIL) has been regarded as one of the most prom- ising micro/nano-manufacturing technologies for mass production of large-area micro/ nanoscale patterns and complex 3D structures and high aspect ratio features with low cost, high throughput, and high resolution. That opens the door and paves the way for many commercial applications not previously conceptualized or economically feasible. Great progresses in large-area nanoimprint lithography have been achieved in recent years. This chapter mainly presents a comprehensive review of recent advances in large- area NIL processes. Some promising solutions of large-area NIL and emerging methods, which can implement mass production of micro-and nanostructures over large areas on various substrates or surfaces, are described in detail. Moreover, numerous industrial- level applications and innovative products based on large-area NIL are also demon- strated. Finally, prospects, challenges, and future directions for industrial scale large- area NIL are addressed. An infrastructure of large-area nanoimprint lithography is proposed. In addition, some recent progresses and research activities in large-area NIL suitable for high volume manufacturing environments from our Labs are also intro- duced. This chapter may provide a reference and direction for the further explorations and studies of large-area micro/nanopatterning technologies. Keywords: large-area nanoimprint lithography, large-area micro/nanopatterning, full wafer NIL, roller-type NIL, roll-to-plate NIL, roll-to-roll NIL 1. -
A Solid Immersion Interference Lithography System for Imaging
A Solid Immersion Interference Lithography System for Imaging Ultra-High Numerical Apertures with High-Aspect Ratios in Photoresist using Resonant Enhancement from Effective Gain Media Prateek Mehrotra1,**, Chris A. Mack2, Richard J. Blaikie1,* 1The MacDiarmid Institute for Advanced Materials and Nanotechnology, Department of Electrical and Computer Engineering, University of Canterbury, Christchurch, New Zealand 2Department of Chemical Engineering, The University of Texas at Austin, Austin, TX *Current Address: Department of Physics, University of Otago, PO Box 56, Dunedin, New Zealand ABSTRACT In the last year our Solid Immersion Lloyd’s Mirror Interference Lithography (SILMIL) system has proved to be a successful tool for evanescent interferometric lithography (EIL). The initial goal was to use SILMIL in conjunction with the surface plasmon polariton (SPP) surface states at the resist-metal interface. Through this resonance, we aimed to counter the decay of evanescent images created using EIL. By analyzing the theory in greater detail we were able to develop a better understanding of the resonance phenomena. In this paper, details of the design of SILMIL and how one may utilize it to produce ultra-high numerical apertures (NAs) are given, as well as an introduction to the resonance phenomena and the mechanism behind it. We introduce a new method that requires a gain medium (one that has a negative loss) to achieve significant enhancements, and present an effective gain medium by using a high-index dielectric on low-index media. We present results at λ = 405 nm using such an effective gain medium and also provide a feasible design example at the lithography standard λ = 193 nm. -
Contrast Analysis of Polarization in Three-Beam Interference Lithography
applied sciences Article Contrast Analysis of Polarization in Three-Beam Interference Lithography Fuping Peng 1,2 , Jing Du 2, Jialin Du 1,2, Simo Wang 1,2 and Wei Yan 2,* 1 University of Chinese Academy of Sciences, Beijing 100049, China; [email protected] (F.P.); [email protected] (J.D.); [email protected] (S.W.) 2 Institute of Optics and Electronics, Chinese Academy of Sciences, Chengdu 610209, China; [email protected] * Correspondence: [email protected] Abstract: This paper analyzes the effect of polarization and the incident angle on the contrasts of interference patterns in three-beam interference lithography. A non-coplanar laser interference system was set up to simulate the relationship between contrast, beam polarization, and the incident angle. Different pattern periods require different incident angles, which means different contrast losses in interference lithography. Two different polarization modes were presented to study the effects of polarization with different incident angles based on theoretical analysis simulations. In the case of the co-directional component TE polarization mode, it was demonstrated that the pattern contrast decreases with the increase in the incident angle and the contrast loss caused by the polarization angle error also grew rapidly. By changing the mode to azimuthal (TE-TE-TE) polarization, the contrast of the interference pattern can be ensured to remain above 0.97 even though the incident angle is large. In addition, TE-TE-TE mode can accept larger polarization angle errors. This conclusion provides a theoretical basis for the generation of high-contrast light fields at different incident angles, and the conclusion is also applicable to multi-beam interference lithography. -
Sub-50 Nm Patterning by Immersion Interference Lithography Using a Littrow Prism As a Lloyd’S Interferometer
3450 OPTICS LETTERS / Vol. 35, No. 20 / October 15, 2010 Sub-50 nm patterning by immersion interference lithography using a Littrow prism as a Lloyd’s interferometer Johannes de Boor,* Dong Sik Kim, and Volker Schmidt Max-Planck Institute of Microstructure Physics, Weinberg 2, 06120 Halle, Germany *Corresponding author: deboor@mpi‑halle.mpg.de Received July 27, 2010; revised September 7, 2010; accepted September 7, 2010; posted September 20, 2010 (Doc. ID 132405); published October 12, 2010 We present a simple setup that combines immersion lithography with a Lloyd’s mirror interferometer. Aiming for smaller structure sizes, we have replaced the usual Lloyd’s interferometer by a triangular Littrow prism with one metal-coated side, which acts as a mirror. Because of the higher refractive index of the prism, the wavelength and, thus, the attainable structure sizes, are decreased significantly. Using a laser with a wavelength of 244 nm, we could produce line patterns with a period of less than 100 nm and a width of 45 nm. The introduced setup retains all the advantages of a Lloyd’s mirror interferometer, in particular the flexibility in periodicity. © 2010 Optical Society of America OCIS codes: 120.3180, 120.4610, 120.4640, 220.4241, 220.4610. Laser interference lithography (LIL) is a powerful tool that sity distribution across the sample. The distance between is frequently used for the fabrication of nanostructures [1]. the intensity maxima, the pitch or periodicity pLIL,is Simple line gratings, but also more complex two- or even given by [14] three-dimensional photoresist patterns, can be created λ [2,3]. -
Nano-Scale Patterning Using Pyramidal Prism Based Wavefront
Available online at www.sciencedirect.com Physics Procedia 19 (2011) 416–421 ICOPEN2011 Nano-scale patterning using pyramidal prism based wavefront interference lithography Sidharthan R a and V M Murukeshanb* a,bSchool of Mechanical and Aerospace Engineering, Nanyang Technological University, 50 Nanyang Avenue, Singapore 639798 *Corresponding author: [email protected] Abstract In this work we propose to fabricate nano-scale square lattice features using the principle of four wavefront interference employing a pyramidal prism. A UV laser of 266nm wavelength was used to pattern features on thinned positive tone resist AZ 7220 using single exposure technique. It was demonstrated that features with sub 500nm pitch size could be recorded using a pyramidal prism with edge angle of 30.4°. Holes with diameter around 187nm in square symmetry with pitch of 414nm were fabricated. The proposed setup is relatively simple, requiring minimum number of components. Keywords: Pyramidal prism; DUV Lithography. 1. Introduction Improvement of integrated circuit performance in microelectronics is made possible by an increase in transistor integration density which coincidently follows the exponential increase pattern predicted by Gordon Moore[1]. It’s a known fact that this density improvement and size reduction starts at patterning or lithography stage. Even though it is not the only technically challenging process which should be improved upon on regularly basis, advances in lithography provides a gateway to IC performance improvement and cost reduction. A standard lithographic system requires an exposure tool, high resolution masks, resists etc and it involves transfer of patterns from masks to resist over a series of steps. Exposure system used for mass manufacturing in industry mainly uses visible, Ultra Violet (UV) or Deep UV (DUV) light. -
Nanoimprint Lithography - Next Generation Nanopatterning Methods for Nanophotonics Fabrication
14 Nanoimprint Lithography - Next Generation Nanopatterning Methods for Nanophotonics Fabrication Jukka Viheriälä, Tapio Niemi, Juha Kontio and Markus Pessa Optoelectronics Research Centre, Tampere University of Technology, Finland 1. Introduction Nanophotonics is wide field covering many interesting applications branching from cutting edge science including plasmonics, metamaterials, cavity quantum electrodynamics in high- Q cavities all the way to applied sciences like silicon nanophotonics for on chip optical interconnections and single frequency semiconductor light sources. Most of the practical device demonstrations in these fields utilize nanopatterned surfaces. Applications require patterning of nanoscopic gratings, photonic crystals, waveguides and metal structures. There are many wonderful demonstrations of nanotechnology-based lasers and other photonic components. However, difficult questions related to fabrication need to be addressed before these components enter any market. Demonstrations in the scientific literature have relied heavily on the use of direct writing lithography methods, such as electron beam lithography or focused ion beam lithography. These methods, although excellent for scientific studies, cannot be scaled up to allow cost effective production of nanophotonics. Lithography solutions developed for integrated circuits can produce extremely narrow linewidths and deliver high precision but are difficult to transfer to photonics fabrication. There exist many alternative lithography methods, but their scale-up to cost effective volume production is challenging. Since the introduction of nanoimprint lithography (NIL) in 1995 (Chou et al. 1995), there has been widespread interest in the development of NIL for various applications. As early as in 2003 NIL had gained substantial support and was chosen as one of MIT's Technology Review’s “10 Emerging Technologies That Will Change the World” (Technology Review 2003).