445-3-H Safety and Health for Field Operations
Total Page:16
File Type:pdf, Size:1020Kb
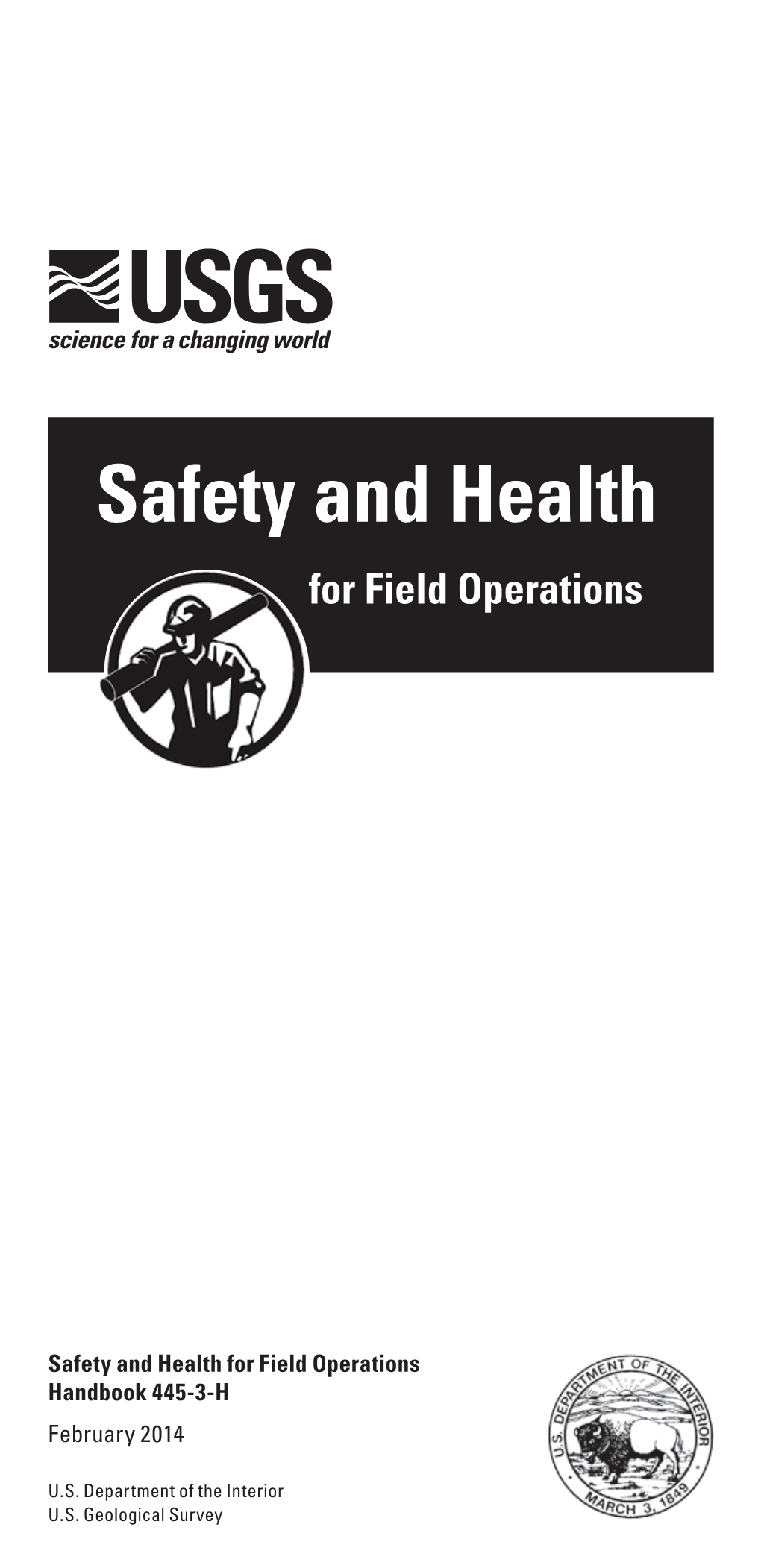
Load more
Recommended publications
-
A Web Survey to Evaluate the Thermal Stress Associated with Personal Protective Equipment Among Healthcare Workers During the COVID-19 Pandemic in Italy †
International Journal of Environmental Research and Public Health Article A Web Survey to Evaluate the Thermal Stress Associated with Personal Protective Equipment among Healthcare Workers during the COVID-19 Pandemic in Italy † Alessandro Messeri 1,2,* , Michela Bonafede 3 , Emma Pietrafesa 3, Iole Pinto 4, Francesca de’Donato 5, Alfonso Crisci 1, Jason Kai Wei Lee 6,7,8,9,10,11 , Alessandro Marinaccio 3 , Miriam Levi 12 , Marco Morabito 1,2 and on behalf of the WORKLIMATE Collaborative Group ‡ 1 Institute of Bioeconomy, National Research Council (IBE-CNR), 50019 Florence, Italy; [email protected] (A.C.); [email protected] (M.M.) 2 Centre of Bioclimatology, University of Florence (UNIFI), 50144 Florence, Italy 3 Occupational and Environmental Medicine, Epidemiology and Hygiene Department, Italian Workers’ Compensation Authority (INAIL), 00143 Rome, Italy; [email protected] (M.B.); [email protected] (E.P.); [email protected] (A.M.) 4 Physical Agents Sector, Regional Public Health Laboratory, 53100 Siena, Italy; [email protected] 5 Department of Epidemiology Lazio Regional Health Service, ASL ROMA 1, 00147 Rome, Italy; [email protected] 6 Human Potential Translational Research Programme, Yong Loo Lin School of Medicine, National University of Singapore, Singapore 117593, Singapore; [email protected] 7 Department of Physiology, Yong Loo Lin School of Medicine, National University of Singapore, Citation: Messeri, A.; Bonafede, M.; Singapore S117593, Singapore 8 Pietrafesa, E.; Pinto, I.; de’Donato, F.; Global Asia Institute, National University of Singapore, Singapore S119076, Singapore 9 Crisci, A.; Lee, J.K.W.; Marinaccio, A.; N.1 Institute for Health, National University of Singapore, Singapore S117456, Singapore 10 Institute for Digital Medicine, National University of Singapore, Singapore S117456, Singapore Levi, M.; Morabito, M. -
Heat Stress and PPE During COVID-19: Impact on Health Care Workers’ Performance, Safety and Well-Being in NHS Settings
medRxiv preprint doi: https://doi.org/10.1101/2020.09.22.20198820; this version posted September 23, 2020. The copyright holder for this preprint (which was not certified by peer review) is the author/funder, who has granted medRxiv a license to display the preprint in perpetuity. It is made available under a CC-BY-NC-ND 4.0 International license . Heat Stress and PPE during COVID-19: Impact on health care workers’ performance, safety and well-being in NHS settings. Sarah L Davey1*., Ben J Lee1., Timothy Robbins2,3., Harpal Randeva2, C. Doug Thake1. 1 Occupational and Environmental Physiology Group, Centre for Sport, Exercise and Life Sciences, (CSELS), Faculty of Health and Life Sciences, Coventry University, Coventry, United Kingdom. 2 University Hospitals Coventry & Warwickshire NHS Trust, Coventry, United Kingdom. 3 Institute of Digital Healthcare, WMG, University of Warwick, Coventry, United Kingdom Corresponding author: Sarah Davey E-mail: [email protected] Key words: PERSONAL PROTECTIVE EQUIPEMENT; HEAT STRESS; HEALTH CARE WORERS, SARS-COV-2 (COVID-19); EXTREME ENVIRONMENTS; HEAT-RELATED ILLNESS. NOTE: This preprint reports new research that has not been certified by peer review and should not be used to guide clinical practice. 1 medRxiv preprint doi: https://doi.org/10.1101/2020.09.22.20198820; this version posted September 23, 2020. The copyright holder for this preprint (which was not certified by peer review) is the author/funder, who has granted medRxiv a license to display the preprint in perpetuity. It is made available under a CC-BY-NC-ND 4.0 International license . Abstract Background: The impermeable nature of PPE worn by health care workers (HCWs) during the SARS-CoV-2 (COVID-19) pandemic can potentiate heat stress which may negatively impact the performance, safety and well-being of HCWs. -
Occupational Exposure to Heat and Hot Environments
Criteria for a Recommended Standard Occupational Exposure to Heat and Hot Environments DEPARTMENT OF HEALTH AND HUMAN SERVICES Centers for Disease Control and Prevention National Institute for Occupational Safety and Health Cover photo by Thinkstock© Criteria for a Recommended Standard Occupational Exposure to Heat and Hot Environments Revised Criteria 2016 Brenda Jacklitsch, MS; W. Jon Williams, PhD; Kristin Musolin, DO, MS; Aitor Coca, PhD; Jung-Hyun Kim, PhD; Nina Turner, PhD DEPARTMENT OF HEALTH AND HUMAN SERVICES Centers for Disease Control and Prevention National Institute for Occupational Safety and Health This document is in the public domain and may be freely copied or reprinted. Disclaimer Mention of any company or product does not constitute endorsement by the National Institute for Occupational Safety and Health (NIOSH). In addition, citations of websites external to NIOSH do not constitute NIOSH endorsement of the sponsoring organizations or their programs or products. Furthermore, NIOSH is not responsible for the content of these websites. Ordering Information This document is in the public domain and may be freely copied or reprinted. To receive NIOSH documents or other information about occupational safety and health topics, contact NIOSH at Telephone: 1-800-CDC-INFO (1-800-232-4636) TTY: 1-888-232-6348 E-mail: [email protected] or visit the NIOSH website at www.cdc.gov/niosh. For a monthly update on news at NIOSH, subscribe to NIOSH eNews by visiting www.cdc.gov/ niosh/eNews. Suggested Citation NIOSH [2016]. NIOSH criteria for a recommended standard: occupational exposure to heat and hot environments. By Jacklitsch B, Williams WJ, Musolin K, Coca A, Kim J-H, Turner N. -
Implementing Sensor Technology Applications for Workplace Health
Spook et al. BMC Public Health (2019) 19:1100 https://doi.org/10.1186/s12889-019-7364-2 RESEARCHARTICLE Open Access Implementing sensor technology applications for workplace health promotion: a needs assessment among workers with physically demanding work Sander Mathijn Spook, Wendy Koolhaas, Ute Bültmann and Sandra Brouwer* Abstract Background: Workers with physically demanding work may be at risk for injury, illness or other adverse health outcomes due to exposure to different occupational hazards, especially at higher age. Sensor technology applications may be useful in the workplace to unobtrusively measure and monitor work exposures and provide workers with real- time feedback or access to data on demand. Many aspects might impede the implementation of sensor technology applications in the workplace, which should be taken into consideration for a successful implementation. Moreover, needs and preferences of workers regarding the use of sensor technology applications during work performance need to be identified. Therefore, the aim of this study was to identify worker needs and preferences regarding the use of sensor technology applications in the workplace. Methods: Four on-site focus group sessions were conducted in four different companies among workers with physically demanding work (n = 30). Semi-structured interview schedules were used to identify which work exposures should be measured, by which kind of sensor technology applications, under which (pre)conditions, how to motivate long-term use of sensor technology applications, and which type of feedback is preferred. For data analysis, a content-analysis with an inductive approach was performed. Results: Participants mentioned that they want to use wearable sensor technology applications to measure and monitor physical job demands, occupational heat stress, noise and fatigue. -
Complete Issue (PDF)
Abstracts Eliminating Occupational Disease: areas in the country. The study studied 40 small scale industries, and collected 40 water samples (potable) for cyanide and mer- Translating Research into Action cury which are used in mining. Questionnaire-guided interviews EPICOH 2017 and work analysis covering mining practices and risk exposures were conducted, as well as chemical analysis through gas chro- 28–31 August 2017, Edinburgh, UK matography. Results of the study showed unsafe conditions in the industries such as risk of fall during erection and dismantling of scaffolds, guard rails were not provided in scaffoldings, man- Poster Presentation ual extraction of underground ores, use of explosives, poor visi- bility in looking for ores to take out to surface, exposure to Pesticides noise from explosives, and to dust from the demolished struc- tures. Mine waste was drained into soil or ground and/or rivers and streams. The most common health problems among miners 0007 ASSESSMENT OF PESTICIDE EXPOSURE AND were hypertension (62%), followed by hypertensive cardiovascu- OCCUPATIONAL SAFETY AND HEALTH OF FARMERS IN lar disease due to left wall ischemia (14%). Health symptoms THE PHILIPPINES such as dermatitis, and peripheral neuropathy were noted and Jinky Leilanie Lu. National Institutes of Health, Institute of Health Policy and Development these can be considered as manifestations of chronic cyanide poi- Studies, University of the Philippines Manila, Manila, The Philippines soning, further, aggravated by improper use of protective equip- ment. For the environmental samples of potable water, 88% and 10.1136/oemed-2017-104636.1 98% were positive with mercury and cyanide respectively. About 52% of drinking water samples exceeded the TLV for mercury Aims This is a study conducted among 534 farmers in an while 2% exceeded the TLV for cyanide. -
Heat Stress & Occupational Health
New Understandings in Heat Stress Emma Moynihan, MPH Doctoral Candidate – Johns Hopkins University Advisor: Gurumurthy Ramachandran, PhD Outline • Introduction • Heat Stress & Occupational Health • Measuring Heat Stress • Worker Protections for Heat Stress • Application of Remote Sensing to Determine Heat Stress • Conclusion 1 Introduction Sengupta, S & Frank, B.L (August 25, 2020). Heat Smoke and COVID are Battering the Workers who Feed America. The New York Times. Heat, Smoke and Covid Are Battering the Workers Who Feed America - The New York Times (nytimes.com) ©2015,© 2020,© Johns2014, Johns JohnsHopkins Hopkins Hopkins University. University. University. All All rights rights All reserved.rightsreserved. reserved. Heat Stress & Occupational Health • Nearly half (47%) of all jobs in the United States require working outside, where exposure to heat stress greatest, for some part of the workday.2 • Workers at particularly high risk to heat stress include: • Agricultural Workers • Emergency Responders • Firefighters • Construction & utility Workers • Healthcare workers • Transportation Workers3 Figure one: OSH Heat-Related Deaths and Extreme Heat Projections4 ©2015,© 2020,© Johns2014, Johns JohnsHopkins Hopkins Hopkins University. University. University. All All rights rights All reserved.rightsreserved. reserved. 3 What is Heat Stress? Universal Thermal Climate Index Heat Exhaustion Heat Stress Heat Stroke Wet Bulb Globe Temperature Heat Strain Heat Index ©2015,© 2020,© Johns2014, Johns JohnsHopkins Hopkins Hopkins University. University. -
Occupational Exposure to Heat and Hot Environments
1 2 Criteria for a Recommended Standard: 3 Occupational Exposure to Heat and Hot 4 Environments 5 6 Revised Criteria 2013 7 8 9 10 11 12 13 14 15 16 17 18 19 DEPARTMENT OF HEALTH AND HUMAN SERVICES 20 Centers for Disease Control and Prevention 21 National Institute for Occupational Safety and Health 22 This information is distributed solely for the purpose of pre dissemination peer review under applicable information quality guidelines. It has not been formally disseminated by the National Institute for Occupational Safety and Health. It does not represent and should not be construed to represent any agency determination or policy. EXTERNAL REVIEW DRAFT 1 Foreword 2 [To be finalized.] 2 This information is distributed solely for the purpose of pre dissemination peer review under applicable information quality guidelines. It has not been formally disseminated by the National Institute for Occupational Safety and Health. It does not represent and should not be construed to represent any agency determination or policy. EXTERNAL REVIEW DRAFT 1 Executive Summary 2 The National Institute for Occupational Safety and Health (NIOSH) has evaluated the scientific 3 data on heat stress and hot environments, and updated the Criteria for a Recommended Standard: 4 Occupational Exposure to Hot Environments [NIOSH 1986a]. This document was last updated 5 in 1986, and in recent years, including during the Deepwater Horizon oil spill response of 2010, 6 questions were raised regarding the need for revision to reflect recent research and findings. This 7 revision includes additional information relating to the physiological changes that result from 8 heat stress; updated information from relevant studies, such as those on caffeine usage; evidence 9 to redefine heat stroke and associated symptoms; and updated information on physical 10 monitoring and personal protective equipment and clothing that can be used to control heat 11 stress. -
Heat Stress 1 18 March 2021
Heat Illness Response Guideline Presented in order of decreasing urgency. One or more indicators in a category indicate a positive determination for that category. Observations Determination and Action Severe Fatigue or Vomiting – Heat Stroke Watch for other signs of heat stroke Emergency Response while starting treatment for severe Begin aggressive cooling (cover in ice or place in cold/ice heat exhaustion. water bath). If ice is not available, other methods of cooling are flushing water over person from hose or shower; or Erratic / Irritable Behavior keep the skin wet and fanning. Confusion / Disorientation Garbled / Gibberish Speech Call emergency services and advise them that it is a heat Hysteria / Delirium / Apathy stroke case. Collapse Shivering Convulsions Unconscious Wobbly Walking Severe Heat Exhaustion Slow Reaction Times Move to air-conditioned space, encourage water/electrolyte Severe Fatigue drink if able, and allow to lay down. Severe Muscle Cramps Vomiting or Collapse without Any Optional: Cover head and shoulders with a towel soaked in Signs of Heat Stroke ice water. Person may say they have Watch for signs of heat stroke. Severe Fatigue Loss of Appetite If recovery is not progressing in 15 min, arrange for medical Nausea treatment and continue to watch for possible heat stroke. Headache Blurred Vision Person may say they feel Mild Heat Exhaustion Tired / Fatigued Inform supervisor Thirsty Recovery in cool area Weak Drink water and/or electrolyte drink Dizzy Lightheaded If symptoms persist after 15 min, treat as severe -
Regional Emphasis Program for Heat Illnesses REGIONAL IDENTIFIER: Region VI
U.S. DEPARTMENT OF LABOR Occupational Safety and Health Administration DIRECTIVE NUMBER:CPL 2 02-00-027A EFFECTIVE DATE: October 1, 2019 SUBJECT: Regional Emphasis Program for Heat Illnesses REGIONAL IDENTIFIER: Region VI ABSTRACT Purpose: This Instruction renews a Regional Emphasis Program (REP) for outdoor heat-related health hazards. Scope: This Instruction applies to all worksites in Arkansas, Louisiana, Oklahoma, and Texas, and those worksites in New Mexico that are under Federal OSHA jurisdiction. References: OSHA Instruction CPL 02-00-025 OSHA Instruction CPL 02-00-051 OSHA Instruction CPL 02-00-163 OSHA Instruction CPL 04-00-002 OSHA Instruction TED 01-00-015 Cancellations: Region VI Regional Notice CPL 2 02-00-027 dated October 1, 2018, Regional Emphasis Program for Heat Illnesses. State Impact: Region VI 21(d) Consultation Project Offices in Arkansas, Louisiana, Oklahoma, New Mexico and Texas will provide outreach, consultation services, and training to affected employers as requested. Action Office s : Region VI Area Offices Region VI Consultation Project Offices Dallas Regional Office Information Office : New Mexico Occupational Health and Safety Bureau Originating Office: Dallas Regional Office Contact: Assistant Regional Administrator for Enforcement Programs 525 S. Griffin Street, Room 602 Dallas, Texas 75202-5007 (972) 850-4145 By and Under the Authority of ERIC S. HARBIN Acting Regional Administrator TABLE OF CONTENTS Abstract………………………………………….…………..Cover Page I. Purpose……………………………………………..…………...…..1 II. Scope………………………………………………..………............1 III. References………………………………………….…..……..…….1 IV. Expiration……………………….……………....…………..………1 V. Background…………………….……………….………..…………1 VI. Objectives……………………….……………………..……………3 VII. Action………………………….……………………………………3 VIII. Inspection Process…………….………….………….……….……..4 IX. Recording in OIS …………….……………..………………...….....5 X. Outreach…………………….…………….….……………………..6 XI. Partnerships and Alliances………………….…….…….………......7 XII. -
To View the Entire USF Health Research Day Abstract Booklet, Go To
To view the entire USF Health Research Day Abstract Booklet, go to http://health.usf.edu/research/home.html Proud Sponsors of the 23rd Annual RESEARCH DAY Morsani College of Medicine College of Nursing College of Public Health School of Pharmacy MCOM Department of Internal Medicine A Special Thank You to Our Patron Sponsors: 23rd Annual Research Day Friday, February 22, 2013 Marshall Student Center (MSC) AGENDA TIME EVENT LOCATION Presenters: Registration and Poster Set-up 7:30 a.m. – 9:30 a.m. Atrium/Ballroom (Early registration: Feb 21st 4:00 – 6:00 p.m.) 7:30 a.m. – 9:30 a.m. Judges: Registration and Assignments Atrium 4th Annual Joseph Krzanowski, PhD 8:00 a.m. – 10:00 a.m. Oval Theater USF Health Invited Oral Presentations 10:00 a.m. – 12:00 p.m. Poster Judging Session Ballroom 12:00 p.m. – 1:00 p.m. Lunch Break Ballroom Atrium Office of Undergraduate Research 12:45 p.m. – 1:30 p.m. Ballroom Stage Presentation to The Villages students 17th Annual Roy H. Behnke Distinguished Lectureship Dr. Howard L. McLeod 1:00 p.m. – 2:30 p.m. Oval Theater Fred Eshelman Distinguished Professor University of North Carolina – Chapel Hill “Using the Genome to Guide Therapy” Posters Available for Viewing Ballroom 1:00 p.m. – 3:30 p.m. Sunshine ERC Posters Plaza Room 2708 2:30 p.m. – 3:15 p.m. Awards Ceremony Oval Theater 3:30 p.m. – 4:00 p.m. Posters Removed Ballroom 4:00 p.m. – 5:00 p.m. Reception Ballroom Atrium 23rd Annual RESEARCH DAY 17h Annual Roy H. -
Change4life Sportsclubs Change4life Sportsclubs
nge4life sports cl cha lubs enture activity pa adv ck school Client Change4Life Ins date 00/00 S36 21176 Campaign Activity Pack Operator DEZ Page 1 Date 15.11.11 11:23 Title Adventure Trim 297x210mm Proof 11 File S36 21176 C4L Activity Pack Adventure TA/SA – Agency XXX 00 XX0000 Colour CMYK Spots - Bleed 3mm IntroducingIntroducing youryour activityactivity packpack Change4Life Sports Clubs have been designed around a clear need to increase physical activity levels in less active children by developing a new type of sports club. We want to create an inspirational environment to engage less active young people, so over time they start to take part in school sport and carry on with lifelong physical activity. Your deliverer’s activity pack includes; 1. A set of 16 activity cards 2. A guide to the contents of each card You have 12 activity cards relating to a theme, and at the back of the pack, So you can find your way around the activity cards quickly and easily, we’ve 4 activity cards to use for warm up activities. provided a guide to what’s on the front and back of each card. Every card is designed with support from national governing bodies of sport to include skills and activities related to their Olympic and Paralympic sports. 3. A sport skills matrix They include: The matrix indicates the range of sport specific skills used within each game and the sports they relate to. There are also some ideas for using the matrix • An image of the activity in action within your planning and delivery. -
Occupational Therapy Classroom Resource Pack for Primary Schools
OCCUPATIONAL THERAPY CLASSROOM RESOURCE PACK FOR PRIMARY SCHOOLS Aislinn Pierse, Breda Barry, Valerie O’ Connor, Sarah Hogan, Elizabeth Kennedy Paediatric Occupational Therapists Primary Care Occupational Therapy Department HSE South – Cork North Lee City General Hospital Infirmary Road Cork 021-4927850 Contents Purpose of the Pack........................................................................................................................................4 Section one – Sensory/Motor Skills Developmental Milestones.............................................................................................................................5 Introduction to Sensory Integration.............................................................................................................6 Sensory Modulation.........................................................................................................................................7 Movement Breaks – Vestibular activities.....................................................................................................8 Movement Breaks – Proprioceptive activities.............................................................................................9 Body Awareness.............................................................................................................................................10 Motor Coordination......................................................................................................................................11 Bilateral