Competent Persons Report for Toromocho Copper Project
Total Page:16
File Type:pdf, Size:1020Kb
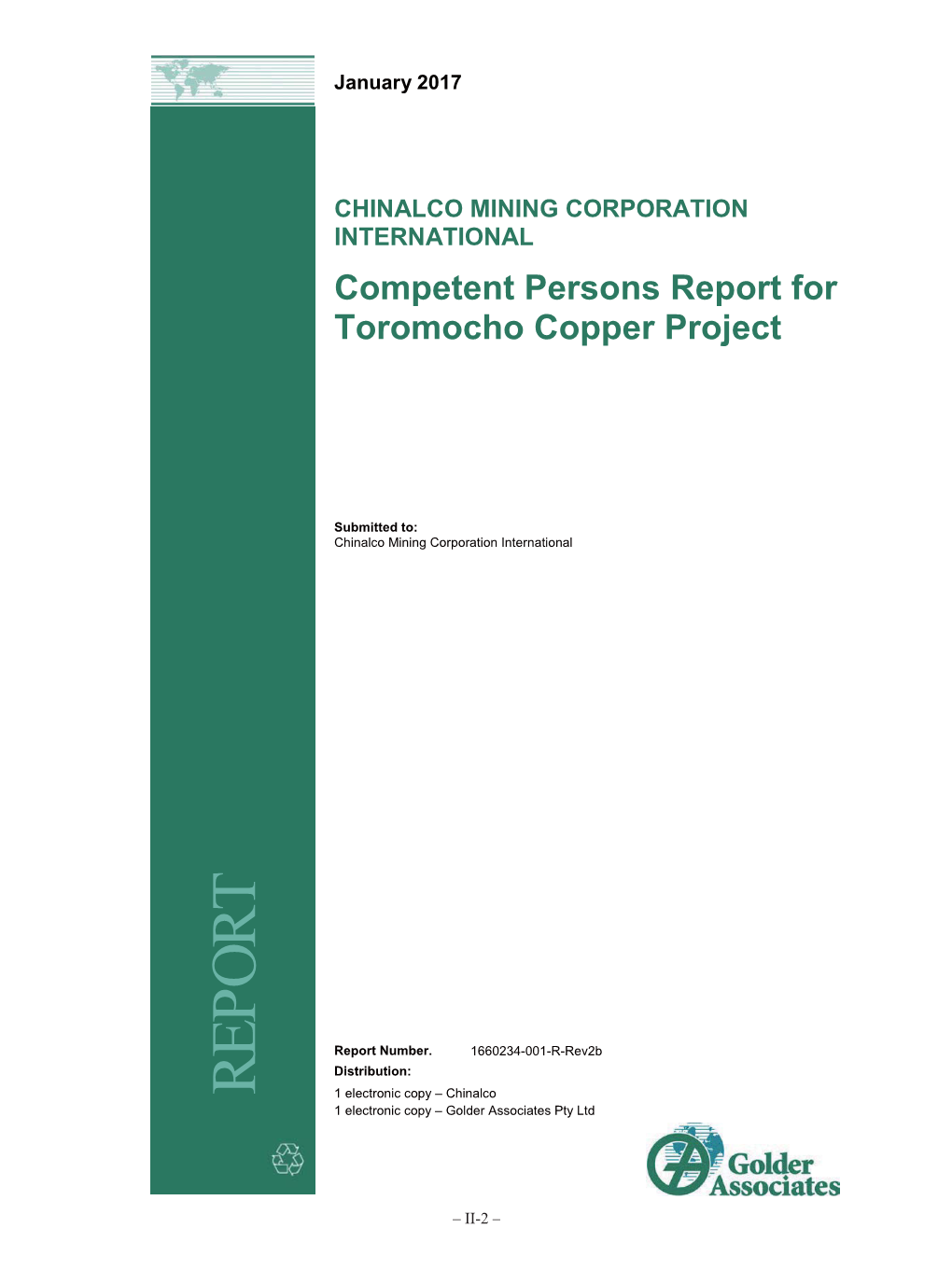
Load more
Recommended publications
-
Thesis Reference
Thesis Geochronological, structural, isotopes and fluid inclusion constraints of the polymetallic Domo de Yauli district, Peru BEUCHAT, Sebastien Abstract L'origine des gisements polymétalliques du Domo de Yauli est liée au magmatisme Miocène ayant affecté les Andes péruviennes. Cette étude met en évidence les relations géochronologiques et structurales entre les intrusions et les corps minéralisés, ainsi que les caractéristiques des fluides hydrothermaux. Les âges obtenus sur les intrusions et les minéralisations indiquent un système pulsé et répétitif durant 9 Ma, alors que les contraintes associées à la formation des gisements montrent un champ hétérogène probablement lié à l'influence de linéaments crustaux. Les rapports isotopiques de Sr, Pb, O et H associés à l'étude des inclusions fluides, par microthermométrie, spectroscopie Raman et LA-ICP-MS, révèlent l'influence d'au moins trois fluides d'origines et de caractéristiques différentes. Leur mélange a conduit à la formation des gisements, alors que les éléments économiquement intéressants ont uniquement été apportés par le fluide s'étant séparé du magma. Reference BEUCHAT, Sebastien. Geochronological, structural, isotopes and fluid inclusion constraints of the polymetallic Domo de Yauli district, Peru. Thèse de doctorat : Univ. Genève, 2003, no. Sc. 3415 URN : urn:nbn:ch:unige-979762 DOI : 10.13097/archive-ouverte/unige:97976 Available at: http://archive-ouverte.unige.ch/unige:97976 Disclaimer: layout of this document may differ from the published version. 1 / 1 UNIVERSITE DE GENEVE FACULTE DES SCIENCES Département de minéralogie Professeur L. Fontboté Docteur R. Moritz Geochronological, Structural, Isotopes and Fluid Inclusion Constraints of the Polymetallic Domo de Yauli District, Pern THE SE présentée à la Faculté des sciences de l'Université de Genève pour obtenir le grade Docteur ès sciences, mention Sciences de la Terre par Sébastien BEUCHAT de Undervelier (JU) Thèse N° 3415 GENEVE Atelier de reproduction de la Section de physique 2003 La Faculté des sciences, sur le · préavis de Messieurs L. -
The Miocene Morococha District, Central Peru – Large-Scale Epithermal Polymetallic Overprint on Multiple Intrusion-Centred Porphyry Systems
The Miocene Morococha District, Central Peru – Large-Scale Epithermal Polymetallic Overprint on Multiple Intrusion-Centred Porphyry Systems K Kouzmanov1, A Bendezú2, H Catchpole3, M Ageneau4, J Pérez5 and L Fontboté6 ABSTRACT In the world-class mining district of Morococha, epithermal polymetallic replacement bodies and veins overprint porphyry mineralisation and skarns related to subvolcanic intrusions of Miocene age, thus indicating ore formation in two different environments, separated in time or forming a continuum. The district covers an area of about 70 km2 in the north-western part of the Domo de Yauli complex in the Western Cordillera of central Peru and is part of the Miocene polymetallic belt, also hosting the deposits of Colquijirca (Bendezú et al, 2008b) and Cerro de Pasco (Baumgartner, Fontboté and Vennemann, 2008). Multiple late-Miocene porphyry stocks intruded Permian, Triassic-Jurassic and late-Cretaceous sedimentary carbonate and volcano-sedimentary formations, as well as large mid-Miocene barren intrusions (Figure 1). Extensive field work and detailed mapping of different styles of orebodies suggest that ore formation in the area was related to the late-Miocene magmatism. Good outcrop conditions and superimposing of different mineralisation styles make Morococha an ideal location for studying ore-forming processes in a complex porphyry-related magmatic-hydrothermal system in which porphyry-to-epithermal transition occurred. Miocene magmatic activity in the area was started by the emplacement of the Anticona diorite intrusive of mid-Miocene age (14 Ma), dominating the north-western part of the district. There is no indication of mineralisation genetically related to it. In late-Miocene times (7 to 9 Ma) a series of porphyry intrusions (diorites, granodiorites to quartz-monzonites, normal calc-alkaline, medium to high-K in composition) intruded into the different sedimentary sequences as well as the Anticona diorite. -
Report Seeks to Demonstrate the Evolution of Chinese FDI Practices
Acknowledgments First and foremost, we would like to thank our helpful and patient professor and research partner, Dr. Judith Shapiro of American University. Dr. Shapiro’s guidance and expertise were indispensable throughout the course of this investigation. We are also incredibly grateful for the opportunity to work with the World Resources Institute (WRI) on this project, and particularly with Denise Leung of WRI’s Sustainable Finance Team, whose advice was integral to our research process. Our team is also indebted to the following individuals: Victoria Chonn Ching, Universidad del Pacífico Kim Claes, Belgian Development Agency Dr. Ken Conca, American University Luis Gonzales, The Nature Conservancy Dr. Barbara Kotschwar, Peterson Institute for International Economics Dr. Stephen MacAvoy, American University Dr. Carlos Monge, Revenue Watch Institute Margaret Myers, Inter-American Dialogue Rachel Nadelman, American University Alejandro Neyra, Peruvian Ministry of Foreign Affairs Dr. Cynthia Sanborn, Universidad del Pacífico Michael Shifter, Inter-American Dialogue Sijin Xian, American University Shougang Case Study Acknowledgments: Departamento del Medio Ambiente de la Municipalidad de Marcona María De Los Angeles Zapata Rodriguez, Pontificia Universidad Católica del Perú Sindicato de Obreros Mineros de Shougang Hierro Peru, S.A.A. Chinalco Case Study Acknowledgments: Ing. Juan Aste Daffós, Adviser to Congresswoman Verónika Mendoza (Cusco) Julio Casas, Social Capital Group Ing. Marlene Cerrón Ruiz, Regional Government of Junin Paul Chachi, Social Capital Group Arq. Pedro Montoya Torres, Regional Government of Junin Ing. Rosi Rojas Cruzatti, Regional Government of Junin Dr. Luis Alberto Salgado Jorge Sanchez, Social Capital Group Mario Villavicensio, Knight Piésold Consulting Jinzhao Case Study Acknowledgments: Xiaohuan Tang, General Manager, Jinzhao Mining Peru SA Catherine Cardich, Deutsche Gesellschaft für Internationale Zusammenarbeit Dr. -
Technical Report for the Morococha Property, Yauli, Peru
Pan American Silver Corp. Technical Report for the Morococha Property, Yauli, Peru Effective date: June 30 2014 Prepared by: Martin Wafforn, P. Eng. Vice President, Technical Services Michael Steinmann, P. Geo. Executive Vice President, Corporate Development and Geology Americo Delgado, P. Eng. Director, Metallurgy November 2014 1 of 71 Pan American Silver Corp. Contents 1 Summary ............................................................................................................................................... 6 1.1 Property description and ownership ............................................................................................ 6 1.2 Geology and mineralization .......................................................................................................... 6 1.3 Status of exploration, development, and operations ................................................................... 7 1.4 Mineral resource and reserve estimates ...................................................................................... 8 1.5 Conclusions and recommendations ............................................................................................ 10 2 Introduction ........................................................................................................................................ 12 3 Reliance on other experts ................................................................................................................... 14 4 Property description and location .....................................................................................................