In Bore Behaviour of Large Calibre Armour Piercing Fin Stabilised Discarding Sabot Projectiles
Total Page:16
File Type:pdf, Size:1020Kb
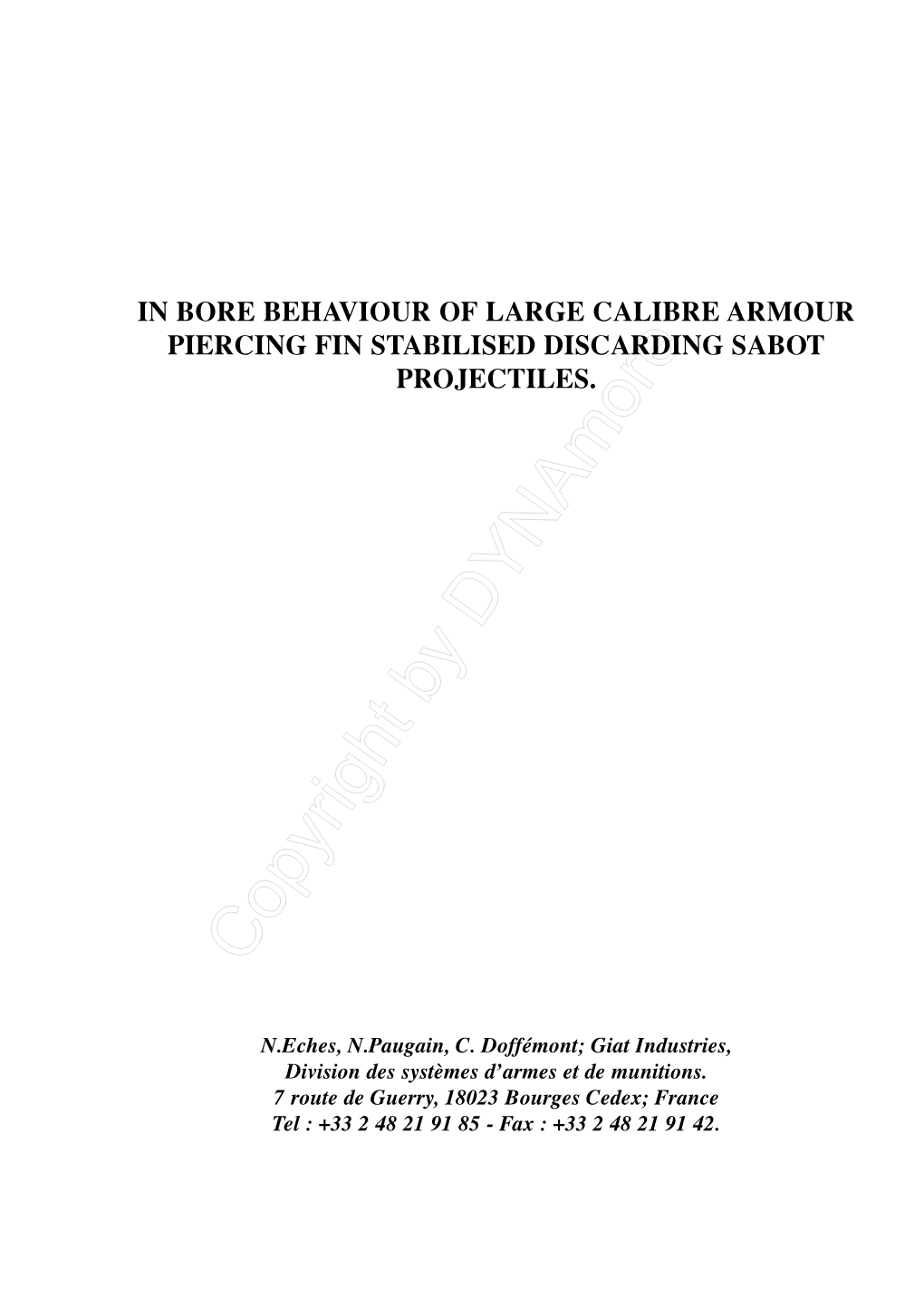
Load more
Recommended publications
-
Ballistic Aiming System Manual
BALLISTICS AIMING SYSTEM Table of Contents Boone and Crockett™ Big Game Reticle ......................... Page 1 Varmint Hunter’s™ Reticle .................................... Page 11 LR Duplex® Reticle .......................................... Page 22 LRV Duplex® Reticle ......................................... Page 29 SAbot Ballistics Reticle (SA.B.R.®) ............................. Page 34 Ballistic FireDot® Reticle ..................................... Page 44 Multi-FireDot™ Reticle....................................... Page 51 Pig-Plex Ballistic Reticle...................................... Page 59 TMOA™ Reticles ............................................ Page 64 Various language translations of the BAS Manual can be found at www.leupold.com. La traduction en français du manuel BAS se trouve à www.leupold.com. La traducción al español del manual BAS se encuentra en www.leupold.com. Das BAS-Handbuch in deutscher Sprache finden Sie unter www.leupold.com. La traduzione in italiano del manuale BAS è pubblicata sul sito seguente: www.leupold.com. 1 The Leupold Ballistics Aiming System®– Boone and Crockett™ Big Game Reticle The goal of every hunter is a successful hunt with a clean harvest. It was with this in mind that Leupold® created the Leupold Ballistics Aiming System®. Because we so strongly agree with the Boone and Crockett Club’s legacy of wildlife conservation and ethical fair chase hunting, we have designated one of the system’s reticles as the Boone and Crockett™ Big Game reticle. The Boone and Crockett Big Game reticle gives the hunter very useful tools intended to bring about successful hunts with clean and efficient harvests. Through the use of these straightforward and easy-to-follow instructions, it is sincerely hoped that all hunters will find their skills improved and their hunts more successful. Boone and Crockett Club® is a registered trademark of the Boone and Crockett Club, and is used with their expressed written permission. -
Artillery Through the Ages, by Albert Manucy 1
Artillery Through the Ages, by Albert Manucy 1 Artillery Through the Ages, by Albert Manucy The Project Gutenberg EBook of Artillery Through the Ages, by Albert Manucy This eBook is for the use of anyone anywhere at no cost and with almost no restrictions whatsoever. You may copy it, give it away or re-use it under the terms of the Project Gutenberg License included with this eBook or online at www.gutenberg.org Title: Artillery Through the Ages A Short Illustrated History of Cannon, Emphasizing Types Used in America Author: Albert Manucy Release Date: January 30, 2007 [EBook #20483] Language: English Artillery Through the Ages, by Albert Manucy 2 Character set encoding: ISO-8859-1 *** START OF THIS PROJECT GUTENBERG EBOOK ARTILLERY THROUGH THE AGES *** Produced by Juliet Sutherland, Christine P. Travers and the Online Distributed Proofreading Team at http://www.pgdp.net ARTILLERY THROUGH THE AGES A Short Illustrated History of Cannon, Emphasizing Types Used in America UNITED STATES DEPARTMENT OF THE INTERIOR Fred A. Seaton, Secretary NATIONAL PARK SERVICE Conrad L. Wirth, Director For sale by the Superintendent of Documents U. S. Government Printing Office Washington 25, D. C. -- Price 35 cents (Cover) FRENCH 12-POUNDER FIELD GUN (1700-1750) ARTILLERY THROUGH THE AGES A Short Illustrated History of Cannon, Emphasizing Types Used in America Artillery Through the Ages, by Albert Manucy 3 by ALBERT MANUCY Historian Southeastern National Monuments Drawings by Author Technical Review by Harold L. Peterson National Park Service Interpretive Series History No. 3 UNITED STATES GOVERNMENT PRINTING OFFICE WASHINGTON: 1949 (Reprint 1956) Many of the types of cannon described in this booklet may be seen in areas of the National Park System throughout the country. -
Artillery Ammunition from the 1781 Siege of Star Fort
University of South Carolina Scholar Commons Archaeology and Anthropology, South Carolina Faculty & Staff Publications Institute of 9-2020 Artillery Ammunition from the 1781 Siege of Star Fort James B. Legg Follow this and additional works at: https://scholarcommons.sc.edu/sciaa_staffpub Part of the Archaeological Anthropology Commons, and the Military History Commons Research Artillery Ammunition from the 1781 Siege of Star Fort By James B. Legg th Regular readers of Legacy, will recall that daily feature of the siege. By June 18 , the The 6-pounder was the standard field in 2018 and 2019, SCIAA Director Steve Americans were entrenched immediately caliber used by both British and American Smith conducted USC “Maymester” north of the ditch of Star Fort, but a large artillery during the Revolution. Historical archaeological field schools in and around relief force of British regular troops was sources indicate that the Americans used Star Fort, a component of the 1781 British on its way to break the siege. Greene at least four, 6-pounder field guns in defenses of Ninety Six, South Carolina, at decided to risk a direct assault on Star Fort the siege of Star Fort, while the British Ninety Six National Historic Site (Figures before giving up the siege, but the attack had only two or three 3-pounders, and 1 and 2). The work included formal met with a bloody repulse. Greene broke possibly some very light-caliber swivel excavation units, and an array of metal off the siege and withdrew the following guns. Nevertheless, we found both detector sample areas. Among our findings day, but the British then decided that the American and British 6-pounder shot in was a significant assemblage related to the post of Ninety Six was too exposed to be Star Fort. -
Muzzleloader Nonlead 112018
A B C D E F G H I J K L M N O P 1 2 Iowa Hunting Regs: Flintlock or percussion cap muzzleloading rifles or muskets btwn .44 & .775 caliber shooting single projectiles; Muzzleloading pistols .44 caliber or larger. Electronic ignition are not allowed. 3 4 Iowa Hunters Leading the Way does not endorse any particular ammunition. Always properly match your firearm and ammunition. 5 Information was obtained from vendor listings on November 1, 2018. Call stores to ensure availability. 6 7 Brand Model Caliber Type Slug Weight Muzzle Manufacture # Quantity Notes Scheels Bass Pro Brownells ammo.com Midway natchezss.com Sportsman's 8 Barnes Expander Muzzleloading .50 Sabot Slug 325 grain 30680 24 Hollow point, flat base; Unavailable- seasonal run X 9 Barnes Expander Muzzleloading .45 Sabot Slug 250 grain 30577 24 Hollow point, flat base; Unavailable- seasonal run X 10 Barnes Expander Muzzleloading .50 Sabot Slug 300 grain 30583 24 Hollow point, flat base; Unavailable- seasonal run X 11 Barnes Expander Muzzleloading .54 Sabot Slug 275 grain 30679 24 Hollow point, flat base; Unavailable- seasonal run X 12 Barnes Expander Muzzleloading .45 Sabot Slug 195 grain 30509 24 Hollow point, flat base; Unavailable- seasonal run X 13 Barnes Spit-fire Expander .50 Sabot Slug 245 grain 30574 24 Spitzer, boat tail X 14 Barnes Spit-fire Expander .50 Sabot Slug 285 grain 30579 24 Unavailable- seasonal run X 15 Barnes Spit-fire TEZ Muzzleloading .50 Sabot Slug 250 grain 30587 15 Polymer tip with flat base X X 16 Barnes Spit-fire TEZ Muzzleloading .50 Sabot Slug 250 -
The Right Slug for Your Slug Gun
IOWA SHOOTING NEWS THE RIGHT SLUG FOR YOUR SLUG GUN By Michael Ware It won’t be long now and we’ll all have buck fever. I know no matter how many times I go hunting with my family, I always manage to get that rush when the ‘king konger’ shows himself. While I deer hunt in Missouri at our family farms during rifle season, there have been times that I was sure General Patton and all that follow were coming over the hill towards my Iowa house in December. It is slug gun season folks. First thing’s first. We need to establish brand and velocity of slug over others. This aggressive and faster twist rate to remain the two common slugs available. Forster is especially true in rimfire rifles, and slug spin stabilized, thus providing accuracy. So and Brenekke are lead projectile types guns are no different. I recommend buying a heavier weight like the Remington 385gr and are very similar. They both are used three or four kinds of Accutip may require a in smooth bore barrels with the Brenekke slugs, sighting your 1/28 twist barrel where style slug having a wad attached to the weapon in diligently, RIFLED SLUG BARRELS a lighter weight like the base. While you see Brenneke brand slugs and weighing the cost TEND TO RANGE Hornady 300gr SST may on the market, oddly they are Forster style vs. accuracy of each so need something closer in manufacture with no wad physically you can make a good FROM 1/28 TWIST to 1/35 or so. -
M829E4 Armor Piercing, Fin Stabilized, Discarding Sabot – Tracer (APFSDS-T)
FY14 ARMY PROGRAMS M829E4 Armor Piercing, Fin Stabilized, Discarding Sabot – Tracer (APFSDS-T) Executive Summary • The M829E4 120 mm cartridge is a line-of-sight kinetic energy cartridge designed for the Abrams main battle tank. • During Integrated Test and Evaluation (IT&E), in-bore structural failures (IBSFs) occurred in the ambient zone temperature range (60-86 degrees Fahrenheit). The program manager stopped testing and conducted a formal failure analysis. • Preliminary testing indicates the M829E4 cartridge is demonstrating an overall reliability of 94 percent as a result of IBSFs. The reliability requirement is 98 percent. • The failure analysis identified reliability problems with the production process of the cartridge. The program has implemented production process changes to address reliability deficiencies and is in the process of conducting additional testing to verify the effectiveness of the changes. • On June 30, 2014, the Program Executive Officer Ammunition approved the M829E4 cartridge for Milestone C with provisions. • The Milestone Decision Authority authorized 910 M829E4 cartridges for low-rate initial production (LRIP) on The visible difference between the two cartridges is the June 30, 2014. Ammunition Data Link (ADL) interface rings on the base of the M829E4. The rings serve as the interface between System the Abrams’ fire control system and the M829E4. The ADL • The M829E4 120 mm cartridge is a line-of-sight kinetic enables the Abrams’ fire control system to send information to energy cartridge designed for the Abrams main battle tank. It the M829E4. is the materiel solution for the Abrams’ lethality capability gap against threat vehicles equipped with 3rd Generation Mission Explosive Reactive Armor. -
Armor Piercing Ammunition
ARMOR PIERCING AMMUNITION Federal Firearms Licensees and others concerned: On August 28, 1986, the President signed Public Law 99-408 (100 Stat. 920) which regulates the manufacture, importation and sale of armor piercing ammunition. The Act amends chapter 44 of title 18, United States Code to define the term armor piercing ammunition as "a projectile or projectile core which may be used in a handgun and which is constructed entirely (excluding the presence of traces of other substances) from one or a C combination of tungsten alloys, steel, iron, brass, bronze, beryllium copper, or depleted uranium. Such term does not include shotgun shot required by Federal or State environmental or game regulations for hunting purposes, a frangible projectile designed for target shooting, a projectile which the Secretary finds is primarily intended to be used for sporting purposes, or any other projectile or projectile core which the Secretary finds is intended to be used for industrial purposes, including a charge used in an oil and gas well perforating device." Provisions of Public Law 99-408 provide that: 1. No person may manufacture or import armor piercing ammunition and no manufacturer or importer may sell or deliver such ammunition except: a. for the use of the United States or any department or agency thereof or any State or any department, agency or political sub division thereof; b. for the purposes of exportation; or c. for the purposes of testing or experimentation ( as authorized by the Director. - z - C Z. Manufacturers and importers of armor piercing ammunition must be licensed by the Bureau. -
Homicide by a Rifled Shotgun Slug: Unconventional Ballistics
Rom J Leg Med [19] 101-106 [2011] DOI: 10.4323/rjlm.2011.101 © 2011 Romanian Society of Legal Medicine Homicide by a rifled shotgun slug: unconventional ballistics Luv Sharma1*, P.K. Paliwal2 _________________________________________________________________________________________ Abstract: Two types of firearms are well known- Rifled and smoothbore. The shotgun is conventionally loaded with shot. Shot is a collective term for small balls of lead used primarily as projectiles in shotguns. Ammunition for shotguns in the USA is shotgun shells, shotshells, or just shells; cartridge is standard usage in the United Kingdom and India. Ballistic expertise in India of the world usually bases on the rigid idiom that pellets emerge from a shotgun while bullets and the like are fired from rifled weapons. Anything not conforming to this reasoning is treated and termed as ‘bizarre’. Homicide by shotgun slugs in India has not been reported extensively, though the incidence may be more than expected. This case highlights the fact that ammunition in the stricter sense may not be ‘pathognomic for a type of firearm and the crime solving agencies must re-educate themselves on this aspect. Key Words: firearms, smooth bore, rifled shotgun is a firearm that is usually designed to be fired from the shoulder, which uses A the energy of a fixed shell to fire a number of small spherical pellets called shot, or a solid projectile called a slug. The usual ammunition as mentioned in texts and routinely encountered by Forensic experts is the traditional smoothbore weapon firing pellets from a cartridge. In India, no standard textbook of Forensic Medicine describes the possibility of a ‘rifled shotgun’ in detail. -
How Does a Cannon Work?
How Does A Cannon Work? Tube Chassis Cascabel Muzzle Vent Trunnions Breech Carriage The tube rested on the carriage, supporting it for firing and controlling recoil (energy re- People have been fascinated These guns are muzzle-loaders. leased when the gun fired). The with guns since the invention of Everything entered and left them tube and carriage rested on a artillery during the Middle Ages. through the muzzle. Most were chassis. A chassis permitted the This basic guide explains how a made of cast iron. They consist movement of the cannon left or 19th Century seacoast cannon of three basic components: the right, forward or back to aim, operated, and the types of tube, the carriage, and the load, and fire. All together, this projectiles that were used. chassis. weapon was called a “piece.” Smoothbore Cannon Smoothbore guns typically fired shot,” used for setting fires. similar to shells, but also con spherical projectiles; the classic tained shrapnel (small iron or round cannonball. Ammunition Shells were hollow with a charge lead balls). These were anti consisted of five kinds: solid shot, of gunpowder inside. The personnel rounds, timed to shell, case shot, canister, and powder was ignited by a timed explode in front of the target. grape shot. fuse which lit when the gun fired. Shells were used to set fires and Canister and grape shot turned a Solid shot were used for punctur as signal shots. cannon into a shotgun, killing ing walls and decks of ships. men and destroying objects. When heated, they became “hot A third type, case shot, were Shot Shell Case Shot Canister Stand of Grape Rifled Cannon Rifled cannon fired cylindrical, accuracy and range. -
Chapter 1 Chapter 1
CHAPTER 1 CHAPTER 1 INTRODUCTION The "Ballistics" is derived tVoni the Latin word "baiiista" which is an ancient machine designed to hurl a javelin. The word baiiista owes its origin to a Greek word "Ballein" meaning 'to throw' '", The stone hurled by prehistoric man was the first example of ballistics. The ability of throwing farther, with more power led to devices such as slings and spears. Thus ballistics can be defined as scientific study of motion of a projectile in some medium: either in space or in atmosphere or in liquid. Motion of gun projectile is studied in Gun Ballistics. The gun can be viewed as a mechanical device in which heat, liberated by a burning propellant, is converted into the useful kinetic energy of projectile. Its function is to propel projectiles toward specified targets. When a round is fired propellant starts burning, ga.ses start coming out which develop pressure inside the gun. Projectile gains velocity and starts moving inside the barrel. It leaves the gun from the muzzle end (Fig. 1.1). Then projectile moves in air till it hits and damages the target. Gun ballistics is studied in following classes: ' i) Internal Ballistics ii) External Ballistics iii) Intermediate Ballistics iv) Terminal Ballistics (Fig. 1.2). i) Internal Ballistics Internal ballistics is the scientific study of the operating processes within the gun from the moment burning of the propellant is initiated. Change in the pressure and gain in the projectile velocity are the oiilcomes o\' these processes due to the chemical energy generated hy burning the propellant. ii) External Ballistics External ballistics deals with characteristics that influence the motion of the projectile as it moves along its trajectory. -
ARMOR Anti- ARMOR Materials by Design by Donald J
Armor/Anti-Armor ARMOR anti- ARMOR materials by design by Donald J. Sandstrom magine tank armor that grains aligned in a sheet of ura- chews up a high-velocity nium that allow it to stretch into a projectile on impact . or long, lethal jet of unbroken metal. I composites of tungsten and These examples illustrate how uranium that lend an antitank Los Alamos is using its knowl- penetrator rod the stiffness of edge of materials to design and the tungsten. the density and py - fabricate new and stronger com- rophoric property of the uranium, ponents for both armor and pene- and the surprising strength of trators of armor. their mixture or tiny crystal Our interest in applying ma- 36 Los Alamos Science Summer 1989 terials research to conventional tive process of theory, design. There is also a complementarily weapons has its origins in the fabrication, and testing used to between the applications of mate- Laboratory’s nuclear weapons develop nuclear weapons serves rials in conventional and nuclear program. To deal with the unique as the basis for a similar process weapons-one that has a syner- materials used in nuclear weap- in developing conventional ord- gistic effect on both programs, A ons, such as actinides, special ce- nance. The attention to detail in nuclear weapon releases so much ramics, polymers, and so forth, material properties required for energy so rapidly that materials the Laboratory had to develop nuclear weapons is, perhaps, even behave much like isotropic fluids significant expertise in materi- more important for conventional and can usually be described by als research. -
Firearms-2015-071.Pdf
Revised 8/14/15 VIRGINIA DEPARTMENT OF FORENSIC SCIENCE EVIDENCE HANDLING & LABORATORY CAPABILITIES GUIDE FIREARMS &TOOLMARKS Contact Information If you have any questions concerning the Firearms & Toolmarks examination capabilities or evidence handling procedures, please call the Training Section or the Firearms & Toolmarks Section at the Forensic Laboratory that services your area. Laboratory Section Contact Phone Number Central Stephen Atkinson (804) 588-4141 Eastern Allison Milam (757) 355-5965 Northern Jay Mason (703) 334-9748 Western Wendy Gibson (540) 283-5932 © 2015 Virginia Department of Forensic Science Firearms & Toolmarks - Page 1 of 12 Revised 8/14/15 OVERVIEW The primary role of the firearms examiner is the examination of firearms and ammunition components in an attempt to associate a particular firearm as having fired particular ammunition components, through microscopic comparison. CAPABILITIES AND SERVICES Mechanical Condition of Firearms Each firearm that is submitted to the Firearms Section is examined to determine whether it is in normal mechanical operating condition and is test fired, when possible. This examination includes the operability of the safety features, physical characteristics of the firearm and determination of manufacturer, model and serial number. Also, capability of full automatic fire is determined. National Integrated Ballistics Information Network (NIBIN) DFS has a formal agreement with the ATF to enter ballistic information into NIBIN and exchange information. Digital images of the markings on fired cartridge/shotshell cases recovered from a crime scene or test fires from submitted semiautomatic pistols and semiautomatic, slide-action, and bolt-action and lever-action rifles and shotguns are acquired and searched against a database. The Department’s NIBIN system is set up to search specimens submitted at all four of the DFS laboratories.