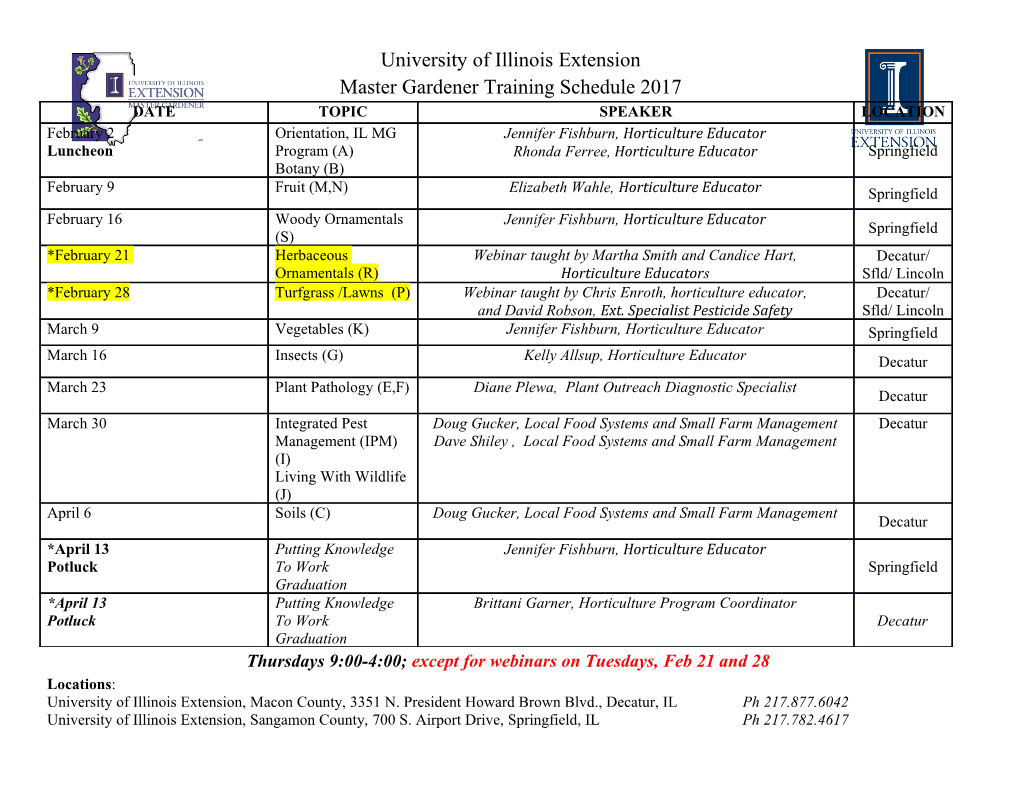
Structural Analysis of Components Obtained by the Injection Molding Process André Antunes Oliveira [email protected] Instituto Superior Técnico, Lisboa, Portugal April 2016 Abstract The mechanical properties of components manufactured using the injection molding process depend on the characteristics of its constituent material, the processing conditions used and, ultimately, on the part’s geometry. This parameters have a strong influence on process resultant variables, like the material flow, the fiber orientation, the internal stress fields and, consequently, the warpage. Thus, the material obtained under these conditions has different properties than the ones initially provided by the manufacturer, causing structural changes in each component, which subsequently modify its load performance. Injection simulation programs, such as Autodesk Moldflow, computationally reproduce each step of this process. In order to implement the manufacturing history of each injection molded component on the reproduction of its loading behavior, it is required the integration of the injection simulation results in programs able to carry out its structural analysis. This way, the finite element analysis programs, such as Simulia Abaqus, allow the determination of the mechanical behavior of a loaded part considering its manufacturing biography (in cavity stress field, residual strains, fiber orientation). The interaction between these software can be accomplished directly, or using external interfaces, like Helius PFA. This work aims to couple the manufacturing history of injection molded components, as well as the material experimental information, in the prediction of its loading behavior. Thus, this study intends to increase the accuracy of structural analysis performed on injection molded parts. Keywords: Injection Molding Simulation, Autodesk Moldflow, Finite Element Analysis, Simulia Abaqus, Residual Stress, Product Performance molded components, it’s required an upgrade on 1 Introduction the prediction of process resultant residual stress fields. The injection molding process causes structural changes in each component, which This work aims for two fundamental subsequently modify its performance under a accomplishments. The first one is the service load. These changes are caused by the optimization of forecasting injection molded accumulation of stress during the part’s filling in components’ loading behavior, which results on the mold cavity, resulting on warpage that the improvement of the prediction of process deforms its geometry after manufacture. Thus, resultant residual stress distribution. This is the component’s deformation and shrinkage intended to be achieved coupling the parts’ generate residual stress fields, functioning as an manufacturing history in its structural analysis indicator of the effects caused by the and, subsequently, evaluating its effects on the manufacturing process on the part’s structural product performance. The second integrity. Therefore, in order to accurately accomplishment of this work is to increase the reproduce the loading performance of injection accuracy of structural analyses of injection 1 molded components, using the material competitiveness of this market, emerge as the experimental data as well. major drawbacks of this process. 2.1.1 Residual Stress 2 Background By definition, residual stresses are elastic stress fields that remain in a solid material 2.1 Injection Molding Process without any external loads or temperature The injection molding process is one of the gradients applied. These stresses are the result of most common manufacturing techniques for the the part’s deformation and shrinkage after its mass production of polymer components. It is ejection from the mold, when the in cavity based on four major stages [1]: constraints are released. Furthermore, residual stresses have a similar effect on a structure than 1. Filling - Initially the polymer contained externally applied forces, which can lead to the in a hopper, usually in the form of pellets, part’s resistance reduction and, ultimately, its is leaked to the surface of a rotating early failure. There are two kinds of residual screw that pushes it into the mold. The stresses: the flow induced and the thermal screw rotation causes the contact of the induced [2]. plastic pellets with the hot cylinder walls, melting due to the heat of compression, The flow induced residual stresses are the friction and the high surface developed during the filling phase. Subsequently, temperature. When there is enough they are the result of contact between the oriented molten material in the screw end, it and disoriented layers of material, due to high paralyzes and injects the molten plastic cooling rates and shear stresses [2]. in the mold cavity through a feed system; The thermal induced residual stresses 2. Packing – this phase begins when 95% to are the result of the part’s unbalanced cooling 98% of the cavity has been filled. This and differential shrinkage [2]. moment is called the velocity/pressure switch-over point, when there is a 2.1.2 In-Cavity Stress Field switch-over from ram speed control to packing pressure. During this phase, While the component is still confined further pressure is applied to the material into the mold cavity, the internal stress field that in an attempt to pack more material into is developed during the material solidification is the cavity. This is intended to produce a called in-cavity stress. In practice, in-cavity reduced and more uniform shrinkage stresses are the driving force of the part’s with less component warpage. warpage and shrinkage after ejection [2]. 3. Cooling – Simultaneously, the mold is 2.1.3 Residual Strain cooled down using a coolant to lower the temperature of the plastic part. Once the The configurations before and after the polymer solidifies, the cavity pressure is part’s ejection are exhibited in Figure 1. In A the reduced to atmospheric pressure. This part is still confined into the mold cavity, while stage ends when the part reaches a safe cools down to achieve room temperature. Using extraction temperature; the Hooke’s Law of equation (1), the stress and 4. Ejection – Finally, when the component strain fields of configuration A are easily is fully solidified, the mold is opened and obtained (equation (2)). In this configuration the the part is ejected. The mold is then resulting stress field, {휎퐴}, is nonzero, unlike the closed so that a new cycle can begin. strain field, {휀퐴}. However, there are residual strains, {휀푛푚}, due to shrinkage when the part is The injection molding process has many into the mold, calculated using the in-cavity advantages, such as its suitability to large stress field, {휎퐴} (equation (2)) [3]. production volumes, obtaining complex geometry parts that require fewer finishing When the mold is removed the scheme operations. However, the high cost of the B it’s obtained, in which the part warps and required equipment and the great develops residual stresses, {휎퐵}. This way, the 2 effect of residual strain can be incorporated in the These tensor’s eigenvectors indicate the residual stress field calculation (equation (3)), main directions of fiber alignment, assuming that accounting for process resultant shrinkage [3]. the material is orthotropic. Thus, its eigenvalues provide a measure of the degree of fiber { } [ ]{ } 휎 = 퐶 휀 (1) alignment of the material. A perfectly aligned {휎퐴} = [퐶]({휀퐴} − {휀푛푚}) ⇔ composite has fiber orientation tensor eigenvalues of (1,0,0), unlike a randomly aligned ⇔ {휀 } − [퐶]−1{휎 } = {휀 } ⇔ 퐴 퐴 푛푚 (2) material, whose eigenvalues are (1/3,1/3,1/3) [3]. ⇔ {휀 } = −[퐶]−1{휎 } 푛푚 퐴 (4) 푎푖푗 = ∫ 푝푖푝푗휑(푝)푑푝 {휎퐵} = [퐶]({휀퐵} − {휀푛푚}) (3) (5) 푎푖푗푘푙 = ∫ 푝푖푝푗푝푘푝푙휑(푝)푑푝 2.2.2 Mori Tanaka micro-mechanics Model The mechanical properties of fiber reinforced materials depend on the direction, as a result of fiber alignment, being often called orthotropic materials. The micro-mechanical models provide a theoretical way to obtain the mechanical properties of a composite based on properties of its constituents (matrix and fibers). The Mori Tanaka micro-mechanical Figure 1 – Stress and strain fields before and model is widely used to calculate the mechanical after the part’s ejection [3]. properties of a composite material. Initially, the matrix and fiber constituent materials stiffness 2.2 Injection of Fiber Reinforced matrixes are combined (퐶푚 and 퐶푓, respectively) in order to obtain the composite stiffness matrix, Thermoplastics 퐶퐶, as shown in equations (6) to (8). Afterwards, A fiber reinforced material, also named this model calculates the material mechanical as a composite, is a combination of two properties using the Hooke’s Law in equation constituent materials: the matrix and the fibers. (1). Therefore, the matrix main function is to keep the 퐶퐶 = 퐶푓 + 푣 (퐶푓 − 퐶푚)퐴 (6) fibers together, securing them and acting as a 푓 −1 (7) mean of load transfer. There are short and long 퐴 = 푇[(1 − 푣푓)퐼 + 푣푓푇] fiber reinforced materials, as well as different 푇 = [퐼 + 푆(퐶푚)−1(퐶푓 − 퐶푚)]−1 (8) fiber orientations available (for instance, perfectly aligned or randomly aligned). Nevertheless, 푆 represents the Eshelby Composite materials are in fact commonly used tensor, 퐴 is the strain concentration tensor and is in the injection molding process, in order to 푣푓 the fiber volume fraction. improve components’ stiffness, resistance and other mechanical properties [4]. 2.3 Numerical Analysis Tools 2.2.1 Fiber Orientation Tensor 2.3.1 Injection Simulation The second and fourth order fiber orientation tensors, shown in equations (4) and The selected software to perform (5), provide a statistical description of the injection simulations was Autodesk Moldflow direction of the fibers in a certain point of the Insight 2016. This software allows the user to domain. This way, the probability density simulate the various steps of the injection function, 휑(푝), describes the behavior of a set of molding process, through different analysis fibers in a given direction [5]. modules that can be used alone or sequentially, 3 such as filling, packing, cooling and warpage.
Details
-
File Typepdf
-
Upload Time-
-
Content LanguagesEnglish
-
Upload UserAnonymous/Not logged-in
-
File Pages11 Page
-
File Size-