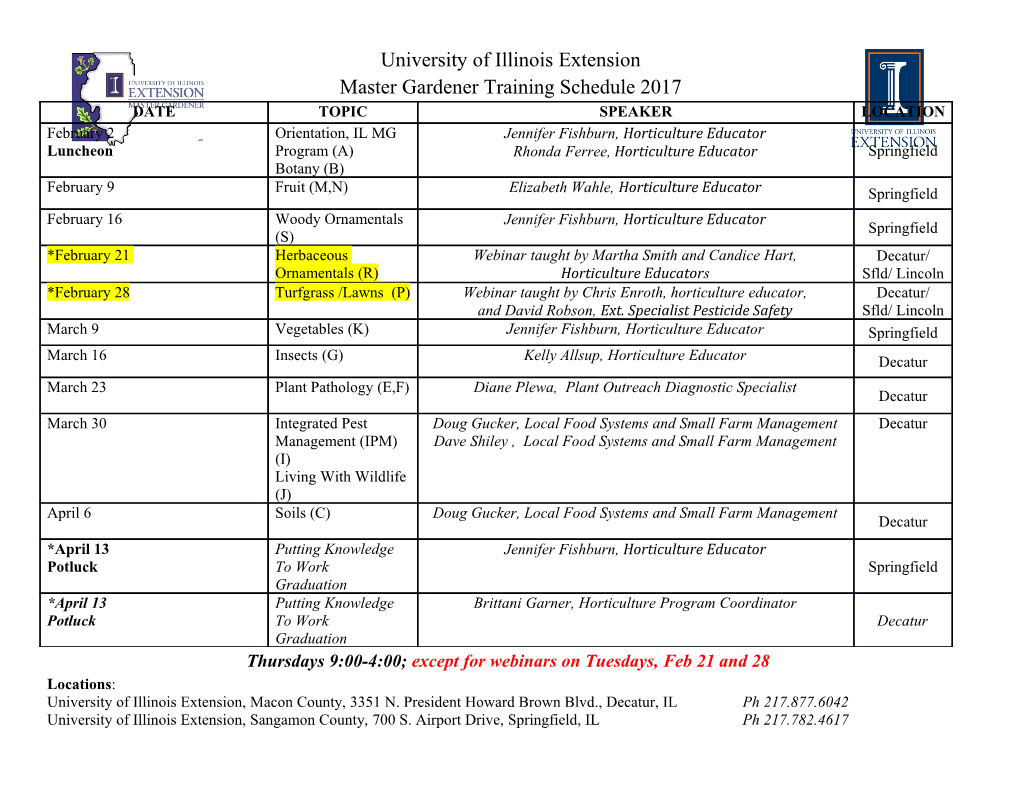
A prototype phasing camera for the Giant Magellan Telescope Srikrishna Kanneganti*a, Brian A. McLeod*a, Mark P. Ordwaya, John B. Roll, Jr.a, Stephen A. Shectmanb, Antonin H. Bouchezb, Johanan Codonac, Roger Enga, Thomas M. Gaurona, Timothy J. Nortona, Phil Streechona, David Weavera aHarvard-Smithsonian Center for Astrophysics, 60 Garden St., Cambridge, MA 02138; bGiant Magellan Telescope Corporation, P.O. Box 90933, Pasadena, CA, 91109-0933; cSteward Observatory, University of Arizona, Tucson Arizona, 85719 ABSTRACT Achieving the diffraction limit with the adaptive optics system of the 25m Giant Magellan Telescope will require that the 7 pairs of mirror segments be phased. Phasing the GMT is made difficult because of the 30-40cm gaps between the primary mirror segments. These large gaps result in atmospheric induced phase errors making optical phasing difficult at visible wavelengths. The large gaps between the borosilicate mirror segments also make an edge sensing system prone to thermally induced instability. We describe an optical method that uses twelve 1.5-m square subapertures that span the segment boundaries. The light from each subaperture is mapped onto a MEMS mirror segment and then a lenslet array which are used to stabilize the atmospherically induced image motion. Centroids for stabilization are measured at 700nm. The piston error is measured from the fringes visible in each of the 12 stabilized images at 2.2 microns. By dispersing the fringes we can resolve 2! phase ambiguities. We are constructing a prototype camera to be deployed at the 6.5m Magellan Clay telescope. Keywords: segmented telescopes, piston measurement, adaptive optics 1. INTRODUCTION The Giant Magellan Telescope (GMT) will be comprised of seven 8.4-m diameter primary mirror (M1) segments paired with seven adaptive secondary mirrors (M2)1. To reach the diffraction limit of the 25m telescope, each of the seven segment pairs must have exactly the same spacing. Existing segmented telescopes such as the Keck Telescope have relied on edge sensors located in the gaps between the segments to provide the necessary control. The Keck edge sensors are stable enough that they are calibrated interferometrically on sky only at month-long intervals2,3. The GMT segment phasing is more difficult for several reasons. The 30-40cm segment gaps combined with the fact that the mirrors are made of borosilicate glass (non-zero thermal expansion) leads to the concern that a metrology system mounted to the edges of the segments will not be stable enough on timescales longer than a few minutes to maintain the necessary ~30nm differential piston required to meet the GMT adaptive optics error budget4,5. While the metrology systems being designed6 may ultimately have the necessary long-term stability, the baseline plan is to continuously monitor stars at intervals of 60 seconds to maintain the calibration of the high-bandwidth metrology systems7. When the AO system is operating in natural guide star mode, the piston measurements will be derived from the on-axis star as sensed by a pyramid sensor8. However, when operating in laser guide star mode there are no available stars close enough to the optical axis to maintain the required phase coherence between segments. This led us to an approach where we would measure the differential piston across the segment gaps using stars several arcminutes off-axis. We form Young’s double slit images from the twelve 1.5m square subapertures that span segment boundaries. By limiting the measurement to a small subaperture, correcting the tip-tilt of the wavefront in each subaperture, and measuring the fringes in the K-band, enough fringe contrast is preserved to make the necessary piston measurement9 (see Figure 1). *Contact information: [email protected] ; [email protected] We thus set out to build a prototype of such a system and test it on sky to show that we could make piston measurements of the required accuracy using stars of typically available brightness. As the work progressed, a further complication was realized. If the M1 segments tilt with respect to each other (as they will naturally do from flexure due to gravity), and the M2 segments are tilted to compensate, an un-sensed piston variation with field angle will arise. The M1 and M2 metrology systems do not quite have the sensitivity and stability to sense the tilts independently, and no optical test is possible. Thus we were forced to conclude that high-accuracy piston measurements far off-axis would not result in a phased telescope on-axis. This is a problem that is fundamental to telescopes where both M1 and M2 are segmented. The current plan then is to make the piston measurement close to the optical axis using a pyramid sensor in the science instrument with a fainter star10. To be sensitive to piston, the star must corrected with an open-loop deformable mirror using a wavefront derived from the laser tomographic reconstruction. Because this on-instrument pyramid sensor is insensitive to 2! phase ambiguities we will maintain the off-axis piston sensor using it in a dispersed mode, but now requiring lower sensitivity. We have carried the prototype effort forward, adding a dispersion mode to it. Tip-tilt correction of the subapertures is still required to maintain fringe contrast. Thus, in section 2 we describe the instrument. In section 3.1 we describe analysis and lab results for the non-dispersed mode. The parts for the dispersion mode arrived recently and we report initial lab results in section 3.2. As of this writing, the instrument is in transport to Chile where we plan to test it on the Magellan Clay Telescope. Figure 1. Phasing subapertures superposed on GMT pupil (left), and resulting images formed from the marked subaperture with varying amounts of piston between the segments (right). 2. INSTRUMENT DESCRIPTION The instrument will be located on the East Nasmyth platform of the Magellan Clay telescope. The optics are all mounted on an optical bench, which in turn is mounted on a cart with casters. Between the optical bench and the cart are a set of ball transfer plates which allow fine adjustment of the location of the instrument relative to the telescope. The instrument is not bolted onto the Nasmyth rotator, but instead operates in a gravity invariant mode. An overall view of the optics is shown in Figure 3, with a close up view in Figure 4. In the sections below we describe the optical components, following the light from where it enters the instrument, through warm reimaging optics and then into the cryostat where it is split by wavelength and reimaged onto CCD and IR detectors. Figure 2. Photo of the phasing camera prototype. Figure 3. Overall view of instrument optics. 2.1 Focal plane assembly Light source/pinhole For lab testing we insert into the beam at the telescope focus location an incandescent light source shining through a Melles-Griot 10 "m pinhole. The pinhole assembly is on a manually actuated stage to move it in or out of the beam. On the same stage as the pinhole is a mirror with a 0.7mm diameter hole in the center. This 2 arcsec diameter hole will pass light from the telescope into the instrument. The outer parts of the field will be directed to an acquisition camera. Because the mirror feeding the acquisition camera is at the focal plane, the optical quality does not have to be very good. Thus, we use aluminum reflector panel, in which it is easy to drill the on-axis hole. The acquisition camera is a StellaCam3 video camera connected to an Axis M7001 Ethernet-based video encoder. The camera is capable of operating at video rates or delivering still images. Out-of-the-box it comes with a streaming video web interface. It can also take single exposures with controllable exposure time. Figure 4. MEMS relay and cryostat optics 2.2 Warm optics The first set of reimaging optics is warm and converts the f/11 beam to f/27. This produces an image scale nearly identical to what the GMT will produce. It also provides a convenient collimated beam in which to introduce a turbulence phase screen and phase step components. We test the system in closed loop using a Kolmogorov phase screen on a rotary stage, all manufactured by Lexitek. The pupil scale projected at the phase screen is 1.3mm/meter. We have two annuli with equvalent r0(500nm)=0.15m and 0.10cm. Our lab tests were conducted with the plate rotating to give an equivalent windspeed of 17m/s, which is somewhat worse than the median speed integrated over all altitudes. Because the experiment is being carried out on a monolithic telescope, we must artificially provide a phase difference between halves of the phasing aperture. A phase discontinuity can be introduced by inserting at a pupil plane two pieces of glass with identical thickness adjacent to each other in the beam. With a 3mm thick window and a microstepping motor, phase differences from 10nm to >25 microns can be introduced. Microstepping non-linearity is eliminated with a high resolution encoder that is attached to the motor shaft. To characterize how accurately we can measure a phase difference of zero, we can translate the phase adjuster completely out of the beam. Figure 5. Phase adjuster assembly with fixed and rotating glass windows (blue). The entire assembly is mounted on a slide for removal from the beam. 2.3 MEMS Assembly The MEMS relay (see Figure 6) consists of an Aluminum coated 100mm radius spherical mirror in double pass fed by two 5mm right angle prisms. This Offner-style relay forms a pupil on the MEMS mirror.
Details
-
File Typepdf
-
Upload Time-
-
Content LanguagesEnglish
-
Upload UserAnonymous/Not logged-in
-
File Pages10 Page
-
File Size-