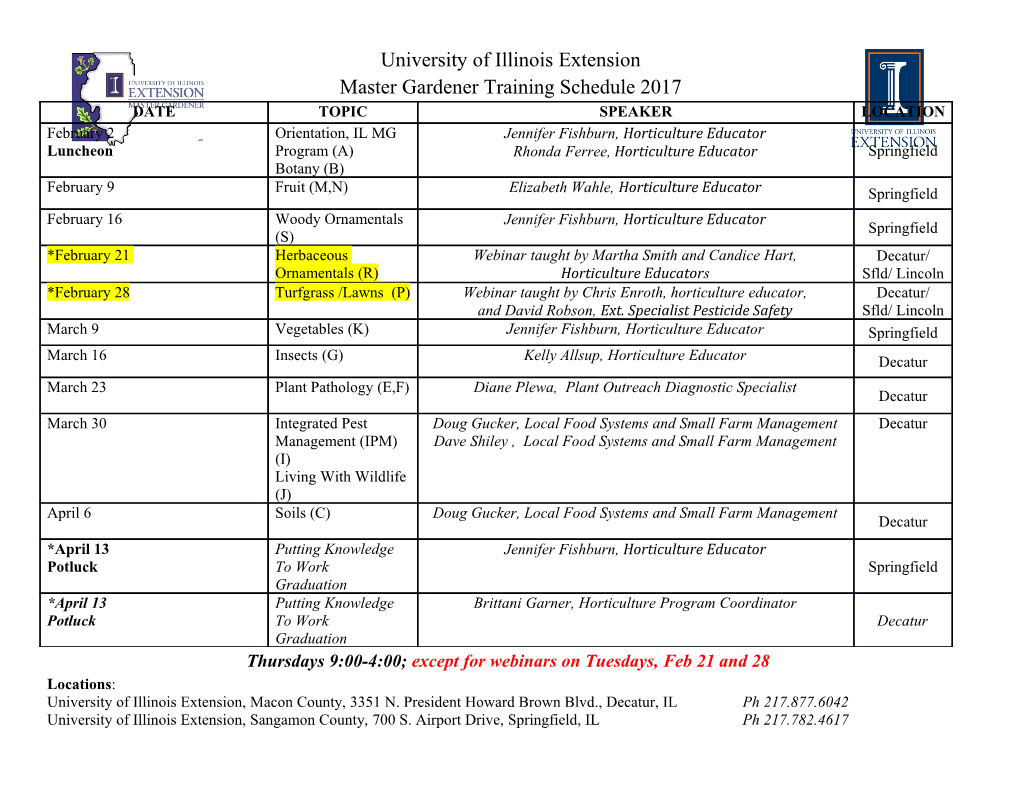
Chalmers Formula Sailing High Performance Skiff Marine Design Project 2017 Naval Architecture and Ocean Engineering International Master Programme Department of Mechanics and Maritime Sciences CHALMERS UNIVERSITY OF TECHNOLOGY Gothenburg, Sweden 2017 Chalmers Formula Sailing High Performance Skiff Marine Design Project 2017 Acerbi, Tommaso Andersson, Rasmus Eriksson, Eric Granli, Simon Jacobs, Eike Rita, Francisco Sahlberg, Robert Werner, Emanuel Chalmers Formula Sailing High Performance Skiff Marine Design Project 2017 Department of Mechanics and Maritime Sciences Chalmers University of Technology SE-412 96 Göteborg Sweden Telephone +46(0)31-772 1000 Printed by Chalmers Reproservice Gothenburg, Sweden, 2017 ii Abstract The 1001VELAcup is a sail race between European universities that takes place annually in Italy. The current report addresses the design and construction of a high performance sailing skiff to allow Chalmers University of Technology to participate in the race. The design is regulated by the Class Rule R3 and the current skiff is mainly inspired by the Olympic class 49er©. According to the class rules, the hull shall have a content of natural material of at least 70%. This is achieved by using a sandwich material with a balsa core and a composite from flax (linen) fibres, and an epoxy resin based on the shell of cashew nuts. Since there are no restrictions in draft or height of mast, this skiff has a relatively high mast and deep centreboard. All parts of the design are based on analyses of the race area in Mondello, outside of Palermo, in Sicily. Thus, the team chose to not use hydrofoils on the centreboard and rudder. The sail area is maximised according to the class rules. The work is carried out by eight students on the master program Naval Architecture and Ocean Engineering with supervision from teachers and experts from the industry. Keywords: skiff, dinghy, sailing, 1001VELAcup, Chalmers University of Technology, CDIO iii Preface and Acknowledgement The Marine Design Project, MMA 151, is a mandatory 15 credits course within the master program Naval Architecture and Ocean Engineering at Chalmers University of Technology. The course is organised by the Department of M2, Mechanics and Maritime Sciences at Chalmers. The objective of this project is to design and build a high performance racing skiff in order to compete in the upcoming 1001VELAcup 2018. Furthermore the participants have to manage the public relation work in addition to the whole process. The project members would like thank and acknowledge the help, funding, expertise and sup- port of the following: To Lars Larsson, Adam Persson, John Mcveagh, Per Wretlind, Henrik Ottoson, Per Hogström and Rolf Eliasson, thank you for the guidance, knowledge and expertise through- out the duration of the project. To Per Hogström and Lars Larsson, thank you for providing us the opportunity to work with such a unique project and for providing us with Ritsalen. This project would have been significantly more difficult without it. To our sponsors and partners in the project: Seldén Mast, North Sails, SSPA, the ITH project supported by the EU regional fund, Chalmers Foundation "Fond för högskolans bästa" and Area of Advanced Materials at Chalmers. To Professor Kai Graf for supplying his VPP. To SSPA, for general support and SNIC (Swedish National Infrastructure for Computing) for computing resources To our classmates, working alongside us and providing the good atmosphere and com- panionship. To Chalmers University of Technology. Project Members CAD Simon Granli Francisco Rita CFD Tommaso Acerbi Robert Sahlberg FEM Eric Eriksson Emanuel Werner VPP Rasmus Andersson Eike Jacobs v Executive Summary The following section is a brief outline of the work accomplished in the project. The mission profile, main particulars for the skiff and a general overview of its rig and sail set up are presented in this section. Mission Profile The mission of this project is to design and build a high performance racing skiff in order to participate in the 1001VELAcup. The regatta will take place in the bay of Mondello, Italy, at the end of September 2018. Main Particulars The dimensions of the skiff are set by the competition regulations as well as performance and structural optimisation. Since the goal is to finish in 1st place in the competition the focus has been on performance and hence the looks of the skiff are purely a result of that. Type High Performance Racing Skiff Flag Sweden Class R3 Hull Dimensions Length over all 4.60 m Beam of canoe body 1.22 m Beam 2.10 m Draft of canoe body 0.17 m Total draft 1.70 m Displacement 250 kg Moment of Inertia of the water-plane area 1.664 · 10−1 m4 Rig Dimensions Mast height 9.50 m Mainsail 16.0 m2 Jib 6.0 m2 Gennaker/Jib 0 11.00 m2 vi vii List of Abbreviations Abbrevation - Description CDIO - Conceive, Design, Implement and Operate FLAT – The flattening of the main sail to empower it GA - General arrangement ISPRA - Istituto Superiore Per la Protezione e la Ricerca Ambientale kn - Knots MDF - Medium Density Fibreboard NACA – National Advisory Committee for Aeronautics ORC - Offshore Racing Congress PDF - Probability Density Function PLA - Polylactic acid Pre-preg - Pre-impregnated RANS - Reynolds-averaged-Navier-Stokes RANS - Reynolds-Avergaed-Navier-Stokes RSM - Reynolds Stress Method RSM - Reynolds Stress Model SF - Scale factor s.f. - Safety factor SST - Shear Stress Transport VMG – Velocity Made Good VOF - Volume of Fluid VOF - Volume of Fluid VPP – Velocity Prediction Program viii List of Varables Variable Unit Description A [m2] Planform area a [m] Distance between forces AR [−] Aspect ratio AW A [◦] Apparent wind angle AW S [m/s] Apparent wind speed b [m] Distance between forces B [m] Beam Bmax, canoe body [m] Maximum beam of canoe body BS [m/s] Boat speed C¯ [m] Mean chord length C1 [m] Upper chord length C2 [m] Lower chord length CB [−] Block Coefficient CD [−] Drag coefficient CD,2D [−] Profile drag coefficient CDI [−] Induced drag coefficient Cf [−] Skin friction coefficient CL [−] Lift coefficient ◦ CL,2D,1◦ [−] 2D lift coefficient at 1 angle of attack CL,3D [−] 3D lift coefficient CE [m] Centre of effort CLR [m] Centre of effort of the appendages CoG [m] Centre of gravity ELT [MP a] Elastic modulus in the longitudinal-transverse plane ETV [MP a] Elastic modulus in the transverse-vertical plane EVL [MP a] Elastic modulus in the vertical-longitudinal plane EL [MP a] Longitudinal elastic modulus ET [MP a] Transverse elastic modulus EV [MP a] Vertical elastic modulus FDI [N] Induced drag force Fx,aero [N] Aerodynamic force in x-direction Fx,hydro [N] Hydrodynamic force in x-direction Fy,aero [N] Aerodynamic force in y-direction Fy,hydro [N] Hydrodynamic force in y-direction Fz,maststep [N] Force in z-direction at the mast step FD [N] Drag force FL [N] Lift force Fx [N] Force in x-direction Fy [N] Force in y-direction Fz [N] Force in z-direction F n [−] Froude Number g [m3/(kg · s)] Gravitational constant GM [m] Metacentric height 4 Ix [m ] Moment of inertia of the cross section ix 4 IxBS [m ] Moment of inertia of the cross section of the bowsprit 4 I49er [m ] Moment of inertia of the water-plane of the 49er© 4 IWP [m ] Moment of inertia of the water-plane area kDY N [−] Dynamic factor L [m] Length l [m] Distance on racks LBS [m] Length of the bowsprit that is unsupported LCF [m] Longitudinal Center Flotation LCG [m] Longitudinal Center of Gravity LOA [m] Length over all LW L [m] Length of Water Line mcrew [kg] Mass of the crew mtot [kg] Total mass Mx [Nm] Moment in x-direction My [Nm] Moment in y-direction Mz [Nm] Moment in z-direction P [N] Point load applied at the racks PBS [N] Point load applied at the tip of the bowsprit 2 pDY N [N/m ] Dynamic pressure 2 pfw [N/m ] Flat water pressure 2 p0 [N/m ] Uniform pressure ρBS [m] Density of the material composing the bowsprit R1 [N] Reaction force on the centreline R2 [N] Reaction force at the gunwale rBS [m] radius of the bowsprit’s cross section Re [−] Reynolds number Rex [−] Reynolds number at distance x from the stagnation point RM [Nm] Righting moment RM˜ [Nm] Righting moment approximation RMR [Nm] Righting moment from the crew on the racks RM˜ R [Nm] Righting moment approximation from the crew on the racks RMT [Nm] Righting moment from the crew in the trapeze RM˜ T [Nm] Righting moment approximation from the crew in trapeze σBS [P a] Stress at a bowsprit section σu [P a] Ultimate stress S12,max [MP a] Maximum shear stress in the XY-/LT-plane S12,min [MP a] Minimum shear stress in the XY-/LT-plane SL,max [MP a] Maximum stress in the longitudinal direction SL,min [MP a] Minimum stress in the longitudinal direction SL [MP a] Stress in the longitudinal direction SLT,max [MP a] Maximum stress in the longitudinal-transverse plane SLT [MP a] Stress in the longitudinal-transverse plane ST,max [MP a] Maximum stress in the transverse direction ST,min [MP a] Minimum stress in the transverse direction ST [MP a] Stress in the transverse direction STV [MP a] Stress in the transverse-vertical plane SV [MP a] Stress in the vertical direction SVL [MP a] Stress in the vertical-longitudinal plane SF [−] Safety factor T [m] Draft t [m] Thickness of the boundary layer x tBS [m] Thickness of the bowsprit Tmax, canoe body [m] Maximum draft of canoe body Tmax [m] Maximum draft TK [−] Draft of the centreboard TCG [m] Transverse centre of gravity TCGcrew [m] Transverse centre of gravity of crew TR [−] Taper ratio TWA [◦] True wind angle TWS [m/s] True wind speed U∗ [m/s] Friction velocity U∞ [m/s] Freestream velocity U2,max [mm] Maximum deflection in the transverse direction U2,no17 [mm] Deflection in the transverse direction of layup No.
Details
-
File Typepdf
-
Upload Time-
-
Content LanguagesEnglish
-
Upload UserAnonymous/Not logged-in
-
File Pages163 Page
-
File Size-