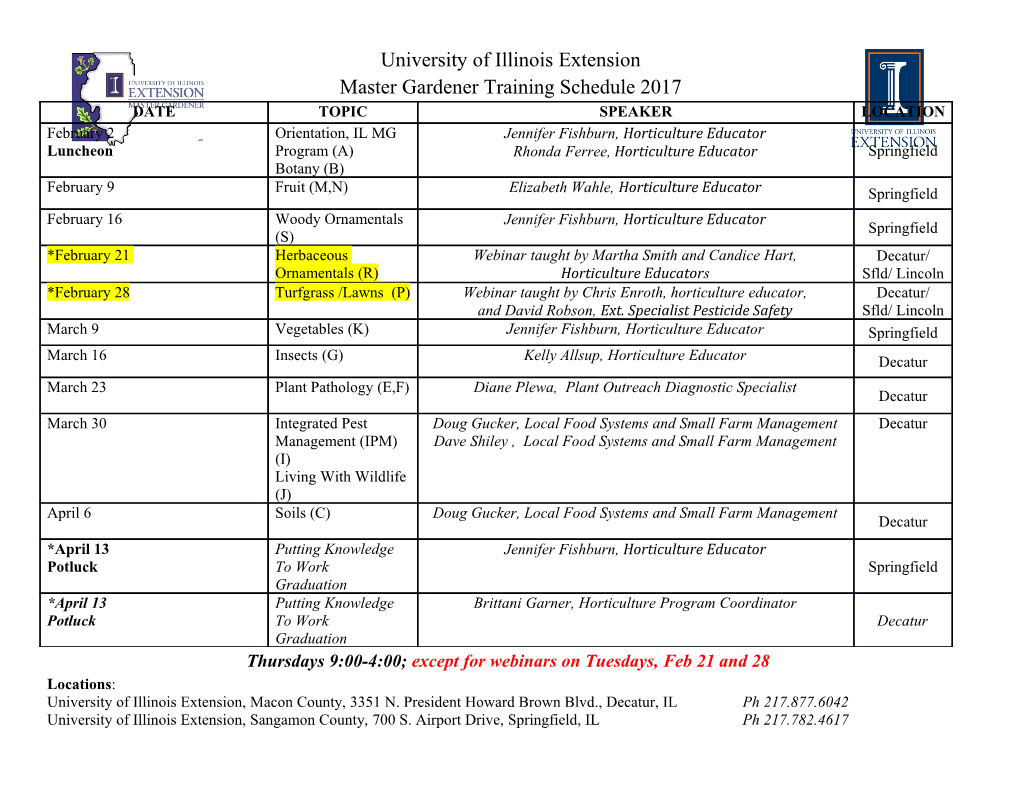
Electronically reprinted from August 2018 PVDF: A Fluoropolymer for Chemical Challenges When it comes to selecting materials of construction, keep in mind the favorable properties of fluoropolymers for corrosive service Averie Palovcak and Jason ince its commercialization in the Pomante, mid-1960s, polyvinylidene fluoride Arkema Inc. (PVDF) has been used across a Svariety of chemical process indus- tries (CPI) sectors due to its versatility and IN BRIEF broad attributes. With flagship applications PVDF AND THE in architectural coatings and the CPI, the FLUOROPOLYMER FAMILY breadth of industries where PVDF is utilized today is expansive. PVDF components (Fig- COPOLYMERS CHANGE ures 1 and 2) are utilized and installed where FLEXURAL PROPERTIES engineers are looking to maximize longevity PVDF COMPONENTS and reliability of process parts in many CPI sectors, including semiconductor, pharma- FIGURE 1. A variety of fluoropolymer components are shown ceutical, food and beverage, petrochemi- here cal, wire and cable, and general chemicals. change the performance properties. Fluo- PVDF and the fluoropolymer family ropolymers are divided into two main cat- PVDF is a high-performance plastic that falls egories: perfluorinated and partially fluori- into the family of materials called fluoropoly- nated [1]. The partially fluorinated polymers mers. Known for robust chemical resistance, contain hydrogen or other elements, while fluoropolymers are often utilized in areas the perfluorinated (fully fluorinated) poly- where high-temperature corrosion barriers mers are derivatives or copolymers of the are crucial. In addition to being chemically tetrafluoroethylene (C2F4) monomer. Com- resistant and non-rusting, this family of poly- monly used commercial fluoropolymers mers is also considered to have high purity, include polytetrafluoroethylene (PTFE), non-stick surfaces, good flame and smoke perfluoroalkoxy polymer (PFA), fluorinated resistance, excellent weathering and ultra- ethylene propylene (FEP), polyvinylidene violet (UV) stability. fluoride (PVDF), ethylene tetrafluoroethyl- Fluoropolymers have carbon and fluorine ene (ETFE), and ethylene chlorotrifluoro- as the main components of their chemical ethylene (ECTFE). backbone. Small changes in percent fluo- PVDF is a partially fluorinated polymer rination or addition of other elements may consisting of repeated units of the vinylidene 400 350 300 C) 250 o 200 Temperature ( Temperature 150 100 50 0 PTFE PFA FEP ETFE ECTFE PVDF Melting Degradation FIGURE 3. The processing temperature window for several fluoropolymers is shown here temperature requirements must be the crystallinity of PVDF, resulting in taken into account when processing added ductility and increased elon- most fluoropolymers. gation [5]. Varying amounts of HFP FIGURE 2. These fluoropolymer tower packings are used in distillation columns Unlike its fluoropolymer counter- can be reacted with VF2 to yield parts, PVDF is the most benign to broad ranges of flexibility. Table 2 fluoride (VF2) monomer [(C2H2F2)]. process. PVDF has the widest gap gives an example of the range of Standard PVDF homopolymer is between its melt temperature and its flexural moduli of PVDF, both homo- 59.4% fluorinated and PVDF copo- degradation temperature, as shown polymer and copolymer, compared lymers (described in later sections) in Figure 3. In fact, PVDF does not to other fluoropolymers. can reach up to 65% fluorination. require special equipment and can Variations in material flexibility re- Generally, the higher the fluorine be processed on standard equip- sult in a wider range of components content, the higher the chemical ment used to process polyolefins, available in PVDF materials. While resistance, as the carbon-fluorine such as polyethylene (PE) and poly- PVDF homopolymer has a long leg- bond is one of the strongest known propylene (PP). acy of use in piping, valves, pumps in chemistry. PVDF homopolymers and other applications that require can tolerate chemistries from a pH Copolymers flexural properties high mechanical rigidity, the PVDF co- of less than 1 up to 12 and PVDF While PVDF is the strongest of the polymer range has a variety of melt- copolymers can extend that range fluoropolymers up to 140°C, PVDF processed components, such as wire from much less than 1 up to 13.5. copolymers can bring added de- and cable jacketing (Figure 4), tubing, While PTFE, with its high melting grees of flexibility. Copolymerization hoses and gaskets, to name a few. point of 325°C, is well known as a is a true chemical reaction. It does liner for high temperature applica- not involve additives or stabilizers PVDF components tions, PVDF homopolymer has a melt that can leach out over time. Some As previously described, the proper- point between 165 and 172°C and of most common comonomers are ties of PVDF make it useful across a maintains a Underwriters Laborato- hexafluoropropylene (HFP), tetra- variety of applications. The following ries (UL) relative thermal index (RTI) fluoroethylene (TFE), and chlorotri- are just a few highlighted components rating of 150°C [2]. Table 1 shows the fluoroethylene (CTFE). HFP is a fully heat deflection temperature of fluo- fluorinated monomer that disrupts ropolymers with PVDF holding me- chanical integrity under pressure up to its usage certification temperature. Aside from PTFE, which is most often processed by sintering, most other commercial fluoropolymers are melt processable, and require high heat to process in a molten state [4]. Equipment used to make most fluoropolymer components must be therefore equipped to han- dle the associated thermal stresses. FIGURE 4. Wire and cable components are com- FIGURE 5. PVDF piping systems come in a various Special considerations related to monly made of fluoropolymers forms FIGURE 7. This flexible tubing is made from PVDF copolymers FIGURE 6. Electrofusion is one joining method of dards [8]. Piping systems for waste PVDF systems drainage applications along with wire FIGURE 8. PVDF fittings are one example of and cables made with PVDF are injection-molded pieces where PVDF materials are specified to widely specified in the plenum areas bring long-lasting solutions. of buildings. Electrofusion is a spe- to bind the PVDF to another mate- Piping systems. PVDF piping sys- cialized pipe-joining technique for rial, such as polyurethane or poly- tems (Figure 5) have a UL RTI rating that industry, where built-in electric ethylene. With PVDF as the fluid of 150°C (302°F) and are available in heating elements are used to weld contact layer on the inside and an various forms: solid piping, lined metal the joint together, thereby minimizing engineering polymer material on the piping and fiberglass-reinforced dual human error in fabrication. outside, the cost of the multilayer laminate piping. Unlike metals, PVDF While PVDF piping systems are construction may be more econom- is non-rusting and lightweight, mak- used in areas where high mechani- ical for some applications. ing installation easier. cal rigidity is crucial, flexible tub- Injection molded components. PVDF piping systems can be ing options are also available that Piping systems and flexible tubing joined by various welding tech- take advantage of PVDF copolymer are usually created via profile extru- niques. Socket fusion is a recom- technology (Figure 7). With flexural sion but injection molding is another mended method in the CPI, as the moduli down to 10,000 psi, tubing method to create components in strong weld creates a lap joint that is important in applications like bev- specialized shapes and dimensions. can resist harsh chemistries, such erage and fuel lines that can be uti- From pumps, nozzles, and valves, as hydrochloric, sulfuric, and nitric lized in many market segments. The PVDF components can be mass in- acids. Butt fusion, one of the easiest beverage industry appreciates mini- jection molded (Figure 8). Recently, types of joining methods, is a choice mal cross-contamination of taste, PVDF components are being molded in areas where the chemistries are making PVDF tubing a long-lasting for conveyor belting for food-pro- more benign. Beadless and smooth choice. Several PVDF copolymers cessing facilities. inner bore systems leave no weld- are FDA compliant per Title 21 CFR Traditional materials used in plas- ing bump, which make them ideal 177.2600 and are listed to NSF 51 tic modular belting have faced scru- methods for the pharmaceutical for food contact. For fuel applica- tiny recently due to plastic bits con- and semiconductor industries. Both tions, the barrier properties of PVDF taminating food [9]. With PVDF, the of these industries need a smooth are used for low permeation of hy- higher mechanical and abrasion surface to minimize bacterial hang- drocarbons in flexible fuel pipes, resistance combined with outstand- ups and ensure the highest levels such as applications compliant with ing chemical resistance have proven of purity. Mechanically joined and UL 971 Nonmetallic Underground to be a longer-lasting solution. Both threaded systems are utilized for ap- Piping for Flammable Liquids. Fluid rigid and copolymer grades of PVDF plications where systems are taken handling systems with PVDF can apart to be cleaned. PVDF piping also be created in multilayer con- can withstand sterilization with satu- structions, where a tie layer is used rated steam at temperatures [6] up to 150°C depending on the joining method and design. Flexible tubing. Flame and smoke additives can be added to PVDF res- ins to meet the
Details
-
File Typepdf
-
Upload Time-
-
Content LanguagesEnglish
-
Upload UserAnonymous/Not logged-in
-
File Pages4 Page
-
File Size-