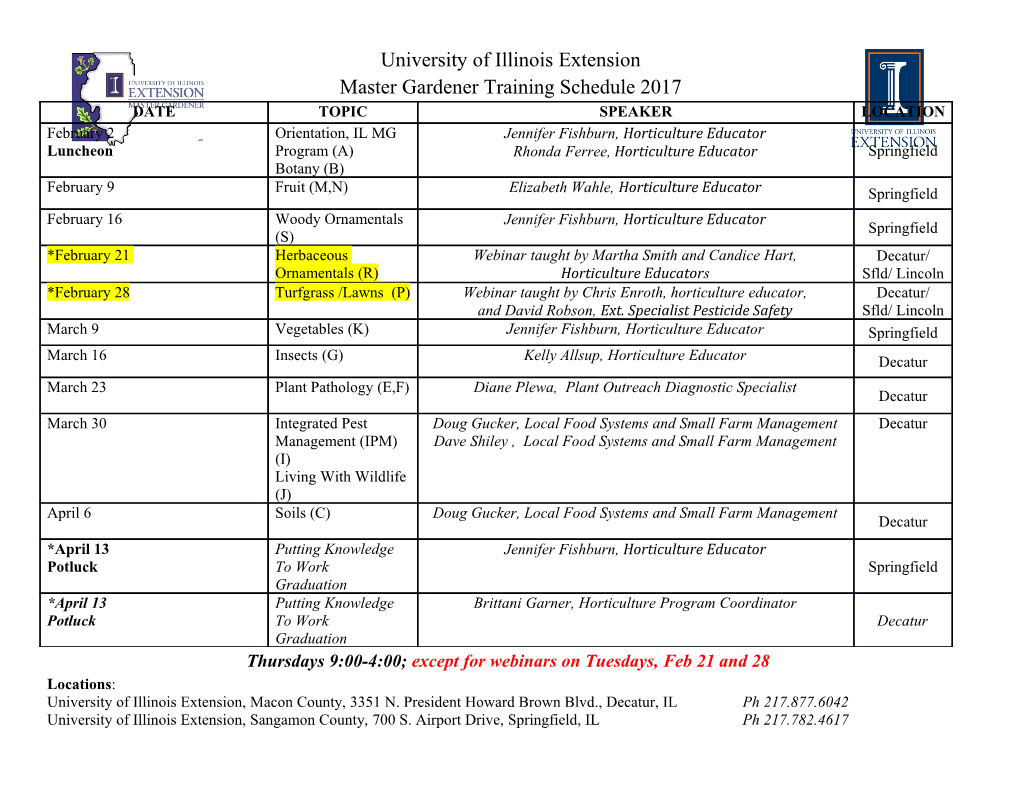
CONTENTS OF BOOK IV. , Page Removing a Barrel Hook ................................... 45 Making a Barrel Hook ..................................... 45 Inserting a Barrel Hook .................................... 45 Repairing the Mainspring .................................. 45 Inserting the Mainspring. 46 Stop Works . 46 To Set a Stop Work. 46 Carrier and Taper ......................................... 47 Centering and Making Carrier. 4 7 To Make the Pivot Rest ................................... 48 Polishing Pivots . 49 Bushing ................................................. 49 Making the Bushing. 49 Inserting the Bushing. 50 Side Shake . 50 Depthing . 50 Correcting the Depthing. 50 Soft Soldering . 51 Straightening a Wheel Tooth. 52 Inserting a Tooth ......................................... 52 Inserting a Tooth in a Barrel. 52 Truing Escape Wheel Teeth. 53 Truing in the Round. 53 Shaping the Teeth ......................................... 53 Refinishing Pallets . 53 The Fiber Disk. 54 Clock Escapements . 54 Dead Beat Escapement. 55 Recoil Escapement ........................................ 55 Anchor Pin Escapement. 55 How to Adjust the Escapement. 55 Assembling a French Clock with Visible Escapement. 56 Setting in Beat and Timing. 58 Copyright, 1914 and 1915, by JOHN DREXLER. REMOVING A BARREL HOOK. If the hook is found broken or too short, causing the mainspring to slip, scratch an arrow on the inside of the barrel to show which way the hook points, and drill a hole in the center of the hook about three-quarters its size. From the outside of the barrel, insert a broach in the hole, strike lightly with a hammer and turn it inward until the shell from the old hook is released from the bar­ rel. If the hook is not threaded, broach the hole in it until the shell drops out and cut a thread in the hole in the barrel with a suitable sized tap. MAKING A BARREL HOOK. Select a steel wire 1.5 m.m. thicker than the threaded hole and turn a shoulder on it 2 c.m. long, tapering grad­ ually toward the end, as shown in Fig. 70. Cut a thread from about midway on the taper up to the shoulder, that will fit the thread in the barrel, and leave the lower half of the taper so that it will easily slip into the barrel. Fasten in the lathe and cut off to the desired length. Then file the face of the shoulder to a slant as at X in B, Fig. 71. File the top to a slant (Y) and file the two sides flat and slanting, as S-8 in C, which is the top view of the hook. INSERTING A BARREL HOOK. Insert this finished hook in the hole from the inside of the barrel and fasten the end in a pin vise. Turn it outward until the slanted portion that is to hold the spring is flush with the inside of the barrel, and pointing in the direction of the arrow made. ( See Fig. 72.) Then cut off the remaining wire on the outside surface of the bar­ rel, file smooth and finish with an emery stick. REPAIRING THE MAIN SPRING. If the hole is torn on the outside end of the main­ spring ( See Fig. 73) draw the temper about 1 c.m. from the end of the spring. Cut off the torn part, round off the corners, and make a heavy punch mark. Flatten, and file the hole to right size. File the part of the spring that holds on the hook slanting, leaving the sharp part on the outside of the spring. If the hook has been properly fitted, the spring will lay against the wall of the barrel. 45 The inner end is repaired the same way. If the spring is broken more than one coil from the outer end, or two coils from the inner end, replace it with a new one, the same length, breadth and thickness. INSERTING THE MAIN SPRING. You will have no difficulty in inserting a mainspring if you follow these directions: Place three-quarters of a coil of the mainspring against the inner wall of the bar­ rel, with the end opposite to the hook, and turn the barrel until the spring hooks in its place. ( See Fig. 72.) Hold the barrel firmly in one hand, and the spring in the other, with a thumb partly inserted in the barrel, and with the aid of the forefinger, press the spring against the first coil inserted. Do not release the barrel or make sharp bends in the spring. Gradually work the spring into its place, and when there is no longer room for the thumb, insert the remaining coils without releasing the spring, as in Fig. 69. When the arbor is in its place, and the spring does not hook properly, bend the last coil inward with a half round plier. Place the cover into the barrel, clamp the barrel, wrapped with heavy paper, between the jaws of the vise, and screw the vise together until the cover snaps into its place. STOP WORKS. There are various kinds of stop works used to pre­ vent extreme winding, and unwinding, of the mainspring; but the explanation of one is sufficient. Fig. 74 represents a maltese cross stop work, which consists of a disk called the male, that has one long tooth, and a maltese cross, called the female, which has five sections, one of which is longer than the others. The male is pinned to the square of the winding arbor and the female is held loosely either to the plate or the barrel with a shouldered screw. TO SET A STOP WORK. Count the teeth of the female stop, and also the num­ ber of complete turns required to fully wind the main­ spring. Subtract the former from the latter and divide the remainder by two. Unwind the spring a number of turns equal to the result thus obtained, and place the male 46 in a notch, as shown in Fig. 74, with the point X of the female resting against it. This allows an equal amount of turns on each side of the stop work. (The left hand wind is set exactly opposite, that is, Y resting against the male, instead of X.) Slowly wind the spring and ob­ serve if the male engages freely in all the sections of the female and whether the diameter (D) passes easily in the curves ( S). If the action is not free, it must be made so by shaping. If the tooth ( M) is too short, stretch it with a hammer on a block, or if too long, file it to the proper length; also notice whether the screw that holds the female stop is secure. CARRIER AND TAPER. Owing to the fact that wheels are trued from their pivots, satisfactory truing of clock wheels cannot be done except by holding the pivots in female tapers, as shown in Fig. 75. Ordinary female tapers, that can be bought, afford no means of propelling the wheels; so we explain how to make a carrier which can be used for propelling the wheel while topping the teeth and polishing the pivots. The taper that is to fit into the taper chuck must be turned smooth with a gradual taper and must correspond with the inside taper of the chuck and tailstock spindle, or it will not hold firmly when polishing pivots, as it is necessary to apply a little pressure to the pivot burnisher. When thin arbors, especially those of French clocks, are to be held between the female centers, it will be advis­ able to make small brass, or soft steel, removable bushes, with different sized holes, so they can be changed to suit different thicknesses of pivots. CENTERING AND MAKING CARRIER. Before making the female tapers, you should know how to center. Find the center before drilling the holes in the wire by turning a V in the end to receive the drill. To insure a perfect V advance the graver gradually on the line toward the center, until the center is reached, and the V appears like M, Fig. 76. If the graver is not held in the center, a little projection will appear at the point 47 of the V ( See N, Fig. 76), which will prevent the drill from entering the center. Fig. 77 shows a square back center ( C), which is held in the tailstock spindle while drilling a hole in the center of a rod (R) at right angles to its length. For making the carrier use a taper blank that fits the taper chuck of the lathe. Insert it in the chuck and fasten in the lathe. With a graver find the center, and drill a hole with a No. 47 twist drill 5 m.m. deep. Turn away the outside edge of the hole 2 m.m. deep to a V shape, to receive the shoulder of an arbor. About 6 m.m from the V end, make a punch mark and drill a hole 2 m.m in diameter through the blank by holding the drill in a chuck and the blank in the grooved V of a square back center. ( See Fig. 77.) At right angles to this hole ( See Fig. 75) drill a second hole 1 m.m. in diameter to meet it. Cut a thread and fit a screw. This screw holds the rod in the first hole drilled, so that it can be adjusted for wheels of various sizes. In the end of a steel rod, 2 m.m. thick and 2 c.m. long, drill a 0.5 m.m. hole 2.5 m.m. deep, thread it and fit a screw. 2 m.m. back on the rod from the same end, drill a 1 m.m.
Details
-
File Typepdf
-
Upload Time-
-
Content LanguagesEnglish
-
Upload UserAnonymous/Not logged-in
-
File Pages19 Page
-
File Size-