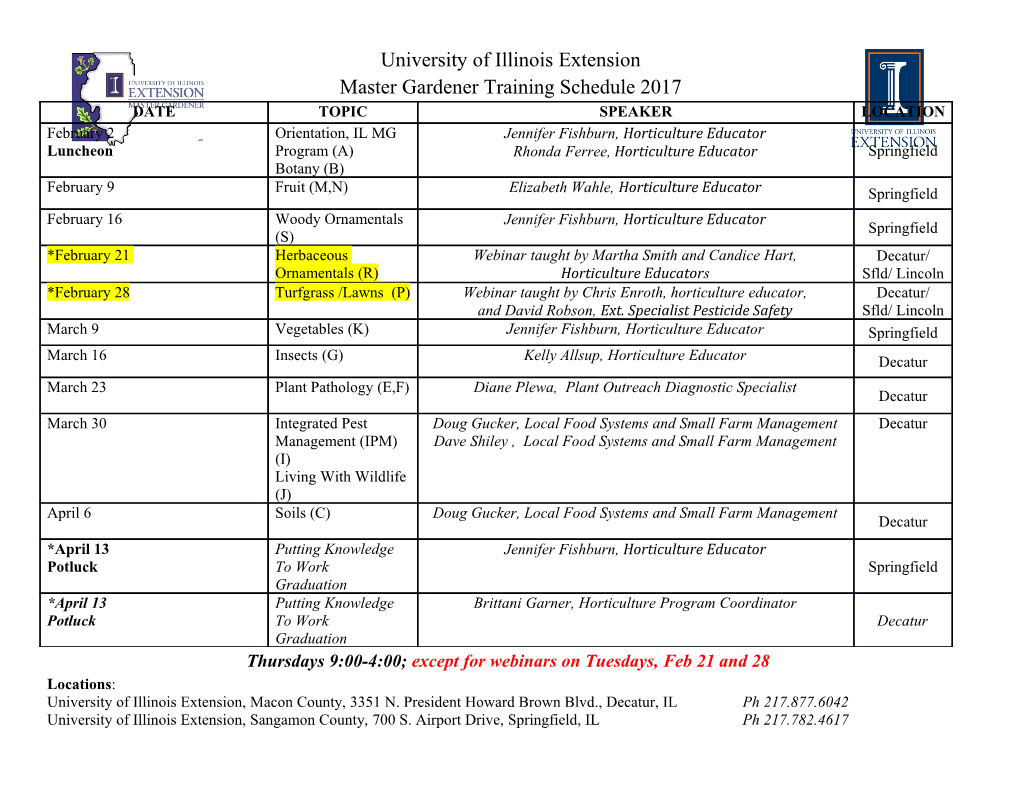
Aug. 22, 1972 J. K. GRUNG ET All 3,685,961 EXTRACTION OF BERYLLIUM FROM ORES Filed Dec. 21, 1970 2. Sheets-Sheet l CRUSHED BeO ORE PREGNAN SOLUTION ROD MLL SOLUBLE 's- 93% H2SO4 FLUORDE CRUDE HYDROXDE HYDROYSS p .. 4 BATCH ACD LEACH — — F LTER - r --EDTA---- BATCH PRECIPITATION FLTRATE E itA CAKE ---REGENERATION F LTER LOAD TANK ----- - - - - SO. No OH O.M (NH4)2SO SUMP- Co (OH)2 -- Not To WASTE CAUSTC F LTRATE an D GESION WASHTANK F TRATE H2S--- WASHINGS SULFIDE PRECIPITATION | FLER -- SOLD RESOUE - To TALINGS FLER f - PRECIPITATE y L - CAKE FRATE 5Oe non REPULPER -- FILTER CAKE FLRATE DEONIZED WATER FLAKE NOH REPULPER FLTER ck. FTRATE To WASTE IN VENT ORS JAMES K. GRUNG WLLA M B. DAVS F. G. WLLA M. C. ATKENHEAD Y k e... 1 (c. -ie (tal. ''. y A-. Attorney'S Aug. 22, 1972 J. K. GRUNG T AL 3,685,961 EXTRACTION OF BERYLLIUM FROM ORES Filed Dec. 2, 1970 2 Sheets-Sheet 2 -- (PROCEDUREB) -- - - -- s ES5 -- DEONZEO H. ula. 2O conversion DLUTION |Procedure? O% Na2S 4 FTER f–98% H2SO4. CONVERSIONSULFATE SULFDIZATIONT -------sif.spshf-- -- -NHs FILTER FLTRATE CAKE HYDROXDE v. -PRECIPITATION Sind F REMcVAL CONC. SULFURICf-H2SO4 CAKE FLTRATE siana inf ses ACD TREATMENT CHELATION EDTA-- -- DiscARD NH HOLDING. ANK (Boil) -T-NHs CHELATON 3 T------------ --- Y - H2SO4. "' DEERYLLIZATION (PRoceDURE c) ----- - CONC. SUFURC A CD TREATMENT DECANTAON TANK -- - - - - - DEONIZED H2O WASHER SETTL NGS DE CANATE - Decantate- t SELNGS F LTER DEONIZED "so FILTER CAKE FRAE f To DiSCARO FLTRAE CAKE To DSCARD To OSCARD style DRYER DRED'Be (OH)2 Be (oh). PRODUCT calcation Be O PRODUCT NVENTORS JAMES K. GRUNG WLLAM. B. OAWS F G 2 WL AM C. ATKENHEAD BY wa AORNEYS 3,685,961 United States Patent Office Patented Aug. 22, 1972 1. 2 tion it becomes necessary to provide a large autoclave ca 3,685,961 pacity to handle the large volume of leach liquor. The cost EXTRACTION OF BERYLLUM FROM ORES for the construction of the autoclaves, therefore, requires James K. Grunig and William B. Davis, Tucson, Ariz., a large capital expenditure. and William C. Aitenhead, Belize City, British Hon 5 S. assignors to The Anaconda Company, New York, SUMMARY OF THE INVENTION Continuation-in-part of application Ser. No. 710,984, Mar. 3, 1968, which is a continuation-in-part of In the process of the present invention, beryllium bear application Ser. No. 316,474, Oct. 15, 1963, now ing material containing aluminum, iron, fluorine, and other Patent No. 3,395,975. This application Dec. 21, O impurities is leached with a mineral acid at a pH in the 1970, Ser. No. 99,753 range from 1.2 to 2.0, to extract the beryllium and a mini nt. C. C22b 59/00 mum of impurities from the material. The acid slurry then U.S. C. 423-127 2 Claims is heated and its pH carefully raised to above 3.0 but be low about 4.5, and preferably below 4.0, to cause the pre cipitation of fluoro-compounds of aluminum and com ABSTRACT OF THE DISCLOSURE, pounds of iron. The precipitates are separated from the The extraction and the recovery of beryllium substan leach liquor by filtration and the pH of the filtrate is then tially devoid of zinc and other impurities from low and further raised to above 7.5 but below 9.0 causing the pre medium grade acid-leachable beryllium bearing ores is cipitation of beryllium from the solution. A minor amount accomplished by acid leaching at a pH in the range from 20 of impurities are also concurrently precipitated. In ac 1.2 to 2, preferably between 1.3 and 1.5, and advan cordance with this invention, the beryllium precipitate is tageously with the aid of a soluble fluoride additive, fol recovered and digested in a sodium hydroxide solution. lowed by raising the pH of the leach liquor in two suc The beryllium in the sodium hydroxide solution is treated cessive steps, initially to below about 4.5 and finally to with a soluble sulfide, preferably sodium sulfide, to pre below 9.0, to precipitate beryllium hydroxide relatively cipitate zinc and any other heavy metal impurities still free from impurities. In the initial pH raising step, alu 25 present, and the precipitate is recovered by filtration. The minum is precipitated from the leach solution. The pre filtrate is then hydrolyzed and reprecipitated as beryllium cipitated beryllium hydroxide is further purified by redis hydroxide thus precipitating values rich in beryllium hy solution and hydrolysis in sodium hydroxide solution. Zinc droxide thus precipitating values rich in beryllium. is removed from the final beryllium product by treating the 30 sodium hydroxide solution with a soluble sulfide before DESCRIPTION OF THE DRAWINGS the hydrolysis of the redissolved beryllium hydroxide. FIGS. 1 and 2, taken together, are a flowsheet of a spe cific procedure and its alternatives for producing substan tially pure Be(OH)2. CROSS-REFERENCE TO A RELATED 35 APPLICATION DESCRIPTION OF THE PREFERRED This is a continuation-in-part application of our applica EMBODIMENT tion Ser. No. 710,984, filed Mar. 6, 1968, which in turn is a continuation-in-part of our application Ser. No. 316,- A number beryllium ores are suitable for treatment by 474, filed Oct. 15, 1963, entitled "Precipitation of Beryl 40 the method of the present invention, such as Spor Moun lium from Ore,” now Pat, No. 3,395,975. tain and Topaz Mountain ores. The beryllium Spor-Topaz ores is thought to be contained in the mineral bertrandite, BACKGROUND OF THE INVENTION BeSiO(OH), and in bery liferous saponite, a clay-like (I) Field of the invention mineral, both of which are soluble in moderate concen 45 trations of mineral acid. In contrast to bertrandite, beryl This invention relates to a process for the extraction (3BeOAlO'6SiO) and phenacite (BeSiO4), other and recovery of beryllium in the form of substantially forms of naturally occurring beryllium, are not readily pure beryllium compounds from beryllium bearing ores. soluble in moderate acid concentrations, but may be ren More particularly, this invention relates to a process for dered acid soluble by prior art processes including fluoride the extraction of acid-leachable beryllium values from ores 50 sintering or alkali fusion. Spor-Topaz ores are thus sus in a manner permitting easy separation of those values ceptible to leaching directly by mineral acid and may there from other mineral components in the ores. The process fore be advantageously used in the process of this inven of this invention is particularly suitable for recovering tion. Other ores containing beryllium values, when ren beryllium values from low and intermediate grade ores. dered acid-soluble by prior art methods, may also be used 55 in the process herein. (II) Description of the prior art Following is a detailed description of a beryllium Several processes for the extraction of beryllium values recovery operation embodying the invention, presented from ores have been developed, some of which are only with reference to the accompanying two sheets of draw suitable for acid-leachable beryllium values. In these prior ings which together show a single flowsheet of a specific art processes, it has been difficult to separate compounds 60 procedure and its alternatives for producing substantially of aluminum, iron, magnesium, and calcium from the pure Be(OH)2. The dotted line shows the alternative beryllium compound component. Hence, the final beryl procedures. lium product is rather impure. It has, heretofore, been Referring to the drawing, the beryllium ore (after it proposed to extract beryllium compounds from beryllium is ground to the desired size) is acid-leached with sulfuric bearing ores by leaching with acid, and then cauticizing 65 acid. Instead of sulfuric acid, hydrochloric acid may be the leach liquor and autoclaving it at high temperature used although sulfuric acid is preferable because of lower and pressure for the elimination of impurities such as costs. Spor-Topaz ores may be leached with conventional aluminum, iron and calcium from the beryllium bearing acid leach liquids having a pH substantially below 1.0, solution. While such prior method is economically at but in accordance with the invention, the ore is leached tractive for the high yield production of substantially 70 preferably with HSO4, the pH of the leach solution pure beryllium hydroxide, for a commercial scale opera being maintained above about 1.2 and below about 2.0 3,685,961 3 4. throughout the duration of the leaching operation. The The fluoride may be added directly into the ore prior temperature of the leach solution is in the range from to the addition thereto of the acid leach solution, or it about 160 F. to just below the boiling point of the leach may be added directly to the leach solution. Preferably, liquor, and the leaching operation proceeds for a period the fluoride addition is made soon after the major acid sufficient to dissolve substantially all the beryllium values addition to form the resultant slurry. The time at which in the material. Leaching may be at a temperature higher the fluoride may be added to the leach liquor, however, than boiling, in which case pressurized equipment is used. is not very critical as long as its addition provides free In the process the pH of the acid solution is maintained fluoride ions for the formation of beryllium fluoro above about 1.3 during one or more major portions of the complexes. leaching period, e.g., for periods of two to three hours O In addition to the aforesaid soluble alkali fluorides, at a time, so that the amount of impurities which leach certain soluble aluminum salts, particularly AIF, may from the ore and enter the leach solution, such as alumi be used as additives to facilitate the leaching operation.
Details
-
File Typepdf
-
Upload Time-
-
Content LanguagesEnglish
-
Upload UserAnonymous/Not logged-in
-
File Pages9 Page
-
File Size-