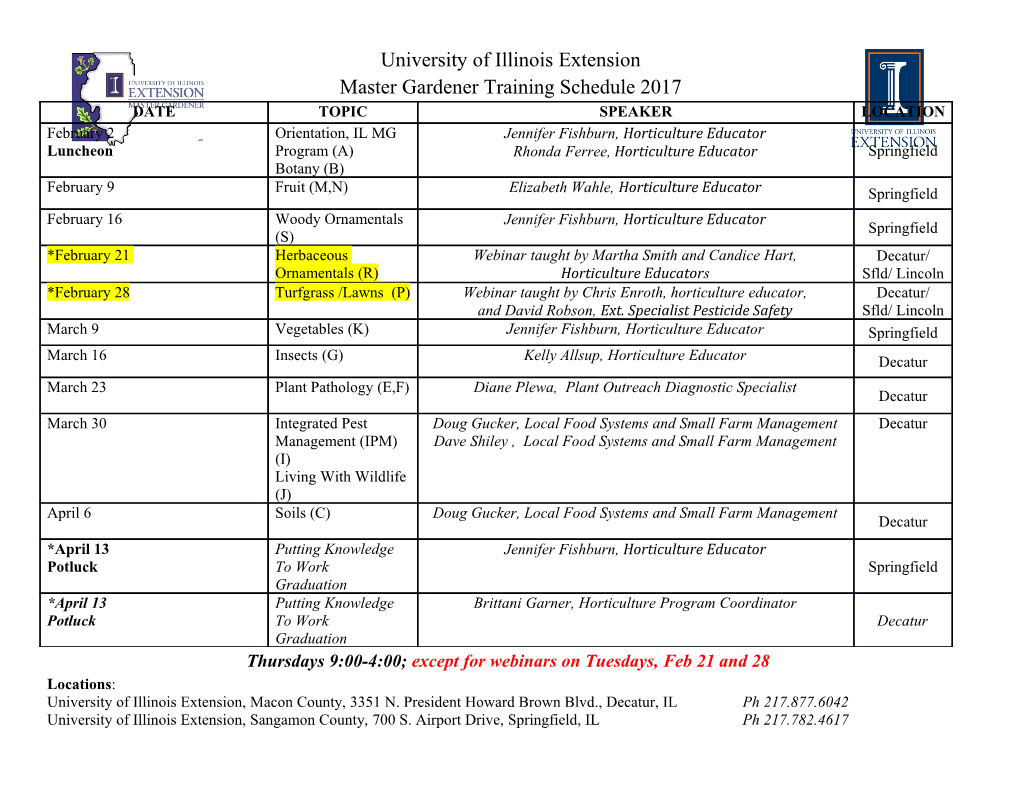
DETAIL TOOL 20 PROPRIETARY NOTICE THIS DATA AND INFORMATION DISCLOSED HEREIN IS PROPRIETARY DATA OF GULFSTREAM AEROSPACE CORPORATION. NEITHER THIS DATA NOR THE DATA CONTAINED HEREIN SHALL BE REPRODUCED, USED OR DISCLOSED TO OTHERS WITHOUT THE WRITTEN AUTHORIZATION OF GULFSTREAM AEROSPACE CORP. REVISION APPROVAL REV REVISED BY APPROVED BY DATE REV REVISED BY APPROVED BY DATE LTR LTR B Thomas Reimer Steve Richie 08/12/13 REVISION BLOCK Revision Applicability: Unless it is expressly indicated, the data in these revisions is not retroactive to parts, assemblies, installations, procedures, or processes that have been previously approved. Group Leads are required to review the revised material to determine the immediate impact it may have on the functions/processes within their group. Retro- Description Of Change Rev Section active B 510 Added information to Drill Hole Color Code section. NO REVIEW BLOCK The following area is used for periodic reviews of the SD20 document by designated personnel. The Documentation Group will review the comments and/or suggestions and may incorporate the information into the next revision of the document. Date Reviewer(s) COMMENTS OR SUGGESTIONS SECTION Contents PAGE 1 of 2 DETAIL TOOL 20 REVISION DATE __________________ TABLE OF CONTENTS Section I Standard Data for Sheet Metal Fabrication Layout SD20.1 Forming Angels and Bends in Sheet Metal SD20.2 Flat Pattern Development SD20.3 Mold Line Reversal SD20.4 Springback (Radius and Mold Line Correction) SD20.5 General/Miscellaneous SD20.6 Section II Standard Data for Detail Tools Tool Steel Pancake Die (BD, BPD) SD20.14 Router Jig (ROJ) SD20.107 Form Blocks (Rubber forming) (PB, PBH, WPB, HPB) SD20.110 Master Flat Pattern Template (TTH), SD20.113 Master Flat Pattern Template, Sellers (TTS) Grind Check Template (GCT) SD20.124 Punch & Nibble Template (PNT) SD20.125 Press Block and Hammer Block Template (PBT, HBT) SD20.126 Punch & Scribe Template (PST) SD20.127 Air Punch Template (APT) SD20.133, 134, 135 Setback Router Jig (SRJ) SD20.136 Saw Fixture (SF) SD20.137 Masking Template (MAT, MATP) SD20.138 White Masters (WM) SD20.139 Drivmatic Masking Template (MTD) SD20.140 Universal Router Masking Template (URT) SD20.150 Drill & Router Board (DRB) SD20.151, 152, 153 Pneumatic Router Box Template (CBT) SD20.160, 161, 162 Records Template (TTR) SD20.163 Strippit Punch Template (SPT) SD20.164 Potting of Bushings with a Thermosetting Compound SD20.166 Tooling for Interchangeable Parts - Conventional (Built-Up) Sheet Metal SD20.167 Tooling for Interchangeable Parts - Chemical Milled Parts SD20.168 Plastic Face Strength Die (SD, SDH, SDM, SDS, HD) SD20.179 SECTION Contents PAGE 2 of 2 DETAIL TOOL 20 REVISION DATE __________________ Section II (cont.) Shear and Router Board (SRB) SD20.180 Hand Router Jig (HRJ) - Flat SD20.181 Hand Router Jig (HRJ) - Contoured SD20.182 Molding Form (MOF) SD20.183 Profiling Template (PFT) SD20.185 Blanking Die, Rubber (BDR) SD20.186 Holding Fixture (HF) SD20.271 Hole Plugging in Template Tools SD20.275 Tooling Ears SD20.276 Form Block "Dam" SD20.277 Form Block Insert SD20.278 Tool & Equipment Identification SD20.510 Section III Standard Data for Electronically Generated Tooling Tool Steel Pancake Die (CBD, CBPD) SD20.24 Router Jig (CROJ) SD20.207 Form Block (Rubber Forming) (CPB, CPBH, CWPB, CHPB) SD20.210 Master Flat Pattern Template (CTTH) SD20.213 Setback Router Jig (CSRJ) SD20.236 Saw Fixture (CSF) SD20.237 Masking Template (CMAT, CMATP) SD20.238 Master Graphics Model (MGM) SD20.239 Drill & Router Board (CDRB) SD20.251, 252, 253 Record Template (CTTR) SD20.263 Plastic Face Stretch Die (CSD, CSDH, CSDM, CSDS, CHD) SD20.279 Shear Router Board (CSRB) SD20.280 Hand Router Jig, Flat (CHRJ) SD20.281 Hand Router Jig, Contoured (CHRJ) SD20.282 Molding Form (CMOF) SD20.283 Blanking Die Rubber (CBDR) SD20.286 Holding Fixture (CHF) SD20.371 Tool & Equipment Codes SD 1.665 Appendix Section I STANDARD DATA FOR SHEET METAL FABRICATION SECTION SD20.1 PAGE 1 of 2 DETAIL TOOL 20 REVISION DATE __________________ Note:All acronyms referred to in this document are defined in “Tool & Equipment Code List” (SD1.665). LAYOUT 1.0 Measurement Techniques: • Work-piece sizes are determined by Photo Lofts, Engineering White Masters, Electronic Models, Flexible White Masters, and measurements given on an Engineering print. • Measurements made by using lines on PL's, EWM's, and FWM's shall be taken from the center of the line to reduce the possibility of introducing errors from varying line widths. 2.0 Flanges: • Flanges are bent 90° to the body of the part unless specified otherwise. A flange bent less than 90° is said to be open. Example: A flange bent 60° is "open 30°"; a flange bent 120° is "closed 30°". Particular attention should be paid to the angle involved. By custom, in the Bend Allowance Charts, the angle referred to as the bent-up angle, is the angle through which the material is actually bent. In the Bend Deduction Charts, the angle referred to is the enclosed angle, which is the supplement of the bent-up angle. SECTION SD20.1 PAGE 2 of 2 DETAIL TOOL 20 REVISION DATE __________________ 3.0 Locating Holes on Flat Patterns: • When locating holes on a flat pattern, which are not shown on the flat pattern, but appear on the formed part, the following procedure should be used: Distance from OML to hole - Bend Deduction = Flat Pattern Hole Distance Hole Locations on Drawing Flat Pattern .050" Material .500" (Hole Distance on Drawing) .174" Bend Deduction .174" (Bend Deduction) .326" (OML to Hole Distance on Flat Pattern) SECTION SD20.2 PAGE 1 of 1 DETAIL TOOL 20 REVISION DATE __________________ Note:All acronyms referred to in this document are defined in “Tool & Equipment Code List” (SD1.665). FORMING ANGLES and BENDS in SHEET METAL T = Material Thickness FC = Form Correction IML = Inside Mold Line OML = Outside Mold Line OHL = Outside Heel Line IHL = Inside Heel Line BT = Bend Tangent BR = Bend Radius RC = Radius Correction SB = Set Back α = Degree of Bend Since the material thickness, bend radius, and degree of bend are always given, the other values may be easily found. FC = T x tan(degrees of bend) = distance from IML to OML 2 (degrees of bend) RC = BR x tan = distance from IML to BT 2 (degrees of bend) SB = (BR + T) x tan = distance from OML to BT 2 SECTION SD20.3 PAGE 1 of 3 DETAIL TOOL 20 REVISION DATE __________________ Note:All acronyms referred to in this document are defined in “Tool & Equipment Code List” (SD1.665). FLAT PATTERN DEVELOPMENT • The length of sheet metal from the beginning to the end of a bend, measured along the neutral axis (a line near the center where the metal is neither stretched nor compressed) is the bend allowance. To develop the flat pattern of a part, this length of arc must be found. • There are three principal methods used to find this length of arc: Use bend allowance when bend tangents are known, use bend deduction when the outside mold point is known, and use of an electronic model. Bend Allowance: • Bend allowance is the distance along the neutral axis between bend tangents, and is based on the formula: Bend Allowance = (.01743R + .0078T) α Where, R = inside radius of bend T = part thickness α = number of degrees of bend • Tables of bend allowance will be found in Appendix 1. These values are for 1 degree of bend, and must be multiplied by the number of degrees of bend to find the bend allowance. SECTION SD20.3 PAGE 2 of 3 DETAIL TOOL 20 REVISION DATE __________________ Example 1: Developing a Flat Pattern Using Bend Allowance 3 BEND RADIUS = /16" ANGLE α =5° Closed MATERIAL = .063" Thick AD = 1" EC = 3" 3 Bend allowance (from chart) for /16" BR, .063" material. Bend Radius 95° = .00377 x 95 = .358" Developed Length = AD + CE + Bend Allowance, or, 1" + 3" + .358" = 4.358" Bend Deduction: • The method for finding the flat pattern length of a part is to use the bend deduction chart. The advantage to the bend deduction method is that bend tangent points are not necessary. • The length of the flat pattern AC is AB (plus) BC (minus) J, where "J" is the bend deduction value read from the chart (Appendix 3) and point "B" is the outside mold point of the bend. To use the chart, lay a straightedge from bend radius (top of chart) to part thickness (bottom of chart). Read across from degrees of bend. The intersection with the straightedge shows bend deduction value "J" (slanting lines). Note: These same values are also available in the Bend Deduction and Bend Allowance booklet. SECTION SD20.3 PAGE 3 of 3 DETAIL TOOL 20 REVISION DATE __________________ Example 2: Developing a Flat Pattern Using Bend Deduction: 3 BEND RADIUS = /16" ANGLE α =5° Closed MATERIAL = .063" Thick Developed length = AB + BC - J From the bend deduction chart, 3 "J" for .063", 5° closed, BR /16" = .190" Developed length = AB + BC - J 3 1 =1/16" + 4 /2" - .190" = 1.1875" + 4.500" - .190" = 5.4975" Center of Bend: 1 1 • AB minus /2 "J" or BC minus /2 "J" gives the distance from the end of either flange to the center of the bend. The center of the bend is necessary for parts whose flanges are formed in a press brake. Electronic Model: • Once the 3D model is established, use the "analysis" function in CADAM/CATIA to determine the length of arc on the total length of the part. SECTION SD20.4 PAGE 1 of 2 DETAIL TOOL 20 REVISION DATE __________________ Note:All acronyms referred to in this document are defined in “Tool & Equipment Code List” (SD1.665).
Details
-
File Typepdf
-
Upload Time-
-
Content LanguagesEnglish
-
Upload UserAnonymous/Not logged-in
-
File Pages319 Page
-
File Size-