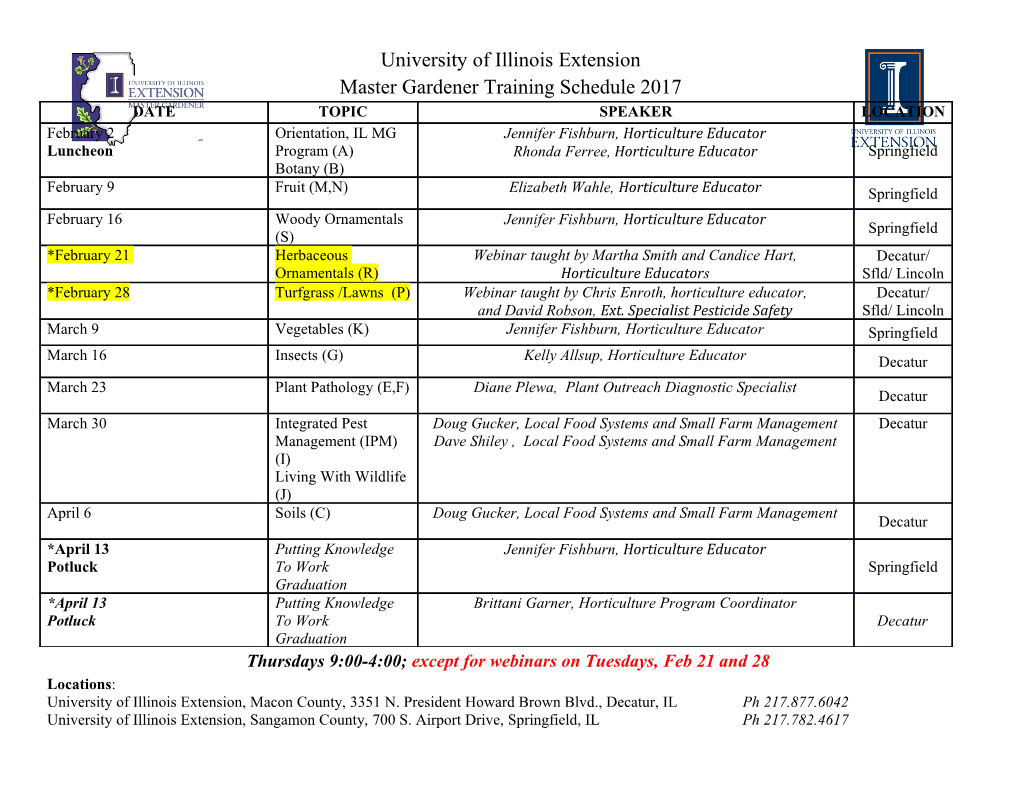
Total Quality Management, 2014 Vol. 25, No. 6, 664–682, http://dx.doi.org/10.1080/14783363.2013.820022 The Toyota Way model: an alternative framework for lean construction Shang Gao∗ and Sui Pheng Low Department of Building, National University of Singapore, 4 Architecture Drive, Singapore As the success of lean production is widespread, both inside and outside the manufacturing industry, there have emerged a number of models of lean construction, which look into the possible implementation of the lean principles in the construction industry. While it is commonly accepted that lean production has its basis in the Toyota production system (TPS), the ‘Toyota Way’ has developed as something more than simply the TPS. This study examines the current implementation frameworks of lean construction and proposes an alternative framework for the construction industry based on the Toyota Way model. It is hoped that this ‘back to the basics’ approach can be used to bring greater clarity to lean construction by means of the Toyota Way model. The comprehensiveness of the Toyota Way model means that it can bring about multiple angles from which to look at the lean construction model for the construction industry. Keywords: Toyota Way model; lean construction; construction industry Introduction Today, lean production – a management philosophy which originated from the Toyota production system (TPS) – is widely applied outside of the manufacturing industry. For example, Dahlgaard, Pettersen, and Dahlgaard-Park (2011), among others, have discussed the development of lean and quality systems for healthcare organisations. The research undertaken by Alsmadi, Almani, and Jerisat (2012) found that the service sector has also embraced the concept of lean, and outperformed in soft lean practices compared with the manufacturing sector in the UK. In the construction industry, the term ‘lean con- struction’ has become an established theme, and is promoted as a means to achieve oper- ational improvement (i.e. quality and productivity) through elimination of waste and maximising value (Egan, 1998; Diekmann, Krewedl, Balonick, Stewart, & Won, 2004). However, a closer examination of the related literature shows that little agreement still exists on the definition of – as well as implementation framework of – lean construction (Green & May, 2005; Morris & Lancaster, 2006; Jørgensen & Emmitt, 2008; Mossman, 2009). As Green and May (2005) noted: Lean construction is variously understood as a set of techniques, a discourse, a “socio-tech- nical paradigm” or even a “cultural commodity” (p. 503). The objectives of this article are to provide an alternative framework to give to the lean construction research community better explanations based on the Toyota Way model. First, current frameworks or models of lean construction will be reviewed and synthesised. Topics derived from these models will be discussed, and missing elements that need to be addressed will be highlighted. Second, the Toyota Way model and its associated principles ∗Corresponding author. Email: [email protected] # 2013 Taylor & Francis Total Quality Management 665 will be reviewed, with the hope of learning lessons or ‘best practices’ to bridge the missing links lacking from the current lean construction models. The discussion of the alternative framework appears in Section 5, where its applicability and implications for the construc- tion quality are discussed. Literature review Development of lean production It is commonly acknowledged that lean production was pioneered by Toyota in what is known as the TPS. Holweg (2007) provides a rich account of the genealogy of lean pro- duction, in which a timeline of research on and dissemination of lean production was mapped. Lean has had an evolutionary journey similar to the path followed by total quality management (TQM) (Dahlgaard-Park, Chen, Jang, & Dahlgaard, 2013): both have travelled from the USA to Japan and from Japan to the West. In the view of Holweg (2007), before Krafcik (1988) coined the term ‘lean’, the TPS as developed by Taiichi Ohno, had long existed as a ‘secret weapon’ for improving operational efficiency. This came to be the first source available in English, until the paper written by Sugimori, Kusunoki, Cho, and Uchikawa (1977) was published. Prior to that, Ohno (1988) acknowl- edged that the just-in-time (JIT) concept was influenced by the American supermarket system. Lean later became a huge success and drew great attention when the International Motor Vehicle Programme (IMVP) published its findings (Womack, Jones, & Roos, 1990), which clearly showed that there was something special in terms of Japanese quality and efficiency (Dahlgaard & Dahlgaard-Park, 2006). Meanwhile, TPS has ‘evolved’ gradually into the Toyota Way. Efforts have been made by Liker (2004), who conceptualised the Toyota Way as a pyramid model, in which a set of principles are built in, at both shop floor level and firm level (see Figure 1). The literature has seen a sizable volume of lean production (and lean manufacturing) models emerged in more recent years. According to Dahlgaard-Park et al. (2013), in the Figure 1. The Toyota Way model (Source: Liker, 2004). 666 S. Gao and S.P. Low period 1987–2011, articles published in the area of JIT/TPS/lean outnumber those on TQM. Basically, these frameworks of lean can be categorised into two broader themes, namely ‘design/conceptual’ frameworks and ‘implementation’ frameworks. Yusof and Aspinwall (2000) compared the differences between conceptual framework and implementation framework in the context of TQM. In a similar vein, the former (concep- tual framework) discusses the contents of lean production, i.e. what the elements of lean production are (Koskela, 1992, 2000; Karlsson & A˚ hlstro¨m, 1996; Shah & Ward, 2007), whereas the latter deals with frameworks that can provide a discussion on how to implement lean production, including what the sequence of activities should be and so on (A˚ hlstro¨m & Karlsson, 2000). Furthermore, several authors have examined the frameworks of lean production. For example, approximately 30 frameworks for lean production were examined by Anand and Kodali (2010) in terms of their comprehensiveness, abstractness, and degree of fit to an organisation. The results showed that a majority of the examined frameworks lacked a high degree of comprehensiveness, whereas many showed high and medium degrees of abstractness. In short, all these features are attributed to an improper under- standing of lean production. Earlier, another comparative study was performed by Paez et al. (2004) with less selected lean production frameworks. In their study, each framework was assessed with respect to its human and technological aspects. The finding implied that most frameworks did not equally take into account of both lean tools on the shop floor and the development of the workforce. Lean construction Over the last few decades, in order to introduce aspects of lean production into construc- tion projects, various research efforts have been undertaken. Although lean construction is still in its infancy, a set of practices have been proposed, tested, and implemented (Paez, Salem, Solomon, & Genaidy, 2005; Jørgensen & Emmitt, 2008). In particular, Jørgensen and Emmitt (2008) noted that, ‘implementation and application’ have emerged as a domi- nant theme in lean construction, in which numerous projects and process performances connected to lean initiatives were reported. However, compared with lean production or TQM (Dahlgaard & Dahlgaard-Park, 2006), which has achieved a certain maturity, lean construction has been slow in opening to critical debate (Jørgensen & Emmitt, 2008). Jør- gensen and Emmitt (2008) also pointed out that, in the transition of the lean principles from production to construction, the process losses appear to be related mainly to the chal- lenges surrounding the application of the practices in a different context. This motivates the present research to evaluate existing frameworks of lean construction with a critical eye, and discover what is really missing. Implementation frameworks for lean construction In this section, various frameworks for lean construction are reviewed (see Table 1). Given that a full coverage of all frameworks would be impractical, only the most widely published and most relevant ones are presented. The parameters used for analysis are provided below: (1) Objective: this parameter helps to identify what is the drive that has led to the fra- mework being utilised by researchers or practitioners. (2) Topics covered: this represents the main issues addressed in each framework. (3) Research methods (if any): this identifies how the data collected – i.e. question- naires, interviews, or case study. Table 1. Comparison of lean construction models. Research Where No. Author(s) Model name Objectives Topics covered methodology applied 1 Ballard Last planner To produce more reliable schedule † Four levels of scheduling: master plan, Case studies USA (2000) systemTM (LPS) phase plan, look-ahead plan, and weekly plan † Reliable matrix: percent plan complete † Daily huddle meeting: remove potential barriers 2 Diekmann Lean construction To assess the extent to which an † Elimination of waste Questionnaire and USA et al. wheel organisation conforms to lean † Standardisation case studies (2004) ideals † Culture/people † Customer focus † Continuous improvement Total Quality Management 3 Green and Not mentioned To evaluate the existing model of † Model 1: waste elimination Industry-wide
Details
-
File Typepdf
-
Upload Time-
-
Content LanguagesEnglish
-
Upload UserAnonymous/Not logged-in
-
File Pages20 Page
-
File Size-