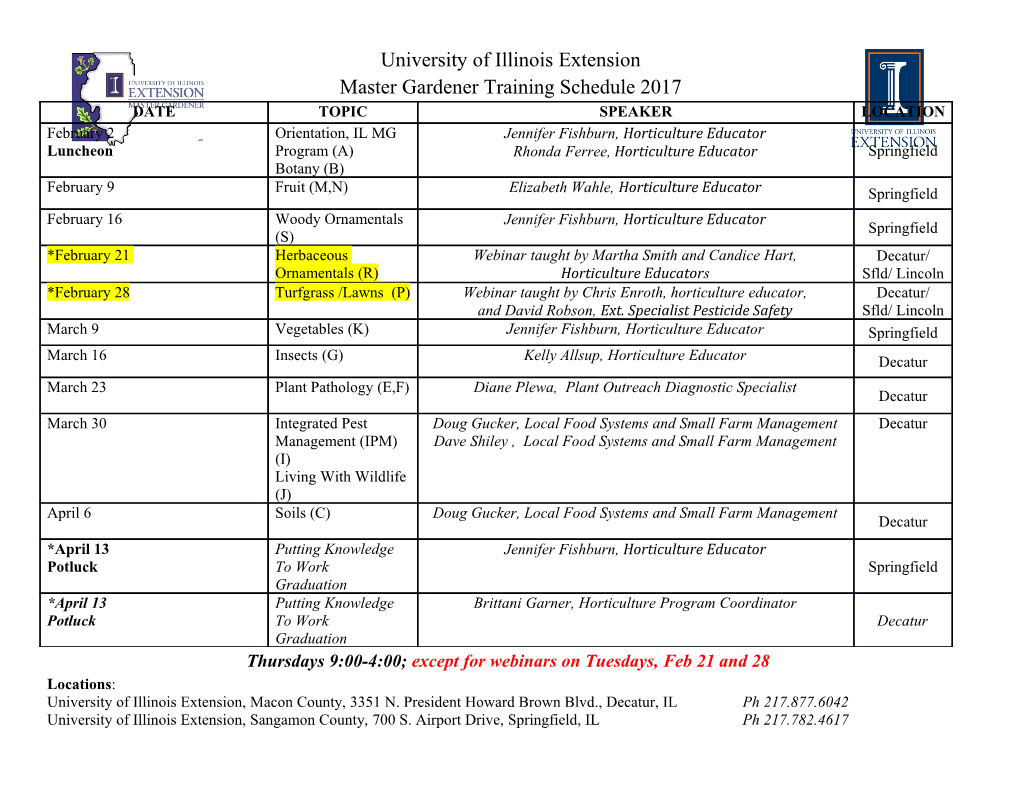
Build Instructions Solar Assisted Essential Oil Distiller Johnathon Wheaton Nathan Johnson Peter Coutts Benjamin Wolfe Rochester Institute of Technology Senior Design Team P15484 Table of Contents Trough ........................................................................................................................................................... 1 Tracker .......................................................................................................................................................... 2 Bike Breakdown ........................................................................................................................................ 2 Subsystem 1: Box collector ....................................................................................................................... 2 Subsystem 2: Can Wheel ........................................................................................................................... 7 Subsystem 3: Gearing ............................................................................................................................. 10 Plant Matter Container ............................................................................................................................... 12 Drip feed / condenser ................................................................................................................................. 14 Condenser: .......................................................................................................................................... 14 Drip Feed: ............................................................................................................................................ 14 Separator/Collector .................................................................................................................................... 15 Condenser Table: ........................................................................................................................................ 15 Plant Matter Container Table: .................................................................................................................... 15 Trough Frame: ............................................................................................................................................. 16 Trough Tools: 1. Water jet cutter 2. Hand drill a. Philips head attachment b. ¼” drill bit c. 2 ½” hole saw 3. Drill press a. Drill bit for pilot hole 1/8 in 4. Lathe 5. Solder , flux, blow torch 6. Welder 7. Clamps 8. 90 degree magnetic supports 9. Band saw 10. Epoxy 11. Spray adhesive Steps: 1. Use water jet cutter to cut parabolic supports and trough walls. 2. Brush off any excess rust using a wire wheel. 3. Use right angle magnets or other supports to position parabolic supports in their final position on the steel angle. 4. Weld each of the parabolic supports on either side to the steel angle. 5. Spray paint the entire metal trough frame including trough walls. 6. Cut the lithographic and mylar to size according to the drawings. 7. Set the lithographic plate in the metal trough frame using the steel angle to hold the lithographic plate against the parabolic supports. 8. Spray adhesive over the surface of the lithographic plate according the instructions on the can. 9. Using at least 2 people, align and gently lay mylar onto the lithographic plate preventing bubbles from forming and scraping or rolling out any that do. 10. Cut the two 1-1/2 x 9 steel safety plates to size according to the drawing. 11. Drill a ¼in clearance hole through the center of the safety plate. 12. Use a brake press to bend the safety plates at the appropriate location at a 90 degree angle. 13. Apply a 1/8 in layer of epoxy to the inner surface of the safety plates according to the drawing. 14. Using a lathe, turn and cut the scrap metal to 1in diameter x ½in length. Thread a hole through the center for a ¼-20 screw. 15. Spray paint the safety plates and turned metal piece. 16. Screw the safety plates to the turned metal piece per the drawing. 17. Screw the 2 tracker bolts into the trough wall. 18. Bolt the bearings to the trough walls. 19. Place the turned metal piece into the 1in bore diameter bearing. Tighten the set screw on the bearing. Page 1 20. Bolt the lower trough wall (with 1in bearing) to the metal trough frame. The lower parabolic edges should be flush (see drawing). 21. Cut the two copper pipes to length according to drawing using a band saw. Remove all burrs. 22. Fit receiver pieces together according to the drawing with solder and flux. Be sure to create a good seal with the solder. Test for seal with water. 23. Spray paint the copper receiver. 24. Slide 1in ID silicone piece over the smaller end of the receiver down to about 4 inches from the end. 25. Slide trough wall with 1-1/2in bore diameter bearing over the end of the trough so that the silicone tube is between the copper pipe and bearing. 26. Place the cap end of the receiver in the safety plates that are assembled to the 1in bearing wall. 27. Bolt upper trough wall to the metal trough frame keeping lower parabolic edges flush. 28. Use the slots in the walls to adjust the receiver distance from the reflector as necessary to allow more or less concentration. Tracker Note: While some of the tracker build is similar to the SolarFlower project, many steps have changed. It is advised to watch the SolarFlower tutorials and be familiar with them, but be aware that about much of it has been adapted to best fit the needs of this project. Bike Breakdown Tools: 1. Wrench 2. Pliers 3. Paper towels to degrease/clean parts with 4. Bike spoke tightener or pliers can be used After obtaining the bike, strip down the bike making sure to collect the: Cable tensioners Wheel spokes and nipples Sprocket Frame Handlebar assembly (remove cables, brakes, shifters, and grips) Wheel inner tube Subsystem 1: Box collector Tools: 1. Hacksaw 2. Power Drill Page 2 3. 6mm drill bit 4. Bench vice 5. Needle nose pliers 6. Hammer 7. Box knife 8. Printer & paper 9. Scissors 10. Measuring cup (10mL) 11. Dremel 12. Spray adhesive 13. Tin snips 14. Sheet Metal Press 15. Drill Press & Drill bits Refer to Drawings: Steps: See also http://www.solarflower.org/tutorial.php?lang=en&tut=box#.VH07_DHF_h4 1. Take the 20cm length of copper pipe and drill a 6mm hole in the pipe, about 2cm from one end. 2. Take a cable tensioner bolt and cut the top bit off the tensioner bolt. This is so it takes up less space when you flatten the copper pipe. 3. Cut a small circle of inner tube rubber, just enough to be slightly larger than the head of the tensioner bolt. 4. Cut a small circle in the center of the inner tube rubber and push the tensioner bolt through it. This is to make sure the pipe will be airtight. a. NOTE: if you are braising or soldering the pipe closed then you don't need to do this. 5. With a hacksaw, put two cuts into the top of the tensioner bolt, so that when it's pressed tight within the pipe liquid can still run through it. 6. Place the tensioner bolt through the hole you just drilled in the copper pipe. 7. Put the original nut back on the tensioner bolt and tighten with pliers. 8. In a vice, or carefully with a hammer (preferably the vice) squash the pipe to about half its width, so that the bolt you just placed is in the middle of one flat side. This doesn't need to be too precise. 9. Flatten one of the corners in the pipe's opposite end. You want the flat area to be about 4cm long. The easiest way to do this is to put something metal about 1cm wide in the vice, place the end of the copper over it, and hit with a hammer until reasonably flat. 10. Drill a 6mm hole in the flat bit, about 2cm from the end. 11. Place a tensioner bolt, with rubber the same as the other one, through the hole and tighten on the original nut. You don't need to cut the top off or make cross cuts. (If you're soldering or braising you don't need the rubber.) 12. Flatten the ends of the pipe. The easiest way is to compress them in the vice, then finish with a hammer. Make sure the rubber stays in place, poking out a couple of Page 3 millimeters, and pay attention to the corners, making sure they're completely sealed. 13. Flatten the whole tube so it contains about 10 milliliters. This is easily done with a hammer on a flat solid surface, such as an anvil or your bench vice. 14. Seal both ends of the copper pipe with epoxy. Allow proper time to let the epoxy set. 15. Check the volume by placing a short length of 6mm PVC tube onto one of the tensioner bolts, putting some water in your mouth, and slowly squirting the water into the pipe while holding it flat. When the water starts coming out the other bolt take off the PVC tube and drain the water from the pipe into a small measuring cup. 16. Continue to flatten with a hammer until the volume is about 10ml, give or take. It's easier to decrease the volume than increase it, so take your time and don't overshoot. 17. You can increase the volume by placing the pipe in your vice flat side up, so that it squeezes the edges back together. Don't suck water out of the pipe into your mouth, it might not be very clean. 18. Now test the seal on the pipe to ensure it's airtight. a. Do this by placing the PVC tube on one tensioner bolt, put your finger tight over the other, and suck as much air out as you can with your mouth. Without letting any air in, put the end of your tongue over the pipe so you can feel the vacuum and hold it there. b. If after 10-15 seconds or more
Details
-
File Typepdf
-
Upload Time-
-
Content LanguagesEnglish
-
Upload UserAnonymous/Not logged-in
-
File Pages17 Page
-
File Size-