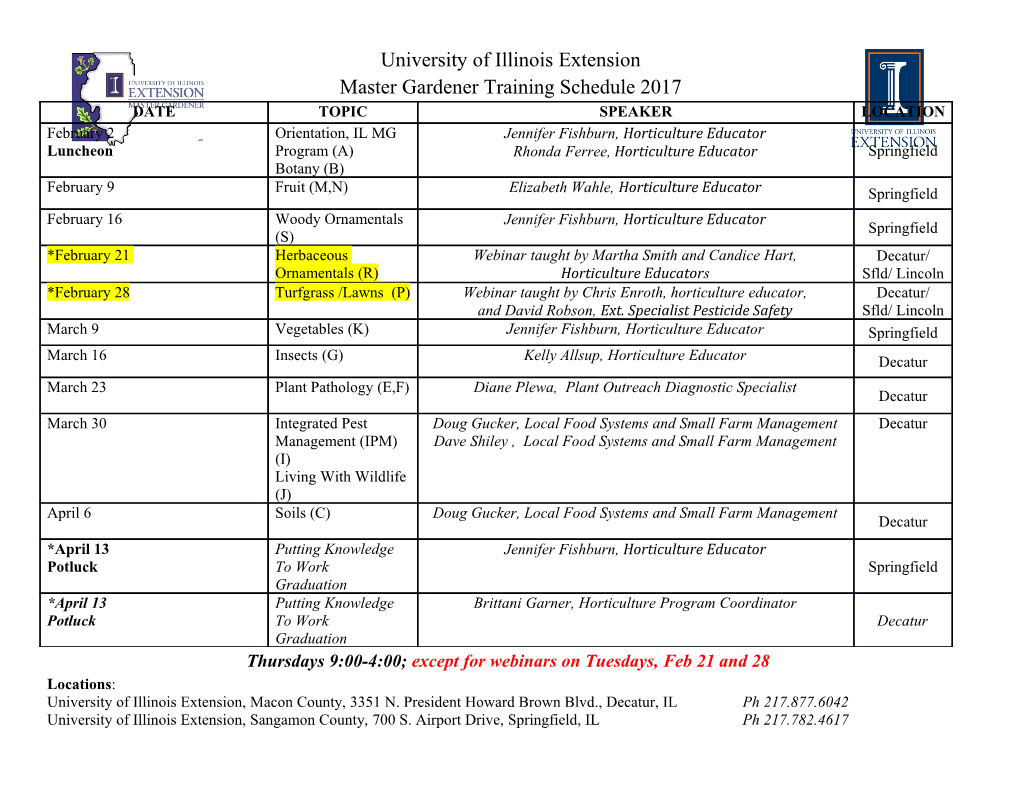
Technical and Economic Assessment of Membrane-based Systems for Capturing CO2 from Coal-fired Power Plants Haibo Zhai and Edward S. Rubin Department of Engineering and Public Policy Carnegie Mellon University Pittsburgh, Pennsylvania Presentation to the 2011 AIChE Spring Meeting, Chicago, IL March 13-17, 2011 Background • Post-combustion carbon capture and storage (CCS) has been considered a key technology for deeply reducing carbon dioxide (CO2) emissions from existing and new coal-fired power plants. • Membranes have been used commercially for industrial gas separation, and have the potential for application to power plant flue gases. • Membrane systems are among the advanced technologies being developed for more cost-effective CO2 capture. 2 1 Postcombustion Membrane Capture Systems for Coal-fired Power Plants Recycling Residue from 2nd Stage C 1st Stage Feed Residue C 2nd Stage Permeate To Storage 3 Research Objective • The objective of this study is to evaluate the technical feasibility and cost of polymeric membrane systems for CO2 capture at coal-fired pow er pl ant s. M or e specifi call y, ¾To investigate the performance (e.g. membrane system size and energy penalty) and cost of different capture system configurations (e.g. single- and multiple-stage modules) to identify feasible membrane systems that are able to simultaneously achieve 90% CO2 capture and above 95% purity of CO2 product; and ¾To examine a range of key factors affecting the capture system perfdtformance and cost. 4 2 Membrane Gas Separation Basics • The driving force for membrane gas separation is the partial pressure difference of a gas component between the feed and permeate sides. The flow flux of a gas component through membranes is: Where: = the volume flux of a component (cm3(S.T.P)/cm2.s); = membrane permeability that measures the ability of the membrane to permeate gas (cm3(S.T.P).cm/(s.cm2.cm Hg)); = membrane permeance (cm3(S.T.P)/(s.cm2.cm Hg))*; = the membrane thickness (()cm); Feed Residue = the mole fraction of CO2 in the feed stream; qf Pf q q ‐ dq qo xf x dA x ‐ dx xo = the mole fraction of CO2 in the permeate stream; = the feed-side pressure (cm Hg); dq, y = the permeate-side pressure (cm Hg). Pp qp Permeate * Note: xp Membrane permeance unit: 1 gas permeation unit (gpu)= 10-6 cm3(S.T.P)/(s.cm2.cm Hg) 5 Key Parameters for Membrane Gas Separation Process • Membrane selectivity: the ratio of two gas permeabilities and the measure of the ability of a membrane to separate two gases, such as CO2 versus N2. 2 2/2 2 • Pressure ratio: the pressure ratio for the feed versus permeate sides • Stage cut: the flow fraction of the feed gas that permeates the membrane 6 3 Technical and Economic Assessment Paradigm Performance Model Cost Model • Membrane • Membrane • Module structure • • area module and Unit cost factors Financing • Flue gas flow • Membrane frame costs properties (e.g. •System • Power selectivity, •CO2 vol.% power use equipments cost permeance) (e.g. compr., • Operating • Pressure designs • Permeate vacuum pump, conditions and residue expander) flows • Heat exchanger cost • Capital cost • O&M cost • Total cost of capture ($/tonne CO2) 7 Technical and Economic Assumptions for Assessment* Parameter Value Plant capacity factor 75% Feed flue gg(as flow rate (S.T.P m3/s) 500 Flue gas CO2 concentration (volume) 13% Flue gas pressure (bar) 1.0 Membrane CO2/N2 selectivity (S.T.P) 50 Membrane CO2 permeance (S.T.P gpu) 1000 Compressor/ pump/expander efficiency 85% Fixed charge factor 0.113 Electricity price($/kWh) 0050.05 Compressor installed capital cost ($/hp) 500 Vacuum pump installed capital cost ($/hp) 1000 Expander unit capital cost ($/kW) 500 Membrane module capital price ($/m2) 50 * Default values for case studies later, unless otherwise noted. 8 4 Single-Stage Membrane Systems Feed Residue (Flue gas) Permeate (CO2 product) 9 Single-Stage Membrane Systems Performance • Given Inputs: » Inlet CO2 concentration = 13% »CO2/N2 selectivity= 50 100% 20 75% 15 10 50% 5 ermeate Purity ermeate Purity P 2 25% CO 0% 0% 25% 50% 75% 100% CO2 Removal Efficiency 10 5 Two-Stage Ideal Cascade with Recycling Recycling Residue from 2nd Stage 1st Stage Feed Residue (Flue gas) 2nd Stage Permeate To Storage (CO2 product) 11 Two-Stage Membrane System: Pressure Ratio Requirement for Meeting Removal Targets • Given Inputs: » Inlet CO2 concentration = 13% »CO2/N2 selectivity= 50 100% 95% 90% rmeate Purity e P Pressure Ratio 2 85% 10 15 20 CO 80% 0% 20% 40% 60% 80% 100% CO2 Removal Efficiency 12 6 Two-stage Membrane System: Effects of Driving Force Design for Gas Separation (a) Feed-side compression (b) Permeate-side vacuum pumping Recycling Residue from 2nd Stage Recycling Residue from 2nd Stage C 1st Stage 1st Stage Feed Residue Feed Residue C 2nd Stage P 2nd Stage Permeate To Storage Permeate To Storage P (c) Feed-side compression + permeate-side vacuum pumping Recycling Residue from 2nd Stage C 1st Stage Feed Residue 2nd Stage Note: P C C = compressor E = expander Permeate To Storage P P = vacuum pump 13 Two-stage Membrane System: Effects of Driving Force Designs (cont’d) 40000 Vacuum Pumping 1500 Vacuum Pumping Prdt) Feed Compression 2 Feed Compression Prdt) 30000 2 Feed Compression + Vacuum Feed Compression + Vacuum 1000 Pumping e Area Pumping f CO of CO of wer Use wer n r o 20000 o 500 Membra / tonnes/h 10000 System P System 2 (m (kWh/ tonne 0 0 50% 60% 70% 80% 90% 100% 50% 60% 70% 80% 90% 100% CO Removal Efficiency CO2 Removal Efficiency 2 2 150 Vacuum Pumping t) Feed Compression f CO d o Pr Feed Compression + Vacuum 2 100 Pumping Capture Capture 50 ($/ tonne CO of tonne ($/ Total Annualized Cost Annualized Total 0 50% 60% 70% 80% 90% 100% 14 CO2 Removal Efficiency 7 Two-Stage, Two-Step Membrane Systems with Combustion Air Sweep • Using boiler combustion air as a sweep gas may remarkably increase the feed CO2 partial pressure and reduce the energy penalty of gas separation (Merkel et al., 2010). Sweep Air to Boiler Combustion Air (Flue gas) Feed 1st Stage 2nd Step Residue 2nd Stage Permeate To Storage (CO2 product) 15 Two-Stage, Two-Step Membrane Systems with Combustion Air Sweep: Effects of Factors • Key factors considered: ¾Feed-side pressure design ¾Pressure ratio for feed- versus- permeate side ¾Membrane CO2/N2 selectivity and CO2 permeability ¾ Membrane facilities price 16 8 Two-Stage, Two-Step Membrane Systems with Air Sweep: Effects of Driving Force Designs @ 90% Removal Efficiency 8000 100.0% Prdt) 2 98.0% 6000 Feed-side Pressure (bars) te Purity Purity te Area of CO a 96. 0% e 202.0 4000 94.0% 3.0 Perme 2 2000 4.0 Membran 92.0% / tonnes/hr CO 2 90.0% (m 0 579111315 579111315 Pressure Ratios of 1st and 2nd Stages Pressure Ratios of 1st and 2nd Stages 2 50 400 Feed-side Pressure (bars) Prdt) t) e 4.0 f CO s 2 d o 45 3.0 Pr 300 2 Feed-side Pressure (bars) 2.0 40 4.0 3.0 capture capture 35 200 2.0 System Power Power U System 30 ($/tonne of CO of ($/tonne (kWh/ tonne (kWh/ tonne of CO 100 annualized cost Total 25 579111315 5 7 9 11 13 15 st nd Pressure Ratios of 1 and 2 Stages Pressure Ratios of 1st and 2nd Stages 17 Two-Stage, Two-step Membrane Systems with Air Sweep: Effects of Membrane Properties @ 90% Removal Efficiency, Pressure Ratio 10 100.0% 400 98.0% Prdt 2 360 te Purity Purity te f CO 96.0% Use wer a o o 320 94.0% 280 Perme 2 92.0% P System CO 240 (kWh/ tonne 90.0% 200 25 35 45 55 65 75 25 35 45 55 65 75 Membrane CO2/N2 Selectivity Membrane CO2/N2 Selectivity 10000 2 50 Membrane CO2 Permeance (gpu) Prdt) t) CO Membrane CO2 Permeance (gpu) f 2 8000 500 d 45 Pr 2 40 500 6000 35 1000 4000 1000 capture capture 30 2000 Membane Area 2000 5000 / tonnes/hr / tonnes/hr ofCO 2000 2 25 5000 ($/ tonne ofCO (m 0 annualized cost o Total 20 25 35 45 55 65 75 25 35 45 55 65 75 Membrane CO /N Selectivity 18 2 2 Membrane CO2/N2 Selectivity 9 Two-Stage, Two-step Membrane Systems with Air Sweep: Effect of Membrane Facilities Price 60 Membrane CO2 Permeance (gpu) capture capture t) 2 d 50 500 Pr 2 40 1000 2000 30 5000 ($/ tonne ($/ tonne of CO tal annualized CO of annualized cost tal o 20 T 25 50 75 100 125 150 Membrane Facilities Price ($/m2) Note: Pressure ratio=10; Feed-side pressure = 2.0 bars; CO2/N2 selectivity=50; feed flue gas CO2 concentration =13%; system CO2 removal efficiency=90% and product purity =+95%. 19 Comparisons between Multi-Stage Membrane Systems @ 90% CO2 Capture Variables Two-stage Two-stage, two-step system system with air sweep Feed flue gas flow (m3/s) (w/o CCS) 500 500 Flue gas CO2 concentration (w/o CCS) 13% 13% Membrane CO2 permeance (gpu) 1000 1000 Membrane CO2/N2 selectivity 50 50 Feed-side pressure (bars) 3.0 2.0 Permeate-side pressure (bars) 1st and 2nd stages 0.2 0.2 2nd step - 1.0 CO2 product purity 95% 98% ↑ 2 Membrane area (m /tonnes/hr CO2) 3808 3766 System power use (kWh/tonne CO2) 399 265 ↓ Total capture cost ($/tonne CO2) 45.6 32.7 ↓ Approximate cost of CO2 avoided ($/t) 100.0 62.3 ↓ 20 10 Conclusions • Multiple-stage membrane systems are capable of meeting the CO2 capture performance targets (90% capture and above 95% product purity) for given membranes.
Details
-
File Typepdf
-
Upload Time-
-
Content LanguagesEnglish
-
Upload UserAnonymous/Not logged-in
-
File Pages19 Page
-
File Size-