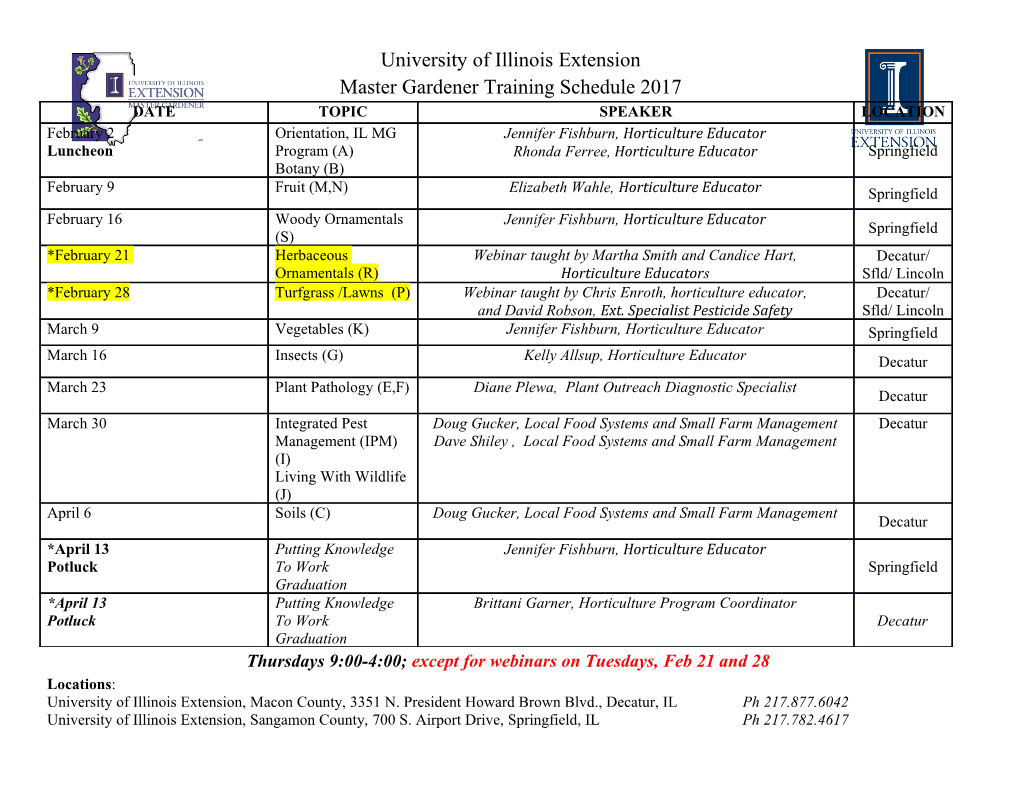
Iowa State University Capstones, Theses and Retrospective Theses and Dissertations Dissertations 1952 The titanium-vanadium system Richard Mather Powers Iowa State College Follow this and additional works at: https://lib.dr.iastate.edu/rtd Part of the Physical Chemistry Commons Recommended Citation Powers, Richard Mather, "The titanium-vanadium system " (1952). Retrospective Theses and Dissertations. 13304. https://lib.dr.iastate.edu/rtd/13304 This Dissertation is brought to you for free and open access by the Iowa State University Capstones, Theses and Dissertations at Iowa State University Digital Repository. It has been accepted for inclusion in Retrospective Theses and Dissertations by an authorized administrator of Iowa State University Digital Repository. For more information, please contact [email protected]. NOTE TO USERS This reproduction is the best copy available. UMI Tlffi TITBlIUM-fMlDItJM SYSTEM by Biehard Mather Pov/ers A Dissertation Submitted to the Graduate Faenlty in Partial Fulfillment of The Requirements for the Degree of DOGTOE OF PHILOSOPIH Major Subject: Physical Chemistry Approved t Signature was redacted for privacy. in ChargJ/bf Ma^or Work Signature was redacted for privacy. Head of Major Defartmenl^; Signature was redacted for privacy. Dean of Graduate College Iowa State College 1952 UMI Number: DP12422 INFORMATION TO USERS The quality of this reproduction is dependent upon the quality of the copy submitted. Broken or indistinct print, colored or poor quality illustrations and photographs, print bleed-through, substandard margins, and improper alignment can adversely affect reproduction. In the unlikely event that the author did not send a complete manuscript and there are missing pages, these will be noted. Also, if unauthorized copyright material had to be removed, a note will indicate the deletion. UMI UMI Microform DP12422 Copyright 2005 by ProQuest Information and Learning Company. All rights reserved. This microform edition is protected against unauthorized copying under Title 17, United States Code. ProQuest Information and Learning Company 300 North Zeeb Road P.O. Box 1346 Ann Arbor, Ml 48106-1346 li f ABLl OF COITIJITS I. PIJBPOSE OF STUDY 1 II. LITIBATIFBE SUHfEY 2 III, PEIPMATIOI OF STMfllG mTEEIALvS ...» 7 A* Blectrolytic Method 7 B» fanadim S 1. Calcim reduction of vanadiiira pentoxide using a sulfur booster .• 8 2#. Calcium reduction of vanadium pentoxide using an iodine booster . 13 C. Titaniuia 1$ 1. Hational Lead Company titanium sponge •»••«•«•••.««••••«»••••••••* 15 2» duPont titanium sponge 19 I¥. ALLOY PREPARATIOI 20 A» Electrolytic Co-deposition of Alloys 20 B# Go-reduction of Alloys 20 C» Arc Melting 30 1, Arc melting of sulfur boosted vanadium with National Lead Com­ pany titanium sponge 30 2, Arc melting of iodine boosted vanadium with duPont titanim sponge 32 T* ALLOY ANALYSIS 3^ YI. BETMMIIATION OF THE PHASE. DIAGRAM 38 A,. Melting Temperature Determinations ,••• 3® 1, Preparation of specimens 2. Melting point furnace H-1 ill » Temperature meastirement H-3 Procediire ^ 5* Standardization of the method w b, ¥Jiiidow correction h-7 Gas pickup 50 Bi Swmmj of melting temperature determinations 53 B• TherssiX An&lysis 60 C* Microstructures of the Titanium- fanadium Alloys 63 1. Preparation of raetallographic speciiaens 63 2. Arc melted alloys 6m- 3* Heat treatment of the alloys 68 D. X-Ray Studies 96 l/II. PHXSICAL PEOPiBTXES OF fHJ; ALLOYS 119 A. Density 119 B. Effiissivity Determinations 127 1» Method 128 2» lmissi-?ity of nickel 129 ImissiTity of the titanium- vanadium alloys ». H'. Summary of emissivity results •.... Melting temperature from emissiTity measurements 1^ C. Surface Tension 1^7 B.. Electrical Eesistiirity I66 E, Mechanical Properties 178 1# Cold rolling characteristics 178 2, Hot rolling characteristics ....... 180 Hardness I8H fensile properties 191 ¥111. CHEMI0AL PEOPERTIES OF THi; TITAHIUM- fAIABITO ALLOYS 203 A. Rate of Oxidation in Air 203 B, 315® C Steam Corrosion Rates 216 C# Solubility of the fitanium-?anadium Alloys in Hydrofluoric Acid 217 i¥ IX, COICLUSIOHS: 22^- X* BIBLIOGBiPHi 231 XI, ACMOWtEMMEIff S 236 -1- I. HJRPGSl OF SroBf SlBee botto tltanim ani TauaSim have "been considered as desirable materials for us® in certain reactors, it was thought that a study of allojs between these two might lead to materials with tmmn more desirable properties than either aetal alone. Consecpiently, a systeuatie investiga* tion of the alloys of the titanina-vanadim system was imdertaken. II. LITlRifOlE STJHTEf Before initiating experimental ^ork on the titanitua- Tanadim alloy system, a literature survey was made. What studies had heen carried out were of a liaited nature only, ao systeaatic overall investigation of this binary system was found# fhe earliest work reported on an alloy of these metals was that of 'Kroll (1) who employed powder metallurgy teehniques on mixtures of titanium with a number of alloying elements, fhe briquets were formed by pressing at 1^ tons per square inch into jA inch diameter coins, 1/k inch in height# these ccwpacts were presintered in a vacuum; then sintered at a high temperature under $0 lailliiaeters of argon# Following this treatment, they were covered with a salt layer and hot-rolled into one milliraeter strips, fhe single vanadiua alloy of I3eoll*s investigation that was prepared in this manner contained per cent vanadium and was reported 'to possess good rollability* fhe alloy had a Brinell hardness of k77 and eichlbited a micro structure shewing a titanium aatrix with a grain boundsj-y constituent, lore recently lU I. Larsen, E» F« -Swazy and others (2) investigated a number of titanium alloys, including those -3- ©f vanadim. fh© alloy® fateieateS by powder metal­ lurgy t#ctoi<pes, using Bareaa of Mines titanium powder, fh© sigje analysis of this material was the follwlngt 8 per cent throiigh 200 aesh, 20 per cent through 100 mesh, ^fl.»6 per cent through 60 laeshj and 99#9 cent tlirough 30 laesh. fhe principal impurities in the titanic were the follca-^ing: Mg 0,27 per cent| Fe 0,06 per cent? il 0,01 per centf ^Si 0,01 per centi CI 0,23 pe^p cent; H 0,095 per cent to ,111 per eent| 0 0,058 per cent to 0,072 per cent; and. S 0,02^ per cent to 0,035 per cent. Powder fixtures w©re compacted at a press-ure of 30 tons p©r scpare inch, fhese compacts were sintered for on© hour at 2200® F in a -racmi® of less than one micron, fhe sintered specimens were eold<-rolled wi'tti intermittent TOC-am anneals, or sheath rolled at 1^75® F, For th© titanimm^Tanadlnis alloys,, the aboT© titaniiua powder was combined with 95 per cent limp grade vanadium that had been crushed to pass the 30 mesh screen. Alloys containing 0,5 per cent, 5 P@r cent, and 15 per cent -ranaditua were pressed into bars and sintered for one hour at 2200® P. Ho depres­ sion of the aelting point was observed. The 15 per cent Tanaditiia bar did not cold-roll appreciably. However, tiie 0,5 per cent and the 5 P®r cent vanadima alloys were cold- rolled to reductions of between 25 per cent and 58 per cent •without serious edge cracking* fhe results of alloying may hest fee stjmariged in the following tahle. Further wrk was reported hy Larsen and others- (3) on a 5,7^ cent vanaditm alloy# 'fhis alloy was pre­ pared from 9? per cent lump vanadit® and du Pont titanium Tahle 1 Propertiei of Several fitiffiitiai-Tanadiuia Alloys (iBS'smf ^ lii. (3) P 239) Hardness Tensile Per cent Beiistivity <Eoekwell strength Per cent vanadiua (aicroha-cm#) (p#s,i») elongation 73 66 130,500 3^ (2") 0*5^ CC.E^77| 61 98,700 12*5^ (2") Ana. at I850® F) • 87 68 153,000 0 15^ <could not be cold-rolled sponge* fhe melting stock was prepared by compacting the mixture of raetals in a 1,93B' i^ich die# Melting and casting took place in graphite under an atmosphere of argon that had heen purified hy passage over titanium sponge at 900° C before entering the ftirnaee* fhe charge was heated by a split-graphite resistance furnace using currents up to 3^0 aaperes at 10 ¥olts» !Ph.e alloy generally absorbed from 0»03 to 0#06 per cent carbon from the crucible. In one alloy that contained 5.7^ per cent vanadium, a superficial tenacious oxidation product formed on annealing in a gas-fired .furnace, Mt did not interfere vith the properties or inpalr forging. They reported that this titanium-^anadiuffl alloy hardened appreciably on cpenehing» Considerable work has recently been published on the binary, ternary, and quaternary alloys of titanium by Craighead and others (^)» fhey report that the transi­ tion temperature of titanium is progressively lowered by additions of vanadium up to 5 P®!* cent# The tensile properties of several titanium-vanadium alloys with 5 per cent vanadium were studied by Busch and Bickenson (5a)• fhey obtained considerable varia­ tion in physical properties of the 5 per cent vanadium alloy samples# Recently, a phase diagram of the tit-anium-vanadium system has been reported by Adesnstedt and others (5b). Using both crystal bar and comaercial sponge titanium, together with cosmercial grade vanadium, these investi­ gators found that taie beta to alpha plus beta phase boundary was lowered by additions of vanadim to -6- titaniiffii* The single phase alpha field x-as found to ex­ tend to the 3*5 pfsr cent vanadiiam composition at 6^0° C for the crystal har titanim# At this temperature, the heta to alpha plus beta boundary was located at about the 20 per cent Tanadiura composition. In addition to the phase diagram, resistivities at 0® C, coefficients of expansion from room temperature to 1200® F, and lattice parameters and hardnesses as a function of composition were determined.
Details
-
File Typepdf
-
Upload Time-
-
Content LanguagesEnglish
-
Upload UserAnonymous/Not logged-in
-
File Pages244 Page
-
File Size-