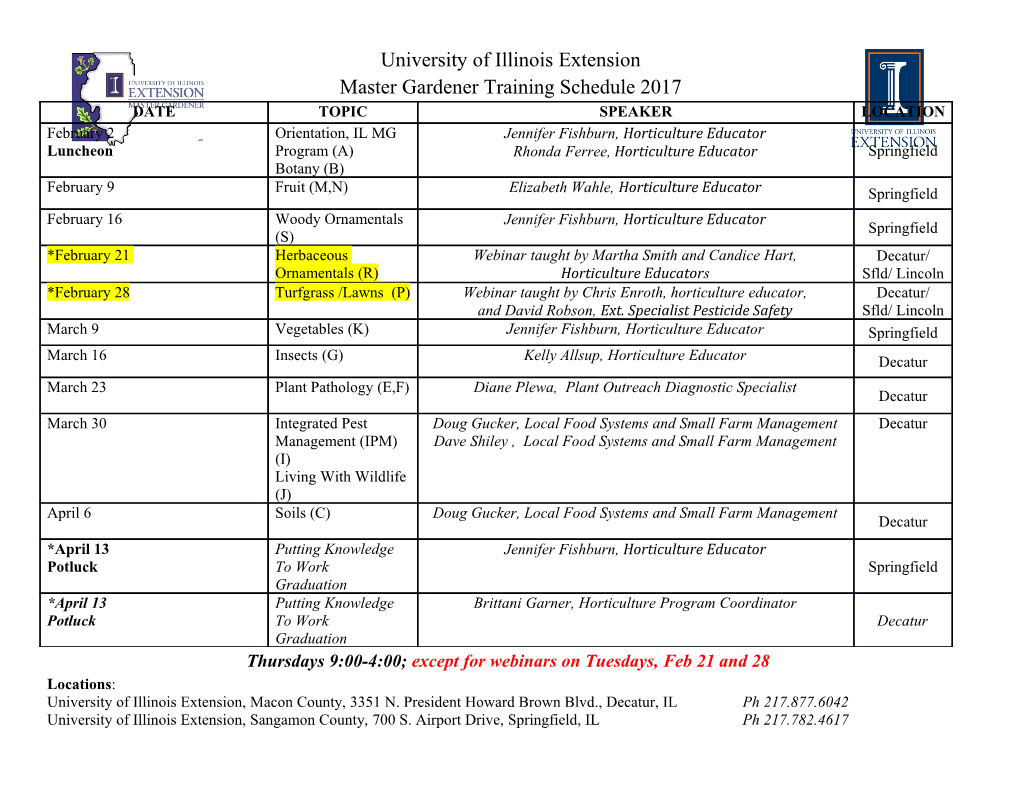
Advanced Stepper Lithography Technology to Enable Flexible AMOLED Displays Keith Best Roger McCleary Elvino M da Silveira 5/19/17 Agenda • About Rudolph • JetStep® G System overview and performance • Display Market Trends - Migration to Flex • Flexible Display Lithography Challenges • Results • Conclusion 2 Process Solutions Across the Semiconductor Industry INSPECT MEASURE Macro Defects Silicon to Die On Product and In-die Dicing and Chipping Detection Multi-layer Film Stacks Interconnect Metrology UBM, RDL, PR, PI, Dielectrics 3D/2D Inspection Structure CD Residue Detection CORE COMPETENCIES IMAGE ANALYZE Lithography resolution ≤1.5µm Process Analysis Active Matrix Display Backplanes Process Control Fan-out and Cu Pillar Tool-centric and Fabwide Wafer and Panel FRONT-END BACK-END SILICON RUDOLPH SOLUTIONS APPLY ACROSS THE SEMICONDUCTOR VALUE CHAIN TEST 3 Lithography Experience Spanning >25 Years PanelPrinter Gen 6 High 9200 (G4.5) Resolution FPD PanelPrinter 5200HR PanelPrinter (G2.5) PanelPrinter JetStep W AP 5200 (G2) 6700 (G3.5) Wafer System JetStep S AP Panel System 1988 1992 1996 2000 2004 2008 2012 2016 2019 8010 GHI 8009 Lens G Lens 6218 GHI 8410 GHI Variable NA Lens 16001 Iline Lens Lens 8015GT Lens Godzilla Lens 4 Rudolph Lithography Family Advanced Packaging Display Lithography Systems Lithography Systems JetStep G Series JetStep W2300 JetStep S3500 JetStep G35 JetStep G45 (wafers) (panels) Resolution in µm 2.5 1.5 Field Size Ø in mm 80 200 Substrate size Gen 2 to 3.5 Gen 4.5 Specifically designed for mobile display and pilot production 5 Display Market Trends Changes Driven by Electronics Everywhere AMOLED displays are key differentiation and wearable enabler Panel makers are aggressively investing in flexible AMOLED to meet demand Bendable Foldable Rollable 6 Trends Driving Changes in Lithography AUTOMATION Lithography systems need to process G5 & 6 highly compliant substrate with warp PIXEL CREATION AMLCD Color Filter OLED Front Plane SUBSTRATE Glass PI on Glass up to Gen 5 & 6 DISPLAY PRODUCTS Rigid Curved Bendable Foldable Rollable NOW 2018 2019 2020 2021 Mobile/ Tablets END MARKET VR AR Automotive Wearables PPI 440 >500 800 1000 2000 TRANSISTOR TECH TFT LTPS LTPS with OLED LITHO 0.5µm Overlay-1.5µm 0.35µm Overlay - 1.35µm 0.25µm Overlay – 1.0µm Resolution PERFORMANCE Resolution Resolution Compiled by Simax Asia Pacific Limited May 2017 7 A Path to Flex Substrate Lithography Scaling to R2R Scaling Addressing dimensional Addressing handling and Instability JetStep G35 topography Variations Stage to accommodate R2R to support an 8” web an 8” Web Overcoming Flex Manufacturing Challenges 8 Addressing Topography Challenges On-the-fly auto focus • Allows lens to follow wafer contours • Addresses the challenges of imaging on warped substrates • Capability to measure and monitor wafer topography 9 Imaging on Thin Substrates Photoresist: DOW SPR955CM, 1.4µm FT on Si. Dose: 300 mJ Focus = 0 um Focus = +2 um Focus = +4 um Focus = -2 um Focus = +6 um 1.25 µm thru Focus, ≥ 8.0 µm DOF 10 Flexible Substrates Distortion Characteristics Compaction and Expansion • Environment Induced • Temperature Effects: ~2um over 100mm field per degree C • Relative Humidity Effects: ~ 1um over 100mm field per % change in RH • Mechanical Induced Strain • Substrate Tension Variations in the Web line • Process Induced Distortion Substrate No Substrate Distortion Distortion Good Overlay Poor Overlay Layer 1 Layer 2 Layer 1 Layer 2 11 Grid Measurement Front and backside alignment • Integrated with JetStep alignment system • Dual Head Off-axis alignment microscopes Optional IR • Real time auto-focus Visible Microscope Microscope • Entire wafer area accessible for alignment Visible scope IR scope Objective 10X 5X Wavelength 500-700nm 500-1050nm* Field of View 1.35 x 1.35 2.7 x 2.7 mm Resolved Feature Size 0.9 µm 5.3 µm DOF 4.4 µm 200 µm Align Precision (3σ) 0.15 µm 0.24 µm *Longer Wavelength Option Available Embedded IR Alignment Target Visible Top-side Alignment Target 12 Compensation Method • 6 DOF Reticle chuck compensation • Up to 400PPM Compensation • Minimize field distortion • Mag, Trap, and Local position displacements X 1, X 2,Y 1 X ,Y, Z 1, Z 2, Z 3 Z,x,y 13 Overlay on Thin Substrates Product B, Layer C, Overlay X (1x Stepper to 2x Stepper) Product B, Layer C, Overlay Y (1x Stepper to 2x Stepper) 1.5 1.5 1 1 0.5 0.5 0 0 1 2 3 4 5 6 7 8 9 10 11 12 13 14 15 16 17 18 1 2 3 4 5 6 7 8 9 10 11 12 13 14 15 16 17 18 -0.5 -0.5 -1 -1 -1.5 -1.5 X Overlay Y Overlay 250 250 200 200 150 150 100 100 Frequency 50 Frequency 50 0 0 -1 -0.8 -0.6 -0.4 -0.2 0 0.2 0.4 0.6 0.8 1 -1 -0.8 -0.6 -0.4 -0.2 0 0.2 0.4 0.6 0.8 1 Microns Microns Production Overlay Results – 28 Consecutive Substrates 14 Rudolph Flexible Lithography Systems . Gen 2.5 Lithography System . Flexible Lithography Sheets . Custom Flexible Display Manufacturing and Research Photo source: ASU monthly magazine Delivering Enabling Capabilities 15 Rudolph R2R Lithography Systems . 6600 Gen 3 R2R Lithography System . New highly improved R2R . Process development research Solution Through Collaboration 16 Functioning Flexible Displays Flex Map Conformal Display Concept Conformal Display Working with World Leading Researches to Turn Concepts in Reality Sources: Arizona State University (ASU) US Army Flexible Display Center & ASU Magazine, September 2013 volume 17 number 1 17 Beyond AMOLED Development results in technology to open new possibilities IP DEVELOPED ADVANCED OLED MOBILE Flexible DISPLAYS PACKAGING TWO CAMERA CU-PILLAR, C4, PCB LARGE FIELD LENS G6 FPD NEXT GEN FPD HR, HIGH THROUGHPUT & LOW COO HR, AP, PANEL STITCHING 18 Photolithography for flexible displays High Fidelity Imaging for Critical Layers 1.5um L/S resolution Overlay Through Active Compensation Real-time compensation while maintaining best focus Addressing the Real World Challenges of Display Manufacturing on Flexible Substrates 19 Thank You! [email protected] www.rudolphtech.com.
Details
-
File Typepdf
-
Upload Time-
-
Content LanguagesEnglish
-
Upload UserAnonymous/Not logged-in
-
File Pages20 Page
-
File Size-