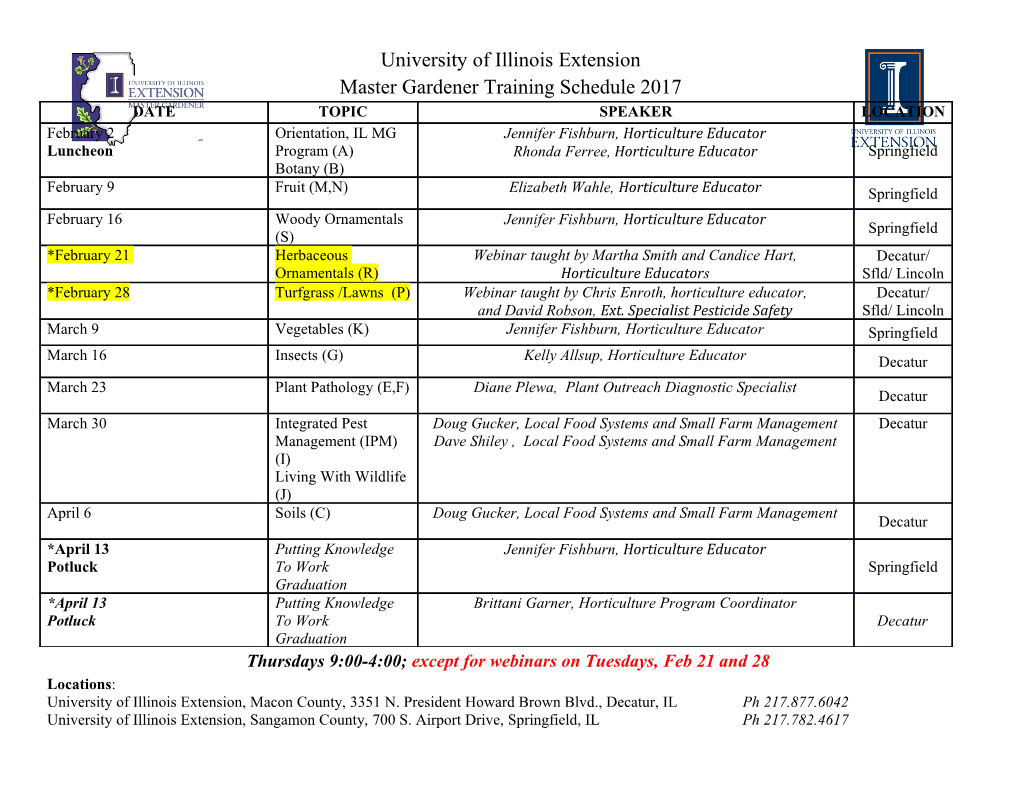
Roll up nanowire battery from silicon chips Alexandru Vlada,b,1, Arava Leela Mohana Reddya,1, Anakha Ajayana, Neelam Singha, Jean-François Gohyc, Sorin Melinteb, and Pulickel M. Ajayana,2 aDepartment of Mechanical Engineering and Materials Science, Rice University, Houston, TX 77005; and bInstitute of Information and Communication Technologies, Electronics and Applied Mathematics, Electrical Engineering, Université catholique de Louvain, Louvain la Neuve B-1348, Belgium; and cInstitute of Condensed Matter and Nanosciences, Bio- and Soft Matter, Université catholique de Louvain, Louvain la Neuve B-1348, Belgium Edited by Jisoon Ihm, Seoul National University, Seoul, Republic of Korea, and approved August 7, 2012 (received for review May 26, 2012) Here we report an approach to roll out Li-ion battery components dealing with Si-based anode materials, where the strain and from silicon chips by a continuous and repeatable etch-infiltrate- the large volume expansion (up to ≈400%) of the active particles peel cycle. Vertically aligned silicon nanowires etched from recycled have to be considered upon formation of the fully lithiated Li4.4Si silicon wafers are captured in a polymer matrix that operates as phase (18, 19). Colloidal mask-sustained Si MACE solves this Liþ gel-electrolyte and electrode separator and peeled off to make issue and as we show herein, this approach not only allows for multiple battery devices out of a single wafer. Porous, electrically large-scale nanowire synthesis through Si waste recycling, it also interconnected copper nanoshells are conformally deposited enables precise tuning of the vertical nanowires morphology around the silicon nanowires to stabilize the electrodes over ex- (length and diameter) as well as of the nanowire packing density tended cycles and provide efficient current collection. Using the up to nearly the bulk limit. We impregnated the high-aspect ratio above developed process we demonstrate an operational full cell (>100) Si nanowire forests with a polymer matrix that acts as a 3.4 V lithium-polymer silicon nanowire (LIPOSIL) battery which is gel-electrolyte and as a physical separator. The polymer-em- mechanically flexible and scalable to large dimensions. bedded Si nanowire composite can be peeled off the substrate yielding a mechanically robust, freestanding membrane. An elec- polymer electrolyte ∣ core-shell nanowires ∣ energy storage ∣ troless growth protocol is developed to wrap the Si nanowires with flexible electronics ∣ waste management a thin porous Cu layer. The accordingly obtained Si-core @Cu-shell nanowires display enhanced electrochemical performances due to ilicon is a promising anode material in lithium batteries due improved current collection efficiency and Si encapsulation. A Sto its high specific capacity and low operation voltage (1). functional 3.4 V LIPOSIL (lithium-polymer silicon nanowire) bat- However, the major concern in using Si-based anodes is the huge tery is demonstrated by laminating a LiCoO2 cathode layer on top volume expansion during the lithiation that leads to a fast degra- of the Si nanowire—polymer composite. dation of the electrode material and a reduced life cycle of the battery with limited use in real life Li-ion applications. The Results and Discussion advent of nanotechnology and successful incorporation of nano- Design and Fabrication of LIPOSIL Composites. For the nanowire structured materials in energy storage devices has further grown synthesis, we employed a continuous Si MACE (20, 21) with var- an interest in revisiting Si as an active anode material. The ious seeding layers (Fig. 1). Colloidal nanosphere lithography was enhancement in the electrochemical performance of nanostruc- used to structure the catalyst layer (see Fig. 1 A–C and Materials tured Si anodes provides novel platforms for the ubiquitous pre- and Methods). The diameter and spacing of the nanowires can be – sence of Si in Li-ion batteries (2 4). Through nanostructuring, precisely controlled by the size of the colloidal particles and sub- the active Si pulverization was minimized yielding stable capacity sequent processing conditions, while their length is adjusted by retention. However, this was found insufficient to maintain a the etching time (see SI Text, Fig. S1). Depending on the catalyst uniform electrical interface and adequate mechanical contact type, it is possible to etch silicon at rates higher than 1 μm/min between the active Si particles and the conductive additives, call- SI Text – (see , Fig. S2). Controlling the diameter, the spacing and ing for the development of new binder materials (5 7). Avoiding the height of the nanowires, facilitates smart tuning of the mor- binders or conductive additives and enabling a direct contact be- phology that directly impacts (i) the electrode mass loading, (ii) tween Si and the current collector is the other way to maintain the the free volume conforming to the Si volume expansion whilst electrical conductivity and mechanical integrity of the electrode. cycling, and (iii) the impregnating volume of polymer, which is This requires special designs of the current collector complying responsible for electrolyte uptake and attainment of the conduct- with the ensuing active material deposition. The optimal alterna- ing gel electrolyte. Adequate balancing of these criteria is the key tive so far is provided by the use of nanowires, nanotubes, or hier- to optimal electrochemical performances of the LIPOSIL anode archical assemblies directly grown, assembled, or bonded onto the current collector (8–12). composite. An excess active material loading by using large dia- Current collectors integrated with Si anodes have been meter nanowires will preclude the free space for volume expan- successfully fabricated through chemical or physical vapor de- sion accommodation and appropriate electrolyte amount uptake, while the reverse will result in low active material loading into position methods, room temperature metal assisted chemical ∼10% etching (MACE), as well as through various top-down methods electrodes. Note that free space can be achieved if the (8, 9, 12–15). One of the major drawbacks of the respective con- figurations is the relatively low tap density of the Si nanostruc- Author contributions: A.V., A.L.M.R., and P.M.A. designed research; A.V., A.L.M.R., A.A., tures leading to low mass loading of active material and low and N.S. performed research; A.V. and A.L.M.R. contributed new reagents/analytic tools; volumetric capacities. Moreover, excess of current collector is A.V., A.L.M.R., J.-F.G., S.M., and P.M.A. analyzed data; and A.V. and A.L.M.R. wrote usually employed in this configuration rendering them less attrac- the paper. tive for high-throughput battery manufacturing (16). Low com- The authors declare no conflict of interest. paction density is intrinsic to nanostructured materials and This article is a PNAS Direct Submission. requires additional processing, including agglomeration and high Freely available online through the PNAS open access option. pressure densification (17). Indeed, these methods do not offer 1A.V. and A.L.M.R. contributed equally to this work. fine adaptation of the composite free space to account for the 2To whom correspondence should be addressed. E-mail: [email protected]. volume expansion during cycling while not compromising the ac- This article contains supporting information online at www.pnas.org/lookup/suppl/ tive component loading. This is of importance primarily when doi:10.1073/pnas.1208638109/-/DCSupplemental. 15168–15173 ∣ PNAS ∣ September 18, 2012 ∣ vol. 109 ∣ no. 38 www.pnas.org/cgi/doi/10.1073/pnas.1208638109 Downloaded by guest on September 30, 2021 Fig. 1. Asecondlifefor silicon: Si chip towards the Li-battery recycling wheel. Schematic of the Si-polymer composite fabrication: (A) colloidal polystyrene parti- cles are self-assembled and processed on a Si chip to rea- lize the (B) holey Au mask used to fabricate the (C)Si nanowires through MACE. Uniform diameter and length nanowires are ob- tained over large areas (In- set). (D) After the polymer/ electrolyte infiltration, the composite is mechanically peeled to obtain the (F)self- supported Si nanowire-poly- mer composite. The fabri- cated composite membrane is highly flexible and can be bent with curvature radii less than 15 μm(Inset,seealso Fig. 2C). (E)Theholeycata- lyst mask remains intact after the peeling step and it is re-used for the fabrication of further Si nanowire-poly- mer composite membranes until the physical exhaustion of the Si chip. colloidal particles are not reduced in size. A Si nanowire forest we proceeded with successive polymer coatings, using a modified consisting of ∼25 μm long nanowires with a diameter of ∼150 nm paint battery technique (22), followed by drying steps until a con- (with 260 nm lattice spacing defined by the colloid packing), has a tinuous polymer film was detected on the surface of the sample free space approximately 70% of the total volume, corresponding (Fig. 2 A and B). The fully impregnated LIPOSIL composite was to a mass loading of 1.75 mg∕cm2. Experimentally we found a then peeled off from the substrate and the freestanding mem- similar value of ∼2 mg∕cm2 with the small variation being attrib- brane was robust enough for subsequent processing through roll- uted to the processing variations and measurements errors. High- ing, wrapping, bending and lamination (Figs. 1 and 2). er mass loading, without compromising the free volume, can be achieved via longer nanowires by simply increasing the etching Silicon Chip Recycling Scheme. Since the colloidal processing may time (see SI Text, Fig. S2). be regarded as an extra-processing step with additional costs Direct implementation as battery anodes of the substrate-sup- for the battery fabrication, we have implemented a multi-loop ported Si nanowires is not desirable since the remaining bulk Si is MACE—polymer infusing—composite peeling protocol. In this prone to pulverization and the physical link to nanowires would respect, we succeeded in realizing up to four LIPOSIL composite be rapidly lost.
Details
-
File Typepdf
-
Upload Time-
-
Content LanguagesEnglish
-
Upload UserAnonymous/Not logged-in
-
File Pages6 Page
-
File Size-