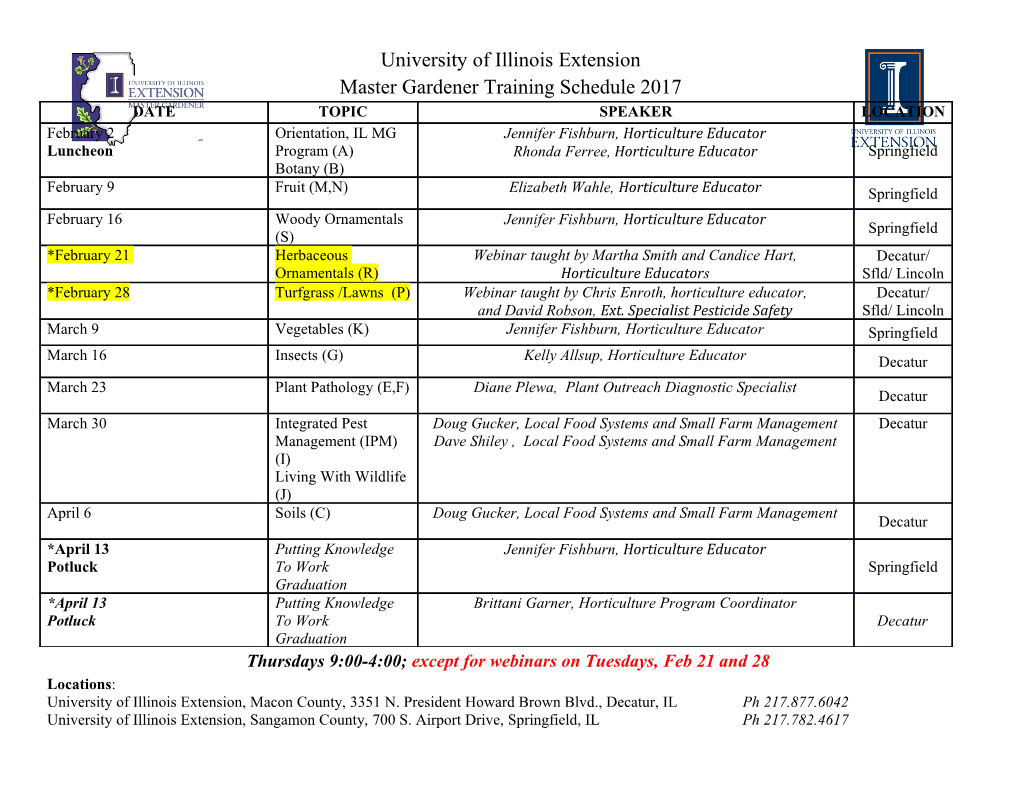
Galling Failures in Pin Joints by Greg A. Radighieri B.S. in Mechanical Engineering, Texas A&M University, 2000 Submitted to the Department of Mechanical Engineering in partial fulfillment of the requirements for the degree of Master of Science in Mechanical Engineering at the MASSACHUSETTS INSTITUTE OF TECHNOLOGY May 2002 @ Massachusetts Institute of Technology 2002. All rights reserved. Author Department of Mecfanical Engineering May 18, 2002 Certified by Samir Nayfeh Associate Professor, Mechanical Engineering Department Thesis Supervisor Accepted by Ain A. Sonin Chairman, Department Committee on Graduate Students MASSACHUSEU ITTU TE OF TECHNOLOGY OCT 2 LIBRARIES BARKER Room 14-0551 77 Massachusetts Avenue Cambridge, MA 02139 Ph: 617.253.2800 MITLiaries Email: [email protected] Document Services http://libraries.mit.edu/docs DISCLAIMER OF QUALITY Due to the condition of the original material, there are unavoidable flaws in this reproduction. We have made every effort possible to provide you with the best copy available. If you are dissatisfied with this product and find it unusable, please contact Document Services as soon as possible. Thank you. The images contained in this document are of the best quality available. 2 Galling Failures in Pin Joints by Greg A. Radighieri Submitted to the Department of Mechanical Engineering on May 18, 2002, in partial fulfillment of the requirements for the degree of Master of Science in Mechanical Engineering Abstract A pin joint is defined as an assembly of a pin and a bushing, under sliding contact, that transfers loads between two components while allowing rotation. Under heavy loads and low sliding velocities, pin joints are considered to be in boundary lubrica- tion. Failure of heavily loaded pin joints is yet to be fully understood and is often generalized as galling failure. Galling is really the end result of failure. A summary review of important parameters involved in boundary lubrication and galling is included. At the end of this review is a section hypothesizing how pin joint failures (and galling in general) may occur. To gain insight on boundary lubrication and the galling phenomenon, a test ma- chine was designed and built to force "galling" failure in pin joints. Initial tests results are given. Thesis Supervisor: Samir Nayfeh Title: Associate Professor, Mechanical Engineering Department 3 4 Acknowledgments I have many people to thank, for it takes a lot of teamwork to get things done. I should first thank my advisor for handing me this project. I could still be looking for a project if it weren't for him. He also provided me lots of insight into machines, machine dynamics, and machine design. He knows his stuff forwards and backwards, and he serves as a fantastic resource. He takes very good care of his students, including me. Thanks, Samir. Many thanks to this project's corporate sponsor. I hope my work will bring rewards to both the sponsor and MIT. My reward is the knowledge and the experience I've gained. 5 6 Contents 1 Introduction 17 1.1 M otivation ....... ...... 17 2 Pin Joint Analysis 19 2.1 Pin Joint Description . ...... .......... 19 2.2 Dimensional Analysis (Scaling) .......... 19 2.2.1 Fluid Mechanics Example .......... 20 2.2.2 Pin Jo it ......... .......... 21 2.3 Macroscopic Deformation..... .......... 23 2.3.1 Beam Bending...... .. ..... ... 23 2.3.2 Torsion .......... .......... 25 2.3.3 Transverse Shear ..... .... ..... 25 2.3.4 Combined Stress..... ... ....... 26 2.4 Microscopic Deformation..... ..... ..... 29 2.4.1 Radial Gap Geometry ... ..... .. 29 2.4.2 Surface Parameters . .......... 30 2.4.3 Undeformed Contact .......... 31 2.4.4 Contact Mechanics . .......... 33 2.5 Tribological Considerations. 35 .. ........ 2.5.1 Lubrication ........ 35 . ..... .... 2.5.2 Friction .......... 39 ... ..... .. 2.5.3 Frictional Heating ..... 40 .... ...... 2.5.4 Sliding Wear ........ 41 ..... ..... 2.6 Failure Theories .......... 43 ... ..... .. 2.6.1 List of Parameters . 43 2.6.2 Discussion of Possible Faili ure Mechanisms . 44 3 Design of a Pin Joint Testing Machine 47 3.1 M otivation ................ 47 3.2 Basic Requirements ........... 47 3.3 Basic Design Rules .... ....... 47 3.3.1 Rules of Thumb ..... .... 47 3.3.2 Kinematic Constraint ...... 48 3.3.3 Iteration .... ......... 48 3.4 Normal Load Design .......... 48 7 3.4.1 Everything Turns Into Rubber 48 3.4.2 Hydraulics ........... 49 3.4.3 Threaded Fasteners and Lever Arms 49 3.5 Torque and Rotational Speed Design 53 3.5.1 Taper Analysis . .. 53 3.6 Machine Elements ...... 55 3.6.1 Bearings ....... 55 3.6.2 Bearing Ring . ... 55 3.6.3 Support Base . ... 55 3.6.4 Bushing Housing 56 3.6.5 Pin Housing..... 56 3.6.6 Torque Transmission 56 3.6.7 Torque Support .. 56 3.6.8 Sensors ....... 56 3.6.9 Test Stand ..... 57 3.6.10 Seals ..... .... 57 3.7 Final Design ..... .... 58 3.7.1 Relative Motion . .. 58 3.7.2 Bearings .. ..... 58 3.7.3 Bearing Ring . ... 58 3.7.4 Support Base . 60 3.7.5 Bushing Housing 60 3.7.6 Pin Housing..... 61 3.7.7 Torque Transmission 65 3.7.8 Torque Support .. 66 3.7.9 Sensors ..... ... 66 3.7.10 Seals ...... ... 68 3.7.11 Test Stand ...... 70 3.7.12 Assembled Test Mach ine 70 4 Pin Joint Designs 73 4.1 Undercut Bushing .......... 73 5 Test Results 75 5.1 Initial Tests .... ....... .. 75 5.1.1 Standard Pin Joint ..... 75 5.1.2 Undercut Bushing ... ... 76 5.1.3 Discussion and Conclusion . 79 5.1.4 Recommendations .. .... 79 A Four Point Beam Bending Analysis 81 B Centroids of Circular Sections 83 C Bolt Calculations 85 8 D Differential Screw Analysis 87 E Taper Analysis 89 F Drawings 91 G Testing Procedure 125 9 41I1dI1iI1I, ill liii oI Iii ---hIiiIII-~iI~M~hEH~I~Iih~iil iihII I~lIhI~i~~~i IE lii II EhhhHIlIM 'I no -MIN List of Figures 2-1 Pin Joint Schematic. ........................... 19 2-2 Four Point Pin Loading. ......................... 23 2-3 Four Point Pin Loading, Dimensions Added ........... ... 23 2-4 Pin deflection versus distance for different loads. ............ 24 2-5 Distributed Pin Loading ......................... 25 2-6 Pin Cross Section ... ....................... ... 27 2-7 von Mises Effective Stress for Applied Load P = 100, 000lbf, Applied Torque T = 2240N . m ...... .................... 28 2-8 von Mises Effective Stress for Applied Load P = 100, 000lbf. Applied Torque T = 2240,3240,4240, 5240N - m (left to right). Maximum von Mises Stress (left to right): 230,241,255,272MPa .. ........... 28 2-9 Radial Gap Schematic .......................... 29 2-10 Gap Ratio R2 as a function of the Pin/Bushing Ratio R.......... 31 2-11 Gap Ratio RI as a function of the Pin/Bushing Ratio R............. 32 2-12 Pressure versus Length of Line Contact.... .. .. .. .. .. .. .. 34 3-1 Bolt Force for an Applied Torque T = 80lbf - ft ........ 51 3-2 Bolt Factor of Safety for Applied Torque T = 80lbf - ft .... 51 3-3 Total Force for a 10-Bolt Array, Applied Torque T = 80 lbf - ft 52 3-4 Bolt Optimization ............... ......... 52 3-5 Force Amplification versus Taper Angle ... .... ..... 53 3-6 Koyo Spherical Bearing ........ .... ......... 58 3-7 Pin Joint with Bushing Housing and Clamps ......... 60 3-8 Cross section of bearing ring assembly ... ..... .... 62 3-9 Section cut of bearing ring assembly ..... ......... 63 3-10 Exploded view of bearing ring assembly ... ......... 64 3-11 Torque Support ................ ......... 66 3-12 Seal design (original) ...... ....... .... .. 68 3-13 Seal design (revised) ......... .... ......... 69 3-14 Test Machine, Front View ........ .. ...... .. 70 3-15 Test Machine, Top View ........... ..... .... 70 3-16 Test Machine, Front View .......... ......... 71 4-1 Undercut Bushing (after testing failure) .. 74 11 5-1 Test Results for Standard Pin Joint. (a) Normal Load versus Time; (b) Third Load Cell versus Time (c) Temperature versus Time ... 76 5-2 Calculated (a) Reaction Torque and (b) Friction Coefficient for Stan- dard Pin Joint .................. ............. 77 5-3 Test Results for Undercut Bushing. (a) Normal Load versus Time; (b) Third Load Cell versus Time (c) Temperature versus Time ...... 77 5-4 Calculated (a) Reaction Torque and (b) Friction Coefficient for Under- cut B ushing ......... ....................... 78 A-I Four Point Pin Loading, Dimensions Added .............. 81 B-i Centroid Schematic ....................... ..... 83 D-1 Differential Screw Schematic ................. ..... 87 D-2 Free body diagram with respect to lower wedge .. .......... 87 D-3 Free body diagram with respect to upper wedge ............ 87 E-1 Taper Free Body Diagram ..... ................... 89 F-1 Bearing Ring, Page I ........ ................... 92 F-2 Bearing Ring, Page 2 ... ........................ 93 F-3 Bearing Ring, Page 3 ...................... ..... 94 F-4 Bearing Ring, Page 4 ................. .......... 95 F-5 Bushing Housing, Page 1 ........... .............. 96 F-6 Bushing Housing, Page 2 ...... ................... 97 F-7 Bushing Housing, Page 3 . ........................ 98 F-8 Bushing Housing, Page 4 .................... ..... 99 F-9 Bushing Clamp, Page 1 ................ .......... 100 F-10 Bushing Clamp, Page 2 ............ .............. 101 F-11 Bushing Clamp, Page 3 ....... ................... 102 F-12 Bushing Housing.Mount, Page 1 ..................... 103 F-13 Bushing Housing Mount, Page 2 ........... .......... 104 F-14 Pin Connector, Page 1 .......................... 105 F-15 Pin Connector, Page 2 .......................... 106 F-16 Pin Connector, Page 3 ................ .......... 107 F-17 Pin Clamp ................... .............
Details
-
File Typepdf
-
Upload Time-
-
Content LanguagesEnglish
-
Upload UserAnonymous/Not logged-in
-
File Pages131 Page
-
File Size-