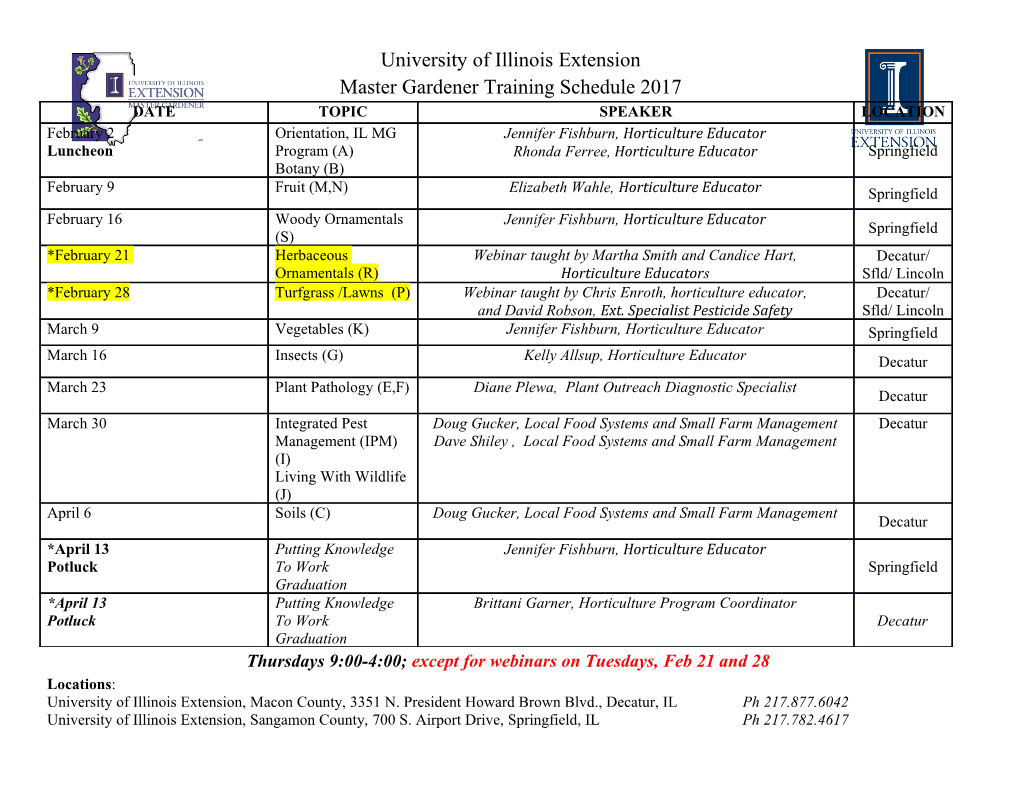
SPITZER SPACE TELESCOPE: OBSERVATORY DESCRIPTION AND PERFORMANCE Keyur C. Pate1 Spitzer Flight Engineering Office Manager, Jet Propulsion Laboratory Stuart R. Spath Spitzer Observatory Engineering Manager, Lockheed Martin Space Systems Company The Spitzer Space Telescope, the last of the four Great Observatories commissioned by the National Aeronautics and Space Administration, was successfully launched on August 25, 2003 from Kennedy Space Center. The engineering systems for Spitzer were developed by the Jet Propulsion Laboratory, Lockheed Martin Space Systems Company, and Ball Aerospace & Technology Corp. This paper provides an overview of Spitzer, a technical description of all the engineering subsystems, and the associated challenges involved in developing them to satisfy the mission requirements. In addition, this paper describes the performance of the engineering subsystems during the In-Orbit Checkout phase, the Science Verification phase, and the early portions of the Nominal Mission. INTRODUCTION The Spitzer Space Telescope, formerly known as the Space Infrared Telescope Facility (SIRTF), was commissioned by the National Aeronautics and Space Administration (NASA) to collect infrared science data of unprecedented quality and quantity. It was developed as the frnal component of the Great Observatories program, joining the Hubble Space Telescope, the Chandra X-ray Observatory, and the Compton Gamma Ray Observatory. In addition, Spitzer is a scientific and technical comerstone of NASA's Origins program. The project made use of some of the nation's premier technologies in fundamental scientific applications such as the search for other solar systems and studies of the earliest stages in the formation of galaxies similar to our own Milky Way. The immense potential of this mission was built upon the large defense-based investment in infrared detector arrays, with additional development under NASA sponsorship. Although the astronomical community has benefited from the breakthroughs in these arrays, their performance is degraded by factors of 100 to 1000 due to the heat radiation encountered on ground-based telescopes. Only with a cryogenically cooled telescope in space can the full potential for discovery be realized. Infrared observations are important for the following reasons: they reveal cool states of matter, they explore the universe hidden by cosmic dust, they access a wealth of spectral features, and they reach back to the early existence of the cosmos. Although the science capabilities of Spitzer are unparalleled, this paper does not discuss the details of the science instruments nor the science data collected thus far in the mission. Instead, it focuses on the engineering subsystems on- board the Observatory, both in the spacecraft (S/C) and the Cryogenic Telescope Assembly (CTA). The Observatory performance has been nothing short of exceptional. Using a subsystem-by-subsystem approach, this paper describes the design characteristics of the various components. It discusses significant subsystem challenges encountered during the development phase. It also contains a block diagram or schematic for each subsystem, illustrating the important hardware and software components. Finally, this paper documents the in-flight performance of each subsystem. MISSION OVERVIEW Mission Traiectorv. Spitzer was launched into an Earth-trailing solar orbit rather than a more conventional Earth orbit used by the other Great Observatories. The solar orbit was selected for a number of reasons: a) low launch energies allow for significant mass savings, b) the Observatory leaves behind the Earth's trapped radiation environment, c) Earth/Moon avoidance constraints are simplified, d) propellant for station-keeping or trajectory correction is not required, e) deep space tracking is simplified, and f) heat input from the Earth is eliminated, providing a vast improvement in the quality of the infrared observations. Mission Phases. Following launch, the Observatory was initialized and commissioned for routine operations during a 62-day period called In-Orbit Checkout (IOC) phase. The emphasis for the IOC phase was to bring the Observatory on- line safely, verify functionality of the instruments, telescope, and spacecraft, and demonstrate that the facility meets all level-1 requirements. After IOC, there was a 30-day period called the Science Verification (SV) phase. The purpose of the SV phase was to characterize the Observatory in-orbit performance, demonstrate capability for autonomous operations, conduct early release observations, and exercise the ground systems software, processes, and staffing sufficiently to commission the facility for routine operations. Following the SV phase, the Observatory began the Nominal Mission phase, which is expected to continue for at least the next 5 years. Udink/Downlink Strategv. During the Nominal Mission phase, commanding is performed primarily by uplinking a new master sequence once per week. The master sequence commands the science observations, the engineering calibrations, and the data playbacks. The sequence prioritizes the playbacks of the various science and engineering data. Spitzer playbacks occur twice per day, and are one hour or less in duration. While the duration can vary, the average playback provides up to 700 Mbytes of engineering and science data. When data is lost during transmission, a ground process is used to create a command file to retransmit the missing data. OBSERVATORY DESCRIPTION AND SYSTEM OVERVIEW The Observatory consists of five primary systems: the Spacecraft (S/C), the Cryogenic-Telescope Assembly (CTA), and three science instruments: the Infrared Array Camera (IRAC), the Infrared Spectrograph (IRS), and the Multiband Imaging Photometer for Spitzer (MIPS). The S/C is comprised of the solar panel, the S/C bus, and various support structures. 'fie SIC bus contains the hardware and software for the following engineering subsystems: Command & Data Handling (C&DH), Pointing Control Subsystem (PCS), Reaction Control Subsystem (RCS), Power Generation & Distribution (PG&D), Telecommunications Subsystem (Telecom), and Thermal Control Subsystem (TCS). The Flight Software (FSW) resides in the flight processor card of the C&DH and provides all the algorithms, parameters, and fault protection required by these subsystems. Baa: SrW . krL1'knl .... I. IJ. 9.. L .I Figure 1. observatory External Conjiguration The CTA is supported by a truss structure that is mounted on the upper deck of the S/C bus. The CTA consists of the outer shell, the 0.85-meter telescope assembly, the cryostat, and the multiple instrument chamber (MIC). The outer shell surrounds the telescope, is shielded from the sun by the solar panel assembly, and radiates heat to cold space in the anti-sun direction. Two intermediate shields isolates heat from the solar panel and the S/C bus. The telescope assembly is attached to the top of the vapor-cooled cryostat vacuum shell. The cryostat is supported by a truss structure that is attached to a base ring within the CTA. The MIC containing the three science instruments is mounted directly to the helium tank, with a high conductivity thermal path. COMMAND AND DATA HANDLING (C&DH) SUBSYSTEM Subsvstem Overview. The C&DH receives, interprets, validates, and executes both stored sequence commands and immediate execution commands. Through these commands, the C&DH coordinates and controls the activities and operations of the other S/C subsystems and the science instruments. In addition, the C&DH receives, collects, and multiplexes the science, engineering, and housekeeping data from the Observatory and provides the data stream to the Telecom subsystem for transmission to the ground. Spitzer uses a dual-string C&DH design to provide full redundancy. The C&DH provides redundant hardware command decoders, Reed-Solomon downlink encoding functions, and a stable clock to correlate data and events. The components of the C&DH are as follows: Flight Processor Card fFPC). The FPC is RAD6000 based and operates at 20 MHz. It contains 128 Mbytes of volatile memory and 3 Mbytes of non-volatile memory. Mass Memory Card (MMC). The two MMCs contain a total of 2 Gbytes of Dynamic Random Access Memory (1 Gbytes each) and are used to store science data and recorded engineering data. Fast Up link/Downlink (FULDL) Card, The FULDL card accepts a serial input command uplink data stream from the Telecom subsystem, and provides a serial telemetry stream to the Telecom subsystem for downlink. The FULDL card supports uplink rates from 7.8125 bps to 2000 bps and downlink rates from 40 bps to 2.2 Mbps. Pavload/PCS Interface Card (PPIC). The PPIC provides serial interfaces for payload use and unique interfaces for the PCS components. It also allows monitoring of the propulsion subsystem pressures and S/C temperatures, and general-purpose digital input/output. C&DH Module Interface Card (CMIC). The CMIC provides Ah3 side selection for both C&DH and PDDU. It implements the reset and select fault protection functions. The CMIC contains memory, power on reset circuitry, the spacecraft clock, and the flight processor test interface. CTA Driver Multiplexer Unit (CDMUL The CDMU provides the control and monitor functions necessary for CTA operations. The internally redundant CDMU operates the CTA components and provides telemetry of the CTA configuration. * 25to20MHz . 128 MBytes DRAM . 3 0 MBytes EEPROM * Custom RS-422 IK) * Custom Serial IO Figure 2. Command & Data Handling Subsystem Block Diagram In-Flight Performance.
Details
-
File Typepdf
-
Upload Time-
-
Content LanguagesEnglish
-
Upload UserAnonymous/Not logged-in
-
File Pages13 Page
-
File Size-