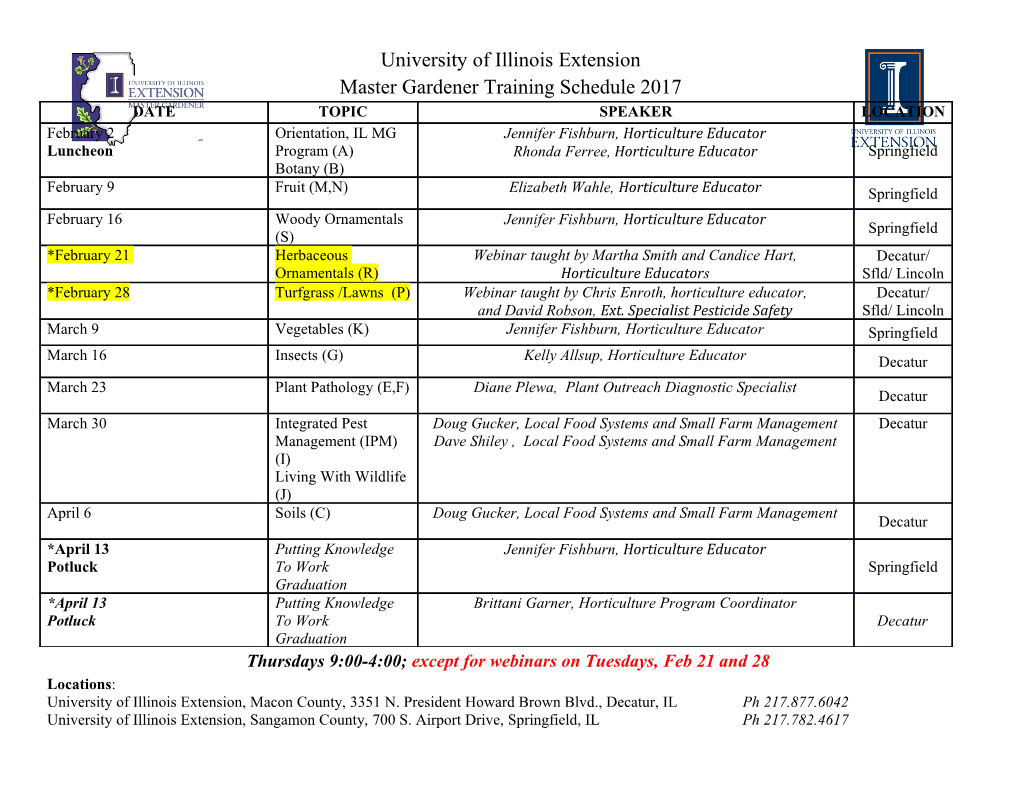
Synthesis Gas Treating with Physical Solvent Process Using Selexol Process Technology The Selexol process has proven to offer economic advantage, energy savings, and operating reliability for gas treating. The use of Selexol- II solvent lowers the ammonia production cost even further. Vinod A. Shah Norton Company, Akron, OH 44309 T.L. Huurdeman DSM Fertilizers, 6160 McGleen, The Netherlands The selection of a gas treating process SELEXOL SOLVENT PROCESS - This section today is more complex than in the past. describes the SELEXOL solvent, its The high cost of energy which has applications for synthesis gas treating prevailed since the 70's has brought many and an illustration of a plant and energy saving processes to the field of its performance and operating history; gas treating industry. Because ammonia and production is a high energy intensive process and because future energy cost NEW SOLVENT - This section presents a is uncertain and expected to be higher, new solvent which is specially formu- ammonia producers and process licensors lated for synthesis gas treatment. were forced to seek more energy- The solvent is named SELEXOL II efficient production methods. This solvent. The solvent and its economic brought many new synthesis gas treating benefits are discussed and compared with processes to the ammonia industry. the present SELEXOL solvent. Some of these processes may be more energy intensive, some have more SELEXOL SOLVENT PROCESS; maintenance, some have economics for removing carbon dioxide while some have General economics for removing hydrogen sulfide from coal and partial oxidation (POX) The solvent is a homologue of dimethyl gasified gas streams. ether of polyethylene glycol, and has been commercially proven in over 40 This paper describes the process that licensed facilities throughout the covers efficient treatment of all world. The process is owned and licensed varieties of synthesis gases. This by Norton Company Chemical Process process is a physical solvent process Products. The process and solvent called the SELEXOL(R) Solvent Process. characteristics of the solvent are The paper is presented into two sections : highlighted in Table 1. 216 TABLE 1 Table 2 summarizes the relative sol- ubilities of various gases in the SELEXOL solvent, process solvent. The actual solubility data is Characteristics proprietary, however the relative sol- ubilities can be compared for the * Non-toxic, non-polluting, non application (Basis: Ü2 = 1.0). reactive * Non-corrosive - biodegradable TABLE 2 * 151° C (304° F) flash point Relative Solubility of Gases in * 0.0007 mm Hg vapor pressure at 25° SELEXOL Solvent C (77° F) - low solvent losses * Selectively absorbs H2S, COS, RSH, Solubility CS2 in preference to C(>2 Component Ratio * Little or no heat required for solvent regeneration H2 (low solubility) 1.0 * Selectively removes heavy paraf- N2 1.5 fins, olefins, naphthenes and CO 2.2 aromatic byproducts of CH4 5 gasification C02 76 * no change of solvent is necessary COS 175 H2S 670 Its application and experience in the SO2 7000 synthesis gas treating area includes: 19,000 H20 55,000 C H 70,000 * Selective sulfur compound and car- 8 10 (high solubility) bon dioxide removal from gases originated from: As shown in Table 2, the H2S is much * natural gas more soluble than H2, N2, and CO2- If * partial oxidation H2S is present, the solubility differ- * coal gasification ences allows the selective removal of * coak gasification hydrogen sulfide from the gas stream * Removal of coal gas heavy hydro- leaving most of the carbon dioxide carbon byproduct unabsorbed. The SELEXOL Process was first In the case of carbon dioxide removal, applied to the treatment of ammonia because it is more soluble than hydrogen, synthesis gas in 1965. Since that time it allows selective removal of carbon the process has proven its applicability dioxide while leaving hydrogen and for synthesis gas treatment in 16 nitrogen essentially unabsorbed. installations, including a total of 10 ammonia plants. These facilities range In the case of physical solvents, in size from demonstration scale to the because the solubilities are enhanced at world-scale 1,360 t/d DSM ammonia higher pressures and lower tempera- facility. Several of these installa- tures, in order to keep the solvent tions are integral parts of "low energy" circulation rates low, the absorbers are ammonia plants. operated at feed pressures and cold -12 ° C (10°F) to ambient temperatures. Since Synthesis Gas Treating Operating the solubility decreases at lower Philosophy pressure, the desorption of the carbon dioxide from the solvent is achieved by SELEXOL Solvent is a physical solvent simply reducing the pressure of the which means that its capacity to absorb solvent. This characteristic eliminates gases is based on the physical solubi- the need of heat for solvent regenera- lities of gases in the solvent and not tion, and that is he primary reason why on any chemical reactions with the the process is an "Energy Saving solvent. Process". 217 Energy Saving Process - Highlights In the case of the SELEXOL Process, the temperature could be any temperature * Application: Steam reforming of in the range of refrigerated at -12" C natural gas or naphtha: (10° F) to water cooled at 49° C (120° F) . If the refrigeration route is - The heat requirement for solvent selected, the requirements are small and regeneration is essentially zero. usually supplied by the ammonia plant - Reformer steam-to-carbon ratio is refrigeration compression system. No independent of treating require- separate refrigeration unit is required. ment; allows minimum steam-to- carbon ratio to the primary Normally the height of the absorber reformer. is moderate in the range of +/- 36 m - Allows substantial heat recovery to 46 m (120 feet to 150 feet) . downstream of low temperature shift. Heat can be used for purposes Process other than solvent regeneration. H2S removal from POX and coal based - Product carbon dioxide is available synthesis gas. The process schematic at high pressures and at low water diagram is shown in Figure 1. content. - Moderate operating temperatures 10° F to ambient. * Application: POX or coal based HjS REMOVAL synthesis gas: MODUCI H2S removal section ACID GAS - highly selective for H2S over carbon dioxide which results in sub- stantial capital and energy cost savings for sulfur production - lower heat of regeneration FEED - low solvent circulation HEAT - ambient temperatures operation - no solvent degradation CO2 removal section - The heat requirement for solvent Figure 1. regeneration is essentially zero. - Product carbon dioxide is available at higher pressures and at low water content. The process unit is a simple operating - Operating temperatures -12° C unit which consists of a conventional (10°F) to ambient. absorber, a recycle flash drum system High carbon dioxide product and a reboiled stripper column. recovery. - No solvent degradation. The higher solubility of hydrogen sulfide and other sulfur compounds in solvent allows selective removal of Process Variables these compounds from the synthesis gas stream. The resultant acid gas For process optimization, the main stream is sufficiently concentrated in process variable is solvent circulation. hydrogen sulfide for Claus processing. The solvent circulation, however is dependent upon CO2 Removal From Synthesis Gas. The process flow diagram and process - the temperature of the solvent, and description for CÛ2 removal unit is discussed in greater detail in the next - absorber height section. 218 Synthesis Sas Treating - A Case packed absorber column with the lean History solvent entering at the top of the absorber. The carbon dioxide is In order to best evaluate the process absorbed by the solvent and collected in application, reliability, and solvent the bottom. capabilities, it is best to evaluate a specific plant performance and its several years of operating history. Carbon dioxide-rich solvent from the The SELEXOL unit at DSM - Ammonia plant bottom of the absorber then flows (formerly UCAM plant) is selected for through a power recovery hydraulic this purpose. turbine, which converts the pressure energy of the solvent to mechanical The DSM Ammonia plant, a part of DSM energy through reduction of pressure. Fertilizers division, is a 1,360 tons This energy is utilized by the main per day ammonia plant located at Geleen, circulating pump and reduces its energy the Netherlands. As of July 1989, the requirement by approximately 50%. plant has completed five years of successful operation. Rich solvent from turbine flows into the recycle flash drum where The plant was designed and constructed by Kellogg Continental, b.v., based on essentially all of the co-absorbed M. W. Kellogg's reduced-energy ammonia hydrogen and nitrogen is flashed. technology for steam reforming of The flashed gas is separated, compressed natural gas. The plant has achieved an and recycled back to the absorber. actual energy consumption of 7.0 million kcal per metric ton of ammonia (25.2 The rich solvent from the recycle flash million Btu/s.ton) without purge gas drum V-l flows into the low pressure recovery. The plant was commissioned flash drum V-2 where more than 70% of in July 1984 and was producing ammonia the carbon dioxide is flashed and only 3 1/2 weeks after initial start-up. recovered. Process Description. The SELEXOL unit In order to achieve the additional schematic process flow diagram is shown carbon dioxide recovery required at DSM in Figure 2. Ammonia Plant (DSM), the solvent from the low pressure drum is further flashed HIGH CO2 RECOVERY in a vacuum flash drum V-3. Vacuum is FLOW DIAGRAM generated by the vacuum compressor which simultaneously compresses the vacuum PRODUCT VENT flash gases up to the desired carbon dioxide product pressure. Should higher carbon dioxied product recovery (up to 97%) be desired, the solvent could be flashed to lower FEED pressures. The actual operating pressure of the vacuum flash drum depends upon the desired carbon dioxide AIR recovery, i.e.
Details
-
File Typepdf
-
Upload Time-
-
Content LanguagesEnglish
-
Upload UserAnonymous/Not logged-in
-
File Pages9 Page
-
File Size-