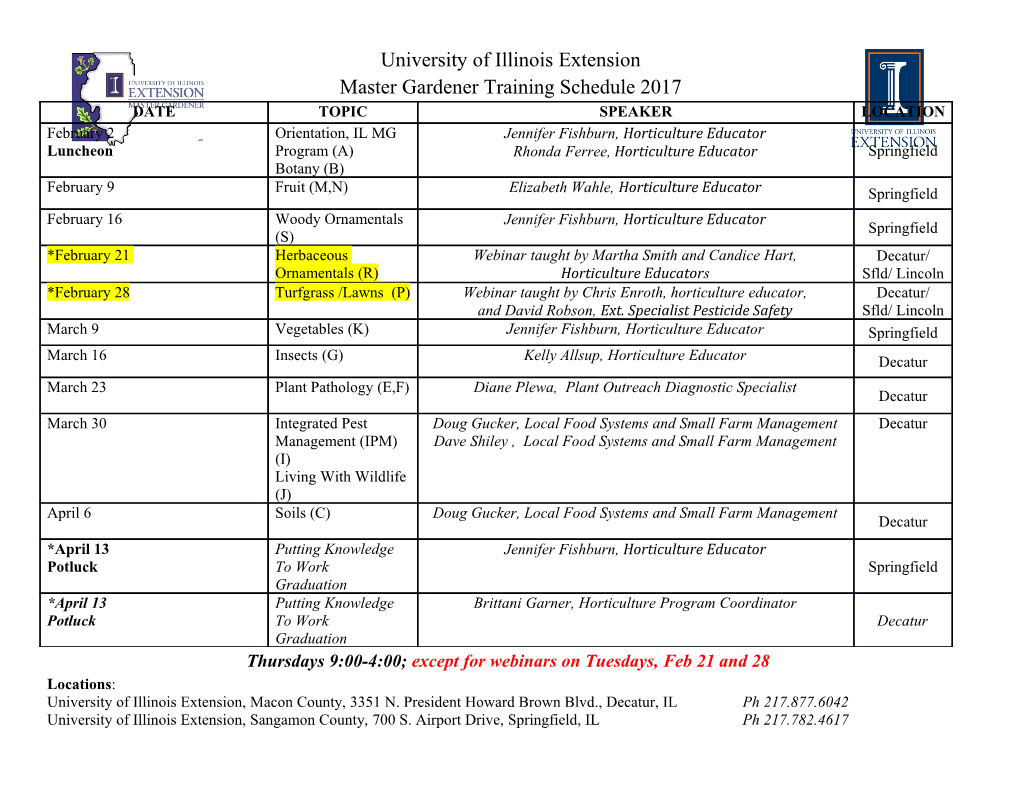
This article was downloaded by: 10.3.98.104 On: 29 Sep 2021 Access details: subscription number Publisher: CRC Press Informa Ltd Registered in England and Wales Registered Number: 1072954 Registered office: 5 Howick Place, London SW1P 1WG, UK Plastics Technology Handbook Manas Chanda Plastics Properties and Testing Publication details https://www.routledgehandbooks.com/doi/10.1201/9781315155876-3 Manas Chanda Published online on: 01 Nov 2017 How to cite :- Manas Chanda. 01 Nov 2017, Plastics Properties and Testing from: Plastics Technology Handbook CRC Press Accessed on: 29 Sep 2021 https://www.routledgehandbooks.com/doi/10.1201/9781315155876-3 PLEASE SCROLL DOWN FOR DOCUMENT Full terms and conditions of use: https://www.routledgehandbooks.com/legal-notices/terms This Document PDF may be used for research, teaching and private study purposes. Any substantial or systematic reproductions, re-distribution, re-selling, loan or sub-licensing, systematic supply or distribution in any form to anyone is expressly forbidden. The publisher does not give any warranty express or implied or make any representation that the contents will be complete or accurate or up to date. The publisher shall not be liable for an loss, actions, claims, proceedings, demand or costs or damages whatsoever or howsoever caused arising directly or indirectly in connection with or arising out of the use of this material. 3 Plastics Properties and Testing 3.1 Introduction There are two stages in the process of becoming familiar with plastics. The first is rather general and involves an introduction to the unique molecular structures of polymers, their physical states, and transitions which have marked influence on their behavior. These have been dealt with in Chapter 1. The second stage, which will be treated in this chapter, is more specific in that it involves a study of the specific properties of plastics which dictate their applications. Besides the relative ease of molding and fabrication, many plastics offer a range of important advantages in terms of high strength/weight ratio, tough- ness, corrosion and abrasion resistance, low friction, and excellent electrical resistance. These qualities have made plastics acceptable as materials for a wide variety of engineering applications. It is important therefore that an engineer be aware of the performance characteristics and significant properties of plastics. In this chapter plastics have been generally dealt with in respect to broad categories of properties, namely, mechanical, electrical, thermal, and optical. In this treatment the most characteristic features of plastic materials have been highlighted. An important facet of materials development and proper materials selection is testing and standard- ization. The latter part of this chapter is therefore devoted to this aspect. It presents schematically (in simplified form) a number of standard test methods for plastics, highlighting the principles of the tests and the properties measured by them. 3.2 Mechanical Properties Several unfamiliar aspects of material behavior of plastic need to be appreciated, the most important probably being that, in contrast to most metals at room temperature, the properties of plastics are time dependent [1–4]. Then superimposed on this aspect are the effects of the level of stress, the temperature of the material, and its structure (such as molecular weight, molecular orientation, and density). For example, with polypropylene an increase in temperature from 20 to 60°C may typically cause a 50% decrease in the allowable design stress. In addition, for each 0.001 g/cm3 change in density of this material there is a corresponding 4% change in design stress. The material, moreover, will have enhanced strength in the direction of molecular alignment (that is, in the direction of flow in the mold) and less in the transverse direction. Because of the influence of so many additional factors on the behavior of plastics, properties (such as modulus) quoted as a single value will be applicable only for the conditions at which they are mea- sured. Properties measured as single values following standard test procedures are therefore useful only as a means of quality control. They would be useless as far as design in concerned, because to design a plastic component it is necessary to have complete information, at the relevant service temperature, on the 307 Downloaded By: 10.3.98.104 At: 18:42 29 Sep 2021; For: 9781315155876, chapter3, 10.1201/9781315155876-3 308 Plastics Technology Handbook time-dependent behavior (viscoelastic behavior) of the material over the whole range of stresses to be experienced by the component. 3.2.1 Stress and Strain Any force or load acting on a body results in stress and strain in the body. Stress represents the intensity of the force at any point in the body and is measured as the force acting per unit area of a plane. The deformation or alteration in shape or dimensions of the body resulting from the stress is called strain. Strain is expressed in dimensionless units, such as cm/cm, in./in., or in percentage. Corresponding to the three main types of stress—tensile, compressive, and shear—three types of strain can be distinguished. Thus, tensile strain is expressed as elongation per unit length (Figure 3.1a), ‘=‘ ‘ − ‘ =‘ e = D 0 =( 0) 0 (3.1) and compressive strain as contraction per unit length (Figure 3.1b), ‘=‘ ‘ − ‘ =‘ e = D 0 =( 0 ) 0 (3.2) If the applied force or load, F, is tensile or compressive, the resulting tensile or compressive stress, s,is defined by s = F=A (3.3) where A is the cross-sectional area perpendicular to the direction in which the force acts (Figure 3.1a). The shearing stress is defined by a similar equation = t = Fs A (3.4) where Fs is the shearing force acting on an area A, which is parallel to the direction of the applied force (Figure 3.1c). Shear strain is measured by the magnitude of the angle representing the displacement of a certain plane relative to the other, due to the application of a pure shear stress, such as a in Figure 3.1c. The corre- sponding shear strain g may be taken equal to the ratio aa′/ab (=tan a). A shear strain is produced in torsion, when, for example, a circular rod is twisted by tangential forces, as shown in Figure 3.1d. For small deformations the shear strain, g, can be calculated from the triangle ABC g = BC=AB = rq=‘ (3.5) where r is the radius and q is the angle of twist. An ideal elastic material is one which exhibits no time effects. When a stress is applied the body deforms immediately, and it recovers its original dimensions completely and instantaneously when the F F Fs A a a´ dd´ d´ d´ α α lo l lo l l r d d r θ Fs b c B C (a)F (b)F (c)Fs (d) Fs ‘ − ‘ =‘ ‘ − ‘ =‘ FIGURE 3.1 (a) Tensile or longitudinal strain, e =( 0) 0. (b) Compressive strain, e =( 0 0) 0. (c) Shear strain, g =aa′/ab. (d) Shear strain in torsion g = rq=‘. Downloaded By: 10.3.98.104 At: 18:42 29 Sep 2021; For: 9781315155876, chapter3, 10.1201/9781315155876-3 Plastics Properties and Testing 309 stress is removed. When the ideal elastic body is subjected to tensile (or compressive) stress, the pro- portionality is expressed as s = E·e (3.6) where s is the applied stress (tensile or compressive) in lbf/in.2, kgf/cm2 or other appropriate units of force per unit cross-sectional area (Equation 3.3), e is the axial strain (Equation 3.1 and Equation 3.2), and E is the modulus of elasticity, commonly known as the Young’s modulus. The proportionality law as defined above is known as Hooke’s law. Likewise, if the ideal solid is subjected to a shear stress (t), then the shear strain (g) developed as a function of stress applied is given by the expression t = G·g (3.7) Here, the proportionality constant G is known as the shear modulus, also called the modulus of rigidity. The elastic constants in tensile deformation and shear deformation are summarized and compared below: Tensile (Figure 3.1a) Shear (Figure 3.1c) Stress s = F/A t = F/A ‘ − ‘ =‘ Strain e =( 0) g = tan a Modulus E = s/e G = t/g Compliance D = e/s J = g/t It may be noted that for an ideal elastic body compliance is the inverse of modulus. The modulus of elasticity, E, and the modulus of rigidity, G,asdefined above, apply under longitudinal and shear forces, respectively. When a hydrostatic force is applied, a third elastic modulus, the modulus of compressibility or bulk modulus, K, is used. It is the reciprocal of compressibility, b, and is defined as the ratio of the hydrostatic pressure, sh, to the volumetric strain, DV/V0: sh 1 K = = = (3.8) DV V0 b As indicated in Figure 3.1, an elongation (or compression) in one direction, due to an axial force, produces a contraction (or expansion) in the lateral direction, i.e., at right angles to the direction of the force. The ratio of the lateral strain to the longitudinal strain is called Poisson’s ratio v. It is an important elastic constant, For instance, a tensile stress, sx, which produces a tensile strain, ex in the x-direction will also produce a contractive strain, ey, in the y-direction, the two being related by − = v = ey ex (3.9) Combining Equation 3.9 with Equation 3.6 and rearranging yields − = ey = (v E)sx (3.10) fi Equation 3.10 thus de nes the contribution (ey) of the stress sx in the x-direction to the total strain in the y-direction.
Details
-
File Typepdf
-
Upload Time-
-
Content LanguagesEnglish
-
Upload UserAnonymous/Not logged-in
-
File Pages127 Page
-
File Size-