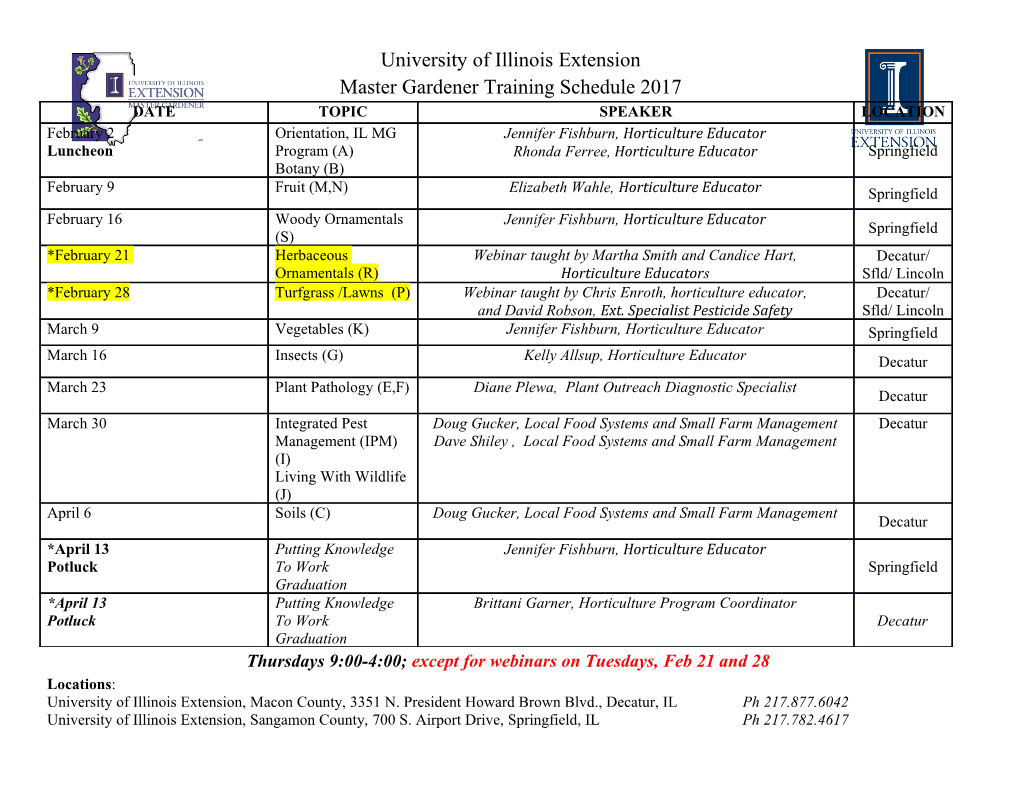
ISSN 2189-1222 UACJ Technical Reports Vol.6 Technical Reports 2019 No.1 Vol.6 No.1(2019) 本社 〒100-0004 東京都千代田区大手町1丁目7番2号 東京サンケイビル TEL:(03)6202-2600(代表) FAX:(03)6202-2021 Headquarters Tokyo Sankei Bldg.,1-7-2 Otemachi Chiyoda-ku, Tokyo 100-0004, Japan TEL. +81-3-6202-2600 FAX. +81-3-6202-2021 https://www.uacj.co.jp/ A-274 2012 TR10 AL建_210×297.pdf 1 2017/11/15 18:18 AL建_210×297.pdf 1 2017/11/15 18:18 Technical Reports Vol.6 No.1(2019) UACJ Technical Reports Vol.6 No.1(2019) 目 次 論 文 Nitridation Reaction of Aluminum and Magnesium Yu Matsui 2 in 5000 Series Aluminum Alloy Masaru Morobayashi Hirohisa Shiomi Koichi Takahashi Effect of Reversing Rotational Magnetic Field Akihiro Minagawa 9 on Grain Size Refinement Koichi Takahashi Shin-ichi Shimasaki Effects of Impurities and Processing Conditions in Al-1%Mn Alloys Hiroki Tanaka 15 on the Formation of Thermally Stabilized Substructures Wataru Narita Al-Mg-Si合金の集合組織形成に及ぼす圧延と熱処理の影響 日比野 旭 21 黒崎 友仁 高強度Al-Zn-Mg-Cu合金の組織と引張特性に及ぼす 則包 一成 25 熱間圧延時の温度とひずみ速度の影響 藤森 崇起 田中 宏樹 ろう付用Al-Si系合金材を用いたポーラスアルミニウムの 黒崎 友仁 33 接合におけるポーラスアルミニウムの気孔構造変化と液相の挙動 小 橋 眞 高田 尚記 鈴木 飛鳥 田中 宏樹 箕 田 正 技術展望・技術解説 高強度・高靭性アルミニウム合金の開発 森 久 史 43 箕 田 正 宮 﨑 悟 戸次 洋一郎 兒島 洋一 アルミニウム材新製造プロセス技術開発 兒島 洋一 51 布村 順司 津田 哲哉 宇井 幸一 上田 幹人 三宅 正男 TOPICS R&D Center(North America)のご紹介 八太 秀周 60 R&D Center(Thailand)のご紹介 渡辺 良夫 62 UACJ-産総研連携ラボ(冠ラボ)の紹介 森 久 史 64 兒島 洋一 田中 宏樹 野瀬 健二 時實 直樹 尾村 直紀 中 村 守 Technical Column アルミニウム技術史 −ジュラルミンから超々ジュラルミンまで−(第五回) 吉田 英雄 67 超々ジュラルミンと零戦(2) 超々ジュラルミンの零式艦上戦闘機への適用 超ジュラルミン24S(2024)はなぜ米国で開発できたか? 吉田 英雄 81 アルミニウムアノード酸化皮膜の構造制御による白色化 布村 順司 90 兒島 洋一 Serendipityに期待して 第二幕 田中 宏樹 95 公表資料一覧 2019年1月から2019年12月までに公表した資料 98 Published Papers UACJ Technical Reports Vol.6 No.1(2019) Contents Papers Nitridation Reaction of Aluminum and Magnesium Yu Matsui 2 in 5000 Series Aluminum Alloy Masaru Morobayashi Hirohisa Shiomi Koichi Takahashi Effect of Reversing Rotational Magnetic Field Akihiro Minagawa 9 on Grain Size Refinement Koichi Takahashi Shin-ichi Shimasaki Effects of Impurities and Processing Conditions in Al-1%Mn Alloys Hiroki Tanaka 15 on the Formation of Thermally Stabilized Substructures Wataru Narita Effects of Rolling and Heat Treatment on the Texture Formation of Akira Hibino 21 an Al–Mg–Si Alloy Tomohito Kurosaki Effects of Temperature and Strain Rate During Hot Rolling Kazushige Norikane 25 on Microstructure and Tensile Properties of Takayuki Fujimori High-Strength Al-Zn-Mg-Cu Alloy Hiroki Tanaka Change in the Porous Structure and the Liquid Phase Migration Tomohito Kurosaki 33 in the Bonding Porous Aluminum Using an Al-Si Based Alloy Sheet Makoto Kobashi for Brazing Naoki Takata Asuka Suzuki Hiroki Tanaka Tadashi Minoda Reviews Development of High Strength and High Toughness Aluminum Alloy Hisashi Mori 43 Tadashi Minoda Satoru Miyazaki Yoichiro Bekki Yoichi Kojima Development of New Production Processes for Aluminum Yoichi Kojima 51 Junji Nunomura Tetsuya Tsuda Koichi Ui Mikito Ueda Masao Miyake TOPICS Introduction of R&D Center (North America) Hidenori Hatta 60 Introduction of R&D Center (Thailand) Yoshio Watanabe 62 Introduction of Hisashi Mori 64 “UACJ-AIST-Collaborative Laboratory(Open Innovation Laboratory)” Yoichi Kojima Hiroki Tanaka Kenji Nose Naoki Tokizane Naoki Omura Mamoru Nakamura Technical Column History of the Aluminum Technology from Duralumin to Extra Super Duralumin (Part 5) Hideo Yoshida 67 Extra Super Duralumin and Zero Fighter (2) Application of Extra Super Duralumin to Zero Fighter Why was Super Duralumin 24S (2024) developed in the United States? Hideo Yoshida 81 Whitening by Structural Control on Aluminum Anodizing Film Junji Nunomura 90 Yoichi Kojima The Second Act in Expectation of Serendipity Hiroki Tanaka 95 公表資料一覧 Published Papers Papers, Reviews and Proceedings Published from Jan. 2019 to Dec. 2019 98 UACJ Technical Reports, Vol.6(2019),pp. 2-8 論 文 Nitridation Reaction of Aluminum and Magnesium in 5000 Series Aluminum Alloy* Yu Matsui**, Masaru Morobayashi*** Hirohisa Shiomi** and Koichi Takahashi**** The purpose of this study is to investigate the origin of nitride inclusions, Aluminum Nitride (AlN) in the aluminum casting process. The oxidation and nitridation behaviors of aluminum and magnesium under several melting conditions were experimentally researched. The results indicated that the sequential occurrence of the oxidation and nitridation reactions during the melting process was a key factor for producing nitride inclusions. The experimental results were consistent with the thermodynamic stability according to the standard Gibbs free energies of the formation of several oxides and nitrides, AlN and Mg3N2 . The method of preventing the formation of the nitride inclusions was both experimentally and theoretically derived. The point is that not having Mg3N2 generated in the magnesium ingot melting process in the furnace is very important to prevent generating the AlN inclusions since the existence of Mg3N2 in the aluminum melt causes the aluminum nitridation. Keywords: melting process, casting process, nitride inclusion, AlN, Mg3 N2 , 5000 series aluminum alloy 1) 2) 3) 4) 1. Introduction to be 700°C , 720°C - 740°C , 820°C , or 1200°C , thus it varies between the different experimental methods. Nitride inclusions are sometimes found inside of an In other words, a unified view of the AlN generation aluminum rolled sheet. These inclusions consist of Al, has not been obtained. Meanwhile, it was confirmed N, a trace of Mg and O. The nitride inclusion, AlN, is that AlN can be generated by adding Mg3N2 solid harder than the aluminum matrix and a pin-hole powder to the molten Mg-Al alloy or Al-Mg alloy5), 6). defect can occur during the rolling process if the Moreover, Ye et al. reported that the key mechanism inclusion size is larger than sheet thickness. AlN is is as described by the following two reactions which often found in Al-Mg alloys, like the 5000 series alloy, occurred when N2 gas is added to the molten Mg-Al and Mg is detected close to the AlN (Fig. 1). alloy7). Therefore, the origin of AlN seems to be related to 3Mg + N2 → Mg3N2 the existence of Mg. Mg3N2 + 2Al → 2AlN + 3Mg Many studies have been carried out regarding the nitridation reaction of aluminum and magnesium. The Thus, it has already been proved that the formation of AlN by bringing N2 gas directly into the generation of AlN has something to do with the Mg liquid aluminum has been experimentally tested. The element, but it has not been fully understood as to formation temperature of AlN, however, was reported what happens during the aluminum melting process and how nitrogen reacts with the aluminum via Al Mg O N magnesium. In the practical aluminum melting process, magnesium ingot is normally added to the aluminum Fig. 1 EPMA image of AlN inclusions found in an Al-Mg melt in a melting furnace or a holding furnace. The alloy sheet. dry air in the furnaces contains 78% nitrogen, 21% * This is a revised prepublication version of an article published in Light Metals (2018), 885-893 The final published version is available online at https://doi.org/10.1007/978-3-319-72284-9_115 ** Casting Technology Department, Nagoya Works, Flat rolled Products Division, UACJ Corporation *** Casting Plant, Production Department, Nagoya Works, Flat rolled Products Division, UACJ Corporation **** UACJ North America, Inc., Ph. D. (Eng.) 2 UACJ Technical Reports,Vol.6(1)(2019) Nitridation Reaction of Aluminum and Magnesium in 5000 Series Aluminum Alloy 3 oxygen, 0.9% argon, 0.04% carbon dioxide, and small Table 1 Heating conditions of the magnesium ingot in several atmospheres. amounts of other gases. It is postulated that Mg tends Atmosphere Oxigen level Holding time to form MgO if it reacts with the air because MgO is A1 Air 19.0% 1 hour thermodynamically more stable than Mg3N2. A2 Air 19.0% 3 hours However, there are the essential elements Al and N A3 N2 purged 2.3% 1 hour A4 N2 purged 2.3% 3 hours for producing AlN in the actual furnaces. The purpose of this study is to clarify the origin of the Table 2 Holding conditions of the pre-burned nitride inclusions, focusing on the magnesium melting magnesium in the aluminum melt. process in the aluminum melt. Heating condition Atmosphere Holding time B1 A2(Air) Air 1 hour B2 A2(Air) Air 3 hours 2. Experimental Procedure B3 A4(N2 purged) Air 1 hour B4 A4(N2 purged) Air 3 hours 2.1 Preliminary melting experiment of magnesium ingots in aluminum melt In order to investigate what happens by adding the To demonstrate the melting behavior of magnesium burned magnesium ingot to the aluminum melt, each in a practical melting furnace, a preliminary of the was then added to the pure aluminum melt experiment that the addition of magnesium ingots to which was maintained at 800°C, and each of the liquids the aluminum melt without stirring was conducted. with the residues was stirred by a graphite stick. Two small pieces of magnesium ingot (100 g) were After stirring, these liquids were held under air at added to the aluminum melt (3 kg), which was melted four isothermal conditions as shown in Table 2 and in advance in a graphite crucible at 800°C. Several quenched with a small iron mold. These cast samples stages of magnesium ingot melting process were were polished and observed by a scanning electron visually observed, and the temperature was microscope (SEM) and a electron probe microanalyer measured. (EPMA). 2.2 Heating experiment of magnesium and holding 3. Results and Discussion experiment of magnesium in aluminum melt Separating into the burning process of magnesium 3.1 Melting of magnesium ingots in aluminum melt and the melting process of magnesium in aluminum Photographs of several melting stages of magnesium melt to comprehend oxidation and nitridation reactions ingot in aluminum melt are shown in Fig.
Details
-
File Typepdf
-
Upload Time-
-
Content LanguagesEnglish
-
Upload UserAnonymous/Not logged-in
-
File Pages114 Page
-
File Size-