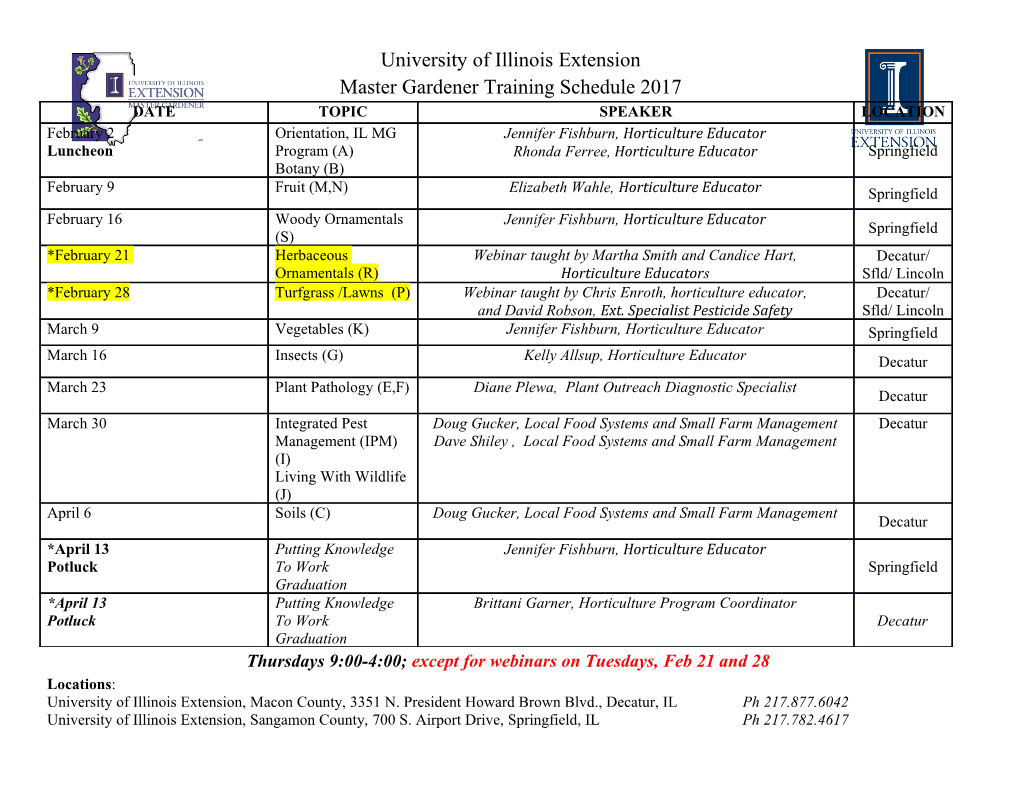
In Situ Leach (ISL) Mining of Uranium (June 2009) l Most uranium mining in the USA and Kazakhstan is now by in situ leach methods, also known as in situ recovery (ISR). l In USA ISL is seen as the most cost effective and environmentally acceptable method of mining, and Australian experience supports this. l Australia's first ISL uranium mine is Beverley, which started operation late in 2000. The proposal for Honeymoon has government approval and it is expected to be operating in 2008. Conventional mining involves removing mineralised rock (ore) from the ground, breaking it up and treating it to remove the minerals being sought. In situ leaching (ISL), also known as solution mining, or in situ recovery (ISR) in North America, involves leaving the ore where it is in the ground, and recovering the minerals from it by dissolving them and pumping the pregnant solution to the surface where the minerals can be recovered. Consequently there is little surface disturbance and no tailings or waste rock generated. However, the orebody needs to be permeable to the liquids used, and located so that they do not contaminate ground water away from the orebody. Uranium ISL uses the native groundwater in the orebody which is fortified with a complexing agent and in most cases an oxidant. It is then pumped through the underground orebody to recover the minerals in it by leaching. Once the pregnant solution is returned to the surface, the uranium is recovered in much the same way as in any other uranium plant (mill). In Australian ISL mines (Beverley and the soon to be opened Honeymoon Mine) the oxidant used is hydrogen peroxide and the complexing agent sulfuric acid. Kazakh ISL mines generally do not employ an oxidant but use much higher acid concentrations in the circulating solutions. ISL mines in the USA use an alkali leach due to the presence of significant quantities of acid-consuming minerals such as gypsum and limestone in the host aquifers. Any more than a few percent carbonate minerals means that alkali leach must be used in preference to the more efficient acid leach The Australian government has published a best practice guide for in situ leach mining of uranium, which is being revised to take account of international differences. Figure 1 shows a pictorial representation of the ISL process. http://www.world-nuclear.org/info/inf27.html 1 / 10 Fig 1. Pictorial representation of the ISL process In either the acid or alkali leaching method the fortified groundwater is pumped into the aquifer via a series of injection wells where it slowly migrates through the aquifer leaching the uranium bearing host sand on its way to strategically placed extraction wells where submersible pumps pump the liquid to the surface for processing. ISL uranium mining was first tried on an experimental basis in Wyoming during the early 1960s. The first commercial mine began operating in 1974. Today most Kazakh and US uranium production comes from ISL mining. Several projects are licensed to operate there, (in Wyoming, Nebraska and Texas) and most of the operating mines date from the 1990s. They are small (under 1000 t/yr) but they supply most of the US uranium production. About 26% of world uranium production is by ISL (including all Kazakhstan and Uzbekistan output). ISL can also be applied to other minerals such as copper and gold. Uranium deposits suitable for ISL occur in permeable sand or sandstones, confined above and below by impermeable strata, and which are below the water table. They may either be flat, or "roll front" - in cross section, C-shaped deposits within a permeable sedimentary layer. Such deposits were formed by the lateral movement of groundwater bearing oxidised uranium minerals through the aquifer, with precipitation of the minerals occurring when the oxygen content decreased, along extensive oxidation-reduction interfaces. The uranium minerals are usually uraninite (oxide) or coffinite (silicate) coatings on individual sand grains. See also Appendix. The ISL process essentially reverses this ore genesis, in a much shorter time frame. There are two operating regimes for ISL, determined by the geology and groundwater. If there is significant calcium in the orebody (as limestone or gypsum), alkaline (carbonate) leaching must be used. Otherwise, acid (sulfate) leaching is generally better. In this case the leach solution is at a pH of 2.5 - 3.0, about the same as vinegar. Techniques for ISL have evolved to the point where it is a controllable, safe, and environmentally benign method of mining which operates under strict operational and regulatory controls. Due to the low capital costs (relative to conventional mining) it can often be a more effective method of mining low-grade uranium deposits. ISL Wellfield The design of ISL wellfields varies greatly depending on the local conditions such as permeability, sand thickness, deposit type, ore grade and distribution. Whatever the type of pattern used, there is a mixture of injection wells, to introduce the leach solution to the orebody, and extraction wells with submersible pumps used to deliver pregnant solution to the processing plant. Wells are typical of normal water bores. Where large sheet-like deposits exist, such as in Kazakhstan, rows of injection wells interleafed with rows of extraction wells can be used cost effectively as shown in Figure 2. Fig 2. Alternating lines of injection and extraction This pattern has a relatively low installation cost and is simple to install. However the time taken to recover the uranium under leach is extended due to the large distances between the well types (typically 50-60m). In most western applications (and Kazakh operations in channels narrower than 60m) closer spaced patterns are employed to recover the uranium at a faster rate (per unit area) than the alternating line patterns. The most common type of pattern employed as illustrated in figure 3 are: - 5-Spot patterns (usually 20-30m between like wells). - 7-Spot patterns (usually 30-40m diameter). Fig 3. Five and seven spot patterns of injection and extraction These tighter patterns are generally used effectively in narrower palaeochannel type deposits where flexibility in the installation is needed. The installed costs of these wellfields are generally higher, so to ensure maximum recovery of the uranium, the following secondary measures can be taken: - Flow reversals - converting injection wells to extraction wells where required. - Infill wells - to increase recovery from higher grade portions of the wellfield. Beverley wellfield In Australia installed wells are hydraulically pressure tested to 150% of their design operating pressure to ensure no leakage to overlying aquifers is possible. Operating wells are also re-tested after a period of 12 months of operation. Whichever pattern type is used, the wellfields (usually a production unit that feeds to a single header house) are progressively established over the orebody as uranium is depleted. A series of monitor wells are situated around each mineralised zone to detect any movement of mining fluids outside the mining area. The wells are cased to ensure that liquors only flow to and from the ore zone and do not affect any overlying aquifers. In the USA the production life of an individual ISL well pattern is typically one to three years. Most of the uranium is recovered during the first six months of the operation. The most successful operations have achieved a total overall recovery of about 80% of the ore, the minimum is about 60%. In Australia individual well patterns can operate from between 6 and 18 months with target recoveries of around 70% in 12 months. The progressive flow through the aquifer also traps clay and silt in the permeable sediments. These can be dislodged to some extent by using higher pressure injection or by reversing the flow between injection and production wells. However the flow capacity of injection wells is generally always on a downward trend thought the life of the well. Uranium Recovery The submersible pumps initially extract native groundwater from the host aquifer prior to the addition of uranium complexing reagents (acid or alkaline) and an oxidant (hydrogen peroxide or oxygen) before injection into the wellfield. The leach liquors pass through the ore to oxidise and dissolve the uranium minerals in situ. Depending on the type of leaching environment used the uranium will be complexed as either a 4- uranyl sulphate, predominantly UO2(SO4)3 , in acid leach conditions or a uranyl carbonate, 4- predominantly UO2(CO3)3 in a carbonate leach system. This can then be precipitated with an alkali, eg as sodium or magnesium diuranate. In either case the pregnant solution from the production wells is pumped to the treatment plant where the uranium is recovered in a resin ion exchange (IX) or liquid ion exchange (solvent extraction - SX) system. IX is used in the vast majority of ISL operations in Kazakhstan, the USA and Australia. In terms of operating and capital costs IX is the preferred processing option. In situations where the groundwater has a high concentration of ions that may compete with the uranyl complexes for active resin sites, such as chloride and nitrates, the use of IX becomes unattractive due to low uranium loadings on the resin. (As a general rule if chloride concentrations in the groundwater is above 5-6 g/L the capture of uranium by IX becomes uneconomical.) SX is better with very saline groundwater (17-20 g/L) as at Honeymoon, though other process challenges can arise. Further treatment for IX in Australia involves stripping the uranium from the resin either with a strong acid or chloride solution or a combination of both in a batch operation. In Kazakh operations the resins are generally stripped with a nitrate solution in a semi-continuous cycle.
Details
-
File Typepdf
-
Upload Time-
-
Content LanguagesEnglish
-
Upload UserAnonymous/Not logged-in
-
File Pages10 Page
-
File Size-