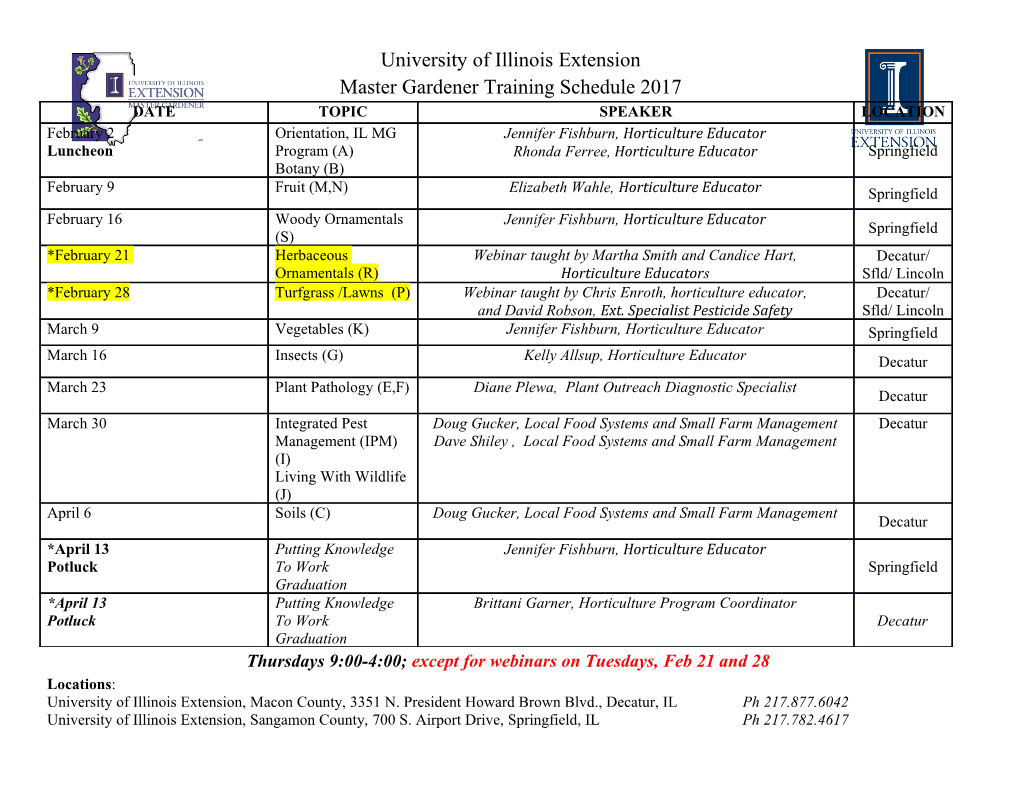
Cellulose Acetate Membrane Spanning 4 and Adhesion Properties To create a suspended, organic membrane over an inorganic substrate with large topographical features requires various strategies. This chapter discusses the spanning of a cellulose acetate membrane across silicon microchannels and the method used for good adhesion between cellulose acetate and the substrate. An overview of adhesion theory is first discussed along with factors that affect adhesion and techniques used to characterize adhesion strength. Porous polymer films, prepared using phase inversion techniques, are coated onto inorganic silicon substrates and then characterized for adhesion strength. Experimental data from a blister test setup was used to measure the critical pressure point when a leak was observed on both chemically and mechanically roughened surfaces with a spin-coated, phase-separated cellulose acetate film. These films were observed to have the best adhesion with surfaces treated with octadecyltrichlorosilane (OTS), withstanding pressures above 50 kPa. The last section of this chapter presents the theory and experimental results for spanning cellulose acetate membranes across silicon microchannels. Based on the surface properties of the substrate and the material properties of the cellulose acetate lacquer, it was possible to successfully span 75 µm wide silicon microchannels. 4.1. Polymer adhesion overview Polymeric films are widely used in the microelectronic industry in such application areas as photoresists, interlayer dielectrics, and packaging [87]. Porous polymers, such as those formed using the phase inversion process, have gained interest in the fields of filtration, drug delivery, protein separation, and microdialysis [187]. Unfortunately these films undergo a considerable amount of residual stress after formation, causing them to delaminate from the substrate. In order to enhance film adhesion, microfabricated structures as well as chemical coupling agents have been employed to adhere polyimide films to silicon substrates [71, 75]. In this section a short 89 background on the theory of adhesion, characterization techniques used to gauge the adhesion strength, and factors that affect adhesion quality will be discussed. 4.1.1. Theories of Adhesion Adhesion is defined as the state in which two surfaces are held together by physical and/or chemical attraction. The main adhesion theories include (i) mechanical interlocking, (ii) interdiffusion, (iii) adsorption and surface reaction, and (iv) electrostatic surface attraction. The next four sections provide a description of each theory. Due to the variety of materials and the diversity of adhesion conditions, the field of adhesion is a complex topic and can’t be defined solely by a single model or theory. In reality, several adhesion theories are involved simultaneously to describe an adhesion interface. In the following discussion, the terms ‘coating’, ‘film’, and ‘membrane’ are used interchangeably. 4.1.1.1. Mechanical interlocking theory. The mechanical interlocking theory of adhesion proposes that surface irregularities, such as cavities, pores, and asperities shown in Figure 4-1, are the determining factor for adhesion strength between a coating and a substrate, due the ability of the coating to key and latch to the substrate. The situation is analogous to using a dovetail joint to hold two pieces of wood together. In many cases, the improvement in adhesion due to mechanical interlocking structures can be attributed to the increase in the interfacial area due to surface roughness (as long as the wetting of the surface occurs). Surface roughness increases the adhesive strength of films by promoting wetting as well as providing mechanical anchoring sites. Packham and coworkers found high values of peel strength for polyethylene on metallic substrates when a rough and fibrous-type oxide surface was formed on the substrate [128]. Jiang et al. used mushroom-shaped silicon microstructures to adhere a polyimide film to the substrate [71] Figure 4-1. (left) Smooth surface. (right) rough surface on a microscopic scale allowing for interlocking with coating. Chip 90 One of the criticisms of the mechanical interlocking theory is that the adhesion improvement does not necessarily result from the latching or keying mechanism but that the surface roughness can increase the energy dissipated viscoelastically around a failure point. The scale of the roughness of surfaces can vary from macroscopic to submicroscopic. The factor that controls the rate of penetration of a liquid into cavities and crevices is analogous to the penetration of a liquid into a capillary. The rate of penetration is greatest if the surface tension of the coating is high. The rate is fastest when the contact angle is zero, in this circumstance the surface tension of the liquid is less than that of the solid substrate. The main coating property that an experimentalist can control is the viscosity. The lower the viscosity, the more rapid the penetration. Yet total penetration of an adhesive into cavities and pores is not always possible because of back pressure from entrapped air within these cavities. Mechanical interlocking structures were explored as a mechanism to improve adhesion of thin cellulose acetate membranes onto silicon wafers. Unlike the polyimide films investigated by Jiang et al. [3], the films prepared are porous, suspended over microcavities, and undergo delaminating forces from pressure-driven fluid flow. 4.1.1.2. Interdiffusion theory This theory proposes the adhesion mechanism to mutual interdiffusion of surface layers to form an interphase region. Similar to the mechanical interlocking theory, interdiffusion involves interpenetration of the adhesive material onto the substrate, yet this is done at the molecular level. The interdiffusion theory was originally proposed as a way to explain the autoadhesion (the capability of a material to adhere to itself) of rubbery polymers [182]. When two polymer samples are brought to intimate contact, the polymer chains in the rubbery state possess enough mobility to diffuse across the initial interface. After some time the interface is blurred, and the interfacial adhesion strength becomes close the bulk cohesion strength. Solvent bonding or welding is an interesting case of coupling by interdiffusion. Solvent bonding is a process where the surfaces of polymers to be joined are treated with a solvent. This swells and softens the surfaces and by applying pressure on the joint and with the evaporation of the solvent, 91 the two surfaces bond. Interdiffusion presumably occurs in the presence of the solvent, even if the polymers are immiscible to each other in a lacquer. 4.1.1.3. Adsorption and surface reaction theory Adsorption theory of adhesion is the most widely applicable and assumes that adhesive materials will adhere to a substrate due to interatomic and intermolecular forces at the interface. The most common interfacial forces are from van der Waals and Lewis acid-base interactions and less frequently ionic, covalent, or metallic interfacial bonds. The magnitude of these forces can be generally related to fundamental thermodynamic quantities, such as surface free energies of both the adhesive and adherend. Covalent bonds are generally considered the strongest bonding force in comparison with physical interactions such as van der Waals, which are secondary force interactions. The typical strength of a covalent bond is of the order of 100 to 1000 kJ/mol, while van der Waals interactions and hydrogen bonds do not exceed 50 kJ/mol. The formation of chemical bonds relies on the reactivity of both the coating and the substrate. The best adhesion method is multiple, strong linkages across the interface between two materials. Two distinct surface modification methods that provide a large number of linkages to improve adhesion based on adsorption theory, are surfactants and silane coupling agents. In addition, it is possible to modify the polymer structure to improve adhesion to the substrate using polymer graft copolymerization. These modification methods will now be overviewed briefly. 4.1.1.3.1. Surfactants A surfactant is a substance that has the property of absorbing onto surfaces and altering the free energy of these surfaces [145]. Surfactants essentially lower the surface tension of coatings. Surfactants are usually organic compounds that are amphipathic, meaning they contain both hydrophobic groups (the "tail" of the molecule) and hydrophilic groups (the "head" of the molecule). These two different chemical groups have the purpose of one end being compatible with the liquid to be modified and the other having a lower surface tension. Therefore, they are typically soluble in both organic solvents and water. A surfactant can be classified by the presence of charged groups in its head. A nonionic surfactant has no charge groups in its head while the head of an ionic surfactant carries a net charge. If that net charge is negative, the surfactant is more 92 specifically called anionic; if the net charge is positive, it is called cationic; if both positive and negative charges are present then it is called zwitterionic. Since most surfaces are negatively charges and in order to make those surfaces hydrophobic by use of a surfactant, the best type is a cationic surfactant. This surfactant will adsorb onto the surface with its positively charged hydrophilic head group oriented toward the negatively charged surface and its hydrophobic group oriented away from the surface.
Details
-
File Typepdf
-
Upload Time-
-
Content LanguagesEnglish
-
Upload UserAnonymous/Not logged-in
-
File Pages41 Page
-
File Size-