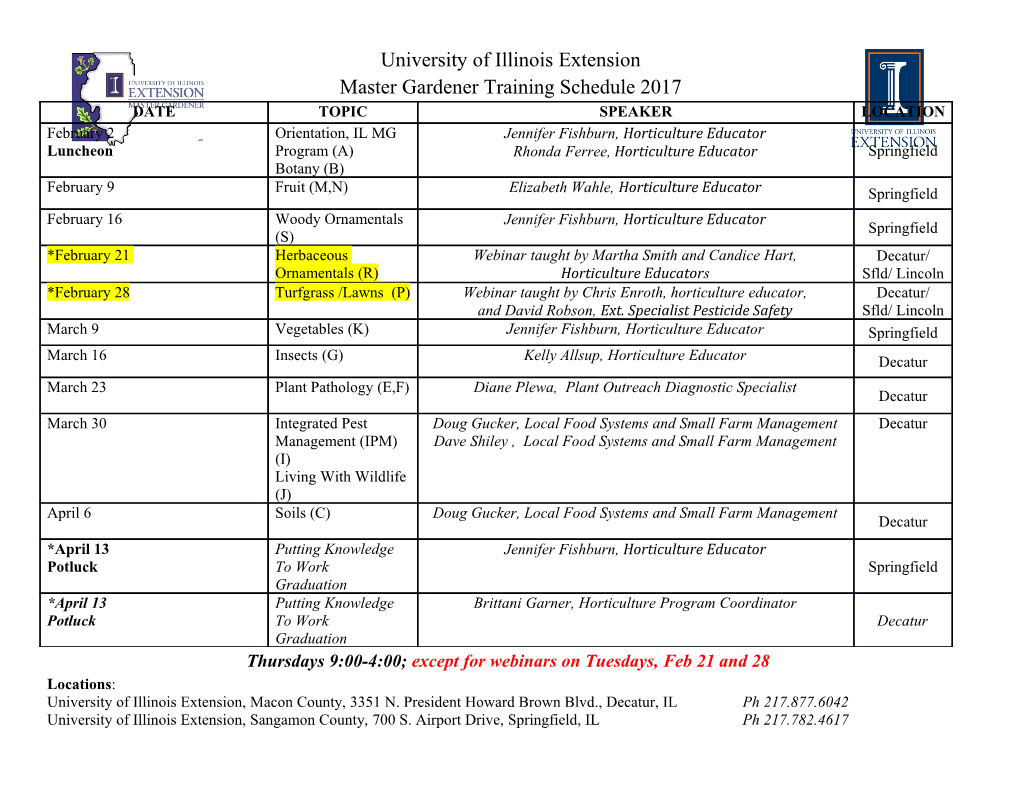
PeroxideDelignification Delignification of aspen wood using hydrogen peroxide and peroxymonosulfate Edward L. Springer Chemical engineer, USDA Forest Service, Forest Products Laboratory, One Gifford Pinchot Dr., Madison, Wis. 53705-2398 ABSTRACT Treatment of finely divided aspen wood with peroxymonosulfate KEYWORDS at low pH, followed by alkaline extraction, resulted in nearly complete lignin Aspen removal. Treatment of the wood with hydrogen peroxide at optimum pH (pH Delignification 11), followed by alkaline extraction, removed at most 36% of the original Hydrogen lignin. Peroxymonosulfate can be easily produced by mixing hydrogen peroxide peroxide with concentrated sulfuric acid. Peroxymonosulfuric acid Sodium hydroxide Sulfuric acid Wood and other lignocelluloses can be (3) studied the delignification of Delignification using readily delignified using organic southern pine kraft pulp with alkaline hydrogen peroxide peroxides such as peracetic and per- hydrogen peroxide. They also found formic acids (1). With the exception that approximately half the lignin One-gram samples of mature aspen of studies using alkaline hydrogen present in the pulp could be removed. wood, ground to pass through a No. peroxide, little research has been done In both cases, the most efficient 40 mesh screen. were treated at room on delignification with inorganic delignification occurred under reac­ temperature (22°C) with a 5.0% solu­ peroxides. The purpose of this work tion conditions where no stabilizers (to tion of hydrogen peroxide adjusted to was to determine whether acidic inhibit peroxide decomposition) were either pH 2.0 with sulfuric acid or to hydrogen peroxide could delignify present and the rate of peroxide pH 11.0 or 11.5 with sodium hydrox­ aspen wood and. if not, whether decomposition was at a maximum. ide. A liquor-to-wood ratio of 10:1 was peroxymonosulfuric acid made by For comparison, we initially studied used, and the treatment time was 3 reacting hydrogen peroxide and sul­ the delignification of aspen wood with days except for the pH 11.5 condition, furic acid could delignify the wood. alkaline hydrogen peroxide. where treatment time was 12 days. Aspen wood (Populus tremuloides Acidic hydrogen peroxide is a much Samples were also treated at the Michx.) was chosen for study because stronger oxidizing agent than alka­ natural pH (pH 5.5) of the 5.006 it is easily delignified. line hydrogen peroxide. Under acidic solution of hydrogen peroxide. The A few studies have been performed conditions, the lignin macromolecule samples were stirred initially but not on delignification of lignocellulosic is extensively degraded and dissolved agitated during treatment. After materials with alkaline hydrogen by hydrogen peroxide (4, 5). It seemed peroxide treatment, each sample was peroxide. Gould (2) found that approx­ likely, therefore, that acidic solutions extracted with 1.0% NaOH at 50°C for imately half the lignin present in of hydrogen peroxide should more 3 h. The results from these treatments agricultural residues, such as wheat readily delignify wood than alkaline are shown in Table I. straw, could be solubilized when the solutions. The most selective delignification residue was treated at 25°C with an occurred at pH 11.0, where 32% of the alkaline solution of hydrogen perox­ original lignin and 17% of the original ide. The delignification was most carbohydrate were removed. Divid­ effective at pH 11.5. McDonough et al. ing the total weight of carbohydrate January 1990 TappiJournal 175 removed by the weight of lignin I. Delignification of 40-mesh aspen wood with 5% hydrogen peroxide at a liquor to wood ratio removed (C/L ratio) gives an index of of 10·1 the selectivity of lignin removal (Ta­ ble I). Increasing the pH to 11.5 and the treatment time to 12 days resulted in a small increase in lignin removal (to 36% of the original); however, the selectivity was slightly reduced (from C/L ratio 2.2 to 2.4). Lowering the pH to 2.0 increased the lignin removal only slightly from what it was at pH 5.5. Much more lignin was removed under alkaline conditions. Residual peroxide levels were not determined. To determine the effect of treat­ ment temperature on lignin removal, runs were made at 80°C. The results from these runs are also shown in Table I. The most effective delignifi­ cation again occurred at pH 11.0; however, the selectivity of lignin removal was somewhat reduced from II. Production of peroxymonosulfuric acid by mixing hydrogen peroxide and concentrated sulfuric that at room temperature. None of the acid at ice bath temperature conditions studied resulted in low lignin contents in the final residue. Since acidic hydrogen peroxide was ineffective in delignification of aspen wood, we decided to attempt to delig­ nify the wood with peroxymonosulfur­ ic acid produced by adding sulfuric acid to hydrogen peroxide. Generation of peroxymonosulfate Adding concentrated sulfuric acid to Several experiments were per- Delignification solutions of hydrogen peroxide results formed to determine the conditions using peroxymonosulfate in the production of peroxymonosul­ needed to produce significant quanti­ furic acid (6). This acid is a much ties of peroxymonosulfuric acid. Cold Small quantities of the solutions stronger oxidizing agent than hydro­ hydrogen peroxide (2°C) was placed containing peroxymonosulfate were gen peroxide. It can also be produced in a vial in an ice bath: concentrated carefully diluted with distilled water by adding peroxydisulfuric acid salts sulfuric acid at room temperature and used to treat 1-g samples of the to concentrated sulfuric acid. Zakis was added, and the two were tho- No. 40 mesh aspen wood at room and Neiberte (7) found that they could roughly mixed. An aliquot of this temperature (22°C). The weight of the delignify spruce sawdust to low lignin mixture was titrated using the meth- peroxide-acid mixture used for a levels using peroxymonosulfuric acid od of Greenspan and MacKellar (8) to given total weight of solution (used to in 50% H2SO4 at 20°C. They produced determine the yield of peroxymono- treat 1.00 g of wood) is shown in the the peroxymonosulfuric acid by ad­ sulfuric acid produced. Results of third column of Table III. The con- ding the ammonium salt of peroxydi­ these procedures are shown in Table centration of the peroxymonosulfate sulfuric acid to concentrated sulfuric 11. Using 32% H2O2 and a mole-to- anion in the initial solution is given in acid. A high concentration of sulfuric mole ratio of acid to peroxide of 1:1. Column 4, and the equivalent total acid seemed to be necessary for effec­ the yield of peroxymonosulfate was percentage of hydrogen peroxide in tive lignin removal. Based on these only 8%. This indicates that the yield the initial solution is given in Column findings, hydrogen peroxide and was probably negligible when a few 8. The treated residues were extracted sulfuric acid mixtures with a large drops of concentrated sulfuric acid as described previously with 1.0% excess of acid present should delignify were added to 5.0% H2O2 to adjust the NaOH. finely divided aspen wood. Our pre­ pH to 2.0. Using more concentrated Initial runs were made using per- vious data indicate that simply adjust­ hydrogen peroxide and a higher mole- oxymonosulfate prepared by Proce­ ing a 5.0% solution of H2O2 to pH 2.0 to-mole ratio of acid to peroxide dure 1. This resulted in very dilute with concentrated sulfuric acid did greatly increased the yield of peroxy- solutions of peroxymonosulfate con­ not result in a solution that effectively monosulfate. taining large amounts of acid and delignified aspen wood. peroxide. In the first run (Table III), the initial concentration of peroxymo­ 176 January 1990 Tappi Journal III. Delignification of 40-mesh aspen wood (1.00 g) using peroxymonosulfate at 22°C nosulfate was only 0.45%, and the All the results mentioned were from the peroxide-acid mixtures. In equivalent total concentration of obtained using peroxymonosulfate Run 7, an equivalent quantity of hydrogen peroxide was 2.3%. Even produced using Procedure 1. Run 6 Oxone was substituted for the Proce­ under these conditions, a relatively shows the result of drastically increas­ dure 3 mixture in Run 6. All other large amount of lignin was removed. ing the peroxymonosulfate concentra­ conditions were identical except that The lignin in the residue (11.8%) was tion by using Procedure 3. Comparing some hydrogen peroxide was present much lower than that for the best of Runs 6 and 4, the same equivalent in Run 6 and the pH was much lower. the hydrogen peroxide runs (16.9%), concentration of hydrogen peroxide is The results were quite similar. For and the C/L ratio (1.5) was also much present: however, the initial concen­ Run 7, the yield of residue was a bit lower than that for the best of the tration of peroxymonosulfate was higher, and its lignin content was also peroxide runs (2.2). As illustrated by greatly increased in Run 6. The somewhat higher. These significant Runs 2 and 3, increasing the concen­ treatment time for Run 6 was reduced differences were probably the result tration of peroxymonosulfate and to one day. Despite this reduced of the much lower pH in Run 6. This extending the reaction time gave even treatment time, Run 6 shows a large is reflected in the large difference in better results. Increasing the liquor­ increase in lignin removal compared residue viscosities in Runs 6 and 7. to-wood ratio from 10:1 to 25:1 gave with Run 4. This is undoubtedly an The much higher hydrogen ion con­ a slight increase in selectivity from a effect of the much higher initial centration in Run 6 undoubtedly C/L ratio 1.5 to 1.3 (compare Runs 1 concentration of peroxymonosulfate.
Details
-
File Typepdf
-
Upload Time-
-
Content LanguagesEnglish
-
Upload UserAnonymous/Not logged-in
-
File Pages4 Page
-
File Size-