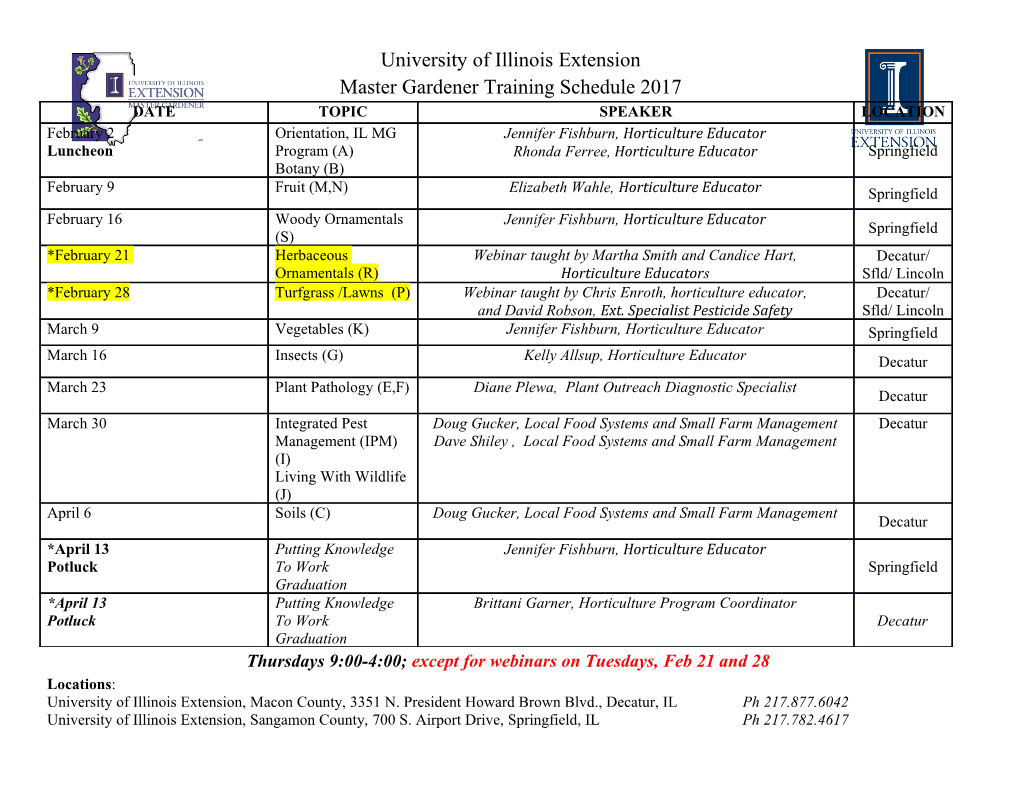
1778 IEEE TRANSACTIONS ON INDUSTRY APPLICATIONS, VOL. 47, NO. 4, JULY/AUGUST 2011 DC Bus Voltage Clamp Method to Prevent Over-Voltage Failures in Adjustable Speed Drives Lixiang Wei, Member, IEEE, Zhijun Liu, and Gary L. Skibinski Abstract—The influences of PWM switching and long cable length on motor insulations have been discussed in numerous pa- pers. This paper investigates their effect on the voltage insulation components inside an adjustable speed drive (ASD). This paper shows that high potential voltage insulation issue may exist on various components inside the ASD and cause earlier failures under very long cable or multiple drive conditions. A system model to describe this phenomenon is described in the paper. A dc bus voltage clamp circuit is proposed to reduce these voltage stresses. The effectiveness of this circuit is verified by both simulation and experimental results. Index Terms—Adjustable speed drive (ASD), insulation, long cable, voltage clamp circuit. I. INTRODUCTION DVANCES in power electronics technology has enabled A the adjustable speed drive (ASD) to reach higher switch- ing and improved controllability of voltage, current and torque. Higher switching frequency may also reduce acoustic noise. The fast dv/dt PWM switching of the inverter devices also induce high frequency ground leakage current, high shaft in- sulation voltage, and high levels of bearing current. Numerous Fig. 1. Schematics of a standard ASD with common mode and cable models: (a) Diagram of an ASD drive with SCR front end; (b) Components that are papers have been published to analyze these issues [1]–[11]. exposed to high voltage stresses. Chen and Lipo [1] pointed out that a net common-mode cur- rent flowing through three-phase stator windings to the axial common mode impedance external to the inverter. This is true direction produces a time-varying flux surrounding the motor for majority of applications. However, when an ASD is applied shaft. This flux induces a shaft end-to-end voltage driving a with very long cable or multiple parallel cables, common mode circulating bearing current in turn. Reference [2]–[5] analyzed capacitance of the cable and motor may be comparable or even the PWM switching and cable length effect on bearing current, higher than the common mode capacitance inside the drive. EMI emission, and motor insulation. In [4]–[12], various meth- Under this condition, high voltage stresses may be generated ods and topologies were proposed to reduce the effect of the inside the drive. Fig. 1(a) shows a typical diagram of an ASD PWM switching on motor insulation, EMI performance and to be studied with SCR based rectifier. Fig. 1(b) further shows bearing current effect; However, they cannot reduce the voltage the voltage insulation components inside the ASD. stresses inside the ASD drive. Nowadays, the physical sizes of the ASD drive and its high However, analysis of over voltage failures of components voltage components have been reduced dramatically to remain inside the drive has not been fully addressed. One simple competitive. Typical ways of reducing drive size is to replace assumption made from these references is that the common the bus bars with printed circuit board (PCB), to integrate high mode capacitance inside the drive is much higher than the voltage component with low voltage circuitry, to shrink the component sizes, and to reduce or remove unnecessary com- Manuscript received October 16, 2010; revised December 13, 2010 and ponents. All above optimizations may increase voltage stresses February 10, 2011; accepted February 17, 2011. Date of publication May 27, of these components and cause unexpected voltage failures. 2011; date of current version July 20, 2011. Paper 2010-IDC-415.R2, presented at the 2010 IEEE Energy Conversion Congress and Exposition, Atlanta, GA, This paper investigates the effects of PWM switching and September 12–16, and approved for publication in the IEEE TRANSACTIONS long cable lengths on voltage stresses of different compo- ON INDUSTRY APPLICATIONS by the Industrial Drives Committee of the IEEE nents inside the ASD. First, it categorizes the high voltage Industry Applications Society. The authors are with the Rockwell Automation-Allen Bradley, Mequon, components and how to analyze their voltage stresses. It is WI 53092 USA (e-mail: [email protected]; [email protected]; found out that the voltage stresses of the component can be [email protected]). simplified by analyzing the voltage differences between dc Color versions of one or more of the figures in this paper are available online at http://ieeexplore.ieee.org. bus terminals and the ground potential (GND). Then, a sys- Digital Object Identifier 10.1109/TIA.2011.2154352 tem model to describe this phenomenon is characterized and 0093-9994/$26.00 © 2011 IEEE WEI et al.: DC BUS VOLTAGE CLAMP METHOD TO PREVENT OVER-VOLTAGE FAILURES 1779 developed. It is found out that several potential high voltage stresses operating conditions (much higher than the dc bus voltage) may exist for some severe conditions. After that, a simple dc bus voltage clamp circuit is intro- duced to help reduce the voltage stresses. This circuit has the minimum number of components—two diodes; one capacitor; and one resistor. It clamps the voltage stresses of the ASD drive components to slightly higher than dc bus voltages. One advantage of this circuit is that it only operates when the GND is higher than dc+ or is lower than dc−. The wattage losses of the overall system and the voltage ratings of the discharging capacitors can be very low. Theory analysis, simulation and experimental result are provided in the paper to verify the effectiveness of the circuit. II. VOLTAGE STRESSES IN ADJUSTABLE SPEED DRIVE A. High Voltage Components and Their Voltage Stresses in ASD Drive One characteristic of ASDs is to use low voltage control signals to control high voltage switching devices. Based on their functionality, there are two types of high voltage components. The first type of components are the main circuit components that transfer power from line to load side, including inverter IGBT, rectifier diode/SCR, dc link choke, dc bus capacitor, snubber capacitor, and etc. They are all located in the differen- tial mode (DM) circuit and their voltage stresses are generally no higher than the dc bus voltage. Selection of voltage ratings for these components is straightforward. The second type of components provide protective separation between the control circuit and the main circuit, including opto-coupler, PCB, sensors, voltage/current transducer, switch mode power supply (SMPS) transformer, and etc. The high voltage (HV) sides of these components are either no higher than the positive bus or no lower than the negative bus. The low voltage (LV) sides are the control voltage that is very close to GND voltage. Therefore, the insulation voltage of the protective separation component can be approximated as the voltage between GND and the dc bus terminals. Selection of the voltage ratings for these components may be influenced by the operating condition heavily and will be analyzed. B. Differential Mode Voltage Between DC Bus Terminals to the GND The voltage stresses between the ground and the dc bus terminals can be calculated by adding the common mode and differential mode components. For the differential mode circuit, this voltage stresses can be approximated as half the dc bus voltage for a Y grounded system. Where Fig. 2. Schematics of ASD circuit: (a) common mode circuit when choke differential mode current is non-zero; (b) common mode circuit when recitifier Vdc Vdc side diode/SCR are all off; (c) ASD circuit when only one side choke (upper) Vpgpk_DM = ; Vngpk_DM = − (1) 2 2 is conducting, the other side is anti-biased; (d) inverter common mode voltage at high speed; (e) inverter common mode voltage at low speed. where Vpgpk_DM is the maximum voltage between positive dc bus and the GND in differential mode circuit, Vngpk_DM is the For a corner grounded system, the maximum voltage stresses minimum voltage between negative bus voltage and the GND between dc bus terminals to the GND can be as high as dc in differential mode circuit. bus voltage between positive bus and the GND and as low as 1780 IEEE TRANSACTIONS ON INDUSTRY APPLICATIONS, VOL. 47, NO. 4, JULY/AUGUST 2011 Fig. 3. Proposed clamp ciricuit is a solid Y ground system. negative dc bus voltage between negative bus to the GND as bus terminals and the inverter side components. The voltage shown in stresses of the drive components are generally higher than Fig. 2(a). − Vpgpk_DM = Vdc; Vngpk_DM = Vdc. (2) Fig. 2(c) shows the third equivalent circuits. Under this con- dition, only one side of the rectifier Diode/SCR is conducting. The common mode and differential mode circuit are combined C. Common Mode Voltage Between DC Bus Terminals together and cannot be separated. For the case of Fig. 2(c), and the GND where only upper side diode/SCR are conducting, the upper side voltage potential between GND and dc+ are clamped by For the common mode voltage, it is determined by the cable the input circuit. length, common mode capacitance of the ASD drive, and PWM At low speed or no load condition, the system may transit be- switching frequency. This voltage can be much higher than the tween these three conditions. As a result, the AC side common rated dc bus voltage for some cable and operating conditions as mode capacitor maybe in and out of different equivalent circuits explained in the following sections. and cause excessive voltages stresses between dc bus terminals The main objective of this paper is to investigate the voltage to GND. stresses of insulation components inside a drive; the effect The inverter common mode voltage is generated by the PWM of the PWM switching to the motor winding and bearing switching of the inverter.
Details
-
File Typepdf
-
Upload Time-
-
Content LanguagesEnglish
-
Upload UserAnonymous/Not logged-in
-
File Pages8 Page
-
File Size-