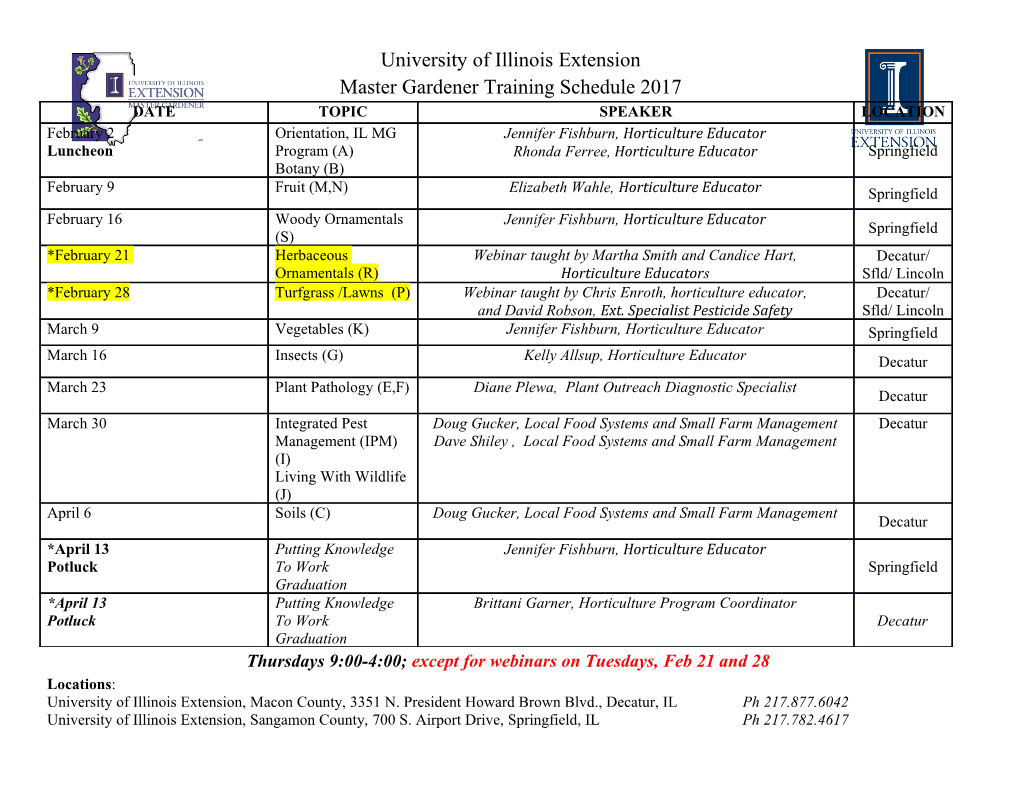
Ivo Wevers Outgassing of Technical Polymers PEEK, Kapton, Vespel & Mylar Vacuum, Surfaces & Coatings Group Technology Department Outline • Part 1: Introduction • Polymers in vacuum technology • Outgassing of water : metallic surface vs polymer • Part 2: Outgassing at Room Temperature • Outgassing measurements of PEEK, Kapton, Mylar and Vespel samples • Fitting with 2-step and 3-step models • Diffusion coefficient, moisture content and decay time constant • Part 3: Attenuation of Polymers Outgassing • Effects of bakeout and venting on pump-down curves • Effects of desication with silica gel • Conclusions & Future Vacuum, Surfaces & Coatings Group Ivo Wevers ARIES 2021 Technology Department 2 Part 1: Introduction • Polymers in vacuum technology • Outgassing of water : metallic surface vs polymer Vacuum, Surfaces & Coatings Group Ivo Wevers ARIES 2021 Technology Department 3 Polymers in vacuum technology Polymers are sometimes the only option as seal/insulator PEEK, Kapton and Vespel -> bakeout temperatures of 150-200C° Vacuum, Surfaces & Coatings Group Ivo Wevers ARIES 2021 Technology Department 4 Polymers in vacuum technology Polymers are sometimes the only option as seal/insulator PEEK, Kapton and Vespel -> bakeout temperatures of 150-200C° Guarantee a certain beam lifetime or certain operation conditions Outgassing limit (maximum pressure to be reached in 24 hours) is defined for each machine AND the residual gas analysis free of contaminants Acceptance test prior to installation: - Pumpdown will define the outgassing rate and variation in time - Leak detection - Outgassing @ 24h - RGA scan Vacuum, Surfaces & Coatings Group Ivo Wevers ARIES 2021 Technology Department 5 Polymers in vacuum technology Operational Average effective Outgassing pressure UNBAKED pumping speed rate limit at 24 requirement (24h Accelerator Area (indicative) h pumping) [l s-1] [mbar.l.s-1] [mbar] LINACS, ISOLDE AND TRANSFER ≤2.10-6 100 5∙10-5 (*) LINES CLOSE TO PSB AND PS PSB, HIE-ISOLDE, PS complex REX AND TRANSFER LINES ≤5.10-8 100 5.10-6 (*) CLOSE TO THE PS RING PS ring ≤2.10-8 70 1.5.10-6 (*) Arcs ≤10-6 10 10-5 SPS LSS (kickers, ≤10-7 100 10-5 (*) septa, RF cavities) TI2&TI8: From ≤10-5 1-2 2.10-5 SPS to TED TI2&TI8: From TED to ≤5.10-7 5 2.5.10-6 LHC Criteria for vacuum acceptance tests, P. Chiggiato, J.A.F. Somoza, G. Bregliozzi, ACC-V-ES-0001 EDMS 1752123 Vacuum, Surfaces & Coatings Group Ivo Wevers ARIES 2021 Technology Department 6 Polymers in vacuum technology PI-KAF45 PS Kicker assembly tank Pumpdown of PI-KAF45 PS Kicker Vacuum, Surfaces & Coatings Group Ivo Wevers ARIES 2021 Technology Department 7 Polymers in vacuum technology LINAC 4 Faraday Cup Vespel & Kapton wires Pumpdown LINAC4 Faraday Cup Vacuum, Surfaces & Coatings Group Ivo Wevers ARIES 2021 Technology Department 8 Outgassing of water : metallic surface vs polymer Outgassing Molecules which have previously Molecules diffusing through the bulk been adsorbed (venting),that material, entering the surface and desorb again desorbing from it Vacuum, Surfaces & Coatings Group Ivo Wevers ARIES 2021 Technology Department 9 Outgassing of water : metallic surface vs polymer Outgassing 1.E-03 ퟏ 1.E-04 풕 1.E-05 Molecules which have previously Molecules diffusing through the bulk been1.E-06 adsorbed (venting),that material, entering the surface and desorb[mbar] Pressure again desorbing from it 1.E-07 1.E-08 1.E-02 1.E-01 1.E+00 1.E+01 1.E+02 1.E+03 Elapsed Time [hours] Vacuum, Surfaces & Coatings Group Ivo Wevers ARIES 2021 Technology Department 10 Outgassing of water : metallic surface vs polymer Outgassing 1.E-03 1.E-03 ퟏ ퟏ 1.E-04 1.E-04 풕 풕 1.E-05 1.E-05 Molecules which have previously Molecules diffusing through the bulk been1.E-06 adsorbed (venting),that material,1.E-06 entering the surface and Pressure [mbar] Pressure desorb[mbar] Pressure again desorbing from it 1.E-07 1.E-07 1.E-08 1.E-08 1.E-02 1.E-01 1.E+00 1.E+01 1.E+02 1.E+03 1.E-01 1.E+00 1.E+01 1.E+02 Elapsed Time [hours] Elapsed Time [hours] Vacuum, Surfaces & Coatings Group Ivo Wevers ARIES 2021 Technology Department 11 Outgassing of water : metallic surface vs polymer Outgassing 1.E-03 1.E-03 ퟏ ퟏ 1.E-04 1.E-04 풕 풕 1.E-05 1.E-05 Molecules which have previously Molecules diffusing through the bulk been1.E-06 adsorbed (venting),that material,1.E-06 entering the surface풆− 풕and Pressure [mbar] Pressure desorb[mbar] Pressure again desorbing from it 1.E-07 1.E-07 1.E-08 1.E-08 1.E-02 1.E-01 1.E+00 1.E+01 1.E+02 1.E+03 1.E-01 1.E+00 1.E+01 1.E+02 Elapsed Time [hours] Elapsed Time [hours] Vacuum, Surfaces & Coatings Group Ivo Wevers ARIES 2021 Technology Department 12 Outgassing of water : metallic surface vs polymer Standard diffusion theory 2-step model : 1.E-03 ퟏ 4퐷 휋휏 1.E-04 퐶0 푓표푟 푡 ≪ 0.5휏 푞 푡 = ℎ 16푡 풕 푓푎푐푒 푡 4퐷 − 1.E-05 퐶 푒 휏 푓표푟 푡 ≫ 0.5휏 ℎ 0 1.E-06 퐶0 = initial diffusant concentration, Pressure [mbar] Pressure 풆−풕 퐷= diffusion coefficient, 1.E-07 ℎ= sample thickness 1.E-08 2 ℎ 1.E-01 1.E+00 1.E+01 1.E+02 휏 = . 휋2퐷 Elapsed Time [hours] Vacuum, Surfaces & Coatings Group Ivo Wevers ARIES 2021 Technology Department 13 Outgassing of water : metallic surface vs polymer Standard diffusion theory 2-step model : 1.E-03 ퟏ 4퐷 휋휏 1.E-04 퐶0 푓표푟 푡 ≪ 0.5휏 푞 푡 = ℎ 16푡 풕 푓푎푐푒 푡 4퐷 − 1.E-05 퐶 푒 휏 푓표푟 푡 ≫ 0.5휏 ℎ 0 1.E-06 퐶0 = initial diffusant concentration, Pressure [mbar] Pressure 풆−풕 퐷= diffusion coefficient, 1.E-07 ℎ= sample thickness 1.E-08 2 ℎ 1.E-01 1.E+00 1.E+01 1.E+02 휏 = . 휋2퐷 Elapsed Time [hours] Vacuum, Surfaces & Coatings Group Ivo Wevers ARIES 2021 Technology Department 14 Outgassing of water : metallic surface vs polymer Standard diffusion theory 2-step model : 1.E-03 ퟏ 4퐷 휋휏 1.E-04 4퐷 휋ℎ2 퐶0 푓표푟 푡 ≪ 0.5휏 퐶 푓표푟 푡 ≪ 0.5휏 푞 푡 = ℎ 16푡 ℎ 0풕 16휋2퐷푡 푓푎푐푒 푡 푞푓푎푐푒 푡 = 4퐷 − 1.E-05 휏 푡 퐶0푒 푓표푟 푡 ≫ 0.5휏 4퐷 − ℎ 퐶 푒 휏 푓표푟 푡 ≫ 0.5휏 ℎ 0 1.E-06 퐶0 = initial diffusant concentration, Pressure [mbar] Pressure 풆−풕 퐷= diffusion coefficient, 1.E-07 ℎ= sample thickness 1.E-08 2 ℎ 1.E-01 1.E+00 1.E+01 1.E+02 휏 = . 휋2퐷 Elapsed Time [hours] Vacuum, Surfaces & Coatings Group Ivo Wevers ARIES 2021 Technology Department 15 Outgassing of water : metallic surface vs polymer Standard diffusion theory 2-step model : 1.E-03 ퟏ 4퐷 휋휏 1.E-04 4퐷 휋ℎ2 퐶0 푓표푟 푡 ≪ 0.5휏 퐶 푓표푟 푡 ≪ 0.5휏 푞 푡 = ℎ 16푡 ℎ 0풕 16휋2퐷푡 푓푎푐푒 푡 푞푓푎푐푒 푡 = 4퐷 − 1.E-05 휏 푡 퐶0푒 푓표푟 푡 ≫ 0.5휏 4퐷 − ℎ 퐶 푒 휏 푓표푟 푡 ≫ 0.5휏 ℎ 0 1.E-06 퐶0 = initial diffusant concentration, Pressure [mbar] Pressure 풆−풕 퐷= diffusion coefficient, 1.E-07 Initial outgassing is independent of the ℎ= sample thickness thickness 1.E-08 2 ℎ 1.E-01 1.E+00 1.E+01 1.E+02 휏 = . 휋2퐷 Elapsed Time [hours] Vacuum, Surfaces & Coatings Group Ivo Wevers ARIES 2021 Technology Department 16 Part 2: Outgassing at Room Temperature • Outgassing measurements of PEEK, Kapton, Vespel and Mylar samples • Fitting with 2-step and 3-step models • Estimate of diffusion coefficient, moisture content and decay time Vacuum, Surfaces & Coatings Group Ivo Wevers ARIES 2021 Technology Department 17 Experimental setup & procedure The system, used always unbaked and kept at a temperature of ca. 22°C/295K, featured: • An RGA and a Penning gauge • A Turbomolecular pumping group • An orifice Ø 1 cm Procedure: • 24 hour venting of the system • Start pumping & logging pressure vs time • RGA on when pressure is < 4 10-8 mbar • Scan when pressure is < 4 10-8 mbar Vacuum, Surfaces & Coatings Group Ivo Wevers ARIES 2021 Technology Department 18 Description of the polymer samples Kapton HN Polyimide - Melting temperature: none Expected water content: 0.96% Samples: square sheets side 100 mm Thicknesses: 0.0125-0.125 mm Vacuum, Surfaces & Coatings Group Ivo Wevers ARIES 2021 Technology Department 19 Description of the polymer samples PEEK 450G PolyEther-Ether Ketone Semi-crystalline thermoplastic Melting temperature: 343°C Expected water content: ca. 0.25% Samples shape: disks ∅ 51 mm Thicknesses: 0.16-1.28 mm Vacuum, Surfaces & Coatings Group Ivo Wevers ARIES 2021 Technology Department 20 Description of the polymer samples Vespel SP-1 Polyimide (Sintered) Melting temperature: none Expected water content: ca. 1% Samples shape: disks ∅ 50.8 mm Thicknesses: 0.25-1.8 mm Vacuum, Surfaces & Coatings Group Ivo Wevers ARIES 2021 Technology Department 21 Description of the polymer samples MYLAR Polyethylene terephthalate Melting temperature: 254°C Expected water content: ca. 0.22% Samples shape: disks ∅ 50 mm Thicknesses: 0.24-1.03 mm Vacuum, Surfaces & Coatings Group Ivo Wevers ARIES 2021 Technology Department 22 Outgassing measurements of PEEK, Kapton and Vespel samples Vacuum, Surfaces & Coatings Group Ivo Wevers ARIES 2021 Technology Department 23 Outgassing measurements of PEEK, Kapton and Vespel samples WATER Vacuum, Surfaces & Coatings Group Ivo Wevers ARIES 2021 Technology Department 24 Outgassing measurements of PEEK, Kapton and Vespel samples AIR Vacuum, Surfaces & Coatings Group Ivo Wevers ARIES 2021 Technology Department 25 Outgassing measurements of PEEK, Kapton and Vespel samples Specific outgassing rates were calculated: 푆푒푓푓 (푃푠푎푚푝푙푒 − 푃푏푔) 푄 = 퐴 푆푒푓푓 = Effective pumping speed for H2O, 푃푠푎푚푝푙푒 = Sample pressure,푃푏푔 = Background pressure, A = Sample area.
Details
-
File Typepdf
-
Upload Time-
-
Content LanguagesEnglish
-
Upload UserAnonymous/Not logged-in
-
File Pages59 Page
-
File Size-