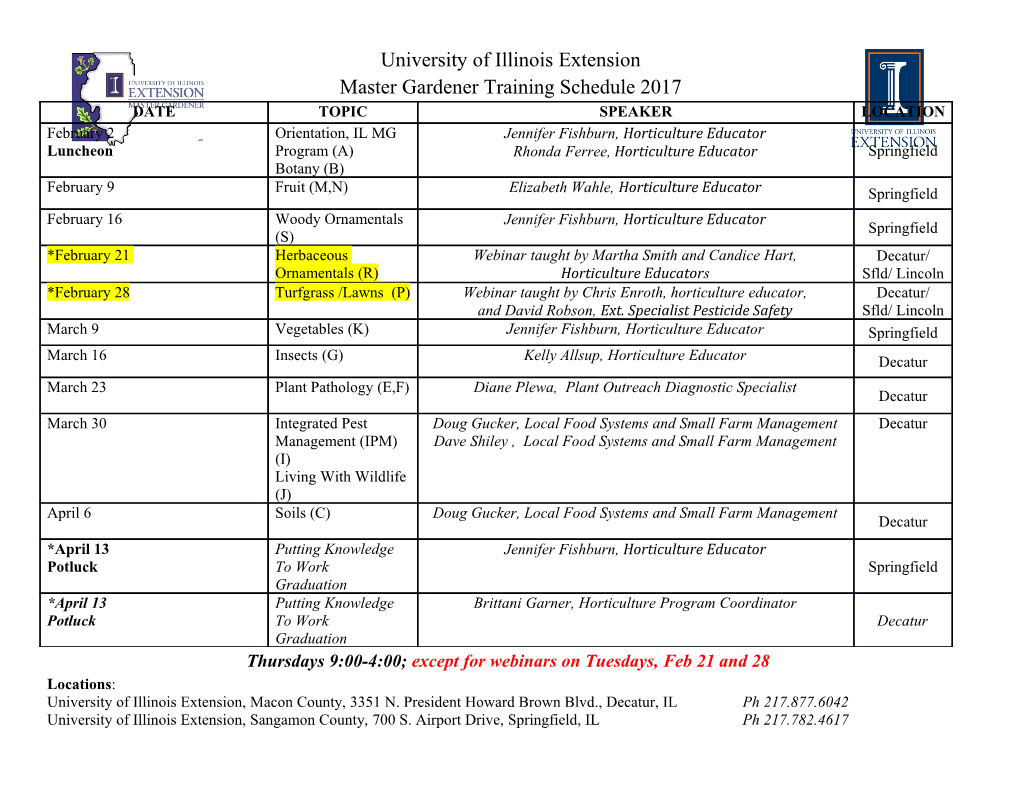
metals Article Enhancing Properties of Soft Magnetic Materials: A Study into Hot Isostatic Pressing and Sintering Atmosphere Influences Ana Romero 1 , Angel L. Morales 2 and Gemma Herranz 2,* 1 Escuela de Ingeniería Industrial y Aeroespacial, Institute of Applied Aeronautical Industry Research, Universidad de Castilla-La Mancha (UCLM), 45071 Toledo, Spain; [email protected] 2 E.T.S.I. Industrial, Institute of Energy Research and Industrial Applications, Universidad de Castilla-La Mancha (UCLM), 13071 Ciudad Real, Spain; [email protected] * Correspondence: [email protected] Abstract: Soft magnetic materials are characterized by achieving a high magnetic induction value in the presence of a small magnetic field. Common applications of these materials, such as transformers or sensors, are in constant evolution and new requirements are becoming more demanding. Nickel and its alloys are employed as smart materials taking advantage of their superior magnetoelastic properties. A metal injection molding (MIM) technique provides high-quality complex-shaped parts with a good density and controlled impurity levels, which are necessary for these applications, by carefully adjusting the sintering stage. Previous investigations have established a sintering ◦ cycle for pure nickel consisting of 1325 C for 12 h within an N2-5%H2 atmosphere. Nevertheless, microstructural, mechanical and magnetoelastic responses can still be greatly enhanced. In this context, the effects of hot isostatic pressing (HIP), and sintering atmosphere have been investigated. The application of an adequate HIP treatment leads to significant improvements in comparison to the reference sintering process. It achieves almost complete densification while increasing field- dependent elastic modulus from 8.1% up to 9.6%. Additionally, the sintering atmosphere has been Citation: Romero, A.; Morales, A.L.; proven to be a key factor in reducing impurities and hence facilitating magnetic domain motion. Herranz, G. Enhancing Properties of Soft Magnetic Materials: A Study into Three different atmospheres have been studied: N2-5%H2 (with a higher gas flow), N2-10%H2- Hot Isostatic Pressing and Sintering 0.1%CH4 and low vacuum. Minimum carbon contents have been registered using more reducing Atmosphere Influences. Metals 2021, atmospheres (N2-5%H2 and N2-10%H2-0.1%CH4) which has led to values of field-dependent elastic 11, 643. https://doi.org/10.3390/ modulus higher than 10%. This value is 2.5 times higher than that obtained when nickel parts are met11040643 processed via conventional techniques. Moreover, although minimizing carbon content has been shown to be easier and more beneficial than achieving complete densification, both strategies could Academic Editor: Tadeusz Kulik be used in combination to improve and maximize magnetoelastic performance. Received: 20 March 2021 Keywords: nickel; metal injection moulding; hot isostatic pressing; sintering atmosphere; soft Accepted: 10 April 2021 magnetic alloy; magnetomechanical properties Published: 15 April 2021 Publisher’s Note: MDPI stays neutral with regard to jurisdictional claims in 1. Introduction published maps and institutional affil- iations. Nickel-base materials are widely used for commercial purposes due to remarkable properties, reported extensively in the ASM Specialty Handbook [1], such as corrosion resistance, mechanical strength, thermal expansion, electrical conductivity, and magnetic properties. As a consequence, commercial products can be obtained in a wide range of shapes and sizes. Copyright: © 2021 by the authors. Licensee MDPI, Basel, Switzerland. The increase of the relative density and the reduction of impurities, such as C or S, This article is an open access article lends itself to the improvement of magnetic performance as has been shown in multiple distributed under the terms and studies such as the one carried out by Lall [2] in which the magnetic properties of different conditions of the Creative Commons Fe-base alloys and a stainless steel type 410L were analyzed. Melting and casting techniques Attribution (CC BY) license (https:// cannot guarantee the high purity and the low level of inclusions required for magnetic creativecommons.org/licenses/by/ applications. On the contrary, Herranz [3] remarks that the processing of a high purity 4.0/). powder via the Metal Injection Moulding (MIM) technique provides contamination control Metals 2021, 11, 643. https://doi.org/10.3390/met11040643 https://www.mdpi.com/journal/metals Metals 2021, 11, 643 2 of 19 and results in high-quality parts. Multiple purity grades of spherical or round carbonyl Ni powders with suitable particle size ranges for use in MIM are commercially available. Furthermore, MIM allows high production quantities of complex shapes, exceptional performance, and lower production costs than other manufacturing techniques. Banerjee and Joens [4] highlight that the main steps in MIM technology are the removal of the binder system followed by the sintering process to ensure the permanent bonding of the particles in a suitable protective atmosphere. Heckel [5] stated that sintering atmospheres must fulfill various functions such as preventing oxygen and other airborne contaminants from entering the furnace, reducing surface oxides on the powder particles, controlling carbon on the surface, removing carbon, controlling oxidation during cooling, and efficiently transferring or removing heat. All these features were also confirmed years later by German [6]. Typical MIM powders have a D90 particle size distribution of around 20 µm. The huge surface area of MIM powders guarantees surface energy that allows the obtention of intense diffusive forces for the sintering process and therefore high densification. This, however, results in an increased risk of oxidation during thermal processing, because nickel is a metal in which the oxides are easily reduced by carbon or hydrogen. For this reason, according to Blais [7], sintering of nickel parts is typically carried out in a sulfur-free reducing atmosphere, such as hydrogen, combinations of nitrogen-hydrogen, dissociated ammonia, or burnt natural gas. Sintering cycles of time–temperature are carefully aimed to obtain specific density requirements. Nevertheless, MIM does not ensure obtaining fully densified materials in some cases when the particle distribution is too narrow. This fact has been verified by Romero et al. [8] in a previous study in which the sintering process of nickel powders between 3 and 7 microns was done at high temperatures and for long periods of the plateau without achieving relative densifications higher than 97%. This obstacle may restrict the use of these materials for applications where high magnetic properties are required since Ma et al. [9] proved that the highest magnetic performance is achieved with the highest density values. Accordingly, some thermal treatments such as hot isostatic pressing (HIP) could be used to decrease porosity and hence improve the magnetic response. In this sense, Qiu et al. [10] achieved fully densities in a nickel-base superalloy after applying for 3 h a HIP process at ∼1190 °C and a pressure of 120 MPa. In a recent study carried out by Martínez et al. [11], higher densifications were obtained in pure nickel powders via HIP than those obtained via a conventional hot-pressing process. The interest in the wide possibilities of nickel and nickel alloys has grown over the years. In the recent review of Horke et al. [12] it is possible to find many studies related to these materials after being processed by MIM, but they are mainly based on their mechanical properties. On the other hand, the application of HIP in nickel [11] or nickel alloys [13] is also an issue of topical interest. However, these studies do not focus on magnetic properties but in the study of densification [14], microstructure [15], elongation [16] or strength and ductility [17] after HIP. There are few studies about the magnetic properties of nickel alloys, and none of the pure nickel, after the combined application of MIM and HIP. Thus, there is still room for exploring the application of these techniques for enhancing the magnetic properties of nickel. In the search for optimizing pure nickel microstructural, mechanical and magnetic performance (by means of facilitating magnetic domain motion), the objective of this paper is twofold: 1. Execution of a HIP treatment after sintering to minimize the residual porosity of the pieces. 2. Selection of an adequate sintering atmosphere (N2-5%H2,N2-10%H2-0.1%CH4 or low vacuum) which decreases impurities. Metals 2021, 11, 643 3 of 19 2. Experimental Procedure Commercially available pure carbonyl nickel powder (3–7 µm) was selected for the evaluations. The rounded morphology of the powder can be seen in Figure1, which shows a Scanning Electron Micrograph (SEM) of the powder with a carbon content of 0.07 wt.% and an absolute density of 8.87 g/cm3 measured by means of an elemental analyzer LECO CS-230 and a helium pycnometer Micromeritics AccuPyc II 1340, respectively. Figure 1. Scanning Electron Micrograph (SEM) image of carbonyl nickel powder. The feedstock was prepared by mixing the nickel powder with a previously devel- oped multi-component binder system consisting of paraffin wax (PW) and high-density polyethylene (HDPE) in equal proportions. The nickel powder content in the feedstock is 50% in volume based on previous research carried out by Herranz et al. [18] in which a feedstock with adequate fluidity was developed after different rheological
Details
-
File Typepdf
-
Upload Time-
-
Content LanguagesEnglish
-
Upload UserAnonymous/Not logged-in
-
File Pages19 Page
-
File Size-