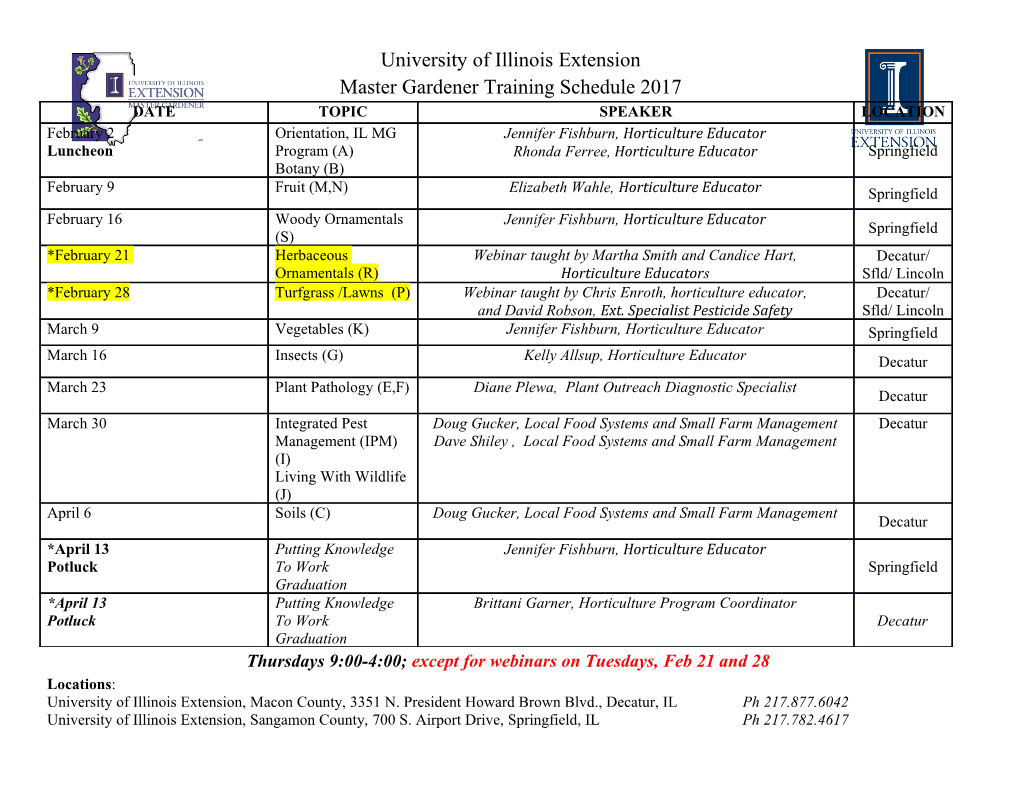
Europäisches Patentamt *EP001037854B1* (19) European Patent Office Office européen des brevets (11) EP 1 037 854 B1 (12) EUROPEAN PATENT SPECIFICATION (45) Date of publication and mention (51) Int Cl.7: C01D 15/08 of the grant of the patent: 27.04.2005 Bulletin 2005/17 (86) International application number: PCT/CA1998/001132 (21) Application number: 98959684.6 (87) International publication number: (22) Date of filing: 07.12.1998 WO 1999/029624 (17.06.1999 Gazette 1999/24) (54) PROCESS FOR THE PURIFICATION OF LITHIUM CARBONATE VERFAHREN ZUR REINIGUNG VON LITHIUMCARBONAT PROCEDE DE PURIFICATION DU CARBONATE DE LITHIUM (84) Designated Contracting States: (56) References cited: AT BE CH CY DE DK ES FI FR GB GR IE IT LI LU GB-A- 2 190 668 US-A- 3 857 920 MC NL PT SE US-A- 4 207 297 (30) Priority: 09.12.1997 US 69165 P • PATENT ABSTRACTS OF JAPAN vol. 012, no. 28.08.1998 US 143330 132 (C-490), 22 April 1988 & JP 62 252315 A (NIPPON CHEM IND CO LTD:THE), 4 November (43) Date of publication of application: 1987 27.09.2000 Bulletin 2000/39 • PATENT ABSTRACTS OF JAPAN vol. 012, no. 005 (C-467), 8 January 1988 & JP 62 161973 A (73) Proprietor: Limtech Carbonate Inc. (SUMITOMO CHEM CO LTD), 17 July 1987 Shawinigan, Quebec G9N 8M7 (CA) • PATENT ABSTRACTS OF JAPAN vol. 011, no. 101 (C-413), 31 March 1987 & JP 61 251511 A (72) Inventors: (SUMITOMO CHEM CO LTD), 8 November 1986 • AMOUZEGAR Kamyab Shawinigan, Quebec G9N 7P7 (CA) Remarks: • HARRISON, Stephen The file contains technical information submitted Shawinigan, Quebec G9N 1B3 (CA) after the application was filed and not included in this • ST. AMANT, Guy specification Shawinigan, Quebec G8Y 6N7 (CA) (74) Representative: Burford, Anthony Frederick W.H. Beck, Greener & Co. 7 Stone Buildings Lincoln’s Inn London WC2A 3SZ (GB) Note: Within nine months from the publication of the mention of the grant of the European patent, any person may give notice to the European Patent Office of opposition to the European patent granted. Notice of opposition shall be filed in a written reasoned statement. It shall not be deemed to have been filed until the opposition fee has been paid. (Art. 99(1) European Patent Convention). EP 1 037 854 B1 Printed by Jouve, 75001 PARIS (FR) EP 1 037 854 B1 Description [0001] The invention relates to an improved process for the purification of lithium carbonate. [0002] Lithium carbonate (Li2CO3) is produced commercially from three sources: (1) extraction from mineral sources 5 such as spodumene; (2) lithium-containing brines; or (3) from sea water. [0003] There are a number of commercial applications of lithium carbonate including: as an additive in aluminum molten salt electrolysis and in enamels and glasses. In its purer forms, for example having 99.1 wt% Li2CO3,Li2CO3 is used to control manic depression, in the production of electronic grade crystals of lithium niobate, tantalate and fluoride. High purity lithium carbonate is also required in the emerging technologies of lithium batteries. There are two 10 major classes of rechargeable lithium batteries, those using lithium ion and thin film polymer electrolyte-lithium metal. [0004] In the case of the lithium ion battery, purified lithium carbonate is required for the cathode. In the case of thin film batteries using polymer electrolytes, lithium metal is obtained by chlorinating lithium carbonate to form lithium chloride and subsequent electrolysis to metallic lithium. The key to obtaining lithium of the grade required for lithium batteries is to use purified lithium chloride and carrying out electrolysis in the virtual absence of air and humidity to 15 minimize lithium's rapid reactions with these substances. [0005] Electrolytic production of lithium metal is practiced commercially using an eutectic melt of LiCl and KCI (45 and 55 wt %, respectively) at 450°C under anhydrous conditions. During electrolysis, lithium metal produced typically at a steel cathode rises to the surface of the melt due to its significantly lower density (0.5 g/ml relative to 1.5 g/ml for the melt). At the anode, chlorine gas is evolved. In some cell designs, there is a diaphragm between the anode and 20 cathode to prevent or at least partially prevent recombination of chlorine and lithium. In other cell designs, as described in US-A-4,617,098 and US-A-4,734,055, a diaphragm is avoided by using the so-called "gas-lift" effect which reduces the contact time between the lithium metal and the chlorine gas, thus reducing their rate of recombination. It is also believed that the molten salt provides a protective covering over the surface of the lithium. [0006] As mentioned above, the key to obtaining high purity lithium metal is to minimize impurities such as sodium, 25 calcium and magnesium in the lithium chloride feed to the electrolyser. There are, however, other impurities such as carbonate, sulfate and borate, which, while not significantly affecting the purity of the lithium metal produced, do affect the performance of the electrochemical cell, by increasing the consumption of the carbon anodes by the oxidation of these species at the anode, resulting in the production of carbon dioxide and by decreasing the current efficiency of the metal production. This effect is well known in molten salt electrolysis, though poorly understood. They are also 30 known to adversely affect the current efficiency of both lithium and magnesium cells, though the mechanism is not known. [0007] Published accounts of the commercial production of lithium chloride describe the reaction of hydrochloric acid with lithium carbonate in an aqueous solution. Impurities such as sulfate are removed by addition of barium chloride and filtration. Lithium chloride is recovered by evaporation and crystallization. In these processes, some impurities are 35 removed by a bleed of the liquor during the evaporation and crystallization. Lithium chloride is extremely hygroscopic, leading to difficulties in the drying step with corrosion and with increased energy requirements. The major difficulties with these processes are the large energy demand, theoretically 30x103 kJ/kg, and the need for corrosion resistant materials and inability to use directly (i.e. without pretreatment) lithium carbonate from sources other than minerals, such as lithium carbonate from brines, since they often contain significant concentration of borates which are deleterious 40 for the operation of the electrochemical cells. [0008] Alternative methods have been described for the production of lithium chloride, including the direct chlorination of lithium carbonate by chlorine at 300 -650 °C in molten lithium chloride. There are equally numerous patents describing the recovery of lithium chloride from brines including US-A-5,219,550, US-A-4,980,136 and US-A-4,243,392 but these do not appear to have yet achieved commercial practicability. 45 [0009] In US-A-4,271,131, US-A-4,243,392, US-A-4,261,960 and US-A-4,474,834, Brown, et al. teach processes whereby lithium chloride is concentrated to 40 % by weight and then heated to over 200 °C to render the boron insoluble as boron oxide. Isopropanol extracts lithium chloride, leaving a residue of boron oxides and other insoluble materials. Purified lithium chloride is recovered by evaporation of isopropanol and crystallization. These processes involve a calcination step which is costly, both in terms of capital and operating costs due to the materials of construction. Ad- 50 ditionally, yields are reduced, further increasing operating costs. [0010] In an improved version of the above process, fatty acid alcohols such as iso-octyl alcohol dissolved in kerosene are used to extract boron as boric acid from lithium brine. The boron-free aqueous brine is then evaporated at 105 - 115 °C under a vacuum of 70 - 90 mm Hg (9 - 12 kPa) absolute pressure to give crystals of lithium chloride. The majority of the calcium and magnesium remain in solution so purer lithium chloride is recovered by filtration or by centrifugation 55 to give 99 % pure lithium chloride. Additional washing with low molecular weight alcohol gives greater than 99 % purity. When combined with extraction with isopropanol, 99.9 % pure LiCl is obtained, as described in US-A-4,274,834. [0011] US-A-5,219,550 describes a process for producing low boron lithium carbonate. Lithium chloride-rich brine is contacted with a fatty alcohol dissolved in kerosene to extract boron. Magnesium and calcium are removed by 2 EP 1 037 854 B1 precipitation and liquid-solid separation. The brine is then treated with sodium carbonate to precipitate lithium carbonate and sodium chloride brine. Lithium carbonate produced by this process has a purity of 99.57 %. Boron content is reduced to 1 ppm from 500 ppm, with calcium levels at 80 ppm and magnesium at 20 ppm. This grade of lithium carbonate contains levels of magnesium and calcium in excess of that required for production of battery-grade lithium. 5 [0012] An alternative process is described by Brown, et al., in US-A-4,036,713 and US-A-4,207,297. These patents describe transformation of impure Li2CO3 into LiOH and precipitation of calcium carbonate by treatment with CO2. The process concentrates brines, either natural or otherwise, containing lithium and other alkali and alkaline metal halides to2-7%oflithium content. Most of the alkali and alkaline earth compounds are removed by precipitation at a pH between 10.5 - 11.5. The pH is modified with recycled LiOH, which removes the remaining magnesium, and by Li2CO3 10 and/or CO2, which produces calcium carbonate as a precipitate. [0013] The purified brine is electrolyzed in the anolyte of an electrochemical cell divided by a cation exchange mem- brane, the catholyte being LiOH.
Details
-
File Typepdf
-
Upload Time-
-
Content LanguagesEnglish
-
Upload UserAnonymous/Not logged-in
-
File Pages12 Page
-
File Size-