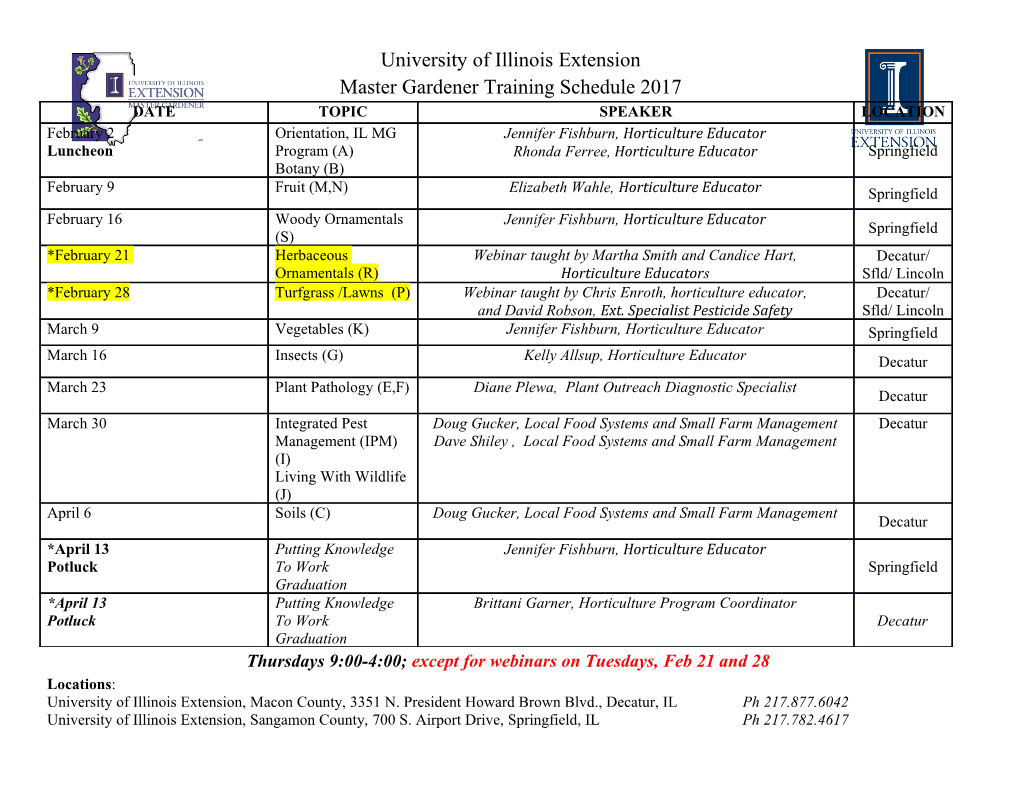
ISOTHERMAL TRANSFORMATIONS IN EUTECTOID ZIRCONIUM-NIOBIUM ALLOYS by MALCOLM JOHN FINLAYSON A THESIS SUBMITTED IN PARTIAL FULFILMENT OF THE REQUIREMENTS FOR THE DEGREE OF MASTER OF APPLIED SCIENCE in th© Department of MINING AND METALLURGY We accept this thesis as conforming to the standard required from candidates for the degree of MASTER OF APPLIED SCIENCE. Members of the Department of Mining and Metallurgy THE UNIVERSITY OF BRITISH COLUMBIA November, 1957- ABSTRACT Isothermal transformations in eutectoid zirconium-niobium alloys have been studied by resistometric techniques at high temperature, and by room-temperature hardness measurements, metallography, and X-ray methods, Room-temperature measurements were performed on specimens which had been heat-treated in evacuated vycor capsules. The resistometric method gave data which were not in agreement with data obtained by room-temperature measurements. A T-T-T curve established by room-temperature hardness and metallography was found to be similar to one obtained by a previous investi• gator. The lack of agreement between measurements made at high temperature and those made at room temperature suggests that a structural change is occurring in these alloys during the quench from the transformation tempera• ture. For this reason, room temperature metallography is unsatisfactory for following transformations in these alloys. The analysis of micro-structure is complicated by the presence of a needle-like •phase' which was not identifiable by the X-ray techniques employed. It is shown that the resistometric technique is a sensitive method for observing transformations in zirconium-niobium alloys. In presenting this thesis In partial fulfilment of the requirements for an advanced degree at the University of British Columbia, I agree that the Library shall make it freely available for reference and study. I further agree that permission for extensive copying of this thesis for scholarly purposes may be granted by the Head of my Department or by his representative. It is understood that copying or publication of this thesis for financial gain shall not be allowed without my written permission. Department of ML^^.^ <^~<J tod/,^j^ The University of British Columbia, Vancouver 5\ Canada. Date 7 M 7 ACKNOWLEDGEMENT The" author is grateful for financial aid in the form of a research assistantship provided by the Defence Research Board of Canada. Funds for the present work were nrovided by the Defence Research Board of Canada under Research Grant DRB 7510-18. The author gratefully acknowledges the assistance of Dr. V. Griffiths, under whose direction this investigation was performed, and the technical advice and assistance given by Mr. R, Butters and Mr. R. Richter. TABLE OF CONTENTS Page I. INTRODUCTION ...... o..oo.o«oo. 9. O0.o««*o I A. Object of the Investigation . 1 B. The Zirconium-Niobium Alloy System 3 II. PROCEDURE AND RESULTS . 14 A * AllOy Melt 6 1*3.3.1 S o«o90«4>ftoooooo«««e » © # 1A- ,'B.. Preliminary Work 16 C. Isothermal. Transformation Study ............. 23 1. AllOyS ..o.eao.o....... ...... 23 2. Transformations in Vycor Capsules . 25 3. Resistance Measurements ... 30 III. DISCUSSION OF RESULTS AND CONCLUSIONS 49 IV. APPENDICES 1. Resistance Data «.«... ...... ........ 53 2. Related Phase Diagrams .o...o..........oo 55 3. ASTM d-Spacings for Related Zirconium Compounds ..... 59 V. REFERENCES »»••»«»»•••••»•*•»••••••••••• 60 LIST OF ILLUSTRATIONS Figure Page 1. A comparison of the neutron cross section of zirconium with that . „ „ of other elements ..... ..... 2 2. The zirconium-niobium phase diagram (after Rogers and Atkins) .... 7 3. Room temperature resistivities of zirconium-niobium alloys in two conditions ..oo.. ..»...•. .o ... o.o.oo 7 4. Change in resistance of a 17.5/5 Nb alloy on slow heating ...... 8 5. Variation in lattice parameter with composition for alloys quenched from 1100°C ' 8 6. Microstructure of a zirconium - 15% Nb alloy quenched from 800°C. 10 7. Microstructure of a zirconium - 12% Nb alloy quenched from 1250°C . 10 8. The zirconium-niobium alloy system (after Bychkov et al). 12 9. Hardness vs composition of zirconium-niobium alloys for different thermal treatments 12 10. T-T-T curve for a zirconium - 14.6% Nb alloy (after Domagala). .... 13 11. Diagram of the levitation melting apparatus of Polonis et al .... 17 12. Vickers hardness vs weight percent Nb for as-cast Zr-Nb alloys ... 19 13. Pure zirconium, as-cast 20 14. Zirconium - 4.16% niobium, as-cast 20 15. Zirconium - 4.62% niobium, as-cast 20 16. Zirconium - 14.2% niobium, as-cast 20 17. Zirconium - 13% niobium, as-cast ,.. • ......... 21 18. Zirconium - 19.6% niobium, as-cast ................. 21 19. Zirconium - 4.6% niobium - heat treated . 21 20. Zirconium - 19.6% niobium - heat treated 21 21. Typical ingot produced by the levitation method. .......... 24 ILLUSTRATIONS (continued) Page 22. Microstructures of a Zr - 17.4% Nb alloy isothermally transformed at 630°C 26 23. Microstructures of a Zr - 17.455 Nb alloy isothermally transformed at 354°C 27 24. Microstructures of a Zr - 17.4% Nb alloy isothermally transformed at 630°C 28 25. Change in Vickers hardness for the 17.4% Nb alloy isothermally transformed at the temperatures shown • 29 26. T-T-T curve for a zirconium - 17.4% niobium alloy based on hardness changes ........ *..».•••.•*•. 32 27. Diagram of furnace and vacuum chamber assembly ........... 33 28. General view of apparatus 34 29. View of main vacuum furnace elements . 34 30. Diagram of resistance measuring circuit ....... 35 31. Vacuum furnace assembly showing position of furnace and connections. 36 32. Close-up of lid showing the method of attaching the specimen .... 38 33. The change of the ratio of resistance to initial resistance .... 39 34. Change of resistance on heating the near-equilibrium structure of a Zr - 16.4% Nb alloy 40 35. Some typical resistance - time curves obtained on a Zr - 16.4% alloy 42 36. Tentative T-T-T curve for a Zr - 16.4% Nb alloy, based on resistance data .....*•••• 43 37. Hardness change in a Zr - 16.4% Nb alloy, isothermally transformed at 515°C 43 38. Microstructures of the 16,4% Nb alloy isothermally transformed at 515°C 45 39. Needles in a Zr - 16.4% Nb alloy water quenched after 48 hrs.at 800°C 46 40. Back reflection Laue pictures of the Zr - 16.4% Nb alloy 47 LIST OF TABLES Page 1. Some Physical and Mechanical Properties of Zirconium and Niobium. 3 2. The Mechanical Properties of Zirconium-Niobium Alloys at Room- Temperature 4 3. Yield Strengths of Zirconium-Niobium Alloys at 649°C ......... 5 4. Analysis of the Alloy Materials of Domagala et al 14 5. Analysis of Foote Crystal Bar Zirconium 15 6. Spectrographic Analysis of Niobium 15 7. Decrease in Gas Content of Niobium on Vacuum Sintering 15 8. Data Pertinent to the Coil Design 17 9. Composition and As-cast Vickers Hardness of Zr-Nb Alloys Prepared by Levitation Melting r 18 10. D-spacings (Angstroms) from X-ray Measurements for Alloys Made with Sponge Zr . 11. Dimensions of Coil Used to Prepare Alloys of Crystal Bar Zirconium 12. Weight Data for Alloys of Crystal Bar Zirconium Base 23 17„ D-spacings (Angstroms) for the 17.4% Niobium Alloy Isothermally Transformed at 514°C 31 14. D-spacings (Angstroms) for a 16.4% Niobium alloy Isothermally Transformed at 515°C 44 ISOTHERMAL TRANSFORMATIONS IN EUTECTOLD .ZIRCONIUM-NIOBIUM ALLOYS INTRODUCTION A. Object of the Investigation For use within the fission zone of nuclear reactors which have to work at high temperatures-, the usual engineering materials are unsuitable, either because they absorb too many neutrons or react with the fuel. Thus attention has been directed to metals formerly regarded as rare, and great advances have been made in the development of such materials for engineering use. Of the metals with relatively high melting points, zirconium has the lowest absorption cross-section for thermal neutrons (see Fig. l). It was therefore considered to be a potentially important structural or canning material for reactors operating at medium and high temperatures. However, since the creep strength of zirconium at elevated temperatures was found to be poor, extensive studies of the alloying behaviour of zirconium have been undertaken. These studies, which are described in a recent volume,^ constituted a search for alloys having high-temperature strength coupled with the retention of the attractive nuclear and chemical pronerties of pure zirconium. It was therefore the object of the present work to add to the data on zirconium alloys by studying isothermal transformations in zirconium-niobium alloys of eutectoid composition and thereby determining the related Time- Temperature-Transformation (T-T-T) diagram. - 2 - Table I Thermal-Neutron Cross Section (Barns) of Commonly Available Elements With Melting Points of Metallic Elements In Low and Intermediate Cross Section Group* Low Cross Section Intermediate Cross Section High Cross Section ( <I.O Barn) • . (1.0 to 10.0 Barn?)-- . (>I0 Barns)- Melting Melting Element cr. Point (CC) Element am Point (CC) Element <r« Oxygen 0.0002 Zinc I.I 419 Manganese 13 Carbon 0.0045 Columbium I.I 2415 Tungsten 19 Beryllium 0.009 1280 Barium 1.2 704 Tantalum 21 Fluorine 0.01 Strontium 1.2 770 Chlorine 32 Bismuth 0.032 Nitrogen 1.8 Cobalt 35 Magnesium 0.05'» 6SiiiI Potassium 2.0 ' 64 Silver 60 Silicon 0.13 Germanium 2.3 Lithium 07 Phosphorus 0.19 Iron 2.4 1539 Gold 94 Zirconium 0.18 1845 Molybdenum 2.4 262S Hafnium 115 Lead 0.17 327 Gallium 2.7 30 Mercury 380 Aluminum 0.22 660 Chromium 2.9 1890 Iridium 440 Hydrogen 0.33 Thallium 3.3 300 Boron 750 Calcium 0.43 '850 Copper 3.6 10S3 Cadmium 2,400 Sodium 0.49 98 Nickel 4.5 14S5 Samarium 6,500 Sulphur 0.49 Tellurium 4.5 Gadolinium 44.0011 Tin 0.6S Z32 Vanadium 4.7 1710 Antimony 6.4 630 Titanium 5.6 1725 Table II Thermal-Neutron Cross Sections and Melting Points of Metallic Elements With .Melting Points Above S0O°C Lou I .
Details
-
File Typepdf
-
Upload Time-
-
Content LanguagesEnglish
-
Upload UserAnonymous/Not logged-in
-
File Pages68 Page
-
File Size-